- PROCEDURE FOR THE HANDLING OF LABORATORY INCIDENTS:
- A laboratory incident refers to any unplanned or unintended event occurring during laboratory activities that could compromise safety, product quality, data integrity, or regulatory compliance. These incidents can range from minor mishaps to more serious events and can have significant consequences.
- During or after analysis, certain inconsistencies may be reported by the analyst, due to equipment malfunction, analytical drift, incorrect weighment, dilution errors and documentation errors etc. Such instances are reported as laboratory incidents.
- All incidents shall be logged in a logbook (format-I) and shall be numbered as under. Incident report shall be allotted a number consisting of eleven characters.
- Upon identification of the incident, the analyst shall immediately record the event in an incident report form (format-II) and submit to supervisor.
- Numbering system of laboratory incident:
- QC/LI/YY-XXX
- The first two characters are alphabets indicating department code as QC for Quality control
- The third character is slash “/”.
- The fourth and fifth character is “LI” indicating ‘Laboratory Incident’.
- The sixth character is slash “/”.
- The seventh and eighth character are numerical indicating the year.
- The ninth character is ‘-‘dash.
- Next three characters are numerical in sequential order starting from 001 every year.
- For E.g. The first incident report filed in QC department in the year 2025 shall be numbered as QC/LI/25-001.
- Examples of the laboratory incident examples are listed below (but not limited to):
- Entry missing in logbooks.
- Incorrect STP (other market) used for analysis.
- Special recommendations/Notes are not followed which are mentioned in STP. Like sample solution storage condition, sample sonication in cold water, column equilibration time etc.
- Hygroscopic components are exposed more time during water content/other analysis.
- Incorrect Oven temperature/drying time used for Loss on drying test.
- HPLC/GC vial not placed properly in carousel.
- Instrument failed due to electrical power cable disturbed, Electrical power failure, solvent delivery lost in HPLC, high pressure.
- Instrument aborted due to Leakage in instrument, leakage at column inlet or outlet, retention time shifting, Wrong instrument selection, incorrect instrument used, Bracketing injection not meeting criteria, high area variation obtained between duplicate injections from same vial.
- Incorrect sample sequence details are entered for HPLC/GC analysis like; incorrect vial No. mentioned, incorrect vial description, Number of injections not given as per STP/GTP, wrong column Name or Number given, injection sequence not followed as per STP, Bracketing injection not given.
- Incorrect solutions are prepared like; Incorrect standard/sample/salt/reagent used, Incorrect mobile phase composition used, correct type of filter not used as per STP, wrong volumetric flask/pipette used, equivalent weight not taken for placebo, Tablets/capsules, std/sample solution prepared glassware broken.
- Procedure deviation during dissolution testing like; Shaft height is not set as per STP, Apparatus type (Basket/Paddle) is not used as per STP, Incorrect dissolution medium used, dissolution sampling not done at specified time point, dissolution medium not added as correction volume in dissolution profile etc.
- Reviewer and GLP in charge shall investigate as per the investigation checklist (Annexure-II) and verify all relevant documents & all solutions used.
- Reviewer shall record all the comments after evaluation in section-II on Incident report.
- GLP In charge/Reviewer shall record corrective and proposal actions in section –III & Section-IV.
- Required corrective and preventive actions shall be decided by in charge and classify Ordinary or Significant event.
- Ordinary events are like Instrument failed during analysis, bracketing standard criteria.
- Significant events are like Specification revision, STP revision, GTP revision, Out of Specification and Out of Trend.
- Closure details of significant events shall be recorded in Section-VI on Laboratory incident by GLP In charge/Reviewer.
- Section-VI shall not be applicable for ordinary events.
- Incident occurred, respective documents like raw data work sheet, chromatograms spectra and weight slips shall be stamped as ‘invalidated’ with appropriate reason and shall be archived along with respective incident report.
