- OBJECTIVE:
- To describe a standard operating procedure for Permit to Work at Height.
- SCOPE:
- This Procedure is applicable for height work permit at {Company Name} {Company Location}.
- RESPONSIBILITY:
- EHS Department in-charge / designee shall be,Responsible to make availability of Permit to Work at Height to concern department.Responsible to inspect the area where work will be executed and authorize the Permit to Work at Height.
- Concerned Department Employee shall be,Responsible to initiate the Permit to Work at Height.Responsible to ensure that all safety precautions are followed during the execution of work.
- Concerned Department Heads shall be, Responsible to approve the Permit to Work at Height and ensure that all safety precautions are followed during the execution of work.
- Engineering Department Head shall be,Responsible for the approval of Height Work Permit.
- Plant Head shall be,Responsible for the approval of work permit in case of extension.
- ACCOUNTABILITY:
- QA Manager shall be accountable for Approval & Implementation of SOP.
- PROCEDURE:
- Permit to Work at Height (Annexure-I) is required for all the jobs that are carried at a height of more than 2 meters, where there is no proper platform and where there is a high risk for carrying the work at height.
- The permit shall be given a serial number of YY/MM/NNN where, YY is the last two digits of the year, MM is the month and NNN is the sequential number. The number starts from 001 every January. For example, 16/01/001.
- The person who plans the job shall initiate the permit and he should not be less than an Executive cadre.
- The Permit Initiator shall ensure that all safety precautions mentioned in the work permit are taken before issuing the permit.
- Permit holder shall be the maintenance supervisor or person responsible for execution of job.
- The permit holder must understand the permit conditions thoroughly and should comply with all conditions stipulated in the permit. He or his authorized/designated supervisor should be present at the work site all the time when work is going on. He is responsible for the safe completion of work.
- Block / area in-charge and Engineering & Utility Head shall ensure the compliance of Permit to work at height requirements and sign at the designated places on the format.
- EHS representative shall check the work area for compliance of permit conditions mentions the additional safety precautions needed if any and permits to work at height by signing at designated place on the permit.
- The permit is valid for the period it is issued on the given day in general shift hours.
- Any extension/ continuation of the work beyond the permitted time shall be done only after checking and ensuring that all the precautions mentioned in the permit are taken and approved by the Plant Head or his designee.
- The EHS Department representative also shall check the conditions and signs at the designated place.
- The work permit shall be automatically rendered invalid if permit conditions are not complied with i.e. in case if an emergency declared / Violation during work execution/ Change in weather conditions.
- On completion of the work, the work place in-charge & Maintenance supervisor shall check and ensure that the all men, all material etc., are removed from the work place and sign on the designated place of the permit for certification of completion of work.
- First copy (white) of the permit shall be handed over to the initiating department and second copy to the EHS department after Completion of Work.
- The completed permit shall be retained for six months with the EHS department.
- In case of any Incident/Accident happening during the execution of this permitted job or within six months, the permit is to be attached to the Incident Report and shall be retained in EHS department till the statutory requirements are compiled / completed.
Flow Chart of Work Permit to Height
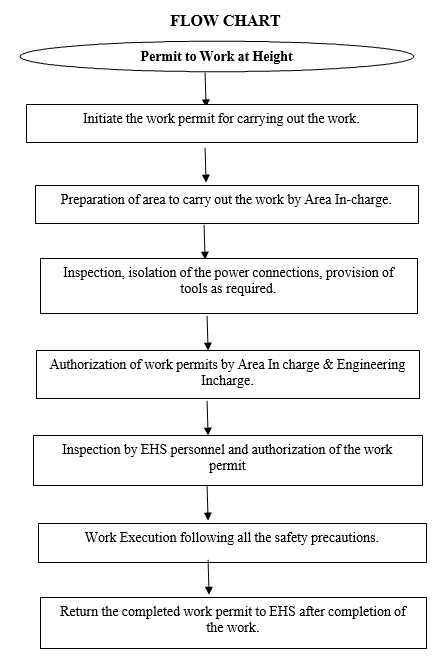
- REFERENCES:
Not Applicable
- ANNEXURES:
ANNEXURE No. | TITLE OF ANNEXURE |
Annexure-I | Personal Protective Equipment Specifications |
- ENCLOSURES: SOP Training Record.
