- OBJECTIVE:
- To lay down the procedure for Receipt, Storage and Control of Printed labels in warehouse.
- SCOPE:
- This SOP is applicable for the procedure for Receipt, Storage and Control of Printed labels in warehouse at {Company Name} {Location}.
- RESPONSIBILITY:
- WH Executive/Designee – is responsible for ensuring compliance with the SOP.
- Executive/Designee QA – shall be responsible to verify the non-conformance(s) if any.
- Executive/Designee QC – shall perform the sampling and testing of materials.
- Head Warehouse – is responsible for compliance of the SOP.
- ACCOUNTABILITY:
QA Head shall be Accountable for implementation of SOP.
- PROCEDURE:
- RECEIPTS:
- Security personnel shall intimate the Warehouse on receipt of labels and shall send the documents for verification.
- Documents shall be verified by Warehouse personnel for P.O. No., Approved vendor, excise particulars and purchase order.
- In case the received quantity is more than the PO qty, communication shall be made to the purchase department.
- Purchase department shall amend the PO to the received quantity.
- The vehicle shall be allowed by security personnel upon the clearance of documents from Warehouse.
- The material shall be unloaded for physical inspection followed by de-dusting using a vacuum cleaner followed by dry lint free cloth in receiving bay.
- During material receipt if any discrepancy found the same shall be intimated to QA by discrepancy report as per Format-I “Discrepancy Report”.
- In case of cut labels, verify the quantity by counting the minimum pack size.( i.e. supplier is packed 500 labels x 10 small bundles/packets =5000 Nos of labels packed in a box, in such cases warehouse personnel shall open the outer box and verify the 10 small bundles/packets) After verification if any short receipt of small packs (10 small bundles/packets) then inform to QA by filling the discrepancy report as per Format-1 through warehouse head and intimate the same to purchase department through mail.
- In case of roll labels, open the outer box/container count the number of rolls inside as mentioned in the documents i.e. if supplier is packed 9 rolls x 5000 numbers and one roll of 3000 numbers in a box and it is mentioned in the documents/COA, then open the outer box and count the number of rolls as per the details given in the documents. (If the supplier is mentioning the quantity on the core of the label then cross verify the same.)
- “Material Received Report” shall be prepared and generate the required number of “UNDER TEST” label.
- Ensure that the “UNDER TEST” label is duly filled before affixing to all the containers.
- Approved or Rejected labels shall be affixed over the under test label by Quality control department and same shall be cross verified by Warehouse personnel with COA after the release of MRR.
- Released MRR copy shall be filed in MRR file.Based on the test status material shall be shifted to the respective storage area.
Click the link to download word file copy of this document:
https://pharmaguidehub.com/product/receipt-storage-and-control-of-printed-labels/
- STORAGE AND CONTROL:
- All printed labels shall be identified and indicate status with status label in its designated storage location.
- Adequate care shall be taken to prevent any type of mix-ups.
- Designated/Authorized personnel only shall be permitted to issue the printed labels room.
