- OBJECTIVE:
- To lay down the procedure for handling of Rejected/Expired material in warehouse.
- SCOPE:
This SOP is applicable for the active material dispensing in the Isolator in the warehouse department at {Company Name} {Location}.
- RESPONSIBILITY:
- WH Executive/Designee – is responsible for ensuring compliance with the SOP.
- QC Executive/Designee- shall be responsible to affix Rejected Label on the rejected material.
- Head Warehouse – is responsible for compliance of the SOP.
- ACCOUNTABILITY:
QA Head shall be Accountable for implementation of SOP.
- PROCEDURE:
- The Process/Material Non-Conformance whichever applicable, shall be initiated by concerned responsible personnel in the following scenarios but not limited:
- Material Received Report (MRR) Rejections – shall be initiated by Warehouse In-Charge/Analytical assurance Executive.
- On-line Rejections – shall be initiated by the Production In-Charge /Manufacturing Assurance In-Charge and/or Warehouse.
- Expired materials – shall be initiated by the Warehouse.
- Obsolete materials– shall be initiated by the Warehouse.
- All the Obsolete/Non-moving materials shall be labelled with the “REJECTED” label in RED colour on the material by QA department.
- Damaged materials during receipt shall be handled as per SOP.
- MRR REJECTIONS:
- “R E J E C T E D” label in RED colour shall be provided on all containers/boxes of rejected material by QC department.
- All the rejected materials shall be segregated Lot No. Wise and stored separately in “Rejected materials” storage area under lock & key.
- The material details shall be entered in the “Rejected Material Stock Register”.
- The Process/Material Non-Conformance shall be initiated by the Analytical Assurance Executive/Warehouse In-charge for the Material received rejections as per SOP.
- PNC/MNC shall be reviewed and approved by QA In-Charge.
- QA In-Charge shall select the concerned Warehouse In-Charge as the CAPA Owner for carrying out the disposition of the rejected material.
- On receiving the disposal instructions from purchase, Warehouse personnel shall start the disposal procedure of the material (i.e., sending back to the supplier/destroying the material by handing over to safety & health department or physical destruction (packing materials) as the case may be and the stores personnel shall update the rejected material stock register).
- CAPA Owner shall select the concerned persons as CAPA team members for disposal of the rejected material.
- The CAPA Owner shall fill the details of the disposition in the Remedial Actions. After completion of the Remedial Action steps, the CAPA Owner shall submit the Remedial Actions Header.
- The final approval of Remedial Action Steps shall be done by CAPA Co-coordinator (QA In-Charge).
- The destruction record shall be maintained by the safety & health department.
- ON-LINE REJECTIONS:
- If any raw material/packing material is found not conforming during production/packing activity PNC/MNC whichever applicable shall be initiated as per SOP by the concerned Production In-Charge / Manufacturing Assurance In-Charge / Executive.
- The Manufacturing Assurance Executive shall counter sign on the ‘Rejected’ Label.
- Intimate to the respective Section In-Charge and Manufacturing Assurance In-Charge for further action.
- The rejected raw/packing material shall be segregated and affix “ONLINE REJECTION” label.
- Respective Section in-Charge/Manufacturing Assurance In-Charge- shall verify all details like Material Manufacturer, Supplier, Quantity Rejected, MRR No., D.C. No. reason for rejections and mention the details in the MNC.
- Initiator shall carry out preliminary investigation for the PNC/MNC.
- MRR REJECTIONS:
- The initiator shall confirm the quantity of material received in the On-line rejected lot.
- Initiator shall confirm whether the same lot material has been used for Manufacturing/packing in other batches.
- If the On-line rejected lot material has been used in other batches, the control sample of the same shall be verified for any such defects.
- The preliminary investigation shall be uploaded as an attachment by the respective Section In-Charge to the initiated PNC/MNC, wherever required.
- PNC/MNC shall be reviewed and approved by QA In-Charge.
- The Warehouse Head shall intimate purchase department for disposal of the material.
- QA In-Charge shall select the concerned Warehouse In-Charge as the CAPA Owner for carrying out the disposition of the On-line rejected material.
- Production shall transfer the material to Warehouse after approval of QA In-Charge/Head QA
- The Warehouse Head shall intimate purchase department for disposal of the material.
- On receiving the disposal instructions from Purchase, In-Charge QA shall enter the mode of disposal of the material (i.e., sending back to the supplier/destroying the material as the case may be).
- CAPA Owner shall start the disposal activity by selecting the concerned persons as CAPA team members for disposal of the On-line rejected material.
