- OBJECTIVE:
- To lay down the procedure for the Receipt, Storage, Palletization and Dispatch of Finished Goods in the Warehouse.
- SCOPE:
This SOP is applicable for the warehouse department at {Company Name} {Location}.
- RESPONSIBILITY:
- WH Executive/Designee – is responsible for ensuring compliance with the SOP.
- Head Warehouse – is responsible for compliance of the SOP.
- ACCOUNTABILITY:
QA Head shall be Accountable for implementation of SOP.
- PROCEDURE:
- Receipt of Finished Goods from Packing Department:
- After completion of packing of the Finished Goods, the completed batches shall be transferred to FG Stores along with Finished Goods Transfer Note (FGTN).
- FGTN shall be filled by Packing Department Person and shall be verified by IPQA Personnel.
- On receipt of Finished Goods, Warehouse Personnel shall verify the physical quantity, Product Code, Product Name, Batch Number and total number of shippers and the details of loose shippers as per FGTN.
- The original FGTN shall be handed over to the Packing Person and one copy of FGTN shall be preserved in FG Stores for record.
- During the handover of the Finished Goods, Warehouse Personnel shall check for any damage to the Finished Goods Packs.
- Storage of Finished Goods:
- The pallets shall be stored in the Warehouse on the locations and the locations shall be updated.The Finished Goods shall be arranged on pallets and the same shall be stored as per the recommended storage condition.
- Pine wood or as per customer requirement.
- Free from chemicals, oil & odour.
- Clean without cracks and wooden splinters.
- Free from termites and borers.
- Nest able ultra-light weight HDPE plastic pallet is also used for palletization as per customer requirement. (For which Heat treatment certificate is not required).
- The pallet size shall be selected on the basis of the market.
- For the dispatch for US market, the pallet size shall be 1200 mm x 1000 mm or as per customer specific requirement.
- For the dispatch to the EU market, the pallet size shall be 1200 mm x 800 mm or as per customer specific requirement.
- For the dispatch of any Finished Goods to US market for the first time, check if the product is a launch product. If so, it is to be verified with the Business Development team to check if any Plair (Pre-Launch Activities Importation Requests ) approval is required.
- If Plair approval is required, get the related intimation from Business Development team and proceed for the dispatch as per the Plair approval (Format-I: Vehicle Inspection and Dispatch Checklist).
- Stacking and configuration of shippers shall be done based on the height requirements specified by the customer.Shipper labels should be visible from all directions.
- The maximum height of the pallet should not have more than 1300 mm for Sea shipments or as per customer requirement or as per stack height monitoring.
- The maximum height of the pallet should not have been more than 1600 mm for all AIR shipments or as per customer requirement or as per stack height monitoring.
- For the purpose of dispatch, if any loose pallet is to be made, the Warehouse Person shall remove the shippers from the top level of the full pallet.
- While doing so he should ensure that no inner layer is removed from the intact pallet since it may lead to confusion of being a full pallet.
- After the palletization, the pallet shall be carry-strapped using edge boards.
- The carry strap shall be tightened by using the carry strap machine.
Click the link to download word file copy of this document:
https://pharmaguidehub.com/product/procedure-for-receipt-storage-palletization-and-dispatch-of-finished-goods-for-export/
- The pallet shall be stretch wrapped.Two pallet labels shall be inserted in between the two layers of shrink filming to each pallet.
- One pallet label at the long side of the pallet and a second label at the short side of the pallet or as per the customer requirements.
- Thermal Blankets shall be used for covering the entire product pallet in case of air shipments depending upon the customer requirement.
- ‘Temperature Sensitive Label’ (Format-VII shall be pasted for all the consignment meant for refrigerated Air shipments).
- Dispatch of Finished Goods:
- Based on Sales Order and stock availability of Finished Goods Warehouse Person shall prepare the Packing List as per the Format-IV.
- The warehouse person will inform the Logistics Department for the arrangement of container/vehicle after the preparation of Packing List.
- On the advice of Warehouse person, the Logistic department shall arrange required trucks / containers for the loading of Finished Products.
- On the basis of Packing List, Pallet Labels shall be prepared and it will be signed with date as per the Format-V.
- As per the SOP Warehouse Personnel shall prepare the Label for pallets as per Format-VIII for every pallet based on packing list and the same shall be pasted on the pallets.
- During the Packing List verification, the Warehouse and IPQA Personnel should check the number of shippers in the loose pallet and sign on the Loose Pallet sticker.
