- OBJECTIVE:
To describe a procedure for performing the smoke studies in the clean rooms, thereby which assure that the HVAC systems are performing as designed.
- SCOPE:
This procedure is applicable to smoke studies being performed as part of HVAC qualification in static and dynamic conditions at {Company Name} {Location}.
- RESPONSIBILITY:
- Quality Assurance: Preparation and approval of the qualification documents for the activity.
Gather and check the completeness of documents, supervise their preparation, distribution and archiving. Ensure that the tests and/or checks are carried out by qualified personnel in possession of the necessary technical experience. Review the results of the tests and/or checks and approve the results in relation to deviation reports, define and carry out any corrective actions, define the intervention plan and methods for execution of new checks, obtain and evaluate the results produced by the corrective actions and approve them. Approve the report and the final qualification summary. Ensure that during airflow visualization for operational activities, aseptic practices and behaviour are reflective of production activities
- Engineering: Provide operating procedures, drawings, manuals and all documentation necessary for the preparation and execution of tests and/or checks as anticipated in the qualification protocol. Ensure that the calibration of all process equipment is maintained in accordance with the approved procedures. Provide appropriate material for execution of the tests (if applicable).
- ACCOUNTABILITY:
QA Head shall be Accountable for implementation of SOP.
- PROCEDURE:
- General: Smoke studies or airflow visualizations are planned activities; these are performed as part of the HVAC qualification of clean rooms. The purpose of this test is to confirm either the airflow direction or airflow pattern or both in regard to the design and performance specifications. The smoke test or airflow visualizations are required to be done in clean rooms at both “at rest” and “In operation” conditions. This test helps identify and minimize airflow disruptions or turbulence in the unidirectional airflow zones caused during manufacturing.
Click the link to download word file copy of this document: https://pharmaguidehub.com/product/air-flow-visualisation-studies-in-pharmaceutical/
- Due to personnel interventions and to establish the optimal personnel position during those required line interventions.
- Determine, based on the obtained results, if the personnel intervention is sound and poses a limited microbiological risk for the processing of the products.
- Provide additional support for the definition of the sampling points for routine environmental monitoring procedures.
- Precautions:
- Personnel shall be wearing appropriate safety masks as required by the smoke generator equipment recommendations.
- All equipment and personnel not pertaining to the normal operation of the line should be located outside the zone surrounding the filling line in order to avoid additional turbulence.
- The video tape equipment should always remain outside the Laminar Air Flow Area.
- Smoke Generation:
- For the purpose of generation of smoke, a clean room acceptable smoke generator or alternatively dry ice and cold-water mix can be used.
- For capturing the airflows, a video camera shall be used.
- Ensure that personnel participating in the studies are adequately trained; equipment/ instrument used in the studies have to be appropriately calibrated.
- Apply smoke from the smoke generator; this gets immediately diffused to the surroundings, start capturing the air flow diffusion within the unidirectional flow zones using the video camera.
- Airflow smoke test studies in the unidirectional airflow zones “At rest” conditions:
- “At rest” Smoke studies shall have include verification of following points in minimum:
- At the floor level
- On exit from the filter face
- In the critical working zones such as Cool zone, aseptic corridor, aseptic filling area (machines in operation) the operation of which may influence the flow direction.
- The smoke studies in the “at rest” conditions, shall meet to acceptance criteria given below:
- The air flow movement in the unidirectional flow zone does not cause vortices or drag with consequent reversal, including local reversal of the flow.
- The airflow in the critical zones is unidirectional.
- There is not air penetration from the surrounding zones to the unidirectional zones
- The air directed out onto the floor does not rebound from there it to critical zones
- Airflow smoke test studies in the unidirectional airflow zones under dynamic conditions:“Under Dynamic condition” Smoke studies shall include verification of air visualization and shall capture all specified interventions.
- Primary interventions: these interventions are evaluated by pulsing small amounts of smoke approximately 10 to 20 cm directly above the portion of the operator inside the critical area. The direction of the airflow is observed and documented.
- Secondary interventions: these interventions are evaluated by pulsing small amounts of smoke approximately 10 to 20 cm directly above the operator standing in the optimal position. The smoke is pulsed over the operator’s head, arms and hand to identify the turbulent air created by the operator and any effect that it may have on the flow of air in the critical area immediately adjacent to the tool held by the operator as part of the simulated intervention.
- A list of all authorized interventions for each aseptic operation shall be prepared; this shall be attached to the Validation Document and shall be approved by Quality Assurance.Airflow visualization under dynamic conditions shall be performed including simulated Production Conditions.
