OBJECTIVE:
To lay down the procedure for determining the microbial load for equipment surfaces, floor and walls.
SCOPE:
This SOP is applicable for the procedure for determining the microbial load for equipment surfaces, floor and walls at {Company Name} {Location}.
RESPONSIBILITY:
Microbiologist: is responsible to perform the activity as per SOP.
In charge- Microbiology- is responsible to ensure compliance as per SOP.
Head/Designee Quality Control – Shall be responsible for ensuring compliance as per SOP.
ACCOUNTABILITY:
QA Head shall be Accountable for implementation of SOP.
About Equipment Swab:
Equipment swabbing in pharmaceutical microbiology is a critical monitoring technique to assess the cleanliness and microbial contamination levels of manufacturing equipment surfaces. Sterile swabs are used to collect samples from various equipment surfaces, such as filling needles, valves, and tubing. These samples are then inoculated into appropriate growth media and incubated to detect the presence and quantity of microorganisms. This process ensures compliance with regulatory standards and helps maintain product quality and safety.
PROCEDURE:
EQUIPMENT BINLOAD
Swab Method:
Sterilize the swab in 30 mL of normal saline with 0.5% Soya lecithin with 1% Polysorbate 80 in a bottle/test tube plugged with non-absorbent cotton and sterilize in an Autoclave as per validated cycle.
Pre sterilized readymade swabs can also be used (sterile cotton swab with polypropylene stick, Size: 150 X 12 mm diameter, Make Himedia, Code:PW009, or equivalent) Note: Before transferring to sampling location add aseptically 30 mL of sterile normal saline with 0.5% Soya lecithin with 1% Polysorbate 80, incase of ready prepared swab stick are used.
Carry the sterilized swabs in a stainless steel box, previously sanitized with 70% v/v IPA to the respective area.
Refer respective cleaning validation protocol for swab sampling locations.
Press the swab with a rolling motion against the side of the glass tube to remove excess saline, Swab an area of approximately 25cm2 (5×5 cm) of the equipment. Swab the area as per the swabbing pattern using the template (made of SS/Teflon/PVC). Subsequently it shall be swabbed at 90° angle to the previous strokes as shown below. (as per figure-1)
Click the link for download word file copy of this document: https://pharmaguidehub.com/product/equipment-swab/
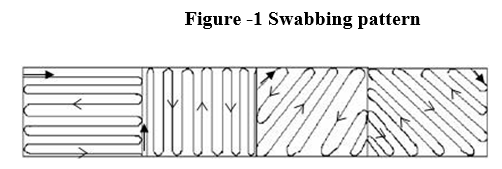
Mix the swab with saline by swirling thoroughly. Label the tube with the equipment name/ID, designated location and date. Transfer the swabs to the microbiology department. Note: In case any delay in analysis, store the swab samples at 2-8°C. The time elapsing between collection and examination should not exceed 72 hours. If stored at 2-8°C, allow the samples to attain the ambient temperature before analysis.
After thorough mixing of the swab, filter 10 mL of saline each through 0.45 µm sterile membrane filters and rinse with 100 mL of 0.1 % sterile peptone water and place in SCDA.
Incubate the plate an inverted position at 20 to 25 0C for 72 Hrs and followed by 30°C to 35°C for 48 Hrs respectively.
Transfer the remaining 10 mL sample to 90 mL of previously sterilized soya bean casein digest broth with 0.5% Soya lecithin with 1% Polysorbate 80 and incubated at 30-35°C for 18-24 hours.
Perform test for specified organisms as per GTP.
Count the number of colonies formed on filters and report as cfu/swab.
Frequency: After every ‘type C ’cleaning.
Acceptance criteria:
Click the link for download word file copy of this document: https://pharmaguidehub.com/product/equipment-swab/
S. No. | Test Parameter | Limits |
1. | Total bacterial count | 50 cfu/swab |
2. | Yeast and mold count | Absent/swab |
3. | Escherichia coli | Absent |
4. | Salmonella spp | Absent |
5. | Staphylococcus aureus | Absent |
6. | Pseudomonas aeruginosa | Absent |
Record the entry in the report sheet as per Format-I and Format-II.
Rinse Binload:
After completion of final cleaning rinse the required equipment with specified quantity of water and collect about 100 mL of this sample in a sterilized bottle.
Label the container/tube with the equipment name/ID, designated location and date. Transfer the swabs to the microbiology department.
Note: In case any delay in analysis, store the swab samples at 2-8°C. The time elapsing between collection and examination should not exceed 72 hours.
If stored at 2-8°C, allow the samples to attain the ambient temperature before analysis.
Take 10mL of this sample and filter through 0.45mm sterile membrane filters followed by 100 mL of 0.1 % peptone water and place in SCDA.
Incubate the plate an inverted position at 20 to 25 0C for 72 Hrs and followed by 30°C to 35°C for 48 Hrs respectively.
Take the remaining 10mL of the sample and transfer to 90 mL of previously sterilized soya bean casein digest broth with 0.5% Soya lecithin with 1% Polysorbate 80 and incubated at 30-35°C for 18-24 hours.
