- OBJECTIVE:
To lay down a procedure for the introduction of new product in the facility.
- SCOPE:
This SOP is applicable for proper introduction of any new product at {Company Name} {Company Location}.
- RESPONSIBILITY:
- Head F&D shall provide the documents for introduction of new product to site.
- Head Purchase shall flow the information for introduction of new product.
- Executive/Officer QA shall review and compile the documents.
- Head ARD shall provide the specification and standard test procedure for new product.
- Head QC shall ensure the preparation of preparation of specification of raw material/packing material, finished product & stability specification.
- Head F&D Provide the MFR of new drug or any change in formulation of existing product.
- Head Production shall ensure the required manufacturing and packing facility for new product.
- ACCOUNTABILITY:
Head QA and Plant Head shall be accountable for compliance of this SOP.
- PROCEDURE:
A new product initiation shall be divided into four categories
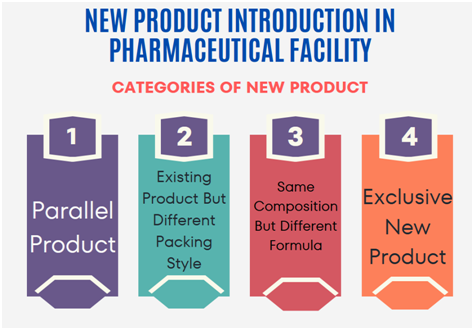
Click the link for download word file copy of this document: https://pharmaguidehub.com/product/standard-operating-procedure-for-new-product-introduction-in-facility/
- Parallel Product:
- In such type of product, the following parameter like Composition, Formulation, Specification/Method, Die & Punch, change part and packing description all should be same with existing product.
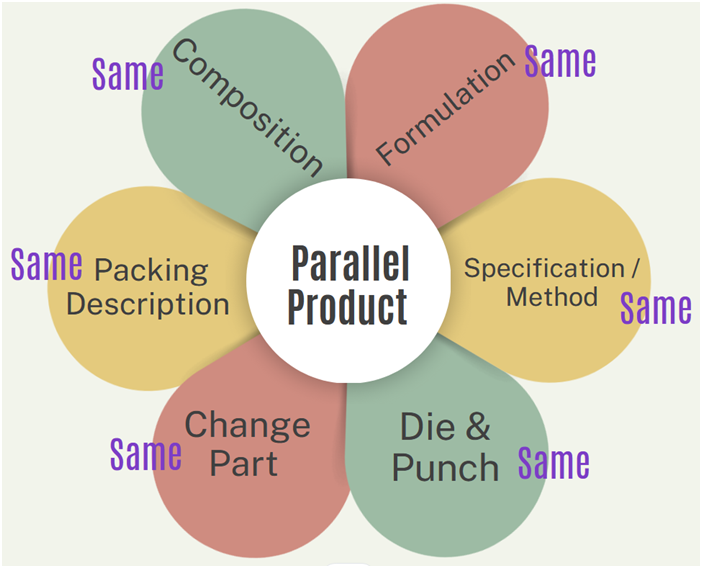
- After receipt of requirement for any new product from any party following activities shall be carried out:
- Purchase Department shall inform to all concern departments about any new product and coordinate with F&D for providing all relevant documents.
- Executive QA shall review all document such as MFR/Analytical specification, stability data, and initiate the change control for introduction of new product.
- Executive QA shall prepare the risk evaluation for introduction of new product and same shall be reviewed by Production, Quality Control and Quality Assurance and finally approved by Head QA/designee.
- Executive QA shall share the document received from F&D to Head Production and Head Quality Control for review. Head QC and Head Production shall review all document and identify the requirement for manufacturing and testing of new product.
- QA shall ensure Mfg. Lic., Batch Size, Shelf Life, Batch Numbering System and coordinates to all concern departments.
- Packing development department shall coordinate with the party for artwork of product and shall develop the artwork for new product to be manufactured at site and shall forward to site QA for review.
- QA and Production shall review the artwork and finally Head QA/designee shall approve the artwork.
- Purchase department shall coordinate with vendor for shade card of printed packing material. Shade cards shall be approved by Head QA/designee, after the approval of shade card purchase department shall coordinate for procurement of packing material from vendor.
- Production and Quality Control department shall raise the requirement for additional items such as change parts, chemicals etc. required for manufacturing and testing of new product.
- Purchase department shall arrange the requirement as required by Production and Quality Control.