- The material shall be disposed of by the Safety Executive by Shredding of all the On-line rejected cartons/labels/containers and shippers by using scissors into the small pieces.
- Collect the pieces of shippers, cartons, containers and labels into a poly bag and transfer to scrap yard through trolley for further disposal.
- The raw material shall be disposed of by the Safety Executive as per SOP.
- The disposition of the material shall be witnessed by the Respective Section In-Charge and Manufacturing Assurance In-Charge.
- The SAFETY & HEALTH DEPARTMENT Executive shall fill in the material disposal details in the destruction record form.
- All the concerned persons who witnessed the disposal shall sign on the destruction record.
- After completion of the Remedial Action steps, the CAPA Owner shall submit the Remedial Actions Header.
- The final approval of Remedial Action Steps shall be done by CAPA Co-coordinator (QA In-Charge).
- The destruction record shall be maintained by the SAFETY & HEALTH DEPARTMENT.
- Entries shall be made in the Rejected Materials Stock Record after disposal.
- HANDLING OF THE EXPIRED MATERIALS:
- Warehouse personnel shall identify the Expired material. The expired materials shall be labelled by QA department with the “EXPIRED” label in RED color on the material.
- All the expired materials shall be labelled by QA department with the “EXPIRED” label in RED color on the material.
- All expired materials shall be segregated by Lot Number wise and stored separately in rejected material storage area.
- MNC shall be raised for the expired material.
- The quantities shall be checked and material details shall be entered in the Expired Material Stock Record.
- Disposal Record for Expired materials shall be raised and same shall be intimated to Planning department for disposal instructions.
- On receiving the disposal instruction from planning/Purchase department, warehouse personnel shall start the disposal procedure by handing over to SAFETY & HEALTH DEPARTMENT or physical destruction as the case may be and the warehouse personnel shall update the expired material stock register.
- MNC shall be reviewed and approved by QA In-Charge.
- QA In-Charge shall select the concerned Warehouse In-Charge as the CAPA Owner for carrying out the Disposition of the Expired material.
- CAPA Owner shall select the concerned persons as CAPA Team members for disposal of the Expired material.
- The material shall be disposed of by the SAFETY & HEALTH DEPARTMENT Executive as per SOP.
- The CAPA Owner shall fill in the details of the disposition in the Remedial Action. After completion of the Remedial Action steps; the CAPA Owner shall submit the Remedial Actions Header.
- The final approval of remedial Action Steps shall be done by CAPA Co-Ordinator (QA In-Charge).
- The physical destruction record shall be maintained by the SAFETY & HEALTH DEPARTMENT.
- Warehouse personnel shall maintain the Disposal Record for Expired Materials.
- NON-MOVING MATERIAL:
- Disposal Record for non-moving materials shall be raised as per format-V.
- Based on the destruction note all Non-moving material shall be segregated by Lot no wise and stored separately in the rejected material storage area
- The quantities shall be checked and material details shall be entered in the Rejected Materials Stock Register.
- QA shall fill in the “REJECTED” labels and affix the labels.
- After completion of commercial formalities, the non-moving materials shall be destroyed by SAFETY & HEALTH DEPARTMENT executive in presence of Section In-Charge.
- The Safety executive shall fill the material disposal details in the destruction record form.
- All the concerned persons who witnessed the disposal shall sign on the destruction record.
- The destruction record shall be maintained by the SAFETY & HEALTH DEPARTMENT.
- Entries shall be made in the Rejected material stock record after disposal.
- OBSOLETE MATERIALS:
- Disposal Record for obsolete materials shall be raised as per format-V.
- On receiving the approval for the disposal record for obsolete materials Warehouse personnel shall initiate MNC as per SOP.
- Based on the destruction note all obsolete material shall be segregated by Lot no wise and stored separately in the rejected material storage area.
- The quantities shall be checked and material details shall be entered in the Rejected Material Stock Register.
- QA shall fill in the “REJECTED” labels and affix the labels.
- QA personnel shall be forward the issue details report after approval of the initiated PNC / MNC by in charge QA and/or Head QA to the Warehouse department for destruction of the obsolete materials as per SOP.
- The material shall be destroyed by the Safety executive in presence of Section In-Charge.
- The Safety & Health department executive shall fill in the material disposal details in the destruction record form.
- All the concerned persons who witnessed the disposal shall sign on the destruction record.
- The destruction record shall be maintained by the Safety & Health department.
- Entries shall be made in the Rejected material stock record after disposal.
