- OBJECTIVE:
The purpose of this SOP is to provide guidance for process validation to be performed at {company Name} Adherence to this procedure shall ensure consistency in meeting its predetermined specifications and quality attributes.
- SCOPE:
This procedure is applicable to carried out the Process Validation of the process for all the products manufactured at {Company Name} {Company Location}.
- RESPONSIBILITY:
- Quality Assurance:
- To prepare and approve validation protocol and report.
- To conduct process validation by monitoring, sampling, testing, challenging the specific manufacturing process for compliance with design limits, specifications, and requirements.
- To establish tolerance limit based on APQR.
- To verify whether the parameters are within the established tolerance limit at time of batch release.
- To create change control number assigned by QA.
- R&D:
- Design and optimize the Manufacturing process within design limits, specifications, and requirements.
- To provide the MFC with critical process parameters and other necessary information to conduct the validation studies.
- To review process validation protocol and report.
Click the link to download word file copy of this document: https://pharmaguidehub.com/product/process-validation/
- Manufacturing:
- Operate and maintain plant, facilities, equipment and execute manufacturing process within its design limits, specifications, or requirements as per the approved process validation protocol and Master Batch production record.
- To ensure that the equipments/Instruments used in the Process validation are Qualified and Calibrated.
- To review process validation protocol and report.
- Quality Control:
- Carryout the analysis of the validation samples and to review process validation protocol and report.
- To check whether the parameters are within the established tolerance limit at time of result reporting.
- Engineering:
- To provide necessary support to perform validation studies.
- ACCOUNTABILITY:
Head Quality Department shall be responsible for implementation of this SOP.
- PROCEDURE:
- Definitions:

- Process Validation: Process validation is established documented evidence which provides high degree of assurance that a specific process will consistently produce a product, meeting its predetermined specifications and quality characteristics.
- Prospective Validation: It shall be carried out on the small scale or F&D batches during development stage.
- Concurrent Validation: It shall be carried out for the determination and evaluation of process parameters applicable from scale up to large batches.
- Retrospective Validation: It is carried out by the historical trending of all critical parameters related to analytical i.e. physical, chemical, and microbiological parameters of product manufactured by same process. To ensure all the parameters shall be in the limit and in uniform range.
- Approach to Process validation:

- Process validation is defined as the collection and evaluation of data, from the process design stage through commercial production, which establishes scientific evidence that a process is capable of consistently delivering quality product.
- Process validation involves a series of activities taking place over the lifecycle of the product and process which involves three stages. It links Product, Process Development and Qualification of the commercial manufacturing process.
Click the link to download word file copy of this document: https://pharmaguidehub.com/product/process-validation/
- Stage 1 – Process Design: The commercial manufacturing process is defined during this stage based on knowledge gained through development and scale-up activities.
- Stage 2 – Process Qualification: During this stage, the process design is evaluated to determine if the process is capable of reproducible commercial manufacturing.
- Stage 3 – Continued Process Verification: Ongoing assurance is gained during routine production that the process remains in a state of control.
- Initiation of process validation studies:
- Process Validation requirement shall be identified through change control procedure and process validation is initiated whenever a new process, new product or new equipment is introduced.