- Simulated production conditions as mentioned below are required to be covered in minimum during the airflow visualization during dynamic state:Unloading of the rubber bungs from the bung processor Aseptic connection of the sterilizing filter to the solution tankMovement of sterile API canister (Dummy)Assembling of the Filling Machine parts Aseptic connection of the solution tank to the filling manifold, Opening the tunnel gate Alignment of filling needles Stopper bowl loading Removal of overturned vials from the conveyor and primary accumulating tableRemoving of vials for check weighing Removing jammed stoppers from the stopper trackChange syringe, change filling valve, change tubing to filling needle, and change tubing between manifold and filling valve
- Fill volume adjustmentRemoving the jammed vials at the tray loaderAPI Canister attachment/ detachment and reattachment Environmental monitoring practices (probes, plates replacement)Lyophilized loading, Lyophilized unloading, Air flow visualization during/ after power failure & resume, i.e. flow from in feed to tunnel, filling room to corridor, flow from filling to sealing etc.
- Air flow visualization in filling zone, keeping the filling door in open condition. The time should be equivalent to that of the time taken to trigger alarm in case of DP disturbances, etc.
- The operator position in the Filling Line Layout shall be clearly observed and stated during the studies (this can be primary/ secondary intervention).
- The methodology and the procedure for execution of smoke study shall be carried out as per the approved Validation Protocol.
- Validation Protocol for smoke study shall contain the following details, but not limited to;Protocol Approval Objective Scope Responsibility Safety related aspects Documentation Verification System Performance Verification Test Methodology Acceptance Criterion Documentation ProceduresGeneral Conclusions
- Validation Report for smoke study shall contain the following details, but not limited to:
- Report Approval
- Details of Validation Team
- Details of Validation Execution (documented evidence for tests)
- Non Conformance and Deviations during study, if any.
- Summary and Conclusions
- Attachments (such as list of interventions, timestamps of specific interventions and activities, training formats, CDs reference number)
Click the link to download word file copy of this document: https://pharmaguidehub.com/product/air-flow-visualisation-studies-in-pharmaceutical/
- Acceptance criteria:
- There should be unidirectional air flow from supply air register to the return raiser.
- There should not be any turbulence/limited distortion of unidirectional air flow during manned condition.
- Frequencyof periodic re-validation:
- Airflow visualization shall be conducted initially as part of the HVAC qualification both “At rest” and “Under Dynamic” conditions.
- Airflow visualizations shall be re-performed whenever there is major modification done to the clean rooms which shall include major modifications done to the equipments in:
- Washing and sterilization area
- Filling line of the filling area
- Stoppering area
- Lyophilization loading and unloading area
- Sterile compounding and filtration area
- The study shall be periodically repeated at least once in 2 years
- Documentation and Results:Each smoke study shall be conducted based on the approved Validation Protocol.
- The protocol shall define the objective and content of the study along with all interventions as required. Video footage of the smoke flow from different angle-shots shall be taken, in order to obtain exhaustive documentation of the effects measured.
- The results of the tests shall be recorded in the Validation Summary Reports. The video footage tapes shall be stored in secure condition; these shall be appropriately numbered before archiving with the reference protocol number.
- The time stamp from the video footage of various areas airflow visualizations shall be identified during review, the same shall be documented in the Validation Summary Report for ease of future reviews.
- If the test shows that the flow movement is not compliant with the acceptance criteria specified, a PNC shall be initiated and investigation shall be carried out to identify the root cause as per SOP.
- Appropriate corrective measures shall be taken and tests shall be repeated. Non Conformance observed (if any) during the testing shall be documented in the Summary Report.
- Contractors/ External Parties for study:
- External parties for performing the air flow visualization studies may be allowed. Assessment of the external party’s capabilities in providing these services shall be verified before allowing them to work.
- The assessment shall include verification of the history of the customer, the eligibility and experience of the technical staff, the calibration standards being followed by the agency and also the standard instruments, as required.
- A formal Contract Agreement with external customers to perform these activities shall be in place.
- Procedure/methodology of the external agency (if used) shall be reviewed for acceptability by plant personnel before use. However, such procedures followed and standard used to define those procedures are required to be documented along with studies.
- Each activity performed by such external agency shall be verified by the QA personnel.