- DISTRIBUTION:
Controlled Copy No. 01 | : | Safety Health & Environment |
Master Copy | : | Quality Assurance Department |
- ABBREVIATIONS:
PPE | : | Personal Protective Equipment. |
SOP EN IN | : : : | Standard Operating Procedure European Norms. Indian Standard. |
- REVISION HISTORY:
CHANGE HISTORY LOG
Revision No. | Details of Changes | Reason for Change | Effective Date |
00 | New SOP | Not Applicable | To be written manual |
ANNEXURE-I
HEIGHT WORK PERMIT
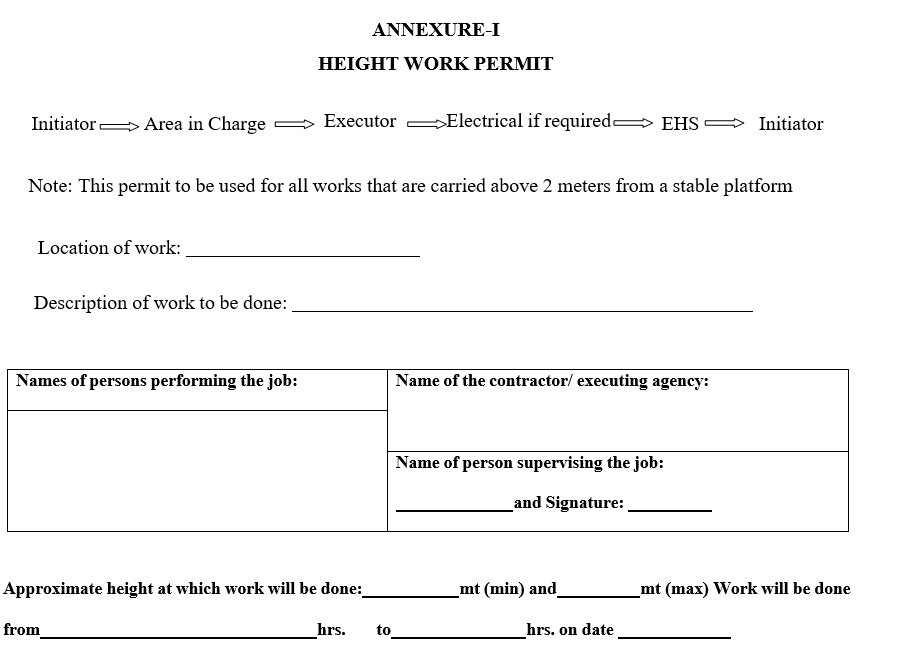
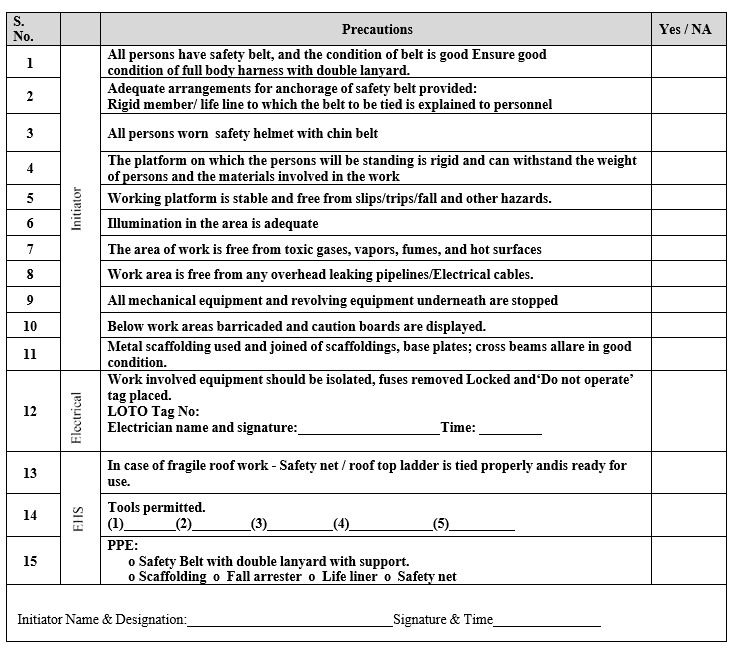
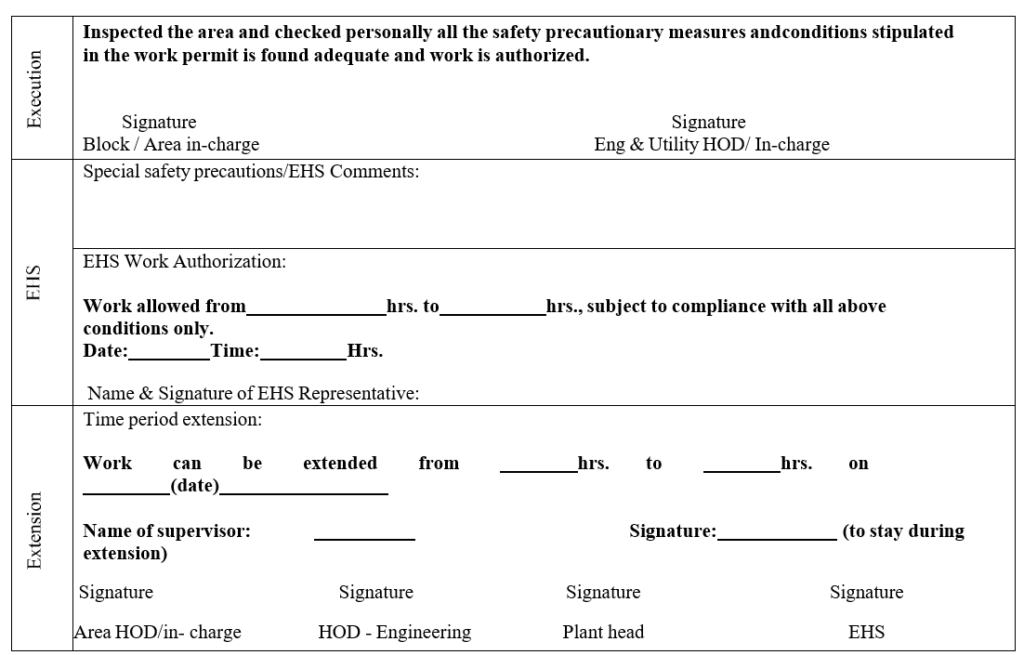
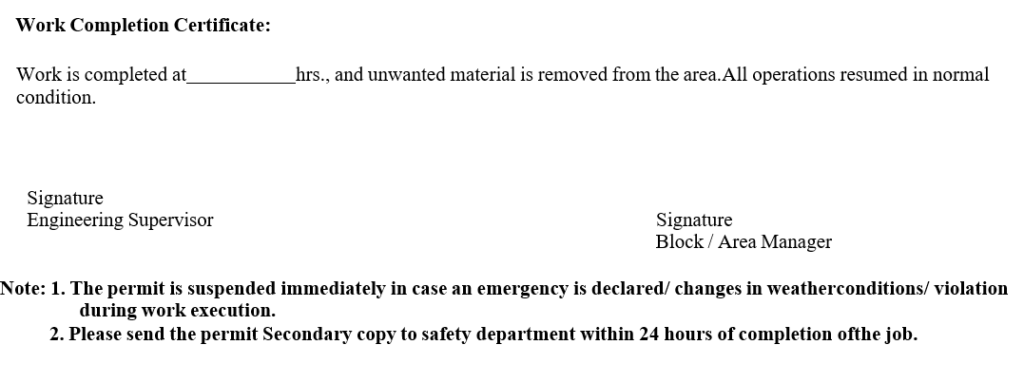
Frequently Asked Question ?
- What is the purpose of a Permit to Work at Height?
- To ensure the safety of workers performing tasks at heights exceeding 2 meters, with no proper platform and high risk involved.
- How is the permit identified?
- A serial number is assigned using YY/MM/NNN format (last two digits of year, month, sequential number starting from 001 each January).
- Who initiates the permit?
- The person planning the job, who must be at least an Executive cadre.
- What are the responsibilities of the Permit Initiator?
- Ensure all safety precautions in the permit are fulfilled before issuing it.
- Who is the permit holder?
- The maintenance supervisor or person responsible for executing the job.
- What are the responsibilities of the permit holder?
- Understand and comply with all permit conditions.
- Be present at the worksite throughout the task.
- Ensure safe completion of the work.
- Who else needs to sign the permit?
- Block/area in-charge and Engineering & Utility Head.
- EHS representative (after ensuring permit compliance and potentially suggesting additional precautions).
- What is the permit’s validity period?
- The day it’s issued, during general shift hours.
- How can work be extended beyond the permitted time?
- Only after re-checking all precautions and obtaining approval from the Plant Head or designee, with confirmation from the EHS representative.
- What happens after work completion?
- Workplace in-charge and maintenance supervisor ensure all personnel and materials are removed, then sign on the permit to certify completion.
- How are permit copies handled?
- First copy (white) goes to the initiating department, second copy to EHS department.
- How long is the completed permit kept?
- Six months with the EHS department.
- What happens in case of an incident or accident?
- The permit is attached to the incident report and kept by EHS until all statutory requirements are met.