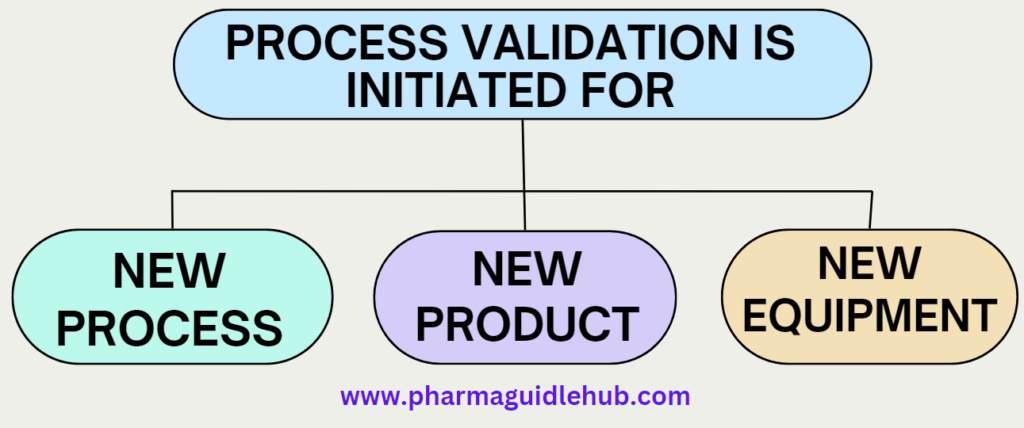
- Process validation studies shall be performed for the changes which has an actual or potential effect on the operating parameters of an existing process, component, or equipment. Also process validation shall be performed when moving an operation from one production line /equipment to another.
- Process Validation shall not be applicable if a change is made to non critical process parameter i.e. where the finished product quality will not be affected by the change.
- Design of process validation studies and establishing strategy for process control:
- Design of process:
- Process design shall be performed by incorporating the Process information available from the product development activities (Process Development Protocol and Report) and R&D batches.
- Design of process:
- Design of process validation studies and establishing strategy for process control:

- R & D shall provide the master formula card and the critical process parameters/ steps as per the process design to evaluate as a part of process validation activity.
- During the design of process validation studies, the functionality and limitations of commercial manufacturing equipment shall be considered.
- The predicted contributions to variability posed by different component lots, production operators, environmental conditions, and measurement systems in the production setting shall be evaluated.
- Process knowledge shall be developed from Design of Experiment (DOE) by revealing relationships, including multivariate interactions, between the variable inputs (e.g., component characteristics or process parameters) and the resulting outputs.
- The Goal of process design stage is to design a process suitable for routine commercial manufacturing that can consistently deliver a product that meets its quality attributes.
- Establishing strategy for process control:
- Process control parameters shall be designed based on the process development data in order to evaluate the variability in the process which affects the approved specification for the quality parameters.
- The strategies for process control shall be designed to reduce input variation, adjust for input variation during manufacturing (and so reduce its impact on the output), or by combining both the approaches.
- The controls shall consist of material analysis and equipment monitoring at significant processing points. These controls shall be established in the master production and process validation records.
- Process Qualification: The reproducibility of the process design during commercial manufacturing shall be evaluated during the process qualification (PQ) stage of process validation, which consist of two elements such as design of the facility, and qualification of the equipment and utilities and process performance qualification (PPQ).
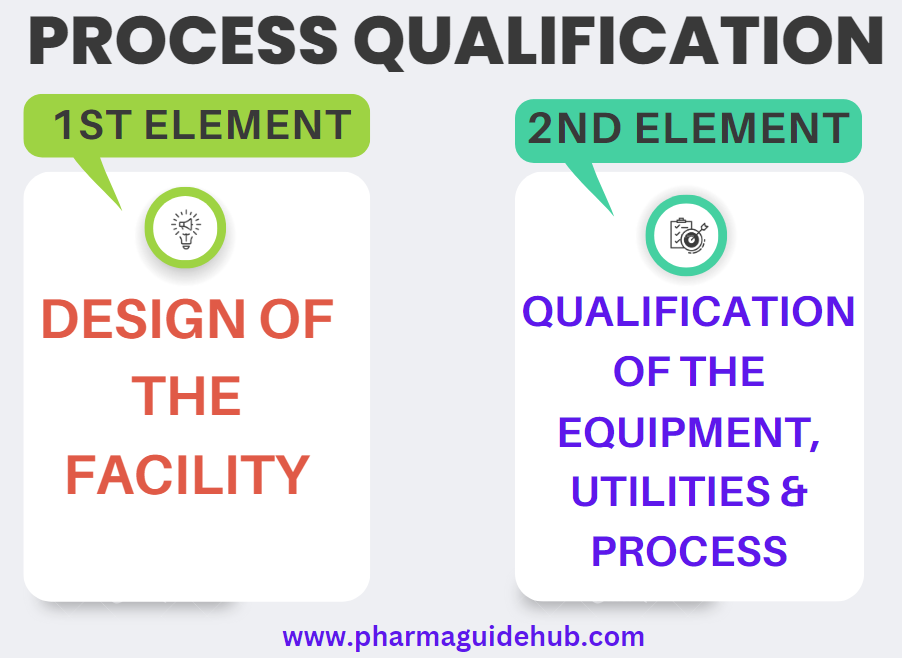
- During the process performance qualification, CGMP-compliant procedures must be followed, and successful completion of this Stage is necessary before commercial distribution.