Click the link to download word file copy of this document:
https://pharmaguidehub.com/product/handling-of-laboratory-incidents/
- ANNEXURES:
ANNEXURE NO | TITLE OF ANNEXURE |
Annexure-I | Laboratory incident logging register |
Annexure-II | Incident Report |
Annexure-I
LABORATORY INCIDENT LOG REGISTER
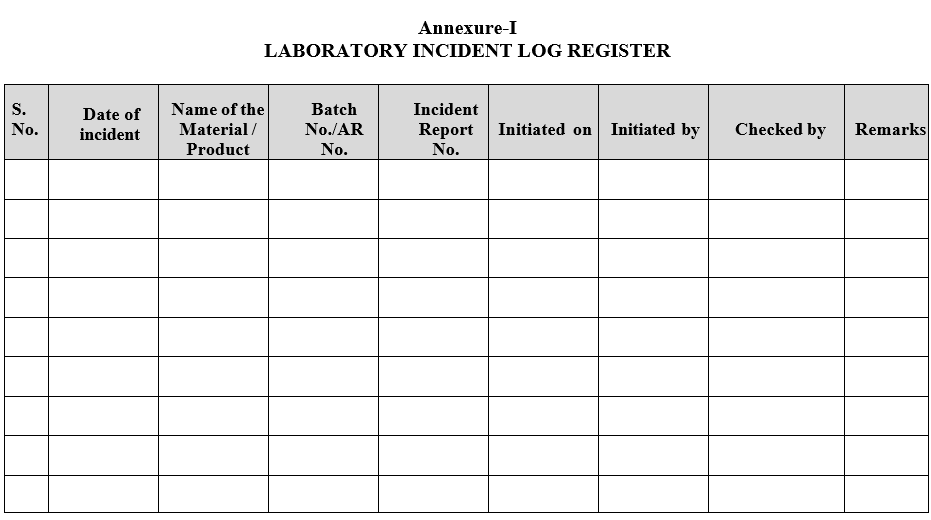
Annexure II
INCIDENT REPORT
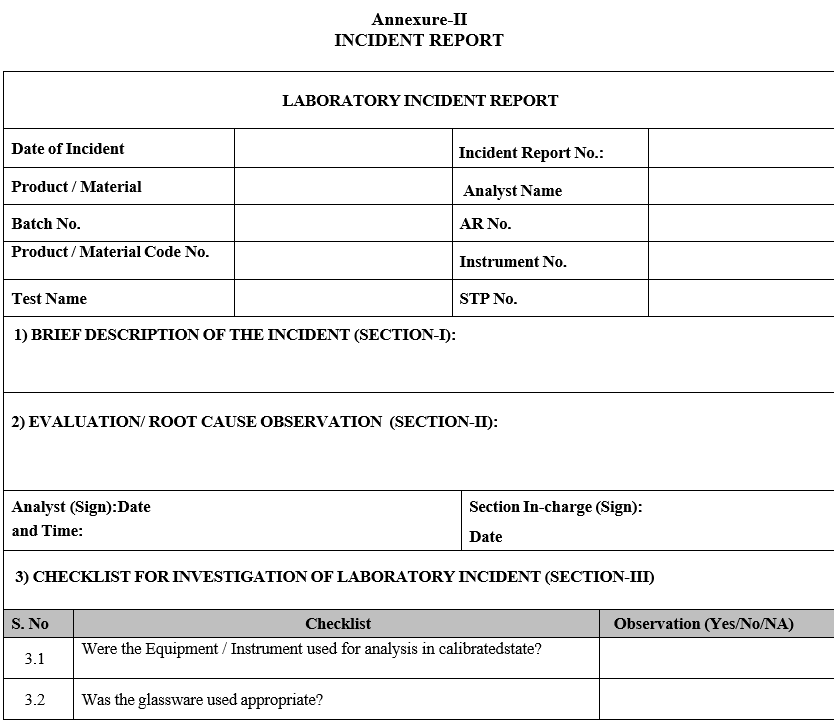
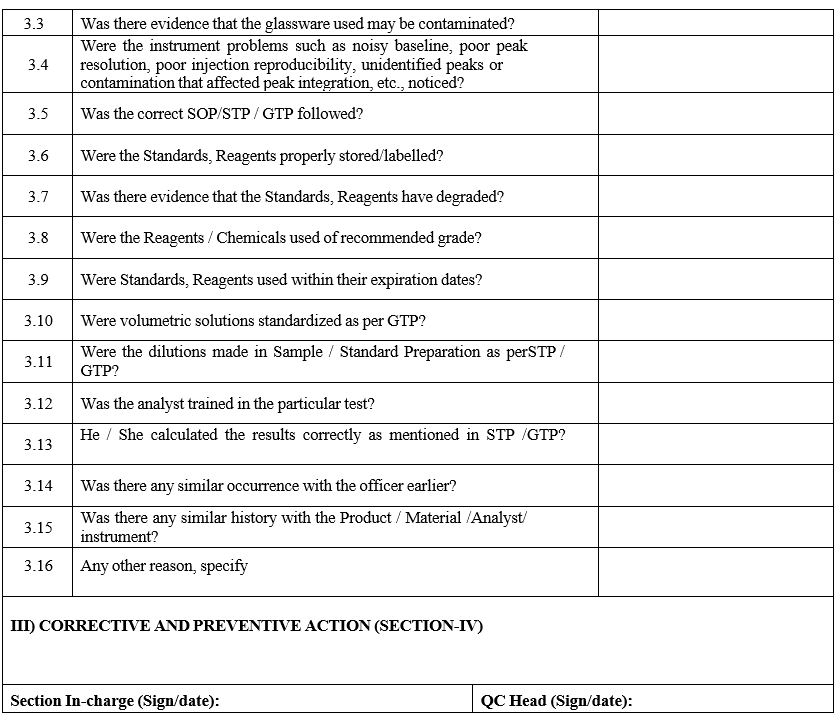
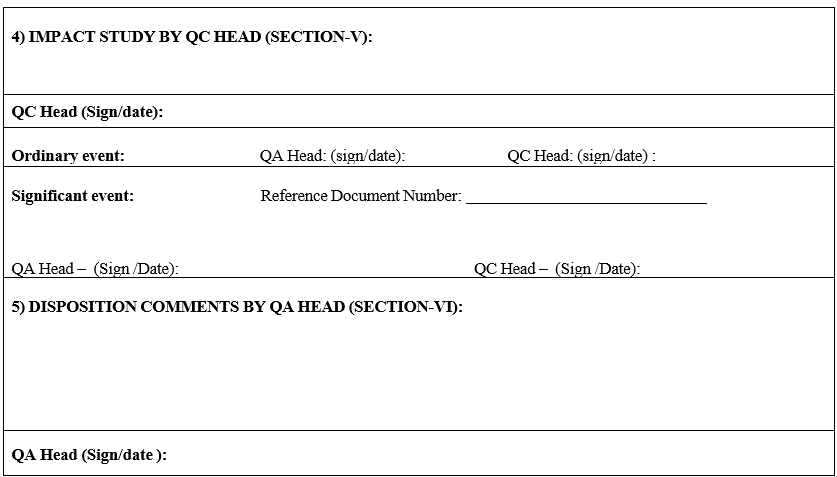
Frequently Asked Questions ?
1. What are some examples of situations that would be considered “laboratory incidents”?
Answer: The paragraph provides several examples, including:
- Incorrect weighment or dilution errors
- Equipment malfunctions
- Deviations from standard operating procedures (SOPs)
- Missing entries in logbooks
- Incorrect sample or solution preparation
- Instrument failures
- Data integrity issues
2. How are laboratory incidents documented and reported?
Answer:
- All incidents are logged in a specific format (Format-I) with a unique 11-character code.
- Analysts complete an incident report form (Format-II) describing the incident and submit it to their supervisor.
- The report number follows a specific format: QC/LI/YY-XXX (department code, “LI” for Lab Incident, year, sequential number).
3. Who investigates laboratory incidents?
Answer:
- The reviewer and GLP in-charge investigate the incident using an investigation checklist and relevant documents.
- The reviewer records their evaluation and comments in the report.
- The GLP in-charge/reviewer proposes corrective and preventive actions.
4. What are the key objectives of laboratory incident reporting in the pharmaceutical industry?
Answer:
- Ensure data integrity and patient safety: Identifying and addressing potential errors protects patient well-being and ensures the accuracy and reliability of data used in drug development and production.
- Improve laboratory practices: By analyzing incidents, laboratories identify areas for improvement in procedures, training, and equipment maintenance, leading to better overall quality.
- Meet regulatory compliance: Reporting adheres to Good Laboratory Practice (GLP) and other regulatory requirements, demonstrating commitment to quality and safety standards.