- QC Department shall provide specification & Standard Test Procedure on the basis of parallel product.
- Production Department shall prepare BMR & BPR as per parallel product; BMR & BPR shall be reviewed by Head production and approved by QA Department.
- QA Dept. shall circulate the check list to all concerned department as per Annexure-I (for their approval along with attachment
Click the link for download word file copy of this document: https://pharmaguidehub.com/product/standard-operating-procedure-for-new-product-introduction-in-facility/
- Existing Product But Different Packing Style:
- In Such products, all parameters shall be same (e.g. composition, formulation, specification/method, dies & punches) with existing product but packing change part and its description shall be different.
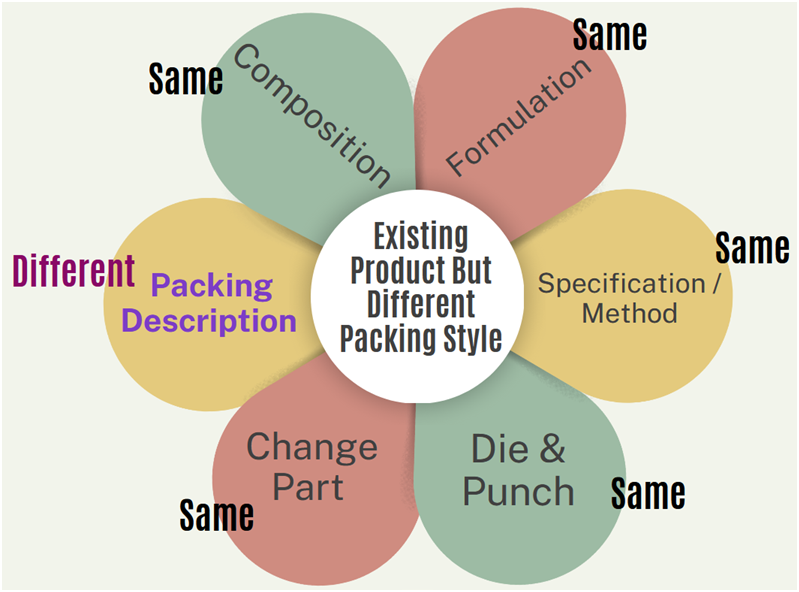
- After receiving requirement of any new product from any party following activities shall be carried out
- Purchase Department shall inform to all concern department about any new product with all available related documents and detailed composition.
- Packing development department shall coordinate with the party for artwork of product and shall develop the artwork for new product to be manufactured at site and shall be forward to QA for review.
- QA and production shall review the artwork and finally Head QA/designee shall approve the artwork.
- Purchase department shall coordinate with vendor for shade card of printed packing material. Shade cards shall be approved by Head QA/designee. After the approval of shade card purchase department shall coordinate for procurement of packing material from vendor.
- Production and Quality control department shall raise the requirement for additional items such as change parts, chemicals etc. required for manufacturing and testing of new product.
- Purchase department shall arrange the requirement as per required by production and Quality control.
- QA shall ensure Mfg. Lic., Batch size, Shelf life, Batch Numbering System and coordinates to all concern departments.
- QC Department shall provide Specification & Standard Test Procedure on the basis of product requirement.
- BMR and BPR shall be prepared by production department; shall be checked by Head Production as per requirement (Packing Specification or pack profile) and approved by QA Department.
- QA Department shall circulate the check list to all concern departments for approval as per Annexure-I along with attachment of all reference documents
- Same Composition But Different Formula:
- Such type of product have same composition with parallel product but different Formulation, Specification /Method, Die & Punch, Change Part and Packing Description with our parallel product.

- After receipt of requirement for any new product from any party following activities shall be carried out.
- Purchase Department shall inform to all concerned departments about new product with all related available documents with detailed composition.
- F&D Department shall develop the formulation as per requirement and submit MFR to Quality Assurance.
- ARD/QC shall be provided Specification & Standard Test Procedure.
- Executive QA shall review all document such as MFR/Analytical specification, stability data etc, and initiate the change control for introduction of new product.
- Executive QA shall prepare the risk evaluation for introduction of new product and same shall be reviewed by production, Quality Control and Quality Assurance and finally approved by Head QA/designee.
- Executive QA shall share the document received from F&D to Head Production and Head Quality Control for review. Head QC and Head Production shall review all document and identify the requirement for manufacturing and testing of new product.