Click the link to download word file copy of this document: https://pharmaguidehub.com/product/process-validation/
- Design of facility and Qualification of utilities and equipment:
- Manufacturing facility shall be properly designed and commissioned before process performance qualification as per the cGMP requirements.
- Qualification of utilities and equipment shall includes the following activities: but not limited to:
- Selection of utilities and equipment construction materials, operating principles and performance characteristics based on whether they are appropriate for their specific uses.
- Verification of utility systems and equipment are built and installed in compliance with the design specifications (e.g., built as designed with proper materials, capacity, and functions, and properly connected and calibrated).
- Verifying that utility systems and equipment operate in accordance with the process requirements in all anticipated operating ranges. This should include challenging the equipment or system functions while under load comparable to that expected during routine production.
- The performance of interventions, stoppages and start-up shall be incorporated during validation studies.
- Process Performance Qualification:The approach to process performance qualification shall be based on sound scientific knowledge and overall level of product and process understanding and demonstrable control. The level of monitoring and testing shall be sufficient to confirm uniform product quality throughout the process in a reproducible manner.
- Preparation of Process Validation protocol:
- QA shall prepare the process validation protocol with reference to Master formula card.
- Quality Assurance Department shall co-ordinate the entire validation activity.
- Representative from Production, R&D, Quality Assurance and Quality Control shall ensure the successful completion of process validation activity.
- The Process Validation Protocol shall contain the following:
- Table of content
- Protocol Approval
- Objective, Scope, details of validation approach, Reason for validation.
- Responsibility of the concerned Department
- Product details which include Product name, market, batch size and packaging details.
- Batch formula
- Manufacturing Flow chart
- The manufacturing conditions, including operating parameters, processing limits, and component (raw material) inputs.
- Data to be collected and when and how it will be evaluated.
- Test to be performed and acceptance criteria of each significant processing step.
- Design of facilities and qualifications of utilities and Equipment.
- Personal Training
- Verification of material sources (Components and Containers/closures)
- Specification references and Master formula Card and BPR Document Number /references.
- Environmental conditions during batch manufacturing process.
- Critical process parameters with rationale and acceptance criteria.
- Status of the validation of analytical methods.
- Criteria and process performance indicators that allow for a science and risk-based decision (Risk assessment and statistical analysis).
- Sampling procedure, details of sampling, and acceptance criteria.
- Annexure (if any) like pictorial presentations for sampling locations, and rationale for challenge studies.
- Evaluation of results and conclusion- On the basis of the evaluation of In-Process & finished product analysis & other critical parameters of the validation batches, suitable conclusion shall be drawn that the Process/ facility is capable to produce product of desired quality on consistent basis.
Click the link to download word file copy of this document: https://pharmaguidehub.com/product/process-validation/
- Defining the Equipment:
- The exact equipment to be used for process validation shall be determined. Equipment shall be identified by its plant / equipment identification number.
- Where there is number of equivalent items of equipment that could be used than the reference number for the actual item of equipment used shall be recorded or a relevant document referenced in the protocol.
