- OBJECTIVE:
To lay down a procedure for Predictive / breakdown maintenance of equipment / instrument.
- SCOPE:
This SOP is applicable for Predictive / breakdown maintenance of equipment / instrument at {Company Name} {Company Location}.
- RESPONSIBILITY:
- Technical Assistant – Engineering is responsible to perform the activity as per the SOP.
- Executive – Engineering is responsible to ensure the compliance of the SOP.
- ACCOUNTABILITY:
Engineering Head
Head Quality Assurance
- PROCEDURE:
- Procedure for breakdown of equipment / instrument to the engineering department:
- The concerned department personnel shall initiate break down request memo (Annexure-I) for any breakdown of equipment / instrument to the engineering department.
- In break down request memo concerned department shall specify the nature of the breakdown and activity being carried out at the time of breakdown along with nature of work, i.e. Mechanical, Electrical, and HVAC etc.
- Concerned department personnel shall sign with date and time in the issued by column and then forward the request to the engineering in-charge / executive.
- The engineering in-charge / executive who receives the request memo shall assign the request number and sign with date and time in the received by column and allocate the concerned technical assistant to attend the breakdown.
- The technical assistant shall label the equipment/instrument UNDER BREAKDOWN LABEL (annexure-III), attend to the breakdown immediately and initiate corrective action and rectify the fault.
- If the breakdown is not able to be rectified in house, same shall be intimated to concerned supplier.
- Concern engineer from supplier will complete the breakdown and submit the report, engineering person shall verify and attached the report along with the breakdown memo.
- After completion of the maintenance activity the engineering executive shall review the work, by duly checking the machine or equipment for its correct functioning.
- If the Breakdown occurred has any impact on the potential quality of the product, then Process Non- Conformance (PNC) shall be raised as per respective SOP and the non-conformance number shall be mentioned in Annexure-I.
- If any planned deviation or if the Breakdown of the equipment/instrument occurs during the Preventive maintenance schedule, then exception shall be raised by the Engineering Department as per SOP and the exception shall be mentioned in Annexure-I.
- The scheduled PMP shall be performed after the Breakdown completion and the same shall be mentioned in the Annexure-II.
- The concerned Engineering personnel shall record the list of components (s) replaced if any and sign in the attended by column with date and time in the equipment history card as per Annexure-II.
- The re-occurrence of Breakdown shall be mentioned in the Breakdown request memo as per Annexure-I by referring the Breakdown Request Memo List as per Annexure-IV
- After completion of the maintenance work, the details shall be recorded in the Breakdown request memo.
- The break down request memo shall then be forwarded to validation department for final review.
- The validation department shall review the request memo and the department personnel shall give the comments and conclusion with sign and date.
- The initiating department shall check the Equipment / Instrument for its correct functioning. A unique number shall be assigned for breakdown request memo.
AAA/ENG/BRM/XX/YYY
AAA: Indicate Abbreviations of company Name
EG: Indicate engineering department.
BRM: Indicate Breakdown request Memo.
XX: Indicate the year
YYY: Indicate serial No. start from 001,002,003………
For e.g the first breakdown number for the year 2024 is AAA/EG/BRM/24/001.
- Based on repeated breakdowns (if any) for individual equipments, trend analysis shall be prepared on a quarterly basis as per Annexure-V.
- The changes ones approved by Head of QA shall be recorded in the respective equipment history card as per Annexure II.
- The Engineering personnel review the equipment history card as per Annexure-II, after each Break down.
- The Breakdown request number shall be recorded along with the Equipment identity Number Equipment Name along with its description as per Annexure-IV and Annexure-IV shall be retained with the Engineering department and updated as per the Breakdown request memos.
- Based on break down trend analysis report if the breakdowns are re-occurred ≥ 3 times, then preventive maintenance schedule or Preventive maintenance check list for the equipment/instrument shall be revised accordingly.
- REFERENCES:
Not Applicable
- ANNEXURES:
ANNEXURE No. | TITLE OF ANNEXURE |
Annexure-I | Breakdown Request Memo |
Annexure-II | Equipment History card |
Annexure-III | Under breakdown label |
Annexure-IV | Breakdown Request Memo List |
ENCLOSURES: SOP Training Record.
