OBJECTIVE:
To lay down a procedure for Out of Trend.
- SCOPE:
- This procedure is applicable to the Out of trend results observed in analysis of Raw material (API only), Packing material, Finished product, In-process samples, Stability evaluations trends, Environmental monitoring results, Water monitoring results and other monitoring parameters conducted at {Company Name} {Company Place}.
- Out of trend results /observation can be defined as an event when a series of data is evaluated and to the significant change/deviation from the normal operating range is observed, however the observed value fall within the acceptance criteria.
- RESPONSIBILITY:
- Officer /Executive Quality Control conducting the test/ analysis shall trend the results and report results which is found out of trend.
- QA/Officer /Executive (Warehouse/Engineering /Utility) shall compare the observation with the normal trend and shall inform the aberrant or abnormal observations.
- Assistant Manager / Manager (Functional Head) shall review and investigate the out of trend results.
- Department Head shall review investigation of the out of trend result(s) and authorise the reanalysis as applicable and review and closing of the Investigation report.
- Quality Assurance head shall be Accountable for compliance of SOP and approval of OOT results.
- ACCOUNTABILITY:
QA Head shall be accountable for implementation of SOP.
- PROCEDURE:
- Out of trend (OOT) result shall be determined on the basis of the trend data / observations of previous batches (as available) or previous analytical data or any aberrant data observed during analysis or observations during environmental condition monitoring in other areas or performance of Utility /equipment. Such result may be within the acceptance criteria but not in the normal trend. OOT results do not means OOS data and hence corrective action to be taken to bring the process /analysis within the control.
- Data from minimum 10 batches or test point or data point shall be available to determine the OOT result.
- In case when alert limit and action limit decided based on trends of data, than the result observed above alert limit shall be recorded as OOT result and shall be investigated.
- The analytical results of the products shall be recorded in the log / card / excel sheet as per Annexure-III.
- OOT FOR THE LABORATORY DATA:
- While performing the analysis or during reporting of analytical results, if any OOT or aberrant data is observed, then the analyst (Officer /Executive) shall inform such observation to the Functional head.
- Functional head (Sr. Executive/Assistant manager) shall conduct the preliminary investigation as per Annexure-I for the OOT observations due to any laboratory error and record the observations.
- In case of stability study, trending of results shall be done based on the historical data obtained from analysis of validation batches. The current data shall be compared with the historical data to analyse any drift from the trend. In case there is a significant change same shall be recorded as OOT result and shall be investigated.
- The details of OOT results with respect to analysis, stability evaluation or transportation study shall be shared with quality assurance head once the investigation has been completed.
- In case of raw material (API only), if aberrant data is observed during the analysis or during reporting of results, as compared to the report of vendor / supplier COA, or previous batch analysis results then out of trend investigation shall be conducted.
- In case of in-process samples, if result obtained at any stage of manufacturing are not comparable with analytical observation of previous batches or any aberrant result observed during analysis or during reporting of results then out of trend investigation shall be carried out.
- In case of finished product, if result obtained is not comparable with analytical observation of previous batches and for other pack size of same batch, then out of trend investigation shall be initiated.
- Functional Head of the respective section along with the analyst/person who has monitored shall investigate reasons for OOT results by checking for analytical error that shall include but are not limited to the following:
- Whether the correct SOP / test procedure has been followed.
- Weight taken for standard and sample is as per the procedure.
- Whether calculation done is correct.
- If more than one batch has been analysed at the same time then results of the other batches shall be checked.
- Instrument used for analysis is within the Calibration status.
- Instrument performance errors, if any.
- Non compliance to critical steps during analysis.
- Validity of Reference Standard, Working standard, volumetric solution and Analytical reagents.
- Sample handling/storage during analysis.
- Any specific technique such as sonication, centrifuge etc. carried out.
- Re-sampling shall be authorised by Quality assurance head only in the following cases:
- Insufficient quantity of the original sample has been withdrawn from the batch for the analysis.
- The sample got contaminated before the analysis was initiated.