- Production and Quality Control department shall raise the requirement for additional items such as change parts, chemicals etc. required for manufacturing and testing of new product.
- Purchase department shall arrange the requirement as per required by Production and Quality Control
- Production Department shall be prepared BMR & BPR as per MFR; BMR/BPR shall be checked by Head Production and approved by QA Department.
- QA Department shall circulate the check list to all concern departments for approval as per Annexure-I along with attachment of all reference documents.
Click the link for download word file copy of this document: https://pharmaguidehub.com/product/standard-operating-procedure-for-new-product-introduction-in-facility/
- Exclusive New Product
- In this type of product the drug is launched first time at the facility.
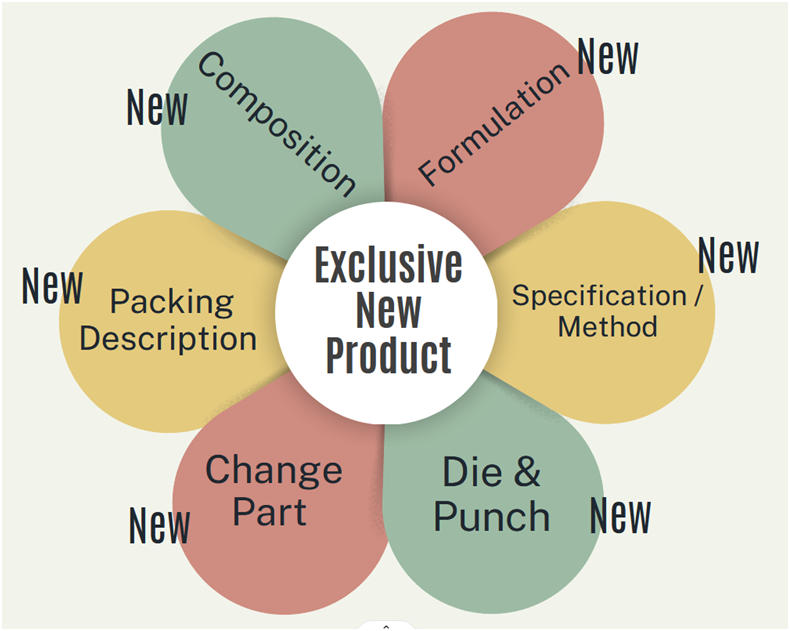
- After receipt of requirement for any new product from any party following activity shall be carried out
- Purchase Department shall inform to all concern departments for any new product with all related documents available with detailed composition.
- F&D Department shall develop the formulation as per requirement and submit MFR to Quality Assurance.
- ARD Department shall be Develop the Analytical Method Validation and provide the specification & Standard Test Procedure.
- Executive QA shall review all document such as MFR/Analytical specification, stability data etc., and initiate the change control for introduction of new product.
- Executive QA shall prepare the risk evaluation for introduction of new product and same shall be reviewed by Production, Quality Control and Quality Assurance and finally approved by Head QA/designee.
- Executive QA shall share the document received from F&D to Head Production and Head Quality Control for review. Head QC and Head Production shall review all document and identify the requirement for manufacturing and testing of new product.
- QA shall ensure Mfg. Lic., Batch Size, Shelf Life, Batch Numbering System and coordinates to all concern departments.
- Packing development department shall coordinate with the party for artwork of product and shall develop the artwork for new product to be manufactured at site and shall forward to site QA for review.
- Site QA and Production shall review the artwork and finally Head QA/designee shall approve the artwork.
- Purchase department shall coordinate with vendor for shade card of printed packing material. Shade cards shall be approved by Head QA/designee. After the approval of shade card purchase department shall coordinate for procurement of packing material from vendor.
- Production and Quality Control department shall raise the requirement for additional items such as change parts, chemicals etc. required for manufacturing and testing of new product.
- Purchase department shall arrange the requirement as required by Production and Quality Control.
- QC Department shall provide specification & Standard Test Procedure on the basis of parallel product.
- Production Department shall prepare BMR & BPR as per parallel product; BMR & BPR shall be reviewed by Head Production and approved by QA Department.
- Procurement Department shall be provided art work for checking to QA with change part details as per party requirement, Procurement Department shall also provide party’s earlier artwork and/or packaging component (if available).
- QA department shall prepare the MFR at site on the basis of the MFR received from F&D as per the SOP.
