- OBJECTIVE:
To lay down a procedure for Handling of Returned Product.
- SCOPE:
This SOP is applicable for Handling of returned product at {Company Name} {Company Location}.
- RESPONSIBILITY:
QA officer/executive – Follow the instruction as per procedure.
QA Sr. Executive-Review and technical correction of SOP.
QA head –Training, approval & implementation of SOP.
Warehouse officer/executive- Follow the instruction as per procedure.
- ACCOUNTABILITY:
Head QA
- PROCEDURE:
- Based on the investigation report or on request of customer or for any other valid reason, QA head shall be authorized for the return of product.
- Store the material on separate pellets as per product storage condition.
- Warehouse supervisor physically check the return goods consignment for any damages to the secondary or tertiary packaging material whichever is applicable.
- If any discrepancies observed immediately notified to QA.
- Segregate the damaged goods from the goods received in the separate REJECTED area.
- Warehouse supervisor store the returned product, segregated with respect to individual batch number in recall room and inform to QA and Production.
- If the conditions under which returned products have been held, stored or shipped before or during their return or if the condition of the product, its container, carton, or labeling, as a result of storage or shipping, cast doubt on the safety, identity, strength, quality or purity of the product, the returned product shall be destroyed unless examination, testing or other investigations prove the product not meets with appropriate standards of safety, identity, strength, quality or purity.
- Records of returned drug products shall be maintained and shall include the S.No., Date of Receipt, Product Name, Batch No., Mfg.Date, Exp. Date, Quantity Dispatched, Quantity Returned, Reason for Return, Date of Destruction, Checked by and Remarks.
REFERENCES:Click the link for download word file copy of this document: https://pharmaguidehub.com/product/handling-of-returned-product/
21 CFR 211.204
- ANNEXURES:
ANNEXURE No. | TITLE OF ANNEXURE | FORMAT No. |
Annexure-I | Return Product Detail | QA-027/F01-00 |
DISTRIBUTION:
Control copy No. 1 | : | Head Quality Assurance |
Control copy No. 2 | : | Head Production |
Control copy No. 3 | : | Head Warehouse |
Master copy | : | Quality Assurance Department |
ABBREVIATIONS:
QA | : | Quality assurance |
SOP | : | Standard operating procedure |
No. | : | Number |
REVISION HISTORY:
CHANGE HISTORY LOG
Revision No. | Details of Changes | Reason for Change | Effective Date |
00 | New SOP | Not Applicable | To be written ,annual. |
ANNEXURE-I
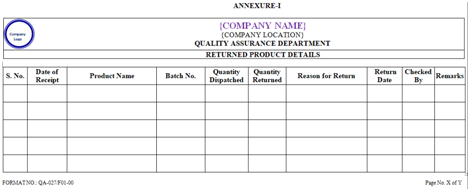
Click the link for download word file copy of this document: https://pharmaguidehub.com/product/handling-of-returned-product/
Frequently Asked Questions:
1. Q: What is the first step in handling returned pharmaceutical products?
A: The first step involves thoroughly inspecting the returned product to ensure it meets safety and quality standards. This includes checking for damage, tampering, and expiration.
2. Q: How should damaged pharmaceutical products be handled upon return?
A: Damaged products should be segregated immediately and reported to the quality control department. The cause of damage should be investigated to prevent future occurrences.
3. Q: What documentation is essential when processing returned pharmaceuticals?
A: Accurate and complete documentation is crucial. This includes a detailed record of the returned product, reasons for return, and any investigations or actions taken. Documentation ensures traceability and compliance with regulations.
4. Q: How is product integrity maintained during the return process?
A: Product integrity is maintained by handling returned products in a controlled environment, following established procedures, and ensuring that temperature-sensitive products are stored appropriately to prevent degradation.
5. Q: How are expired pharmaceuticals managed during the return process?
A: Expired products are typically quarantined and disposed of according to regulatory guidelines. Proper documentation and reporting are essential to track and manage expired products.
6. Q: What steps should be taken to investigate the reason for product returns?
A: A comprehensive investigation should be conducted to identify the root cause of the return. This may involve communication with customers, examining manufacturing records, and collaborating with the quality assurance team.
7. Q: How is communication managed with customers regarding returned products?
A: Timely and transparent communication is key. Customers should be informed of the return status, investigation outcomes, and any corrective actions taken. Clear communication helps build trust and ensures customer satisfaction.
8. Q: How can the pharmaceutical supply chain be safeguarded during the return process?
A: Implementing robust serialization and tracking systems helps safeguard the supply chain. This enables quick identification of returned products and minimizes the risk of counterfeit or tampered items entering the distribution network.
9. Q: What role does the quality assurance department play in handling returned pharmaceuticals?
A: The quality assurance department is central to the process. They conduct thorough inspections, approve/disapprove returned products, and provide critical input for investigations and corrective actions.
10. Q: How does regulatory compliance factor into the handling of returned pharmaceuticals?
A: Regulatory compliance is non-negotiable. All actions related to handling returned products must adhere to local and international regulations. This includes documentation, reporting, and following Good Distribution Practice (GDP) guidelines.
Click the link for download word file copy of this document: https://pharmaguidehub.com/product/handling-of-returned-product/