- In case of a new equipment, the critical device list and rationale for the equipment shall be detailed with their operating ranges, accuracy and calibration requirements.
- For each stage of the process, testing will be defined in the respective Process Validation Protocols so that there is a clear definition of what testing is to be done at Process Validation.
- If Process Validation involves changes in equipment it is advisable to define acceptance criteria so as to differentiate equipment failures from process related failures.
- Utilities and facilities such as purified water and HVAC should be qualified or validated before starting development work supporting process validation and must be validated before running the Process Validation batches.
- Defining the Process:
- A well-defined process must be available before the start of Process Validation activities.
- A process shall be consistently capable of meeting agreed specifications and a statistical approach should be used to provide evidence of process capability.
- A new process or major modification of an existing process shall be developed and optimized on production equipment and the development / optimization work documented.
- This documentation will describe the process, justify which of the process parameters are considered critical or non – critical, detail the proven acceptable range for the critical parameters over which the validation exercise will be performed and detail the operating range within these parameters including the settings to be used for routine production.
- Where an operating range is required for production, typically the range used at process validation will be as per the Master Formula card and Qualification ranges.
- Limits for process parameters such as product temperature, outlet temperature, drive speed during drying of granulated product or control parameters (such as bulk density, tap density, particle size analysis – in case of blend) shall be specified in the protocol / BPR / specification wherever applicable.
- Process validation protocol is to be prepared as per the details mentioned in the respective BPR of the product.
- Product Specifications and Analytical Methods:
- Analytical Methods used in process validation must be validated and product Specifications and methods should be in place.
- All the raw and packaging material specifications must be approved.
- Product Specifications and Analytical Methods:
- Testing Programme:
- The number and size of batches:
- The number of batches for process validation shall be sufficient to demonstrate the consistency of the critical parameter ranges specified in the protocol.
- Three initial consecutive batches shall be considered for process validation. Consecutive batches means, three batches in a row of the product to be validated.
- Where there are a number of variables to be validated, process validation may require more than three batches to demonstrate the consistency of the process.
- The batch size shall be representative of routine production. Where fixed batch size is used in production, the process validation batches shall be the same size.
- For continuous process operations, such as filling or tablet compression, the length of time run shall be adequate to simulate production conditions.
- Sampling details:
- A clear and concise sampling plan shall be provided and explained.
- Samples shall be of an appropriate size, taken at a sufficient time interval and tested to give a high level of assurance that the whole batch will comply with its specifications. The batches shall be released as per the Finished Product Release Specifications.
- Evaluation of process validation documents:
- On completion of Process Validation Batch, manufacturing documents shall be completed and sent to the QA department for review.
- The batch records and the In-process and laboratory test results shall be scrutinized to ensure that the batches were manufactured, sampled, and tested as per the process validation protocols.
- Failures and deviations:
- Any test failures during Process Validation must be formally investigated to determine the cause of failure.
- Where the cause of failure is not obvious, it may be useful to use an investigation procedure to ensure that all the possible areas of potential failure are covered.
- Once the cause of the Process Validation failure has been identified, the failure shall be classified into the following categories.
- Type 1: Where the failure can be attributed to an occurrence which is not intrinsic to the process.
- Type 2: Where the failure may be attributed to a process failure or where the investigation is inconclusive than the validation exercise has failed.
- In case the validation team decides to revalidate the Process Validation, then the following things shall be considered.
- Introducing a change in operating parameters, process steps or control systems.
- Changing the process equipment or the procedure for using the equipment.
- Suspension of the Process Validation exercise until further evaluation and / or development has been carried out.
- Changing in the sampling Plan.
- Review of historical data.
- Change in the Process Validation acceptance Criteria.
Click the link to download word file copy of this document: https://pharmaguidehub.com/product/process-validation/
- Once it is agreed, what action needs to be taken to enable the process to routinely meet the acceptance criteria, a minimum of three further validation batches need to be produced which address the area of failure.