- QA Department shall be prepared Bill of Material (BOM) for Raw & Packing Materials as per Annexure-II & Annexure-III respectively on the basis of MFR, approved artwork/print proof approval checklist and approved pack profile.
- After approval of Bill of Material, QA shall distribute one copy to Production for BMR preparation and one copy to packing department for BPR preparation.
- Copy of Approved BOM sheet shall be disturbed to Procurement, Production/Packing & QA Department.
- Production Department shall prepared BMR & BPR on the basis of MFR, Approved Artwork, Pack Profile, Approved Bill of Materials & Product Permission.
- QA Department shall circulate the check list to all concern departments for approval as per Annexure-I along with attachment of all reference document.
Click the link for download word file copy of this document: https://pharmaguidehub.com/product/standard-operating-procedure-for-new-product-introduction-in-facility/
- REFERENCES:
Not Applicable
- ANNEXURES:
ANNEXURE No. | TITLE OF ANNEXURE |
Annexure- I | Checklist for New Product initiation |
Annexure-II | Bill of Material (Raw Material) |
Annexure-III | Bill of Material (Packing Material) |
- DISTRIBUTION:
Controlled Copy No. 01 | : | Head Quality Assurance |
Controlled Copy No. 02 | : | Head Quality Control |
Controlled Copy No. 03 | : | Head Production |
Controlled Copy No. 04 | : | Formulation and Development |
Controlled Copy No. 05 | : | Analytical Research Development |
Controlled Copy No. 06 | : | Purchase |
Master Copy | : | Quality Assurance Department |
- ABBREVIATIONS:
SOP | : | Standard Operating Procedure |
No. | : | Number |
QA | : | Quality Assurance |
F&D | : | Formulation and Development |
ARD | : | Analytical Research Development |
MFR | : | Master Formulation Record |
BMR | : | Batch Manufacturing Record |
BPR | : | Batch Packing Record |
FDA | : | Food and Drug Administration |
- REVISION HISTORY:
CHANGE HISTORY LOG
Revision No. | Details of Changes | Reason for Change | Effective Date |