5. Who is responsible for reporting laboratory incidents?
Answer:
- Primarily, any laboratory personnel who observes or identifies an incident is responsible for reporting it.
- Supervisors and laboratory managers play a crucial role in ensuring timely and complete reporting and follow-up.
6. What are some common challenges in laboratory incident reporting?
Answer:
- Fear of blame or disciplinary action: Creating a culture of open communication and focusing on learning from incidents can encourage accurate reporting.
- Lack of awareness or understanding: Proper training on incident identification, reporting procedures, and the importance of reporting is essential.
- Time constraints and workload: Streamlining the reporting process and providing clear guidelines can help overcome time pressure.
7. How are significant vs. ordinary incidents differentiated and handled?
Answer:
- Significant incidents: Have the potential to impact data integrity, product quality, or patient safety. Require a more thorough investigation, documented corrective actions, and potential regulatory reporting.
- Ordinary incidents: Minor issues like equipment malfunctions or minor deviations from SOPs. Require documentation and corrective actions but may not involve extensive investigation or reporting.
8. How can technology be used to improve laboratory incident reporting?
Answer:
- Electronic reporting systems can streamline the process, improve data capture, and facilitate analysis.
- Real-time monitoring of critical equipment and processes can help identify potential issues before they become incidents.
9. What are the long-term benefits of effective laboratory incident reporting?
Answer:
- Enhanced product quality and safety: By identifying and addressing potential issues early, laboratories can prevent defects and ensure the safety and efficacy of their products.
- Reduced costs: Effective incident reporting can help prevent costly errors and rework, leading to increased efficiency and profitability.
- Improved employee engagement: A culture of open communication and continuous improvement fosters a more engaged and motivated workforce.
Click the link to download word file copy of this document:
https://pharmaguidehub.com/product/handling-of-laboratory-incidents/