- PROCEDURE FOR THE OOS IN MICRO:
- OUT OF SPECIFICATION: OOS stands for “Out-of-Specification”. It refers to a test result for a drug, raw material, or in-process material that falls outside of the pre-determined acceptable limits.
- When sample tested – exhibits OOS results:
- Notify the In-Charge – Microbiology immediately and initiate microbiology laboratory investigation.
- When the OOS is observed enter the details in Out of Specification Log (Format-I).
- If the laboratory investigation identifies the assignable cause sample may be retested.
- Where the laboratory investigation does not establish assignable cause initiate the failure investigation as per SOP.
- At the conclusion of the failure investigation, In-Charge and/or Head-QA will take a necessary action.
- Microbiology Laboratory Investigation:
- Report the OOS result to the In-Charge – Microbiology and/or In-Charge-QC immediately. This must be done before any additional testing is performed.
- Initiate laboratory investigation within one business day completing section as per Format-II.
- If a section is considered not applicable to the investigation mark the section as Not Applicable (NA).
- The appropriate signatures must be made on all actions including those marked as Not Applicable.
- Justification to proceed to the next step shall be provided as a conclusion in Format-II.
- When an assignable cause is identified after completion of investigation:
- Re sample and retest the material as per the SOP & GTP.
- After completion of the retesting, inform the results to Head-QC & In-Charge QA for necessary action.
- If no assignable cause is identified after completing the investigation as per Format-II.
- The Head-QC notifies the OOS results to In-Charge-QA via Quality Alert Report (Format-III) within one working day. Copies of Quality Alert Report shall be sent to Head-QA.
Click the link for download word file copy of this document:
https://pharmaguidehub.com/product/investigation-of-out-of-specification-test-results-oos-in-microbiology-laboratory/
- For finished products after receiving the quality alert report In-Charge-QA shall meet microbiologist and review the relevant data and discuss the timing for conducting failure investigation.
- If a new organism is found, potential risk of that organism shall be identified.
- After completion of the investigation, the In-Charge – Microbiology and/or In-Charge-QC completes the documentation and inform the retest results to Head-QC.
- In case where more than one lot of materials is investigated for the same problem, only one investigation report is required. All affected lots must be clearly listed and copies of the laboratory investigation must be included with the testing documentation for each lot.
- Laboratory investigation shall be completed within 20 working days from the date of initiation of laboratory investigation.
- If the investigation cannot be completed in 20 working days the Head-QC must prepare an interim report describing the current status, reasons for carrying Laboratory investigation beyond 20 working days and an estimated time of completion to the In-Charge-QA. An interim report is required for every 20 working days while the investigation continues.
- RETEST PROCEDURE:
- For an OOS result retesting is only appropriate after laboratory investigation has been completed and where an assignable cause has been identified.
- Retesting after obtaining an assignable cause, result is at the discretion of the Head-QC. The retest must be justified scientifically only after completion of assignable cause.
- The test sample, which was the source of OOS result, must be included in the retest plan when possible.
- Otherwise, additional representative samples may be obtained for retest purposes.Any retesting shall be performed as per the GTP and SOP.In retesting (For microbial limit test) use 10g specimen of the product/material.
- At the conclusion of the retesting the Head-QA will take a decision. If the results of the retesting do not justify the material release and laboratory investigation does not establish assignable cause initiate a failure investigation as per the SOP.
- Alternate test procedures will not be used to approve material that initially had OOS results using the primary test procedure, unless permitted by the applicable compendia.
- RESAMPLING GUIDELINES:
- Re sampling is only appropriate when there is insufficient original sample the laboratory investigation determines an assignable cause or if the failure investigation requires extensive retesting.
- Re sampling must be done as per the normal sampling procedure by taking the prior approval from In-Charge-QA.
- Results obtained by re sampling, as a part of failure investigation must not be used to provide the sole basis for material approval.
NOTE: If the sample does not meet the specification limit in retesting, invalid the whole batch of the product.