00 | New SOP | Not Applicable | To be written manual |
ANNEXURE – I
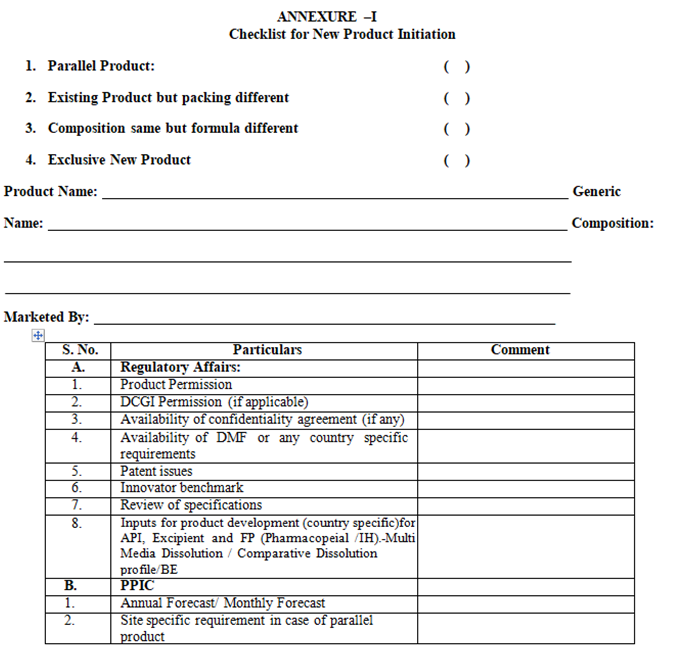

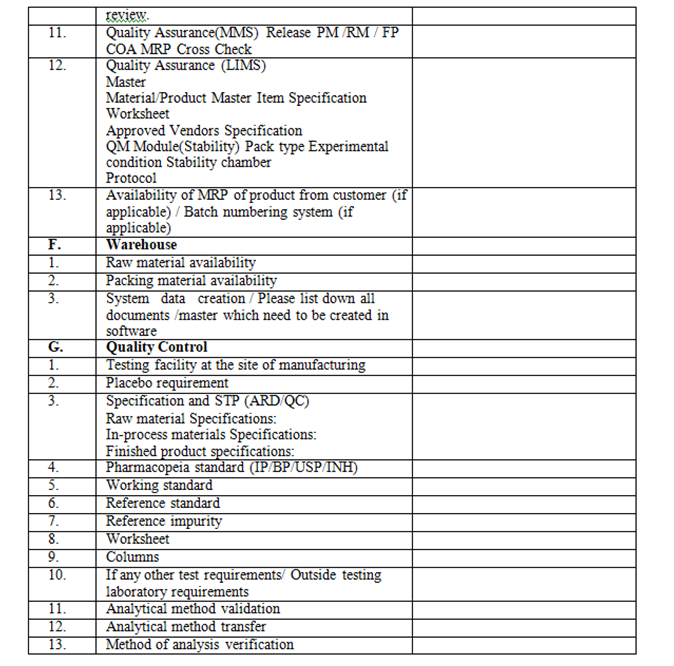
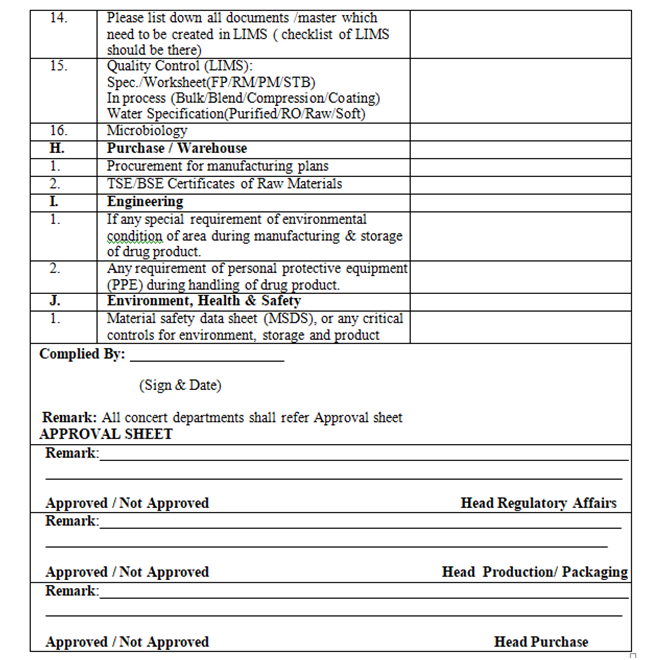
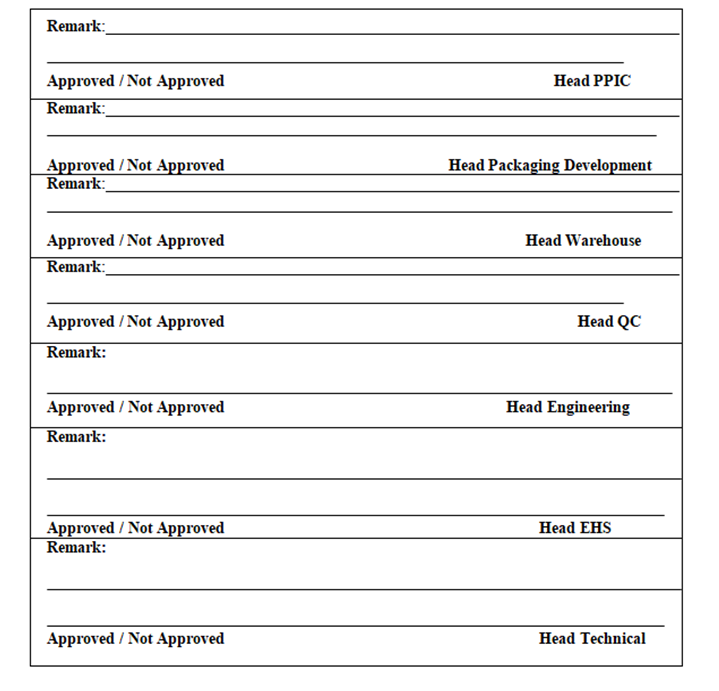

ANNEXURE – II
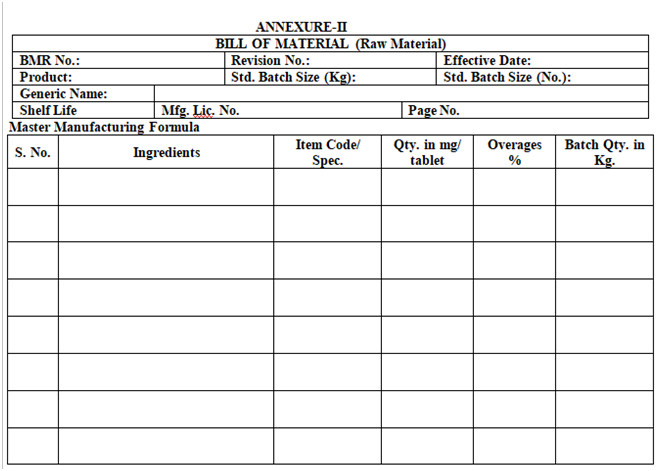
ANNEXURE-III
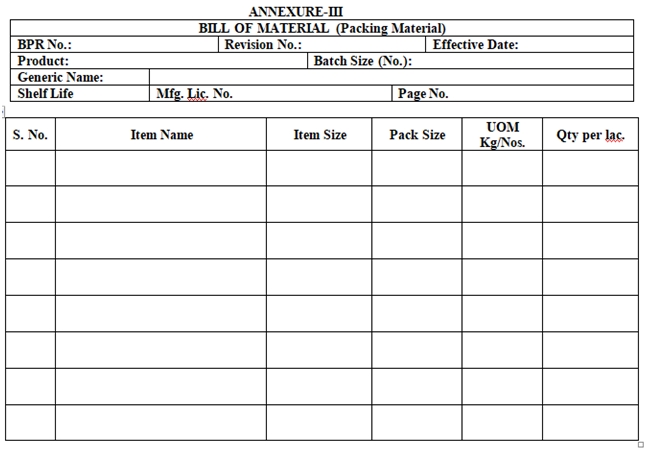
Click the link for download word file copy of this document: https://pharmaguidehub.com/product/standard-operating-procedure-for-new-product-introduction-in-facility/
Frequently Asked Question?
- Q: Why is a thorough assessment necessary before introducing a new pharmaceutical product?
- A: A comprehensive assessment helps ensure that the new product complies with regulatory standards, is compatible with existing manufacturing processes, and meets quality and safety requirements.
- Q: What are the key regulatory considerations when introducing a new pharmaceutical product?
- A: Regulatory considerations include obtaining necessary approvals from health authorities, compliance with Good Manufacturing Practices (GMP), and adherence to specific guidelines for the pharmaceutical industry.
- Q: How do you determine the manufacturing capacity required for the new product?
- A: The manufacturing capacity is determined by considering the anticipated market demand, production timelines, and the capabilities of the existing facility. It involves assessing equipment availability, production lines, and resource allocation.
- Q: What steps are taken to ensure the compatibility of the new product with existing manufacturing processes?
- A: Compatibility is ensured through process validation studies, equipment qualification, and risk assessments. Any necessary modifications to existing processes are carefully evaluated and implemented.
- Q: How is the quality control and assurance process adapted for a new pharmaceutical product?
