- OBJECTIVE:
- To lay down a procedure for Preparation, Review and Approval of Artwork.
- SCOPE:
- This SOP is applicable for artwork of all products manufactured at {Company Name} {Company Location}.
- RESPONSIBILITY:
- Marketing Head, Packaging Department Head/designee, Production executive/designee, QC executive / designee & QA executive/designee.
- ACCOUNTABILITY:
Packaging department Head & QA Head.
- PROCEDURE:
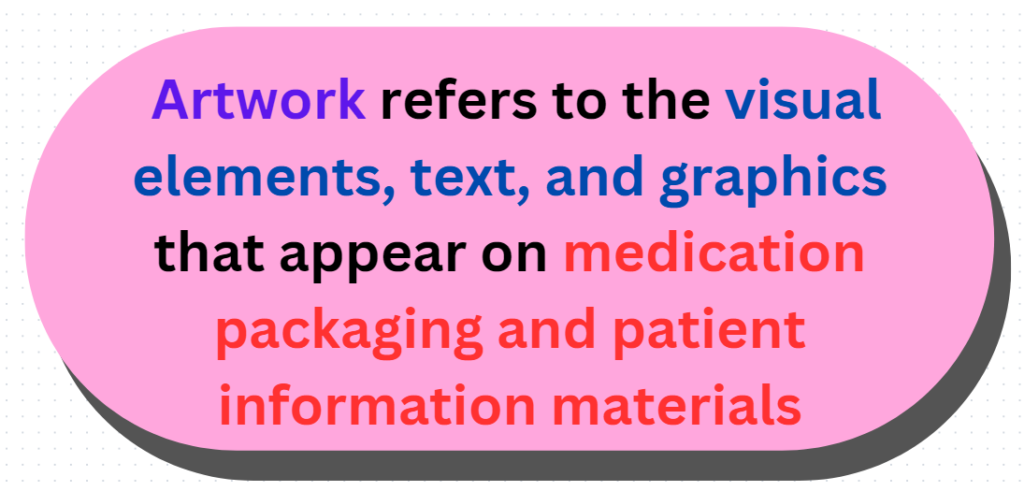
- Defination:Artwork refers to the visual elements, text, and graphics that appear on medication packaging and patient information materials. It’s not about artistic expression, but rather about clear and accurate communication that prioritizes safety and regulatory compliance.
- For New Artwork:
Click the link for download word file copy of this document: https://pharmaguidehub.com/product/preparation-and-approval-of-art-work/
- Head Marketing department shall be responsible for providing Artwork module & CDR/PDF files to Packaging department along with approval certificate from concerned authority or state licensing authority.
- Head Marketing/designee shall be responsible for verification of number of colors and resolving customer queries on the artwork.
- In case of text in English and local language marketing has to ensure the text matter of both languages.
- Packaging Department shall be responsible for designing of the artwork as per packaging module and product information.
- Packaging Department shall be responsible for verification of the bar code, item code provided by the IT department.
- Head Packaging Department/designee shall be responsible for forward the artwork with CDR and PDF files to the QA department for scrutiny.
- QA department shall take printout of artwork provided by Packaging Department & shall forward the artwork printout to Production department then Production head/Designee shall be responsible for approval of layouts in case of new products or for new change parts or pack.
- Head Production shall verify the artwork with respect to the machine suitability or dimensions of packing material.
- After the verification of artwork by Production Department, Artwork shall forward to QC department for respective verification.
- Head QC/designee shall be responsible for verification of text matter of the artwork with respect to Pharmacopoeial status. After that QC shall forward that particular artwork to QA for further verification.
- QA Assistant manager/designee shall verify the text matter/label claim/brand name/generic name of the artwork with respect to the regulatory requirement or as per the registered product information.
- In case of any correction QA department shall forward those corrections to Packing Department. But if artwork is correct in terms of design dimensions & in terms of regulatory. Artwork shall be forward to QA Head for final approval.
- Head QA shall be responsible for final approval of the artwork.
- After Head QA final approval, scanned copy of the same with Annexure-I shall be forwarded to all concern departments.
- The Packing Department shall forward final approved artwork CDR/PDF files to purchase department for further process.
- The purchase department shall raise the Purchase Order to the printer for respective Product designing along with the final approved CDR/PDF file of the artwork.
- In the light of approved artwork copy by the printer shall provide the shade cards/negatives for shades/waterproofs for final approval.
Click the link for download word file copy of this document: https://pharmaguidehub.com/product/preparation-and-approval-of-art-work/
- Revision of Artwork :
- For change in text matter, the revision number shall be changed to next version i.e. first version and for next change in text matter the second version shall be allocated by QA Department.
