OBJECTIVE:
To lay down a Procedure for Building Maintenance.
SCOPE:
This SOP is applicable for Building Maintenance at {Company Name} {Location}.
RESPONSIBILITY:
Technician- Follow the instruction as per procedure.
Engineering Officer/Executive- Execution as per laid down procedure.
Engineering Head- Technical correction, review, training & monitoring of SOP.
ACCOUNTABILITY:
Engineering Head
Quality Assurance Head
PROCEDURE:
Precautions and general conditions:
During height works use safety belts and helmets.
During electrical works use proper HT gloves and goggles and safety shoes.
During civil works wear necessary gloves, nose mask and goggles.
Use proper tools during the work.
Engineering personnel shall make an inspection of building maintenance Half-Yearly as per the list mention below:
- Production
- Warehouse
- Quality Control
- Quality Assurance
- Utility
- Security & Building Surrounding Area
- Administration
Engineering personnel shall check the following points in Half-Yearly inspection of building maintenance.
Exterior Part:
- External painting of wall
- External cracks on wall
- Water seepage from wall
- Debris around the building
- Lights are in working order
- Walkway around the building free
- Cable tray
- Doors and windows
- Storm water drain
- Any other
Terrace:
- Flooring condition
- Drain condition
- Cable tray
- Piping
- Debris
- Any other
Interior Part:
- Painting condition of wall
- Cracks on wall
- Water seepage from wall
- Lights are in working order
- Ensure light should be sufficient and lux level should be within acceptance criteria (Limit of lux level for core area NLT 1000 lux and for other area NLT 500 lux).
- Lux level will be monitor for each working area or where ever require.
- Lux level should be check with lux meter from 1 meter of working height and record in Annexure V.
- Lux level should be checked annually (Variance ±30 days) by external agency or whenever required.
- During lux level examine if found lux level is below the limit then replace the light and after replace of light ensure lux level should be within acceptance limit.
- Cable tray
- Pipe rack
- Doors
- Windows
- Drain
- Flooring conditions
- Ceiling condition
- Supply grill and return riser
- Any others
- Check door seal on half yearly and if faulty then replace door seal and when required.
External agency shall perform the earth pit testing on half yearly basis (variation ±30 days) or whenever required and record in Annexure-IV.
- Get the entire earth pit.
- Test the earth pit through calibrated multimeter / electrical conductor/ Megger.
- Add Sun power back fill earth compound solution if resistant reading exceeds 5Ω.
- After addition of salt if resistance not get 5 Ω or below 5 Ω then replace the ground electrode.
- Earth pit numbering can be given in following order: PGH/EP/XX
Where the following are stands for;
PGH- {Company Name}
EP- Earth Pit.
XX- Earth pit serial no. like 01, 02, 03……
Engineering services team shall inspect the premises of the building area for civil, mechanical and electrical aspects for any maintenance.
Based on the inspection the engineering services team informs to the user department to issue the building maintenance work order request memo as per Annexure-I.
The user department provide building maintenance work order request memo duly filled and approved by the QA head/designee.
Building maintenance work order request memo shall be reviewed by the engineering head for action plan.
Engineering services team shall ensure that the contractor’s supervisor is present if the work is being carried out by outside contractor.
Ensure that the contractor’s workmen follow all protective and safety measures.
Click the link to download word file copy of this document:
https://pharmaguidehub.com/product/building-maintenance/
On completion of the job/work, the core respective area shall be cleaned by following the respective cleaning procedures.
Inspection of building maintenance check points will be done as per Annexure-II.
Inspection of building maintenance Safety Evaluation will be done as per Annexure-III
During safety evaluation smoke detector test can be done through smoke generation and record the data in Annexure-VI.
Smoke generation can be done through poly ethylene glycol with the help of fume generator.
When smoke detectors detect the fume, it gives a sound for fire/smoke alert.
After performing the smoke test, reset the alarm through control panel which is place at security room.
If smoke test shall not find satisfactory, then instrument shall go into breakdown and again smoke test shall be performed after rectification.
Smoke challenge test shall be performed before the smoke test.