- Where the sample has degraded before analysis.
- Sample intended for bio burden determination.
- Re-sample quantity shall be double of the amount than what is prescribed. One portion of the sample shall be retained as the “control sample” (where applicable) and other portion shall be used for analysis.
- During the above investigation, if the cause of OOT result is identified as laboratory error then quality control head shall conclude and authorized for repeat analysis to confirm the results after discussion with quality assurance head.
- If no assignable cause is found during the investigation, quality control head shall recommend repeating the analysis for confirming the observations after approval of quality assurance head and if repeat analysis is found similar to previous analysis, then the OOT observations shall be considered valid and the cause of OOT shall be further investigated.
If the reanalysis results are within the trend or observations are not aberrant, then the initial analysis shall be investigated for the cause of OOT and the repeat observations shall be reported.
If repeat analysis observed is not complying with specification then investigation shall be done as per SOP .
If the laboratory error is not established then the OOT investigation shall be extended to manufacturing area as per the section II of the investigation as per Annexure-I.
In the event of the OOT observation in environmental monitoring, following shall be considered for investigation:
- Personnel Practices.
- Sanitization / Cleaning Procedure.
- Qualification data of HVAC system.
- Performance of AHU.
- Filter cleaning procedure and frequency.
- Performance of other components.
- Calibration of measuring devices.
- Seasonal variation.
- Temperature / RH mapping record.
In case of OOT observation of water monitoring, following shall be considered for investigation:
- Working of various components of water system.
- Performance of water systems/data over last six months.
- Sampling Procedures.
- Drainage of water.
- Temperature of water in storage tank and distribution loop.
- Valve functioning.
- Water system sanitization procedure and frequency.
- Integrity of distribution loop.
- Calibration of measuring devices.
The investigation shall be thorough, well documented and scientifically justifiable. If necessary supportive documents for justification shall be attached
QA shall follow up to ensure the compliance of Corrective Action.
An OOT investigation should be completed within 30 days.
All documents related to OOT investigation shall be filled with respective analytical data.
Format of OOT shall be issued by QA officer.
Use For Control Charts:
For establishing the trend of existing products, data of preferably minimum 10 batches shall be collected and subjected to statistical analysis.
Subsequently for existing products, each year separate trend shall be generated by considering preferably minimum 10 released data from previous year or years.
For new product, data from first 10 or minimum 5 released batches shall be considered including validation batches.
Batches manufactured with same process and manufactured under similar condition/Controls are only required to be considered for trending of data.
The collected data shall be statistically reviewed by QA and subjected to statistical trending.
Following statistical parameter shall be used to establish the acceptance limits of variation
From the trend of analysis results, variation is identified by using following formula.
Upper Tolerance Limit (UTL) = X +KS
Lower Tolerance Limit (LTL) = X – KS
X is the mean of all results
K is tolerance factor which is constant as given in Annexure IV.
S is standard deviation
- During gummies deposition of product, considering variation in process, calculate the average and standard deviation from the individual weight of 20 randomly selected gummies.
- E.g. calculated average weight of gummy (x) with standard deviation (s).
K = Constant (Annexure-IV)
UTL = Average weight + value of k X standard deviation
LTL = Average weight – value of k X standard deviation
Numbering and filling of OOT.
OOT report number shall be assigned in the following manner:
ZZZ/OOT/XX/YYY
Where:
ZZZ | – | Initial of Company Name |
OOT | – | Represents out of trend |
\ | – | Represents separator |
XX | – | Represents last two digit of year |
YYY | – | Serial number of OOT in a particular year |
REFERENCES:
Not Applicable.