- After verification of Finished Goods, FG Warehouse Person shall sign the Packing List and Pallet Labels.
- Palletized Finished Product/Loose Shippers as per the packing list shall be taken to Dispatch Bay by using hydraulic trolley (If available) into Finished Goods Dispatch Bay.
- For the dispatch of non-palletized shippers, ‘Shipping Mark Label’ shall be prepared and pasted on each shipper as per Sales Order.
- Retailing from shippers shall be done in the presence of IPQA Person and Label for Loose Quantity shall be pasted on the shipper.
- The left-over quantity shall be recorded on the sticker after removal of quantity.
- Both Warehouse and IPQA personnel shall sign the Loose Material Sticker.
- IPQA personnel shall verify the palletized Finished Goods, Packing List and FGTN.
- After completion of verification, IPQA Person shall sign on the Packing List.Signed documents (Packing List & FGTN), COA and Product Labels/Cartons shall be submitted to Customs Department for Invoice preparation.
- Arrange for an inspection of Finished Goods by an inspection agency if required.
- After the verification of Packing List by IPQA Person, Warehouse Person shall inform Customs department for their verification.
- Customs Officer may randomly verify the pallets and other details against packing list.
- The container/vehicle shall be called in for loading of FG.
- Once the cleaned vehicle is placed at the Dispatch Bay, it shall be checked by the Warehouse Person and verified by the IPQA Person.
- Check the temperature inside the container.Ensure that the loading of refrigerated container/vehicle shall be started after reaching the temperature inside the container in the range of 20 to 25°C and the temperature reading shall be noted in the Vehicle Inspection and Dispatch Checklist.
- If more than two Data Loggers are to be sent with the consignment, then the Log of Data Loggers shall be used to capture the relevant details of it.
- On completion of Customs Officer’s verification, Finished Goods shall be loaded into the container.
- Product packs/Labels should not get damaged while loading into the trucks/containers.
- Start the loading activity. Temperature shall be monitored and mentioned in the dispatch check list.
- In case, the temperature exceeds 25ºC (or as per product requirement), immediately stop the loading activity and close the doors of refrigerated container.
- Only after attaining the temperature in the range of 20°C to 25°C (or as per product requirement), the loading activity shall be resumed.
- In the case of loading of shippers, the Warehouse Person shall verify the shippers and tick the Shipper Loading Check List.
- Another person from Warehouse shall check the shippers of the consignment at random and sign the checked by column.
- Pre-Validated Data logger shall be placed in a loose shipper for continuous monitoring of Temperature during transportation.
- Before placement, photographs of the Data Logger shall be taken with the current Temperature on Display.
- If loose shipper is not available, Data logger shall be placed in separate shipper and affix the green label ‘Data Logger Label’.
- While placing the Data Logger inside the shipper, a photograph shall be taken.
- After placement of Data Logger, the sticker shall be signed by the person who is placing the Data Logger inside the box followed by the sign of IPQA Person.
- In case of partial sea shipments, Air bags shall used to fill the empty spaces between pallets to avoid any damages to the shippers in transit.Lashing to be done with nylon straps to avoid the damages during transit.
- Photographs shall be taken, during the loading process for further reference.After completion of loading, trucks/containers shall be sealed.
- The relevant documents shall be handed over to the driver of the vehicle and acknowledgement on NRGP shall be obtained.
- As per the customer requirement, the pre-validated Data Logger certificate shall be handed over to the Driver, along with Dispatch Documents.
- Palletization of Finished Goods:
- For the purpose of dispatch, the Finished Goods shall be arranged on pallets according to Product and Batch Number.
- Pallets having Heat Treatment Certificate shall be used for the palletization of Finished Goods for all Markets.
- The time of departure of the vehicle from the gate shall be recorded in the Format-I.
- Pallet which is used for palletization should comply with the parameters given below:
Click the link to download word file copy of this document:
https://pharmaguidehub.com/product/procedure-for-receipt-storage-palletization-and-dispatch-of-finished-goods-for-export/
- REFERENCES:
Not Applicable
- ANNEXURES:
ANNEXURE NO | TITLE OF ANNEXURE |
Annexure-I | Vehicle Inspection and Dispatch Checklist |
Annexure-II | Log of Data Loggers |
Annexure-III | Label for Loose Quantity |
Annexure-IV | Packing List Specimen |
Annexure-V | Label of PALLET |
Annexure-VI | Shipper Loading Check List |
Annexure-VII | Temperature Sensitive Label |
Annexure-VIII | Pallet Label |
Annexure-IX | Data Logger Label |
ENCLOSURES: SOP Training Record.