- As soon as the artwork with change in text matter and new revision number shall be received to QA department and QA will check the text as per change suggested.
- REFERENCES:
Not Applicable
- ANNEXURES:
ANNEXURE | NAME OF ANNEXURE |
Annexure-I | Artwork Approval Form |
- DISTRIBUTION:
Controlled Copy No. 01 | : | Head Quality Assurance |
Controlled Copy No. 02 | : | Head Quality Control Department |
Controlled Copy No. 02 | : | Head Production Department |
Controlled Copy No. 03 | : | Head Packaging Department |
Master Copy | : | Quality Assurance Department |
- ABBREVIATION:
QA | : | Quality assurance |
SOP | : | Standard operating procedure |
No. | : | Number |
- REVISION HISTORY:
CHANGE HISTORY LOG
Revision No. | Details of Changes | Reason for Change | Effective Date |
00 | New SOP | Not Applicable | To be written manual |
ANNEXURE-I
SIGN & NAME OF ALL CONCERN DEPARTMENTS | |||
S. No. | Department Name | Date | Name/Sign |
Packaging Department | |||
Production Department | |||
Quality Control | |||
Quality Assurance Department |
Click the link for download word file copy of this document: https://pharmaguidehub.com/product/preparation-and-approval-of-art-work/
Frequently Asked Questions?
Q1: What is the significance of artwork in the pharmaceutical industry?
A1: Artwork plays a crucial role in the pharmaceutical industry as it represents the visual elements of product packaging, labeling, and promotional materials. It ensures that information is accurately conveyed, complies with regulatory requirements, and maintains brand identity.
Q2: Why is it important to have a standardized process for the preparation and approval of artwork in the pharmaceutical sector?
A2: A standardized process ensures consistency, accuracy, and compliance with regulatory guidelines in the preparation and approval of artwork. This helps in preventing errors, maintaining product quality, and meeting regulatory requirements for packaging and labeling.
Q3: What are the key stakeholders involved in the preparation and approval of pharmaceutical artwork?
A3: Key stakeholders include regulatory affairs, marketing, packaging development, quality assurance, and external printing partners. Each plays a vital role in ensuring that the artwork meets regulatory standards and aligns with the marketing and quality objectives.
Q4: How does the pharmaceutical industry ensure that artwork complies with regulatory requirements?
A4: The pharmaceutical industry follows established guidelines and standards such as those provided by regulatory bodies (e.g., FDA, EMA). Additionally, rigorous quality control processes are implemented, involving thorough reviews and approvals by regulatory experts and internal teams.
Q5: What steps are typically involved in the preparation of pharmaceutical artwork?
A5: The preparation of pharmaceutical artwork involves steps such as initial design, content creation, adherence to regulatory requirements, translation of text (if applicable), and collaboration with cross-functional teams. It also includes considerations for printing processes and packaging materials.
Q6: How is the approval process for pharmaceutical artwork managed to ensure efficiency and accuracy?
A6: The approval process is typically managed through a well-defined workflow involving multiple levels of review. Cross-functional teams assess the artwork for compliance with regulatory requirements, accuracy of information, and adherence to brand guidelines. Electronic approval systems may be utilized for traceability and efficiency.
Q7: What challenges can arise during the preparation and approval of pharmaceutical artwork?
A7: Challenges may include changes in regulatory requirements, translation issues, miscommunication between stakeholders, and tight timelines. Managing these challenges requires effective communication, flexibility, and a proactive approach to address potential issues.
Q8: How does technology contribute to the improvement of the artwork preparation and approval process in the pharmaceutical industry?
A8: Technology, such as electronic approval systems, digital asset management, and computer-aided design tools, enhances efficiency, traceability, and collaboration during the artwork preparation and approval process. These tools streamline workflows and facilitate real-time communication among stakeholders.
Q9: What role does quality control play in ensuring the accuracy of pharmaceutical artwork?
A9: Quality control is essential for verifying that the artwork meets regulatory requirements, is free from errors, and aligns with the approved specifications. Thorough quality checks are conducted to ensure that the final artwork accurately represents the intended product information.
Q10: How does the pharmaceutical industry handle updates and revisions to approved artwork?
A10: Updates and revisions to approved artwork are managed through a controlled change process. This involves initiating a change request, conducting the necessary assessments, obtaining approvals, and ensuring that all affected stakeholders are informed of the changes. Documentation is updated accordingly to maintain a comprehensive record.
Click the link for download word file copy of this document: https://pharmaguidehub.com/product/preparation-and-approval-of-art-work/