- ANNEXURES:
ANNEXURE No. | TITLE OF ANNEXURE | FORMAT No. |
Annexure-I | Investigation of out of trend (OOT) results | QA-023/F01-00 |
Annexure-II | Out of Trend (OOT) log | QA-023/F02-00 |
Annexure-III | Analytical results log. | QA-023/F03-00 |
Annexure-IV | Tolerance factor K value | QA-023/F04-00 |
DISTRIBUTION:
- Controlled Copy No. 01 : Head Quality Assurance
- Controlled Copy No. 02 : Head Quality Control
- Controlled Copy No. 03 : Head Production
- Controlled Copy No. 04 : Head Engineering
- Controlled Copy No. 05 : Head Warehouse
- Master Copy : Quality Assurance Department
ABBREVIATIONS:
SOP | : | Standard Operating Procedure |
QA | : | Quality Assurance |
QC | : | Quality Control |
CAPA | : | Corrective Action & Preventive Action |
OOT | : | Out of Trend |
OOS | : | Out of Specification |
RH | : | Relative Humidity |
AHU | : | Air Handling Unit |
REVISION HISTORY:
CHANGE HISTORY LOG
Revision No. | Details of Changes | Reason for Change | Effective Date |
00 | New SOP | Not Applicable | To be written manual |
ANNEXURE – I
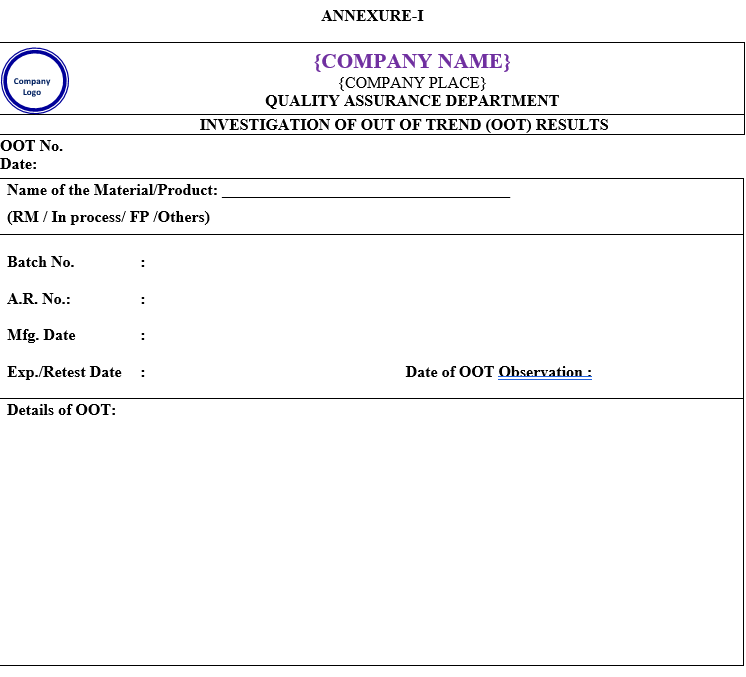
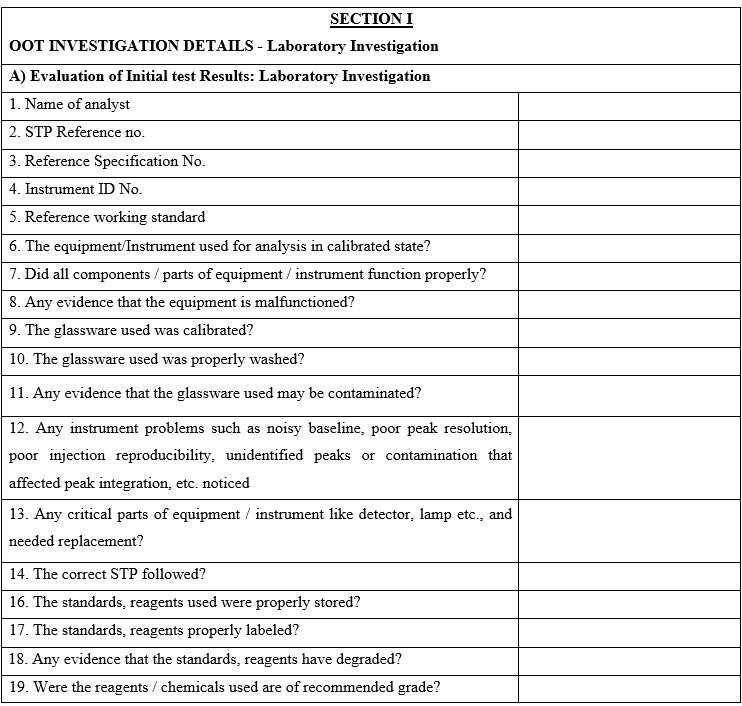
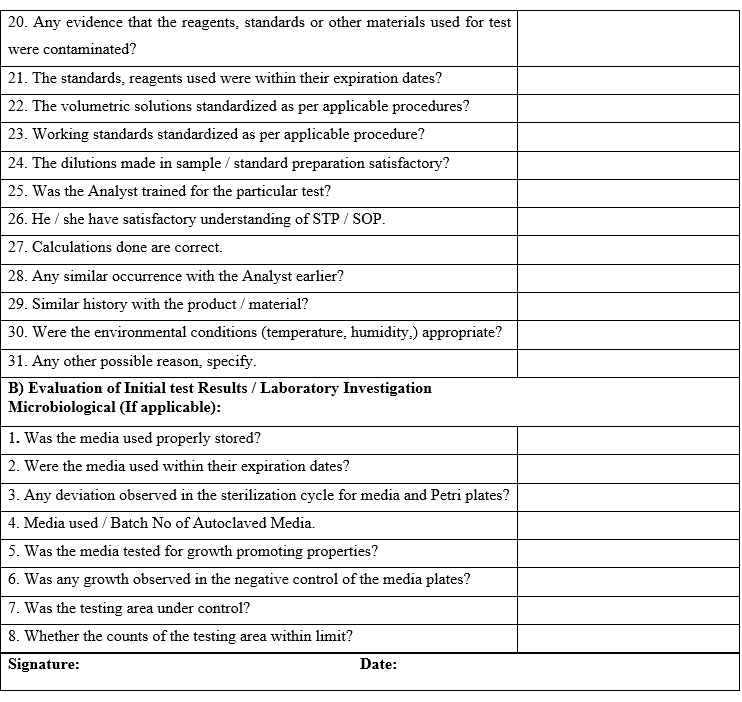
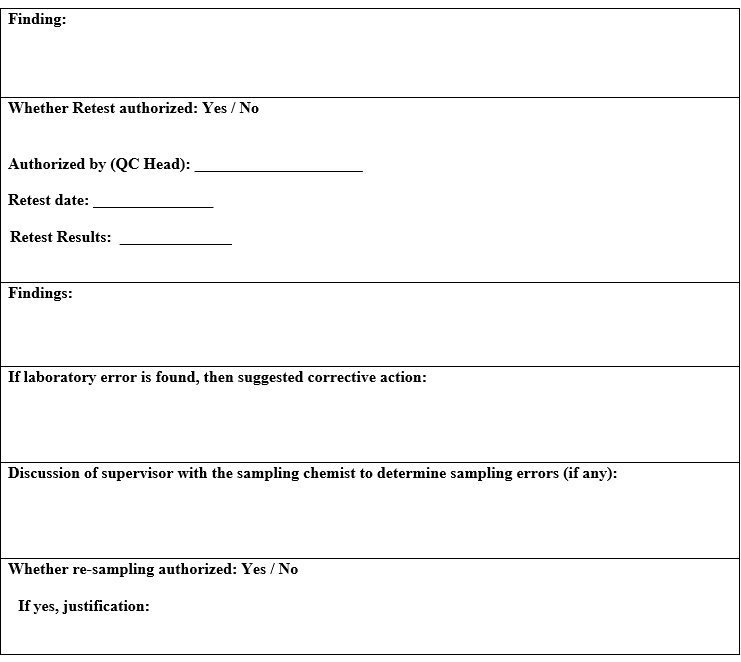
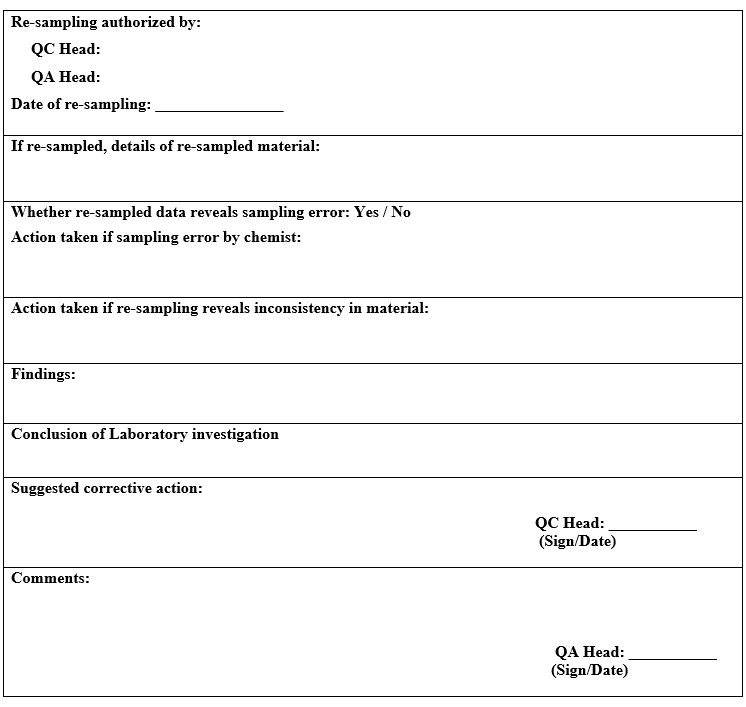
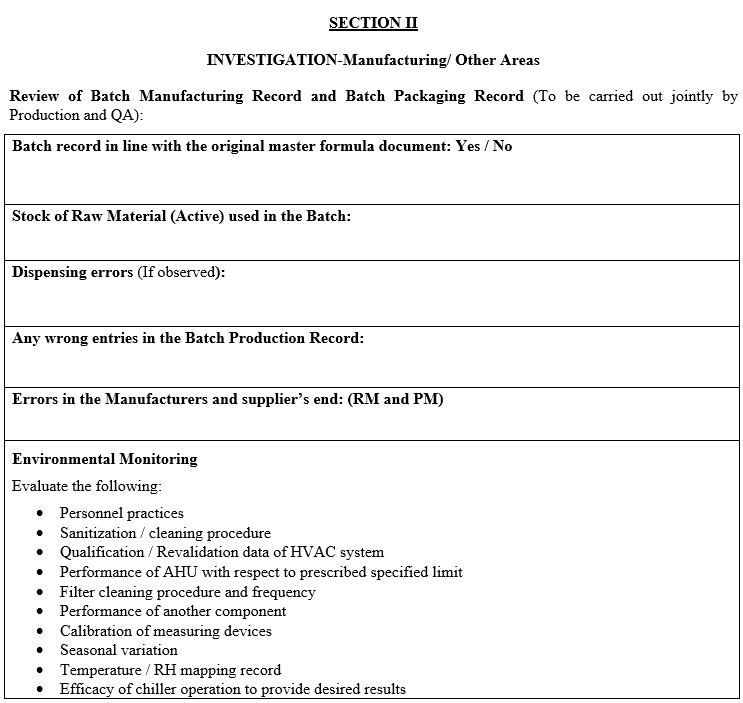
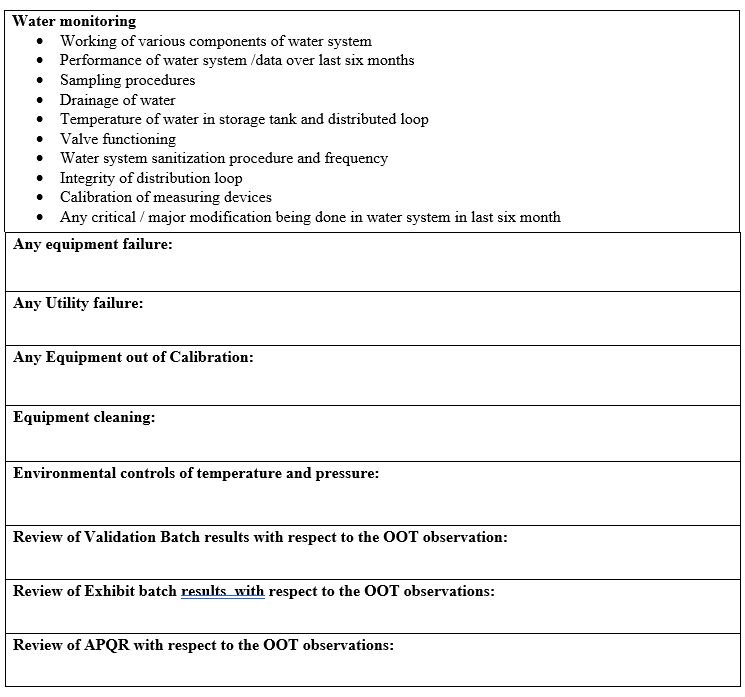
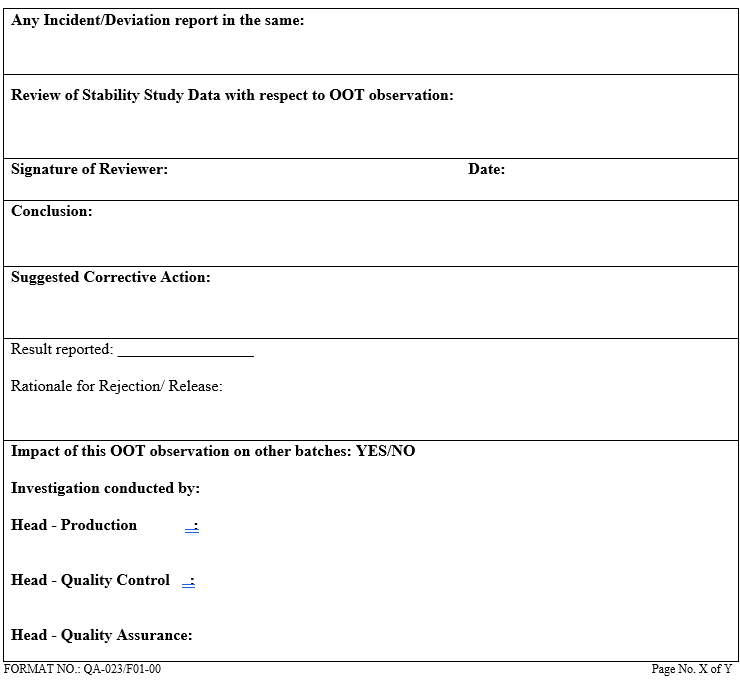
ANNEXURE – II
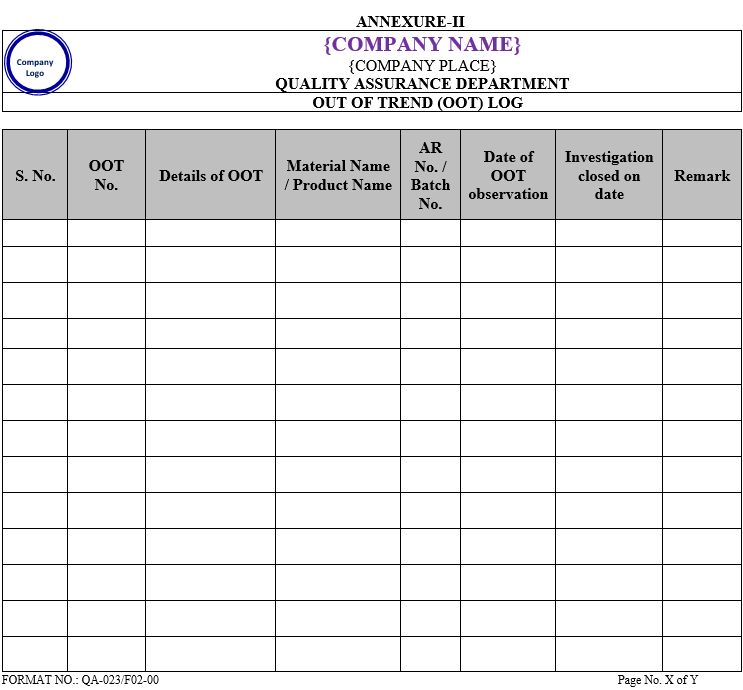
ANNEXURE-III
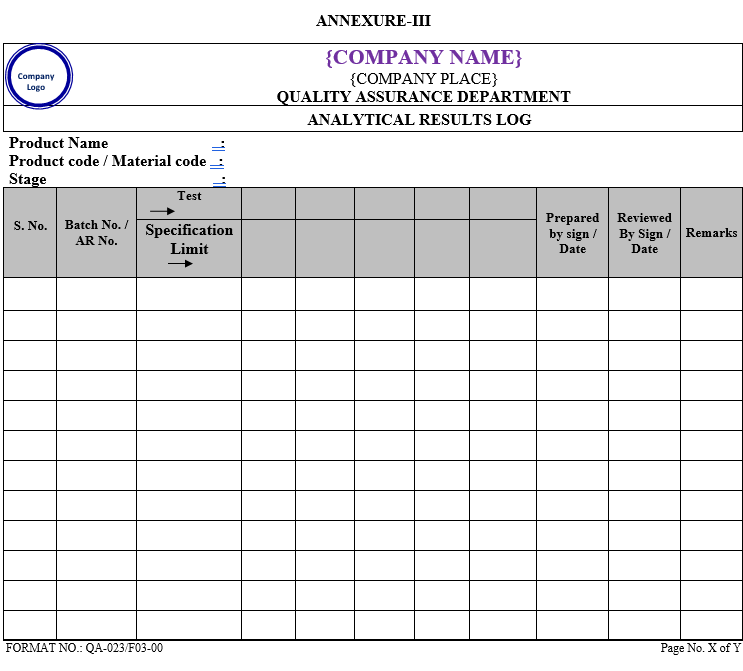