- DISTRIBUTION:
- Controlled Copy No. 01 : Head Quality Assurance
- Controlled Copy No. 02 : Head Warehouse
- Controlled Copy No. 03 : Head Production
- Master Copy : Quality Assurance Department
- ABBREVIATIONS:
PGH | : | Pharmaguidehub |
No. | : | Number |
SOP | : | Standard Operating Procedure |
COA | : | Certificate of Analysis |
QA | : | Quality Assurance |
NRGP | : | Non-Returnable Gate Pass |
BPR | : | Batch Production Record |
QA | : | Quality Assurance |
HDPE | : | High Density Polyethylene |
FGTS | : | Finished Goods Transfer Note |
DGFT | : | Director General of Foreign Trade |
FG | : | Finished Goods |
- REVISION HISTORY:
CHANGE HISTORY LOG
Revision No. | Details of Changes | Reason for Change | Effective Date |
00 | New SOP | Not Applicable | To Be Written Manual |
Annexure-I
Vehicle Inspection and Dispatch Checklist
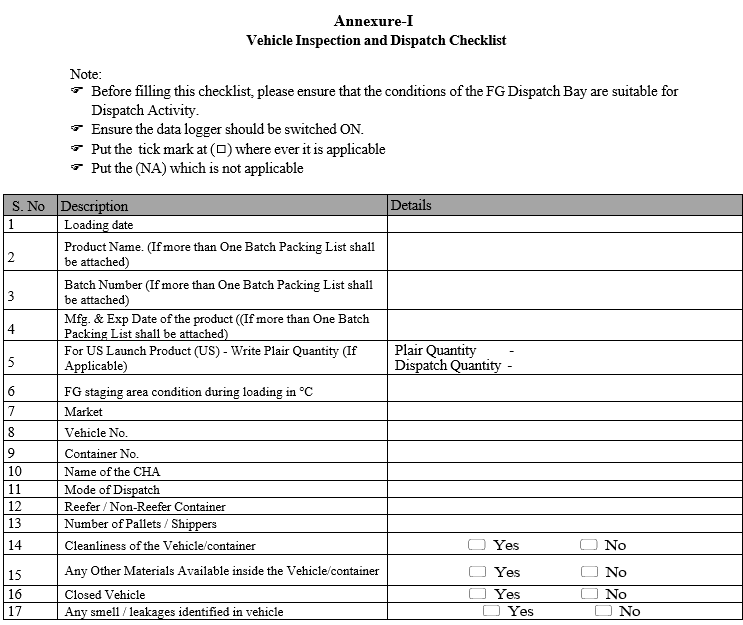
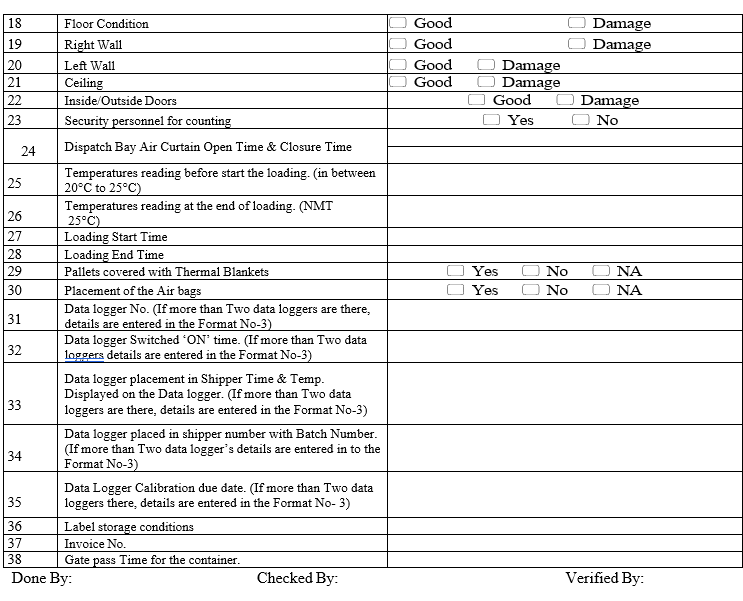
Annexure II
Log of Data Loggers
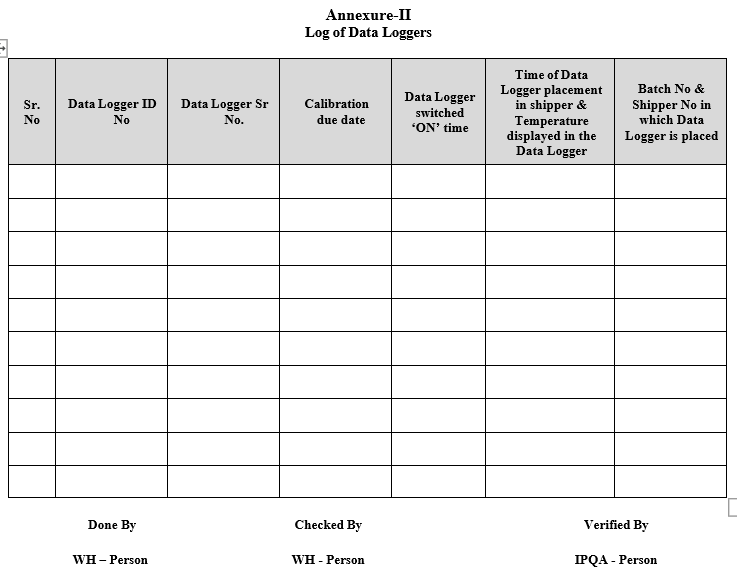
Annexure-III
Label for loose quantity
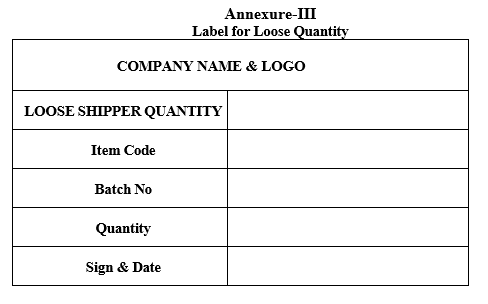
Annexure-IV
Packing List Specimen
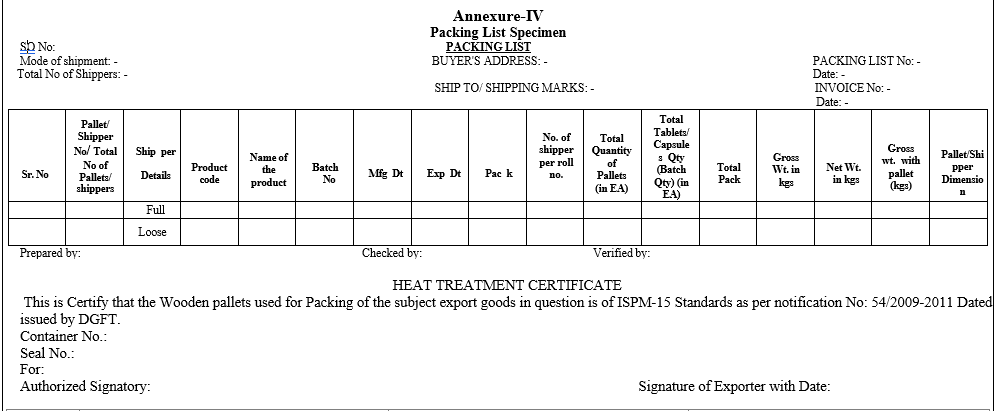
Annexure-V