Click the link for download word file copy of this document:
https://pharmaguidehub.com/product/investigation-of-out-of-specification-test-results-oos-in-microbiology-laboratory/
- ANNEXURES:
Annexure No. | Title of annexure |
Annexure-I | Out Of Specification Log |
Annexure-II | Investigation report on Microbial test OOS results |
Annexure-III | Quality Alert Report |
- ABBREVIATIONS:
No. | : | Number |
OOS | : | Out of Specification |
GTP | : | General testing procedure |
MNC | : | Material Non-Conformance |
SOP | : | Standard Operating Procedure |
QC | : | Quality Control |
Flow Chart For OOS in Micro
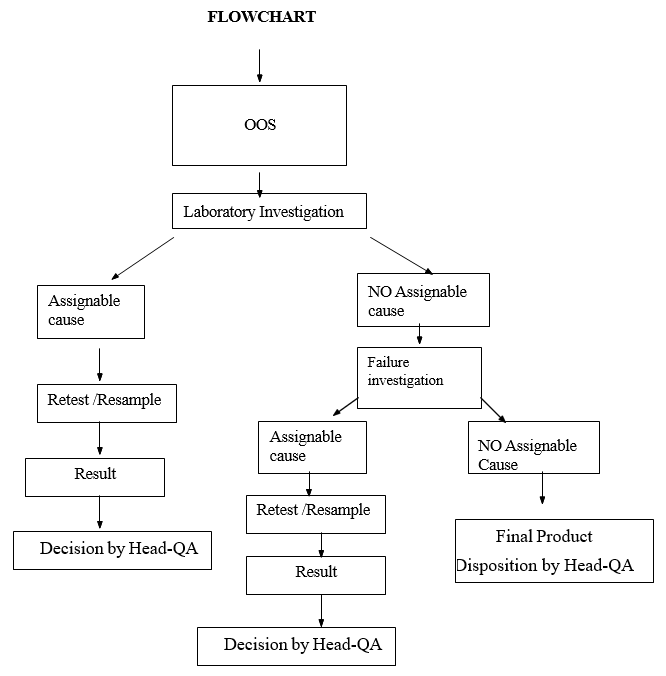
Annexure-I
OUT OF SPECIFICATION LOG
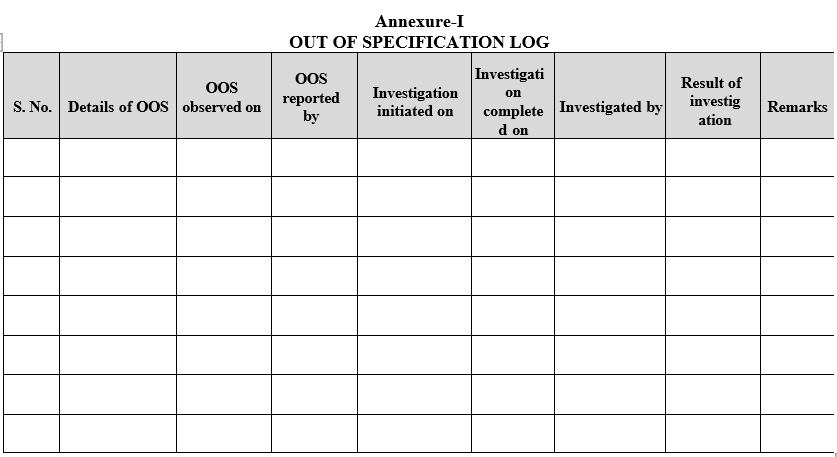
Annexure-II
Investigation report on Microbial test OOS results
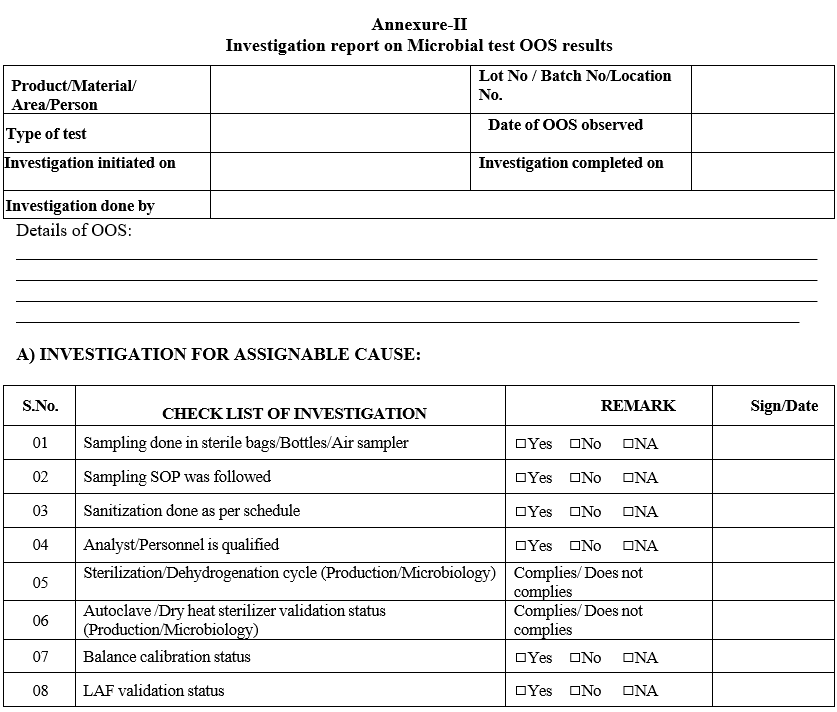
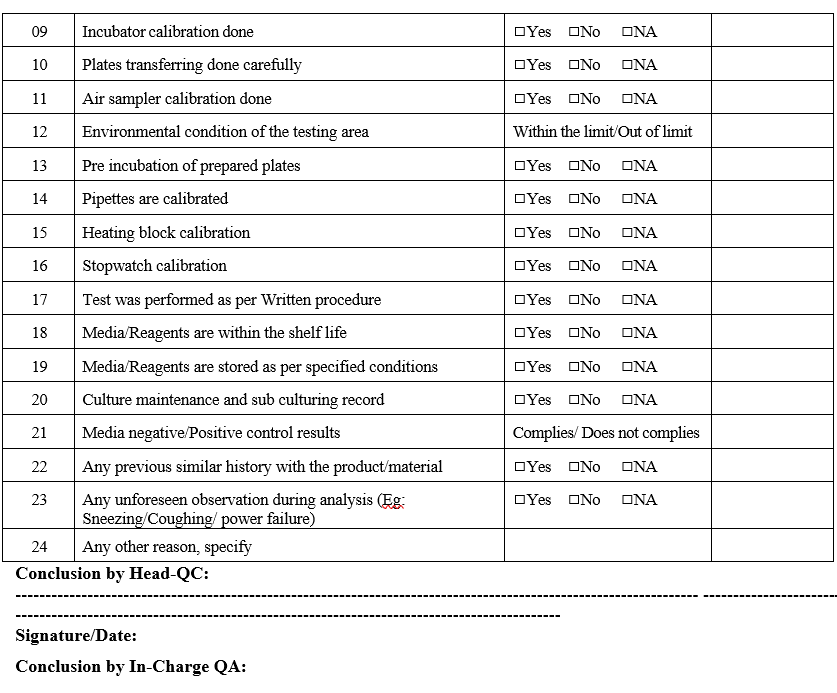
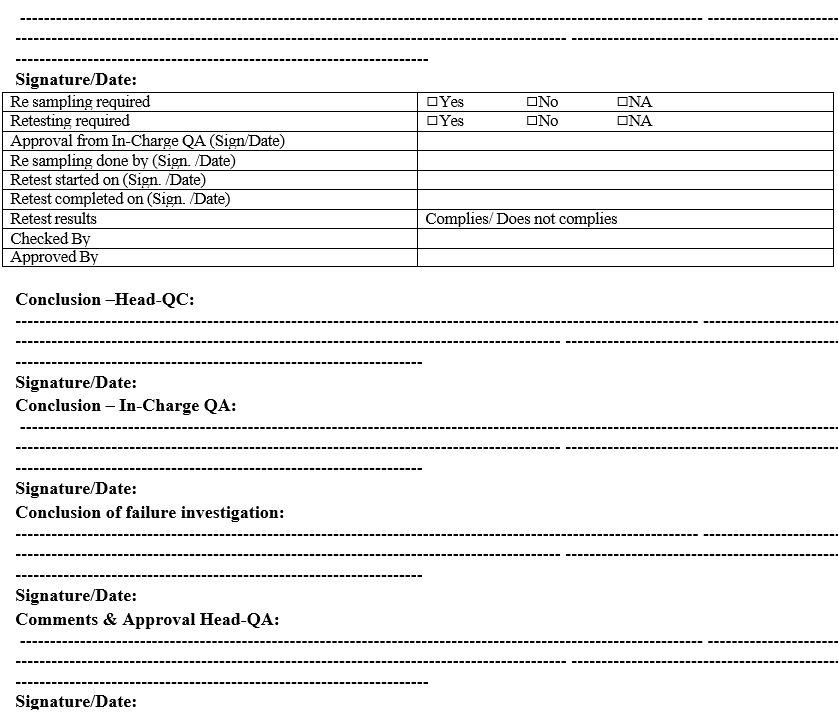
Annexure-III
Quality Alert Report
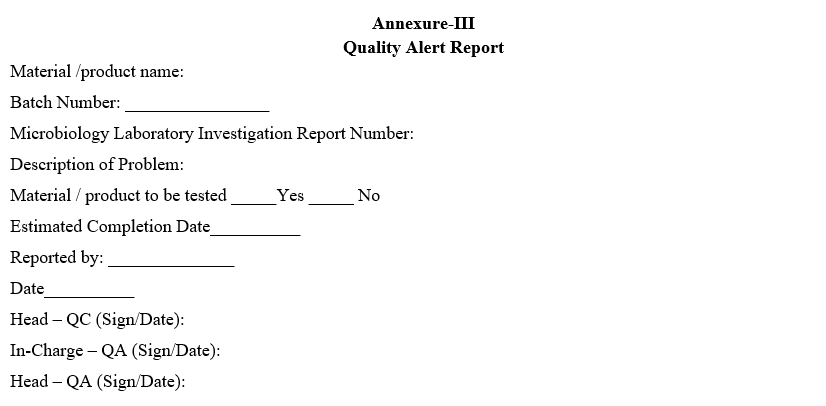
Click the link for download word file copy of this document:
https://pharmaguidehub.com/product/investigation-of-out-of-specification-test-results-oos-in-microbiology-laboratory/