- Process Validation Report:
- Process validation report shall be prepared after the completion of the Process Validation activity described in the Process Validation protocol.
- The following points need to be covered in the Process Validation report, but not limited to:
- Reference to Process Validation protocol
- The validation batch numbers, and batch details pertained to the Process Validation execution.
- Raw Material / or component batch numbers used in Process Validation execution.
- A unique Reference number for the equipments used and their Qualification status.
- Detail of the critical process parameters and process ranges that were used for the Process Validation batches.
- In process, finished product Test results and acceptance criteria as stated in the protocol.
- Details of deviations from the protocols / process / procedure.
- Summary of all non-conformances and unexpected observations: OOS investigations and incident reports raised for any of the input raw material, component or intermediate batches used in the validation batches should also be assessed for their impact on the validity of the validation exercise.
- Discuss and cross reference of all aspects of the protocol.
- Reference to any investigation reports.
- Clear conclusion as to whether the data indicates the process met the conditions established in the protocol and whether the process is considered to be in a state of control.
- Recommendations and corrective actions.
- Conclusion.
- Certification
- Approval of the process validation report
- All the details of process validation study shall be reviewed and compiled.
- Process Validation Report:
- The compiled report shall be reviewed and evaluated by QC/ R & D/Production and Quality assurance and suitable conclusion shall be drawn to validate the manufacturing process.
- Continued Process Verification:
- The continued process validation studies shall be performed to provide assurance that the process remains in the state of control (validated state) during commercial manufacturing.
- The unplanned departures from the process shall be detected by collecting and evaluating the information/data about the performance of the process.
- The ongoing program to collect and analyse product and process data that relate to the product quality shall be established and the data collected shall be statistically trended and reviewed.
- The collected data and information shall be used to suggest ways to improve and optimize the process by altering some aspects of the process or product such as operating conditions, process controls, and component or in-process material characteristics.
- Once established, the qualification status must be maintained through routine monitoring, maintenance and calibration procedures and schedule.
- In case of any changes in the validated parameter, the same shall be handled through change control / deviation management system. Impact assessment for the proposed change shall be done and based on the impact assessment revalidation shall be carried out.
- In case of change in batch size up to 10X of the initially validated batch size, revalidation shall be performed, and the batch manufactured shall be released for commercial distribution based on the recommendations of the process validation report.
- The batches shall be released to market for commercial distribution after successful completion of process performance qualification.
- Documentation:
- All the information related to each stage of process validation lifecycle shall be documented.
- Process flow diagrams shall describe each unit operation, its placement in the overall process, monitoring and control points, and the component, as well as other processing material inputs (e.g., processing aids) and expected outputs (i.e., in-process materials and finished product).
- Analytical Methodology:
- Procedures for analytical method and equipment maintenance, documentation practices, and calibration practices supporting process-development efforts should be documented or described.
- Data collection and Establishment of trend:
- Data for continuous Process Verification shall be collected by QA from routine production batches before batch release.
- The data shall be collected for all parameters that make significant impact on product quality and process variability. This includes quality of inprocess material (Blend) and finished product.
- Indicative list of parameters (but not limited to) to be considered for different dosage form is as per annexure I.
- For establishing the trend of existing products, data of preferably minimum 10 batches shall be collected and subjected to statistical analysis.
- Subsequently for existing products, each year separate trend shall be generated by considering preferably minimum 10 released batches data from previous year or years.
- For new product, data from first 10 or minimum 5 released batches shall be considered including validation batches.