- A: The quality control and assurance process is adapted by developing new testing protocols, validating analytical methods, and ensuring that quality standards are met at every stage of manufacturing.
- Q: What measures are in place to address potential supply chain challenges during the introduction of a new product?
- A: Strategies include establishing alternative suppliers, securing critical raw material stocks, and developing contingency plans to mitigate any potential disruptions in the supply chain.
- Q: How is the training of personnel managed during the introduction of a new product?
- A: Training programs are developed to educate personnel on the specifics of the new product, including manufacturing processes, quality control procedures, and safety protocols. Continuous training is provided to ensure ongoing compliance.
- Q: What role does risk management play in the introduction of a new pharmaceutical product?
- A: Risk management involves identifying potential risks, assessing their impact, and implementing measures to mitigate or eliminate them. This includes evaluating risks related to manufacturing, quality, regulatory compliance, and supply chain.
- Q: How do you ensure communication and collaboration between different departments during the introduction of a new product?
- A: Regular cross-functional meetings, clear communication channels, and collaboration tools are essential to facilitate information sharing between departments such as research and development, manufacturing, quality control, and regulatory affairs. Refer Attachment I
- Q: What post-introduction monitoring processes are in place to ensure the ongoing success of the new product?
- A: Post-introduction monitoring involves ongoing quality control, regular audits, and continuous improvement initiatives. Feedback from the market and any adverse events are carefully monitored and addressed promptly.
Click the link for download word file copy of this document: https://pharmaguidehub.com/product/standard-operating-procedure-for-new-product-introduction-in-facility/