Precaution of smoke challenge test shall be performed as per Annexure-VII
REFERENCES:
Not Applicable
ANNEXURES:
ANNEXURE No. | TITLE OF ANNEXURE |
Annexure-I | Building Maintenance Work Request Memo |
Annexure-II | Half-Yearly Inspection Check List of Building Maintenance |
Annexure-III | Half-Yearly Building Safety Evaluation Checklist |
Annexure-IV | Earth pit testing checklist |
Annexure-V | Checklist for lux level monitoring |
Annexure-VI | Check list for smoke test |
Annexure-VII | Precaution of smoke challenge test |
ENCLOSURES: SOP Training Record.
DISTRIBUTION:
Controlled Copy No. 01 | : | Quality Assurance Head |
Controlled Copy No. 02 | : | Engineering Head |
Master Copy | : | Quality Assurance Department |
ABBREVIATIONS:
SOP | : | Standard Operating Procedure |
QA | : | Quality Assurance |
HT | : | High Tension |
QC | : | Quality Control |
PGH PPE | : : | Pharmaguidehub Personal Protective Equipment |
REVISION HISTORY:
CHANGE HISTORY LOG
Revision No. | Details of Changes | Reason for Change | Effective Date |
00 | New SOP | Not Applicable | To Be Written Manual |
ANNEXURE-I
BUILDING MAINTENANCE WORK REQUEST MEMO
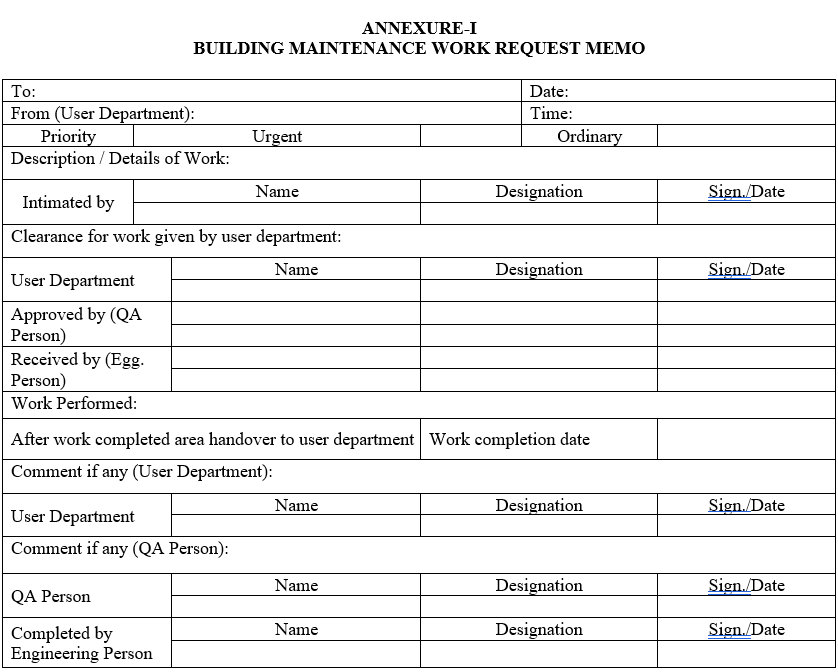
ANNEXURE-II
HALF-YEARLY INSPECTION CHECK LIST OF BUILDING MAINTENANCE
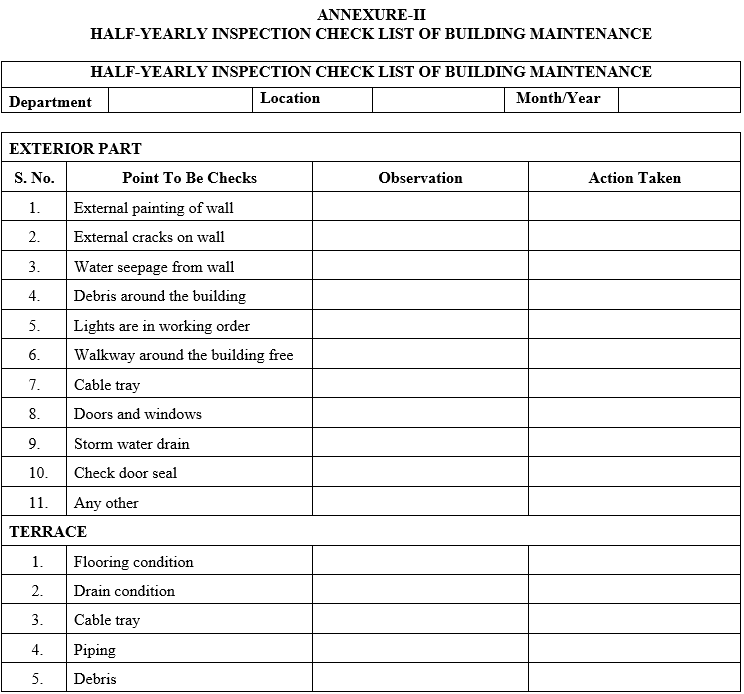
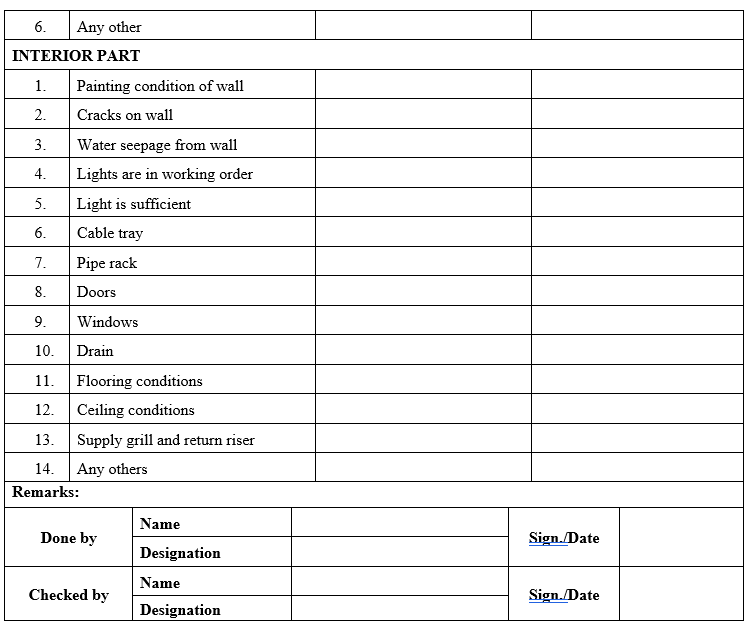
