- OBJECTIVE:
To lay down a procedure for cleaning of Filters.
- SCOPE:
This SOP is applicable for cleaning of Filters at {Company Name} {Company Location}.
- RESPONSIBILITY:
- Technical Assistant – Engineering is responsible for the SOP.
- Executive – Engineering responsible to ensure the SOP.
- Head / Designee– Engineering is responsible for compliance of the SOP.
- ACCOUNTABILITY:
Engineering Head
Head Quality Assurance
- PROCEDURE:
- PRECAUTIONS
- Switch OFF the power supply to the equipment before removing the filter.
- Handle the filters carefully.
- Before fixing filters must be in dry condition.
- Don’t damage the filter media and tubular spacers.Clean the Bag type filters with compressed air.
- Do not use water for cleaning.
- Clean the H.D.P.E filters with compressed air and raw water.
NOTE: Wear personal protective Equipment before cleaning the filters.
- FILTER DISMANTLING PROCEDURE
- Open the screws and keep in a tray.
- Check the filter condition.
- Check the filter gasket and filter media, if any damage observed replace the filter.
- CLEANING PROCEDURE
- Wherever possible Measure the pressure drops across the filter before dismantling and record it in the filter cleaning Log.
- Put the filter into Poly Bag and transfer the filters to the uncleaned filters Room.
- Both the AHU and Return air riser filters are identified with “UNCLEANED FILTERS” status label as per Foramt-2 on the polythene covers. This status label shall be verified by Engineering personal.
- Check that compressed air pressure is regulated to 1.0 to 2.0 kg/cm².
Click the link to download word file copy of this document:
https://pharmaguidehub.com/product/cleaning-procedure-for-filters/
- Shift the filters to the filters cleaning area.
- Remove the filters from the poly bag and keep the poly bags in dustbin.
- Tap the filters gently by hand on floor with up steam (dirty) side facing down to floor to dislodging all loose particles.
- Clean the filters with compressed air jet at about 1.0 to 2.0 Kg/cm² jet directing at an angle towards downstream.
- Simultaneously the dust dislodges is clean by a vacuum cleaner in take nozzle kept and slightly away from the surface of the filter media at the upstream side.
- Clean the filters with raw water of 0.5 to 1 kg/cm².
- Finally rinse with Potable water.Ensure the filters are completely dry, keep them in new poly bags and shift them to cleaned filter room.
- Re-installed the filters in the respective equipment and measure the pressure drop across the filter (wherever possible) and note down in the filter cleaning log. If the filter pressure drop still exceeds the maximum limit replace the filter with new filter.
- Both the AHU and Return air riser filters are identified with “CLEANED FILTERS” status label as per Format-3 on the polythene covers. This status label shall be verified by Engineering personal.
- If spare filters are available, install it and clean and store the removed filters.
- Clean the Return Air Riser filters and grills with purified water in respective washing areas.Record the filter cleaning details in Filter Cleaning Record, Annexure -1.Replace the filters in case of damage.
- While performing the cleaning operation any major damage of filters/unit observed, the corrective measures shall be taken in co-ordination with validation department.
- Check for fixing of filters with respect to numbering.
- Tighten all the bolts of the filters and service doors.
- Switch on the main Supply.
- Check the service door if any leakage observed, replace with new gasket.
- All 5µ filters of AHU to be cleaned with compressed air only.
- All 10 µ and return air riser filters to be cleaned with potable water and compressed air only.
- All 5µ filters of LAF, sampling booths, dispensing booths, powder containment booths and dehumidifiers and Pre Filters of BagIn-BagOut unit should clean with compressed air only.
- All FBP, FBD and Coating Machine AHU’s filters should clean with compressed air.
- Filter cleaning Area Cleaning Procedure
- Remove the filter from vacuum cleaner and clean it with air.
- Mop the vacuum cleaner inside and out side with dry cloth.
- Clean the walls and exhaust fan in the cleaning area.
- Remove the used poly bags from dustbin and shift to scrap yard.
- Dustbin shall be cleaned.
- After completion of cleaning activities, the area shall be cleaned with raw water.
- Floor mopping shall be done.
- Return Air Raiser Filters
- Every product changes over.
- whenever Differential Pressure across the room does not meet the limit.
- The filter cleaning frequency for process areas shall be 15 ± 3 days and for non process areas shall be 30 ± 7 days.
- When the Process area is idle for more than 30 days then the return air filters will be cleaned on the 31st day.
Note: The above points shall be applicable for LAF, Dispensing Booth, and Sampling Booths.
- AHU Filters
- Every product changes over.
- When Ever Differential Pressure across the filters does not meet the limit.
- The filter cleaning frequency for process areas shall be 15±3 days and non-Process areas shall be 30±7 days.
- Differential pressure limits of filters:
Description | 3 Micron Filter | 5Micron Filter | 10 Micron Filter |
Air Handling unit | NA | 8-20 mm of WC | 4-16 mm of WC |
Air Handling Unit of Fluid Bed Processor and Coating Machine | 8-24mm of WC | NA | 2-10 mm of WC |
Dispensing Booth | NA | 4-10 mm of WC | 1-4 mm of WC |
- REFERENCES:
Not Applicable
- ANNEXURES:
ANNEXURE No. | TITLE OF ANNEXURE |
Annexure-I | Filters Cleaning Record |
Annexure-II | Status Label for Uncleaned Filters |
Annexure-III | Status Label for Cleaned Filters |
ENCLOSURES: SOP Training Record.
- DISTRIBUTION:
- Controlled Copy No. 01 Head Quality Assurance
- Controlled Copy No. 02 Head-Engineering
- Master Copy Quality Assurance Department
- ABBREVIATIONS:
AHU : Air Handling Unit.
Kg/Cm² : Kilograms per square centimeters.
LAF : Laminar Air Flow.
FBP : Fluid Bed Processor
H.D.P.E : High Density Polyethylene
mm of WC : Milli meter of Water Column
- REVISION HISTORY:
CHANGE HISTORY LOG
Revision No. | Details of Changes | Reason for Change | Effective Date |
00 | New SOP | Not Applicable | To be written manual |
ANNEXURE-I
FILTERS CLEANING RECORD

ANNEXURE-II
STATUS LABEL FOR UNCLEANED FILTERS
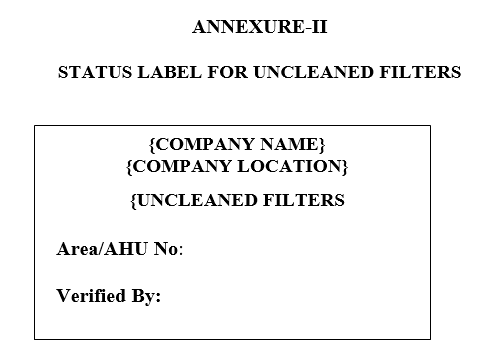
ANNEXURE-III
STATUS LABEL FOR CLEANED FILTERS
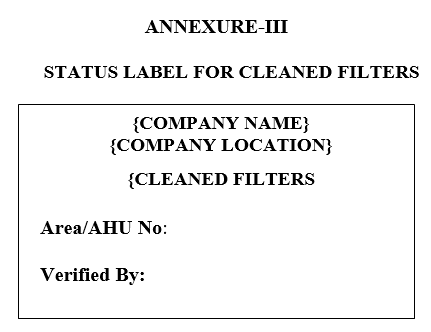
Click the link to download word file copy of this document:
https://pharmaguidehub.com/product/cleaning-procedure-for-filters/