- REFERENCES:
Not Applicable
- ANNEXURES:
Annexure No. | Title of Annexure |
Annexure- I | Discrepancy Report |
- DISTRIBUTION:
- Controlled Copy No. 01 : Head Quality Assurance
- Controlled Copy No. 02 : Head Warehouse
- Controlled Copy No. 03 : Head Quality Control
- Master Copy : Quality Assurance Department
- ABBREVIATIONS:
No. | : | Number |
SOP | : | Standard Operating Procedure |
MRR | : | Material Received Report |
P O No. | : | Purchase Order Number |
QA | : | Quality Assurance |
- REVISION HISTORY:
CHANGE HISTORY LOG
Revision No. | Details of Changes | Reason for Change | Effective Date |
00 | New SOP | Not Applicable | To Be Written Manual |
Annexure-I
DISCREPANCY REPORT
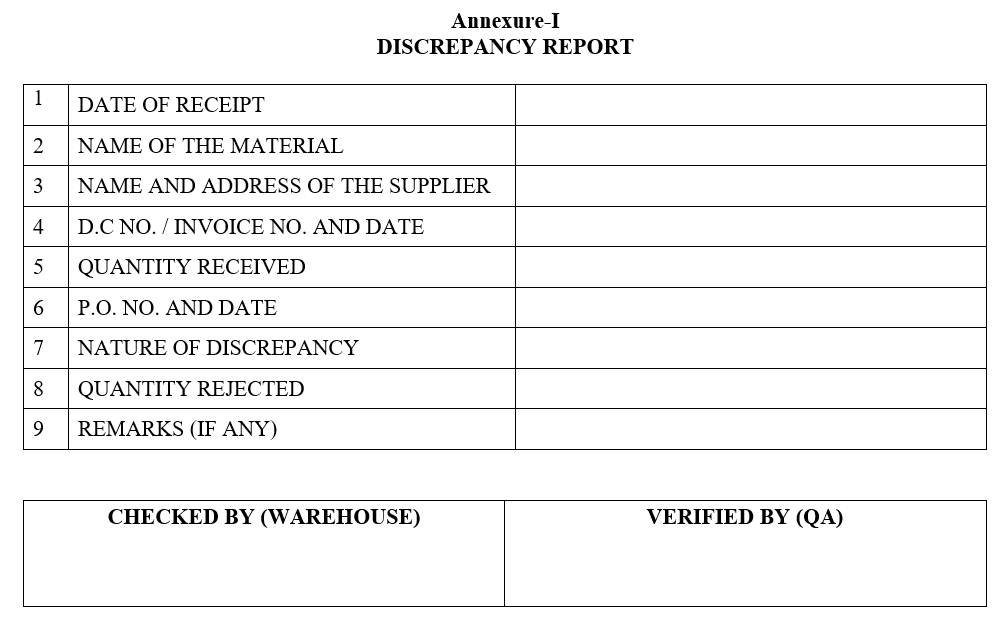
Frequently Asked Question ?
Q: What is the process for receiving labels in the warehouse?
A: Security personnel must intimate the Warehouse on receipt of labels and send the documents for verification. Warehouse personnel will then verify the documents for P.O. No., approved vendor, excise particulars, and purchase order. If the received quantity is more than the PO qty, communication must be made to the purchase department. The purchase department will then amend the PO to the received quantity. The vehicle will then be allowed by security personnel upon the clearance of documents from Warehouse.
Q: How are labels inspected upon arrival?
A: The material shall be unloaded for physical inspection followed by de-dusting using a vacuum cleaner followed by dry lint free cloth in receiving bay. During material receipt, if any discrepancy is found, it must be intimated to QA by discrepancy report as per Format-I “Discrepancy Report”.
Q: How are cut labels and roll labels handled differently during inspection?
A: In case of cut labels, the quantity must be verified by counting the minimum pack size. If there is any short receipt of small packs, then inform to QA by filling the discrepancy report as per Format-1 through warehouse head and intimate the same to purchase department through mail. In case of roll labels, open the outer box/container and count the number of rolls inside as mentioned in the documents. If the supplier is mentioning the quantity on the core of the label, then cross verify the same.
Q: What happens after the labels are inspected?
A: A “Material Received Report” must be prepared and the required number of “UNDER TEST” labels must be generated. The “UNDER TEST” label must be duly filled before affixing to all the containers. Approved or Rejected labels will be affixed over the under test label by Quality control department and the same shall be cross verified by Warehouse personnel with COA after the release of MRR. The released MRR copy will be filed in MRR file. Based on the test status, the material will be shifted to the respective storage area.
Q: How are printed labels stored and controlled?
A: All printed labels must be identified and indicate status with status label in its designated storage location. Adequate care must be taken to prevent any type of mix-ups. If Possible printed labes must be kept under lock and key. Designated/Authorized personnel only shall be permitted to issue the printed labels room.
Click the link to download word file copy of this document:
https://pharmaguidehub.com/product/receipt-storage-and-control-of-printed-labels/