- STORAGE OF MRR REJECTIONS/ON-LINE REJECTIONS/EXPIRED MATERIALS/NON-MOVING MATERIAL/OBSOLETE MATERIALS/DAMAGED/SPILLED MATERIAL DURING MATERIAL HANDLING:
- MRR Rejections/On-Line Rejections/Non-Moving Material/Obsolete Materials/Damaged/ Spilled Material during Material Handling of raw materials and packaging materials shall be stored in Rejected material storage area.
- Expired materials of raw materials and packaging materials shall be stored in the Rejected material storage area.
- Expired/Obsolete/Non-Moving/Damaged/Spilled Material during Material Handling shall be disposed off.
- REFERENCES:
Not Applicable
- ANNEXURES:
ANNEXURE NO | TITLE OF ANNEXURE |
Annexure-I | Rejected Material Stock Record |
Annexure-II | Expired Material Stock Record |
Annexure-III | Online Rejection Label |
Annexure-IV | Expired Label |
Annexure-V | Disposal Record for Expired/Obsolete/Non-Moving Material/ Damaged/Spilled Material during Material Handling |
ENCLOSURES: SOP Training Record.
- DISTRIBUTION:
- Controlled Copy No. 01 : Head Quality Assurance
- Controlled Copy No. 02 : Head Warehouse
- Master Copy : Quality Assurance Department
- ABBREVIATIONS:
No. | : | Number |
SOP | : | Standard Operating Procedure |
CAPA | : | Corrective And Preventive Actions |
MRR | : | Material Received Report |
PNC | : | Process Non Conformance |
MNC | : | Material non conformance |
QA | : | Quality Assurance |
- REVISION HISTORY:
CHANGE HISTORY LOG
Revision No. | Details of Changes | Reason for Change | Effective Date |
00 | New SOP | Not Applicable | To Be Written Manual |
Annexure-I
RejectedMaterialStock Record
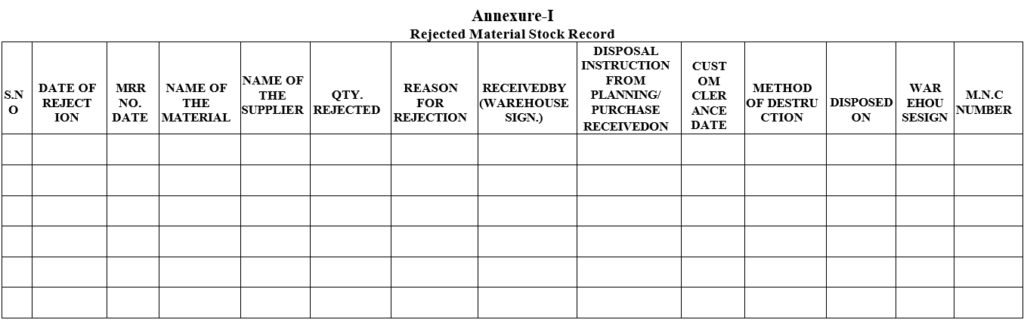
Annexure-II
Expired Material Stock Record
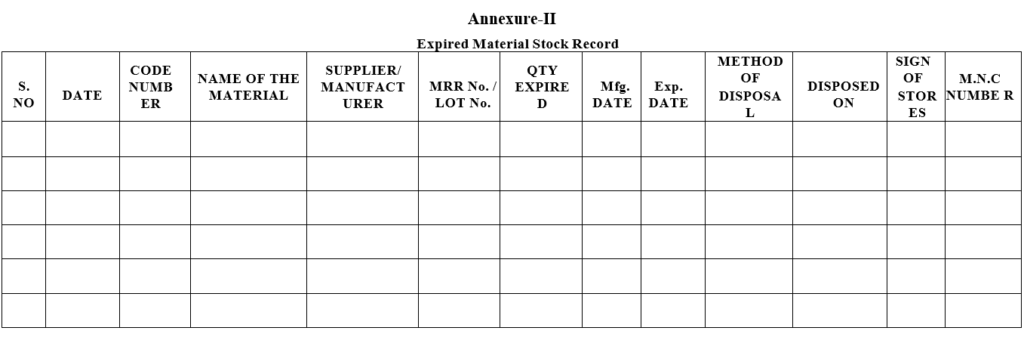
Annexure-III
Online Rejection Label
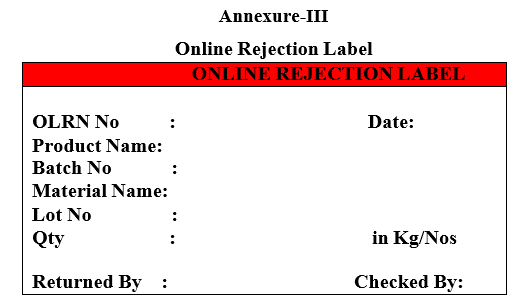
Annexure-IV
Expired Label
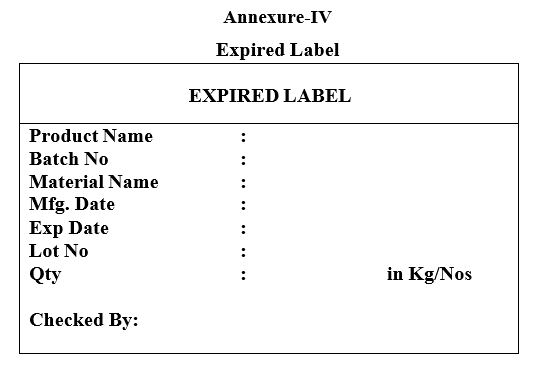
Annexure-V