- Data collection and Establishment of trend:
Click the link to download word file copy of this document: https://pharmaguidehub.com/product/process-validation/
- REFERENCES:
USFDA Guideline for Industry : Process Validation: General Principles and Practices (Jan. 2011)
- ANNEXURES:
ANNEXURE No. | NAME OF ANNEXURE |
Annexure-I | Process Validation Protocol |
Annexure-II | Process Validation Report |
- DISTRIBUTION:
Controlled Copy No. 01 | : | Head Quality Assurance |
Controlled Copy No. 02 | : | Head Production |
Controlled Copy No. 03 | : | Head Quality Control |
Master Copy | : | Quality Assurance |
- ABBREVIATIONS:
SOP | : | Standard Operating Procedure |
No. | : | Number |
Ltd. | : | Limited |
QA | : | Quality Assurance |
- REVISION HISTORY:
CHANGE HISTORY LOG
Revision No. | Details of Changes | Reason for Change | Effective Date |
00 | New SOP | Not Applicable | To be written manual |
Click the link to download word file copy of this document: https://pharmaguidehub.com/product/process-validation/
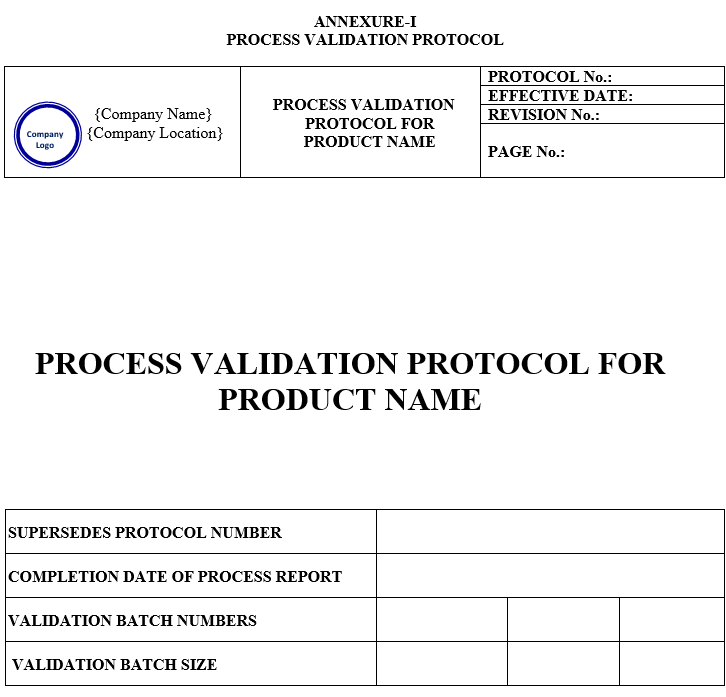
ANNEXURE-II
PROCESS VALIDATION REPORT
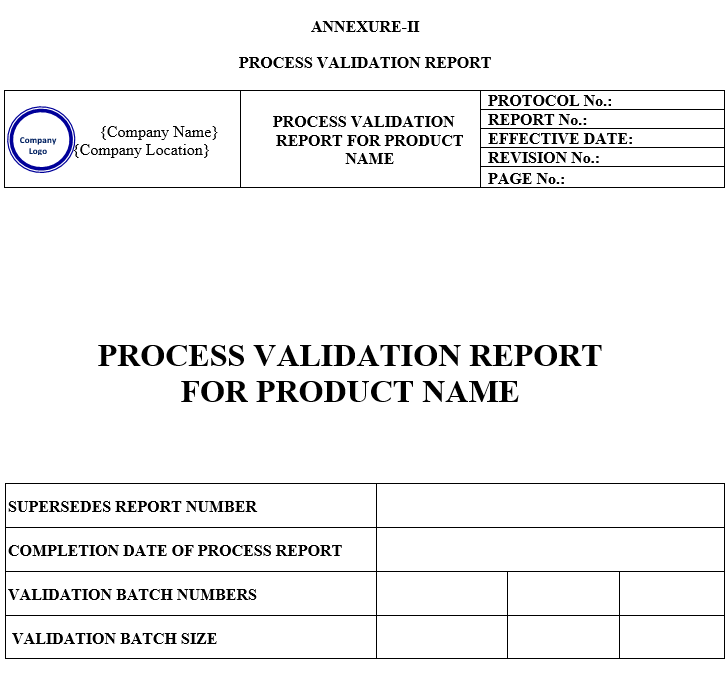
Frequently Asked Question?