Label of Pallet
Annexure-VI
Shipper loading Checklist
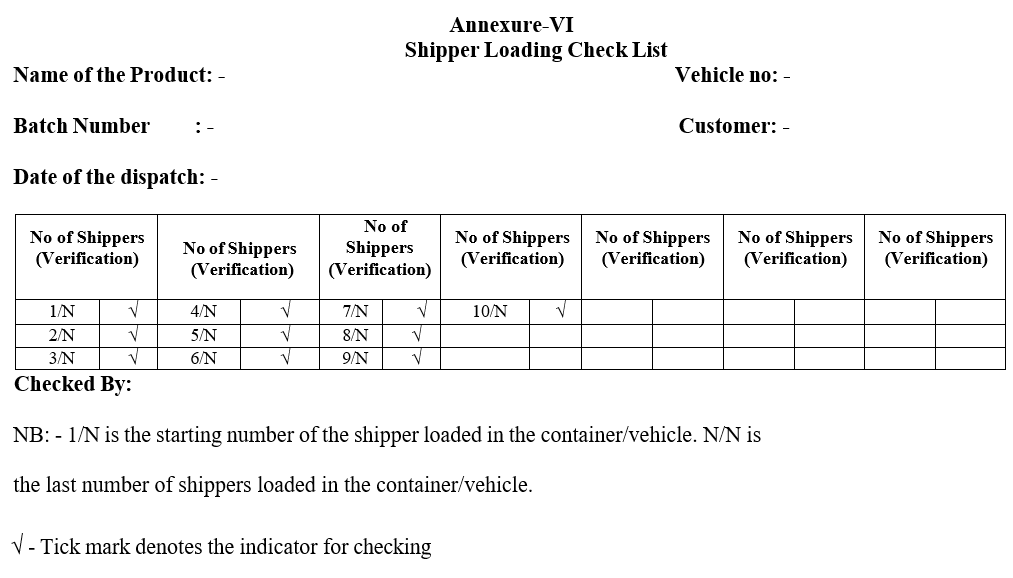
Annexure-VII
Temperature SensitiveLabel
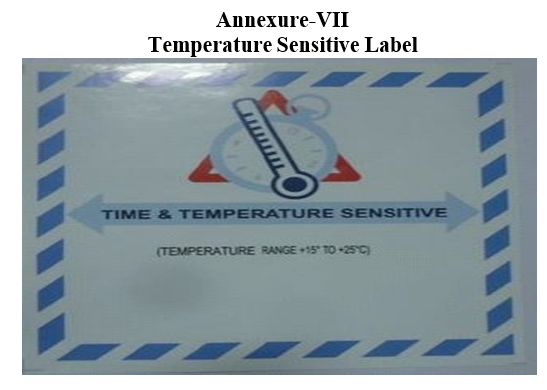
Annexure-VIII
Pallet Label
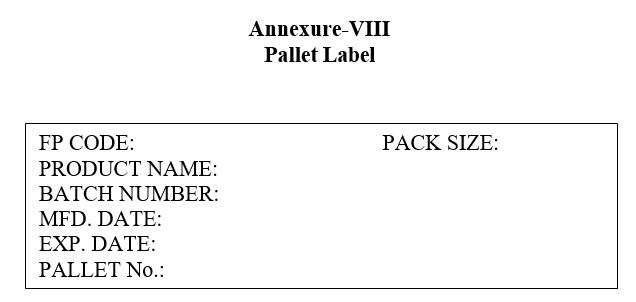
Annexure-IX
Data Logger Label
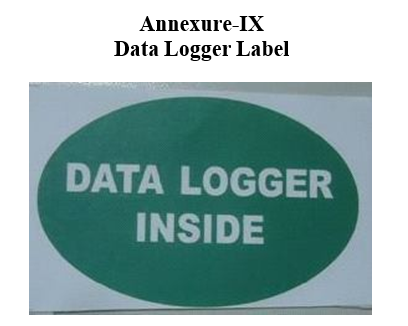
Frequently Asked Question ?
Q: How are completed batches of finished goods transferred from packing to storage?
A: They are transferred with a Finished Goods Transfer Note (FGTN), verified by IPQA, and checked for quantity and damage by warehouse personnel.
Q: How are finished goods stored within the warehouse?
A: They are organized on pallets in designated locations according to recommended storage conditions.
Q: What are the key steps involved in palletizing finished goods for dispatch?
A: Pallets are chosen based on market requirements, goods are arranged by product and batch, and specific pallet types/sizes are used. Stacking shall be evalute as per stack height monitoring and configuration consider customer height requirements and label visibility. Pallets are then strapped, shrink-wrapped, and labeled.
Q: How is the packing list prepared for dispatch?
A: It’s based on sales orders and stock availability, and specific formats are used.
Q: What happens after the packing list is prepared?
A: The logistics department is informed for vehicle/container arrangement, pallet and pallet labels are generated, and packing list and loose pallet quantities are verified. Documents and certificates are submitted to customs.
Q: What are the key checks performed before loading finished goods onto the vehicle/container?
A: The vehicle/container is inspected and its temperature is monitored (especially for refrigerated shipments). Data loggers might be used for temperature tracking. Goods are loaded carefully to avoid damage, and temperature is monitored during loading. Specific procedures are followed for loose shipper loading and partial sea shipments.
Q: What happens after loading is complete?
A: The vehicle/container is sealed under supervision, documents are handed over to the driver, and the departure time is recorded.
Click the link to download word file copy of this document:
https://pharmaguidehub.com/product/procedure-for-receipt-storage-palletization-and-dispatch-of-finished-goods-for-export/