ANNEXURE-IV
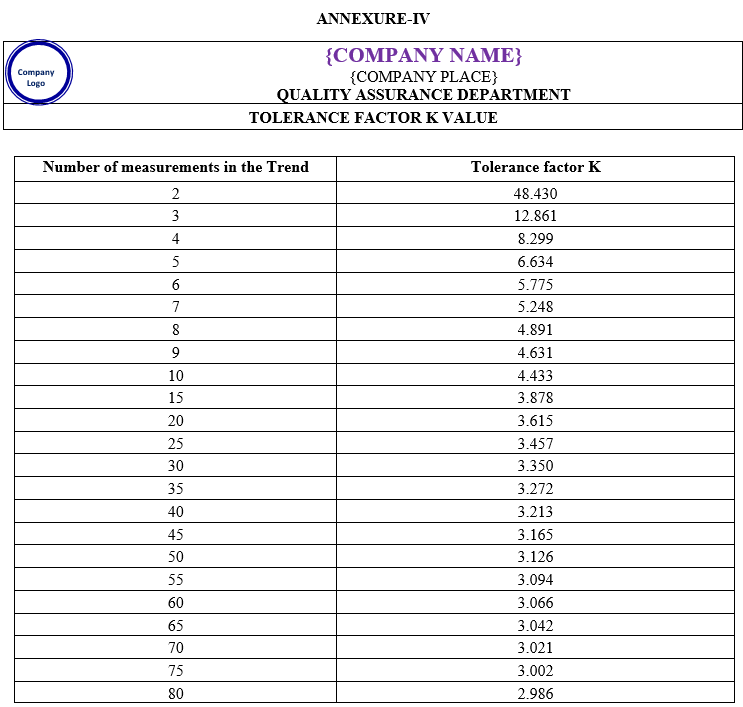
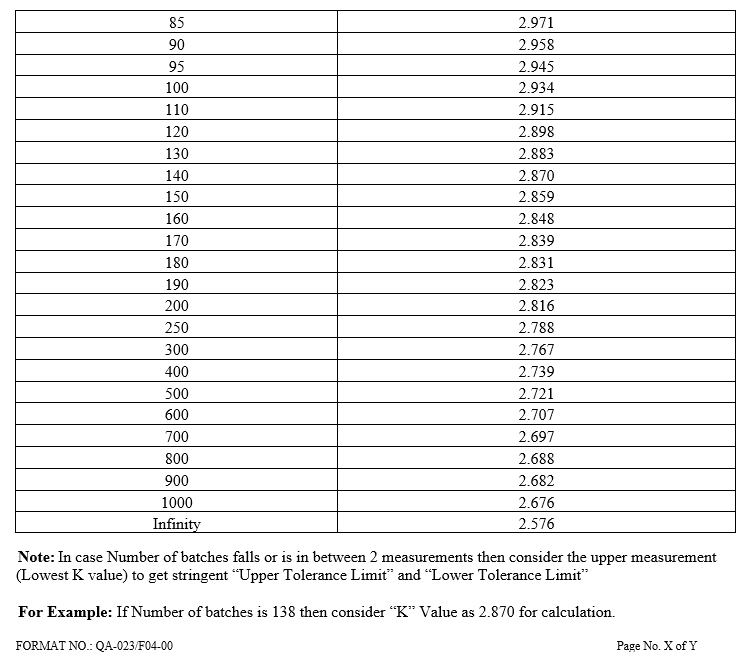
Frequently Asked Questions ?
- What is an out-of-trend (OOT) result in the pharmaceutical context?
- An out-of-trend (OOT) result refers to a deviation or a result that falls outside established specifications or trends during pharmaceutical manufacturing or testing processes.
- Why is monitoring trends important in pharmaceutical processes?
- Monitoring trends is crucial to ensure consistency and reliability in pharmaceutical processes. Deviations from established trends may indicate issues that could affect product quality and regulatory compliance.
- What are the common causes of out-of-trend results in pharmaceutical manufacturing?