Disposal Record for Expired/Obsolete/Non-Moving Material/Damaged/Spilled Material during Material Handling
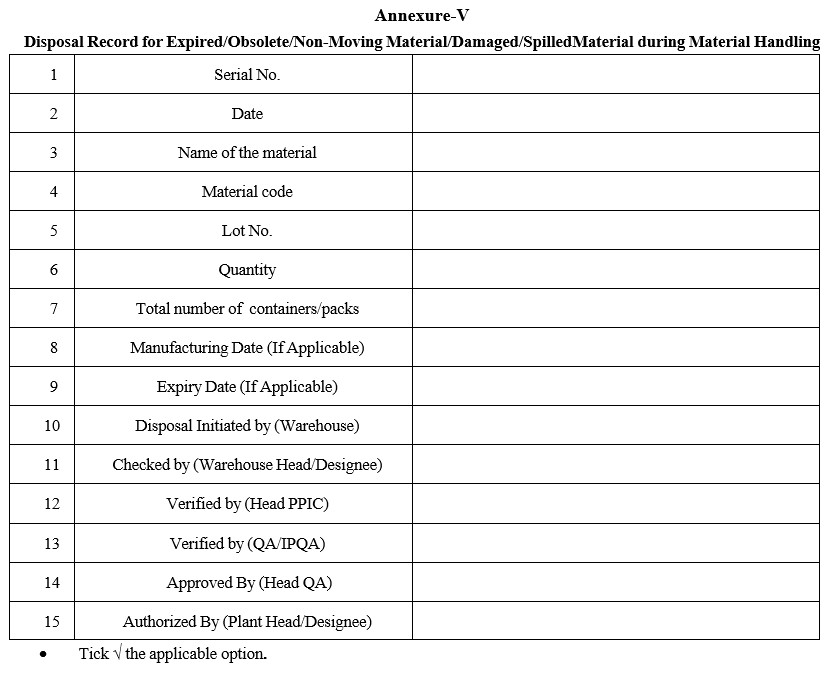
Frequently Asked Question ?
Question 1: How does a warehouse identify expired materials?
Answer: Warehouse personnel are responsible for identifying expired materials. The QA department labels these materials with a red “EXPIRED” label.
Question 2: What happens to rejected materials after they are identified?
Answer: All rejected materials are:
- Segregated by lot number and stored in a designated “Rejected Materials” area.
- Labeled with “REJECTED” or “ONLINE REJECTION” by the QA department.
- Documented in the “Rejected Material Stock Register.”
- Disposed of according to specific procedures depending on the reason for rejection.
Question 3: Who is responsible for initiating a Process/Material Non-Conformance (PNC/MNC)?
Answer: The responsible personnel initiate a PNC/MNC depending on the scenario:
- MRR Rejections: Initiated by Warehouse In-Charge/Analytical Assurance Executive.
- On-line Rejections: Initiated by Production In-Charge/Manufacturing Assurance In-Charge or Warehouse.
- Expired Materials: Initiated by the Warehouse.
- Obsolete Materials: Initiated by the Warehouse.
Question 4: What happens to obsolete materials after they are identified?
Answer: Obsolete materials follow a similar process to rejected materials:
- Segregation by lot number and storage in the “Rejected Materials” area.
- Labeling with “REJECTED” by the QA department.
- Documentation in the “Rejected Material Stock Register.”
- Destruction by the Safety & Health department after commercial formalities.
- Record keeping of the destruction process.
Question 5: How are expired materials disposed of?
Answer: Expired materials can be disposed of in two ways:
- Returned to the supplier: This requires approval from the Purchase department.
- Destroyed: The Safety & Health department handles the physical destruction, and a record is maintained.