Perform test for specified organisms as per GTP.
Count the number of colonies formed on filters and report as cfu/mL.
Acceptance criteria:
Click the link for download word file copy of this document: https://pharmaguidehub.com/product/equipment-swab/
S. No. | Test Parameter | Limits |
1. | Total bacterial count | 50 cfu/mL |
2. | Yeast and mold count | Absent/mL |
3. | Escherichia coli | Absent |
4. | Salmonella spp | Absent |
5. | Staphylococcus aureus | Absent |
6. | Pseudomonas aeruginosa | Absent |
Test Negative control:
For Swab sample, negative control shall be performed by filtering with sterile swab containing with 30 mL sterile saline solution with 0.5% Soya lecithin with 1% Polysorbate 80, after filtration rinse with 100 mL of 0.1% peptone water. For rinse sample, negative control shall be performed by filtering 100 mL of 0.1% peptone water.
Acceptance criteria: Negative control should not show any growth.
Action plan for excursion of Acceptance criteria:
If any test result exceeds the specified limits, Investigation shall be carried out as per SOP and necessary corrective and preventive action (CAPA) shall be taken.
REFERENCES:
Not Applicable
ANNEXURES:
Annexure No. | Title of annexure |
Annexure-I | Equipment swab /Rinse Report |
Annexure-II | Equipment swab/rinse raw data Report |
ENCLOSURES: SOP Training Record.
DISTRIBUTION:
Master Copy : Quality Assurance Department
Controlled Copy No. 01 : Head Quality Assurance
Controlled Copy No. 02 : Head Quality Control (Micro.)
ABBREVIATIONS:
No. | : | Number |
GTP | : | General Testing Procedure |
STP | : | Standard Testing Procedure |
MNP | : | Maintenance Procedure |
SBCDA | : | Soya bean casein digest agar |
SOP | : | Standard Operating Procedure |
QC | : | Quality Control |
REVISION HISTORY:
CHANGE HISTORY LOG
Revision No. | Details of Changes | Reason for Change | Effective Date |
00 | New SOP | Not Applicable | To Be Written Manual |
Annexure-I
EQUIPMENT SWAB /RINSE REPORT
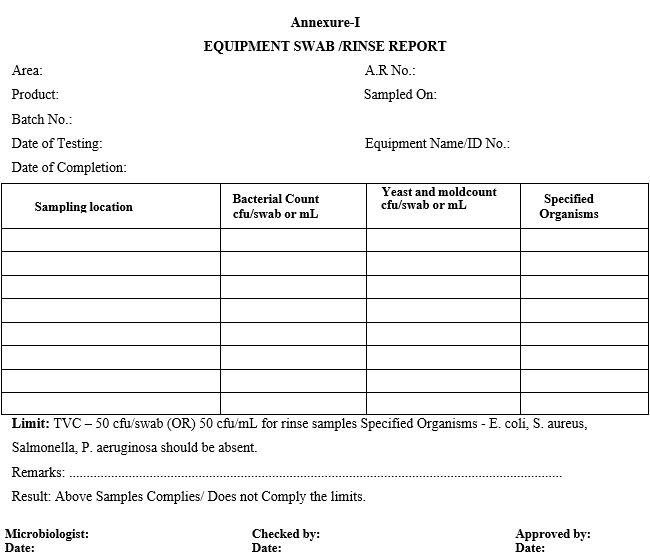
Annexure-II
EQUIPMENT SWAB/RINSE RAW DATA REPORT
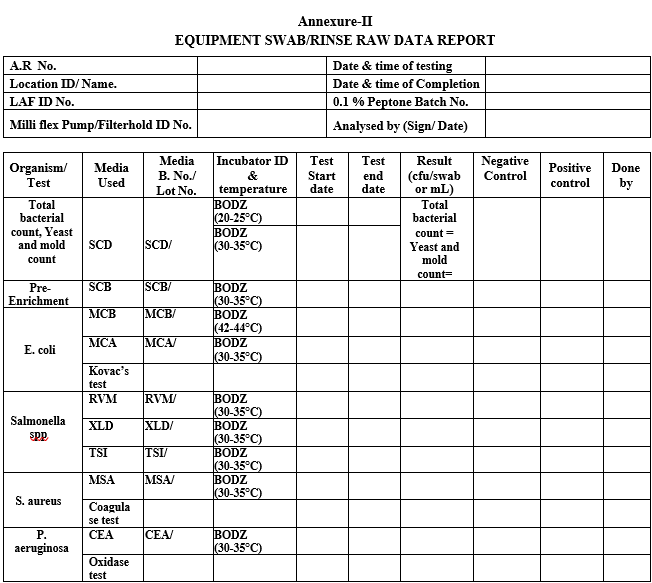
Remarks: ……………………………………………………………………………………………………………………………
Observed By: Checked By:
Click the link for download word file copy of this document: https://pharmaguidehub.com/product/equipment-swab/