- DISTRIBUTION:
- Controlled Copy No. 01 Head Quality Assurance
- Controlled Copy No. 02 Head-Engineering
- Master Copy Quality Assurance Department
- ABBREVIATIONS:
HVAC : Heating, ventilation, and air conditioning
SOP : Standard operating procedure
QA : Quality Assurance
BRM : Breakdown Request Memo
PNC : Process non-conformance
- REVISION HISTORY:
CHANGE HISTORY LOG
Revision No. | Details of Changes | Reason for Change | Effective Date |
00 | New SOP | Not Applicable | To be written manual |
ANNEXURE-I
BREAKDOWN REQUEST MEMO
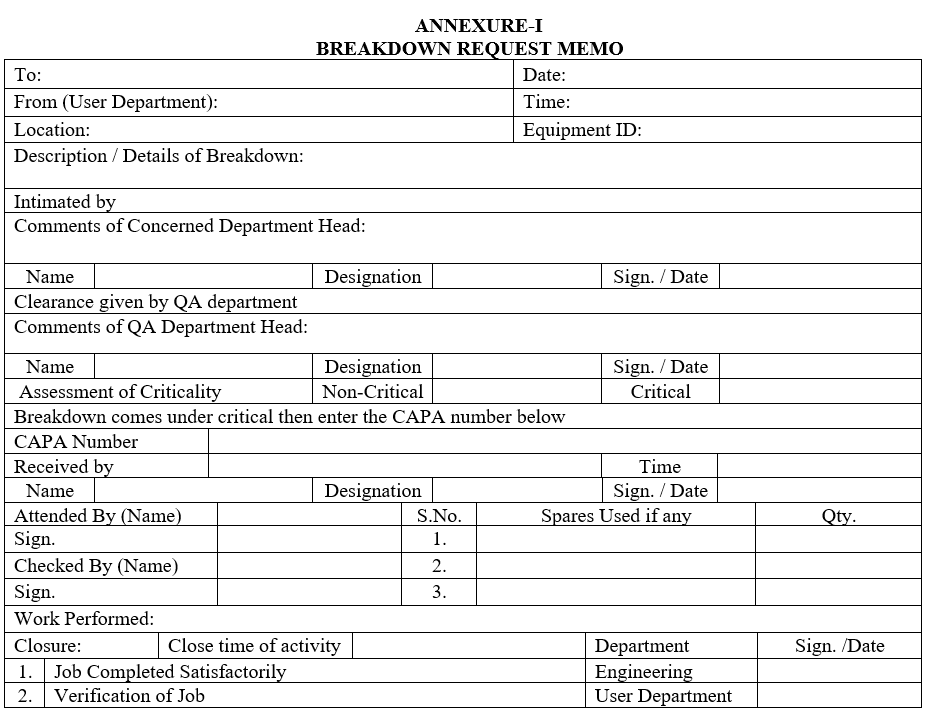
ANNEXURE-II
EQUIPMENT HISTORY CARD
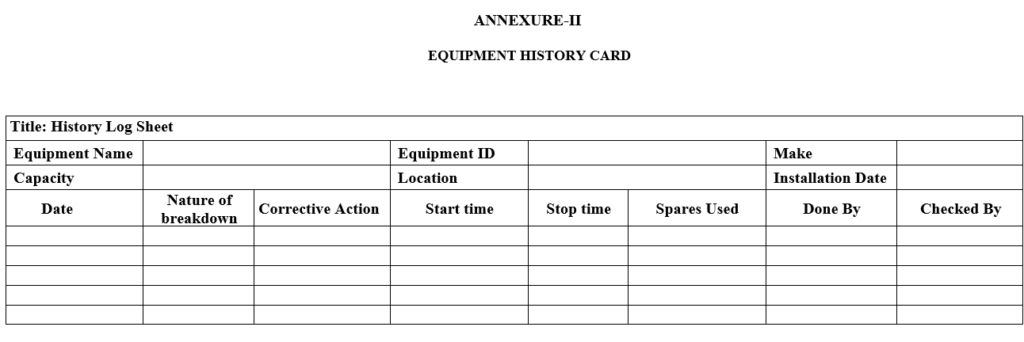
ANNEXURE-III
UNDER BREAKDOWN LABEL
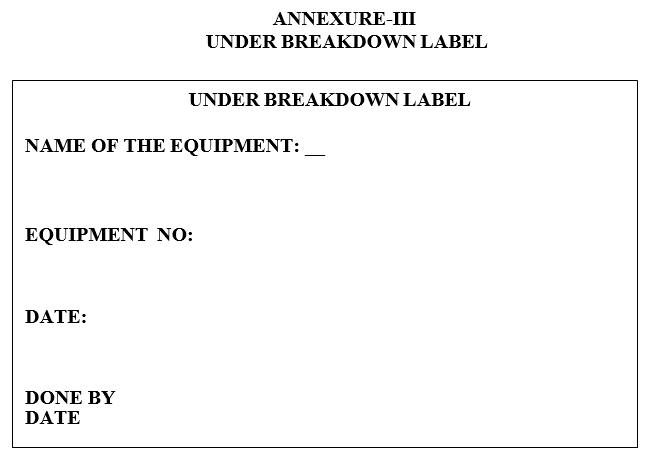
ANNEXURE-IV
BREAKDOWN REQUEST MEMO LIST
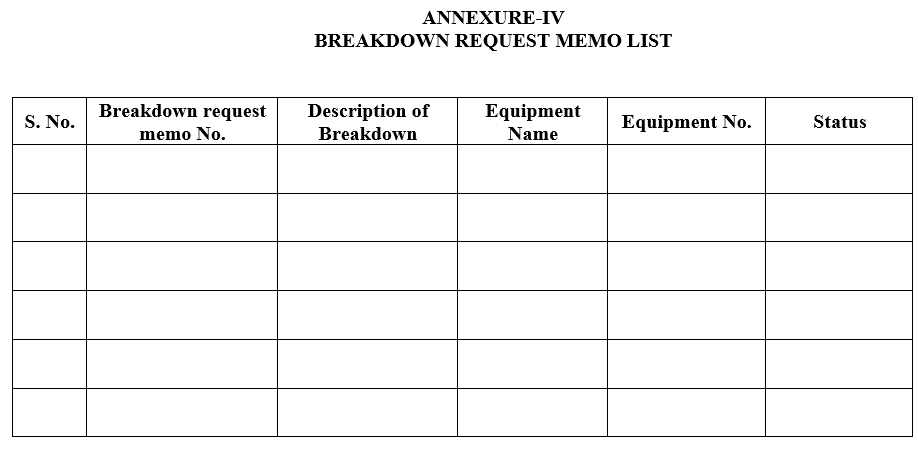
Frequently Asked Question?
Questions and Answers about the Equipment Breakdown Procedure:
1. Who initiates the breakdown request?
The concerned department personnel initiate the breakdown request when equipment or instrument malfunctions.
2. What information is required in the breakdown request memo?
- Nature of the breakdown
- Activity being carried out at the time of breakdown
- Nature of work (mechanical, electrical, HVAC, etc.)
- Date and time of breakdown request
- Department initiating the request
3. What happens after the breakdown request is received by the engineering department?
- The request is assigned a number and received by date and time is recorded.
- A technical assistant is allocated to attend the breakdown.
4. How is the breakdown addressed?
- The technical assistant labels the equipment as “UNDER BREAKDOWN” and attempts to rectify the fault.
- If internal repair is not possible, the concerned supplier is informed.
- The supplier engineer completes the repair and submits a report.
- The engineering department verifies the repair and attaches the report to the breakdown memo.
5. What happens after the breakdown is fixed?
- The engineering executive reviews the work and ensures proper equipment function.
- If the breakdown potentially affects product quality, a Process Non-Conformance (PNC) is raised.
- Deviations from planned maintenance or breakdowns during preventive maintenance are documented as exceptions.
- Replaced components are recorded in the equipment history card.
- Breakdown re-occurrence is tracked in the breakdown request memo.
6. How are repeated breakdowns handled?
- A trend analysis is conducted quarterly based on breakdown request data.
- Based on this analysis, the preventive maintenance schedule or checklist may be revised if breakdowns occur three or more times for the same equipment.
7. Where are breakdown request records kept?
- The engineering department retains breakdown request memos and updates the breakdown request number list accordingly.
- Equipment history cards are updated with approved changes and reviewed after each breakdown.