Click the link to download word file copy of this document:
https://pharmaguidehub.com/product/building-maintenance/
ANNEXURE-III
HALF-YEARLY BUILDING SAFETY EVALUATION CHECKLIST

ANNEXURE-IV
LOG SHEET FOR EARTH PIT TESTING
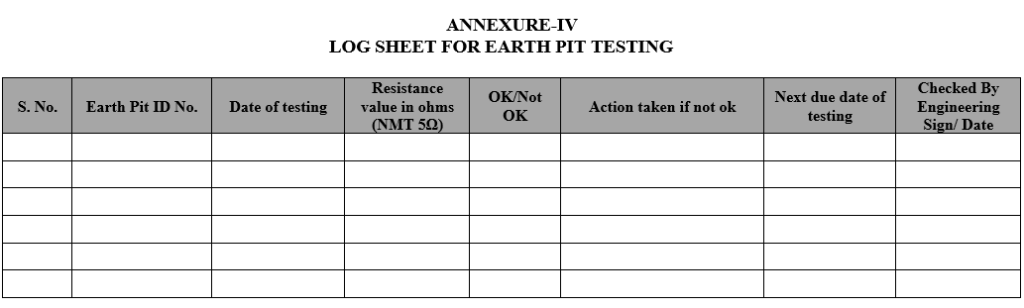
ANNEXURE-V
CHECKLIST FOR LUX LEVEL MONITORING
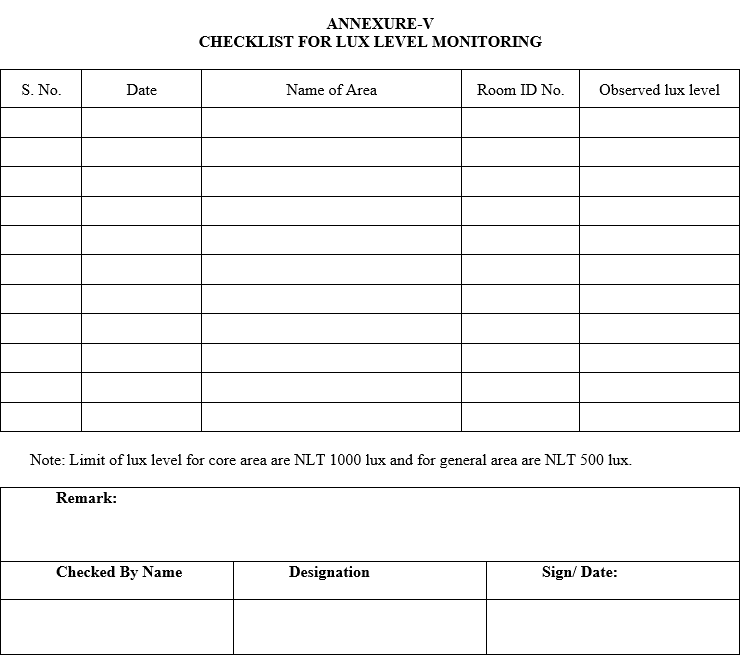
ANNEXURE-VI
CHECKLIST FOR SMOKE DETECTOR TEST
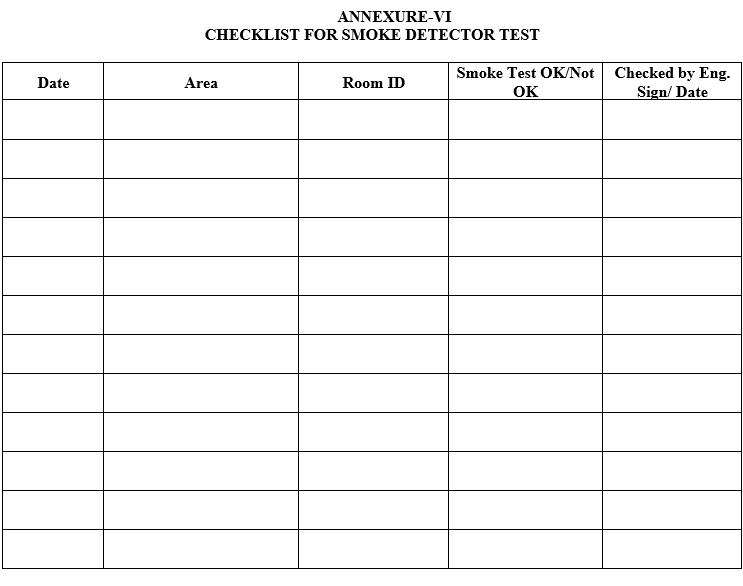
ANNEXURE-VII
PRECAUTION OF SMOKE CHALLENGE TEST
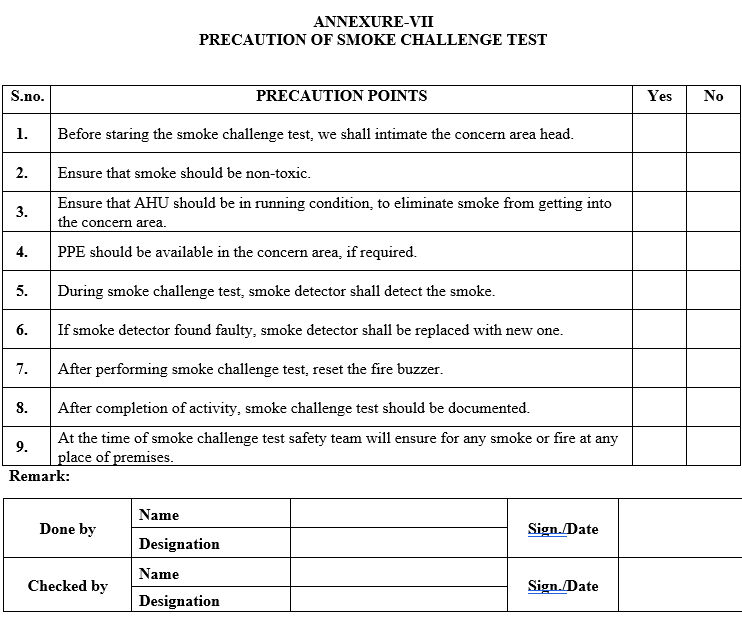
Click the link to download word file copy of this document:
https://pharmaguidehub.com/product/building-maintenance/