1. What is the purpose of process validation?
The purpose of process validation is to establish documented evidence that a specific manufacturing process can consistently produce a product that meets its predetermined specifications and quality characteristics. This helps ensure product safety, efficacy, and consistency.
2. Who is responsible for process validation?
Multiple departments are involved in process validation, each with their own responsibilities:
- Quality Assurance (QA): Prepares and approves validation protocols and reports, conducts process validation, establishes tolerance limits, verifies parameters during batch release, and creates change control numbers.
- Research and Development (R&D): Designs and optimizes the manufacturing process, provides critical process parameters and information to QA, and reviews validation protocols and reports.
- Manufacturing: Operates and maintains the plant, facilities, and equipment, executes the manufacturing process within its design limits, ensures equipment is qualified and calibrated, and reviews validation protocols and reports.
- Quality Control (QC): Analyzes validation samples and reviews validation protocols and reports.
- Engineering: Provides necessary support to perform validation studies.
3. What are the different stages of process validation?
There are three stages of process validation:
- Stage 1: Process Design: The commercial manufacturing process is defined based on knowledge gained from development and scale-up activities.
- Stage 2: Process Qualification: The process design is evaluated to determine if it is capable of reproducible commercial manufacturing.
- Stage 3: Continued Process Verification: Ongoing assurance is gained during routine production that the process remains in a state of control.
4. What are the key elements of a process validation protocol?
A process validation protocol should contain the following information:
- Objective and scope of the validation
- Responsibilities of each department involved
- Product details
- Batch formula and manufacturing flow chart
- Manufacturing conditions, operating parameters, and processing limits
- Data to be collected and how it will be evaluated
- Tests to be performed and acceptance criteria for each significant processing step
- Design of facilities and qualifications of utilities and equipment
- Training requirements
- Verification of material sources
- Environmental conditions during batch manufacturing
- Critical process parameters with rationale and acceptance criteria
- Sampling procedures and details
- Evaluation of results and conclusion
- Annexures for pictorial presentations, rationale for challenge studies, etc.
5. What are some potential failures during process validation?
Process validation failures can be categorized as follows:
- Type 1: Failures not intrinsic to the process, such as equipment malfunctions or operator errors.
- Type 2: Failures related to the process itself, indicating the process needs further optimization or changes.
6. What happens if the process validation fails?
If the process validation fails, the cause of the failure will be investigated and a corrective action plan will be developed. This may involve revalidating the process with modifications, changing operating parameters, or improving process control.
7. How is continued process verification performed?
Continued process verification involves collecting and analyzing data from routine production batches to ensure the process remains in a state of control. This data is used to identify trends, detect potential problems, and make improvements to the process.
8. What documentation is required for process validation?
All stages of the process validation lifecycle should be documented, including flow diagrams, analytical methods, data collection procedures, and trend analysis.
9. Explain the difference between Prospective, Concurrent, and Retrospective Validation.
Answer: . Types of Process Validation:
- Prospective Validation:
- Conducted on small scale or F&D batches during the development stage.
- Concurrent Validation:
- Carried out for the determination and evaluation of process parameters applicable from scale up to large batches.
- Retrospective Validation:
- Involves historical trending of critical parameters to ensure uniformity in physical, chemical, and microbiological aspects of products manufactured by the same process.
10. How is the initiation of process validation studies determined, and when is process validation not applicable?
Answer: . Initiation of Process Validation Studies:
- Determination: Identified through the change control procedure when a new process, product, or equipment is introduced.
- Applicability: Not applicable if a change is made to a non-critical process parameter where the finished product quality will not be affected.
Click the link to download word file copy of this document: https://pharmaguidehub.com/product/process-validation/