- Common causes include equipment malfunctions, human errors, raw material variations, environmental factors, and changes in manufacturing processes.
- How is the out-of-trend investigation typically initiated?
- The investigation is usually initiated when a result deviates from predefined specifications or when a trend is identified through routine monitoring.
- What is the role of quality control in addressing out-of-trend results?
- Quality control plays a key role in investigating and resolving out-of-trend results. It involves thorough analysis, root cause identification, and implementation of corrective and preventive actions (CAPA).
- How does the pharmaceutical industry ensure data integrity during out-of-trend investigations?
- Data integrity is maintained through robust documentation practices, proper record-keeping, and adherence to Good Manufacturing Practices (GMP) guidelines. Transparency in the investigation process is crucial.
- What are the regulatory implications of out-of-trend results in pharmaceutical manufacturing?
- Out-of-trend results can have regulatory implications, potentially leading to non-compliance with regulatory standards. Timely and thorough investigations are essential to address and rectify issues before they escalate.
- How can pharmaceutical companies prevent recurrent out-of-trend issues?
- Prevention involves implementing effective quality management systems, ongoing process monitoring, staff training, and continuous improvement initiatives to address root causes.
- What role does statistical analysis play in managing out-of-trend results?
- Statistical analysis is used to assess the significance of deviations, identify trends, and determine if results are within acceptable limits. It provides a quantitative approach to decision-making during investigations.
- How does the pharmaceutical industry ensure transparency in communicating out-of-trend findings?
- Transparency is maintained through clear documentation, effective communication between departments, and reporting to regulatory authorities when necessary. Open communication helps in addressing issues promptly and implementing corrective actions.