- Contractors/ External Parties for study:
- REFERENCES:
Not Applicable
- ANNEXURES:
Annexure Number | Title of annexure |
Annexure-I | List of authorized interventions simulated during Smoke Study |
- DISTRIBUTION:
- Controlled Copy No. 01 : Head Quality Assurance
- Controlled Copy No. 02 : Head Engineering
- Controlled Copy No. 03 : Head Production
- Master Copy : Quality Assurance Department
- ABBREVIATIONS:
PNC | : | Process Non Conformance |
No. | : | Number |
SOP | : | Standard Operating Procedure |
HVAC | : | Heating Ventilation Air Conditioning |
QA | : | In process Quality Assurance |
API | : | Active Pharmaceutical Ingredients |
- REVISION HISTORY:
CHANGE HISTORY LOG
Revision No. | Details of Changes | Reason for Change | Effective Date |
00 | New SOP | Not Applicable | To Be Enter Manual |
Click the link to download word file copy of this document: https://pharmaguidehub.com/product/air-flow-visualisation-studies-in-pharmaceutical/
ANNEXURE-I
LIST OF AUTHORIZED INTERVENTIONS SIMULATED DURING SMOKE STUDY
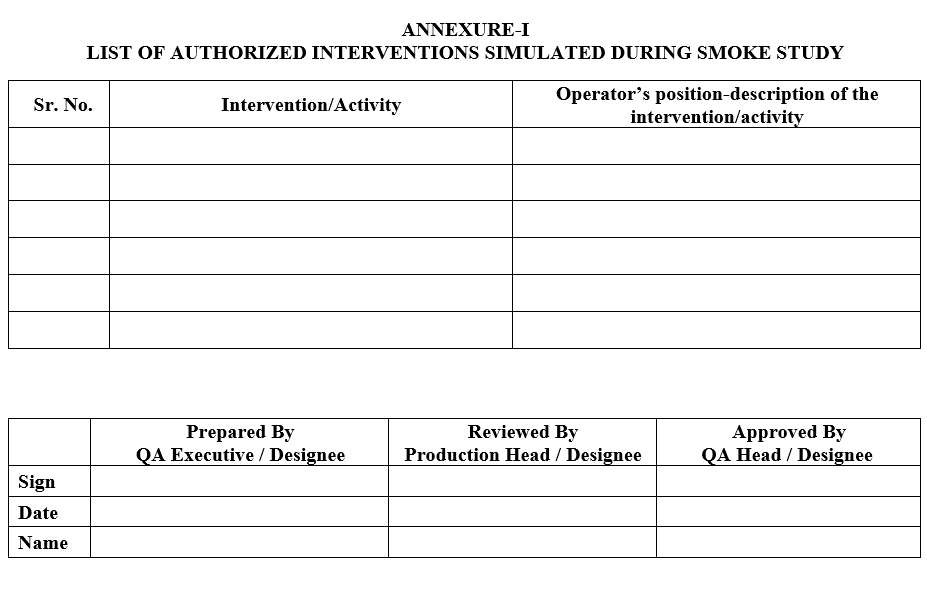
Frequently Asked Question?
Q: What is the purpose of air flow visualization studies in the pharmaceutical industry?
A: Air flow visualization studies in the pharmaceutical industry serve the purpose of assessing and understanding the patterns of air movement within controlled environments such as cleanrooms. These studies are crucial for ensuring the maintenance of aseptic conditions and preventing contamination during pharmaceutical manufacturing processes.
Q: How are air flow visualization studies conducted in pharmaceutical settings?
A: Air flow visualization studies involve the use of techniques such as smoke studies, tracer gas studies, and particle counting. Smoke studies use visible smoke to trace air movement patterns, while tracer gas studies involve the release of a detectable gas to track its dispersion. Particle counting measures airborne particles to evaluate the effectiveness of air filtration systems.
Q: Why is it important to control air flow in pharmaceutical manufacturing?
A: Controlling air flow is essential in pharmaceutical manufacturing to maintain a clean and sterile environment. Proper air flow helps prevent the spread of contaminants, such as particles and microorganisms, which can compromise the quality and safety of pharmaceutical products. It ensures adherence to regulatory standards and compliance with Good Manufacturing Practices (GMP).
Q: What are the key parameters assessed during air flow visualization studies?
A: Key parameters assessed during air flow visualization studies include air velocity, direction of air movement, turbulence, and the effectiveness of air exchange rates. These parameters help determine whether the air circulation within cleanrooms is sufficient to meet the required cleanliness standards.
Q: How do air flow visualization studies contribute to the validation of cleanroom facilities?
A: Air flow visualization studies play a vital role in the validation process of cleanroom facilities by providing evidence that the design and operational parameters are effective in maintaining the required level of cleanliness. Successful studies ensure that cleanrooms meet regulatory requirements and are suitable for pharmaceutical manufacturing processes.
Q: What challenges or issues can air flow visualization studies identify in pharmaceutical facilities?
A: Air flow visualization studies can identify issues such as dead zones where air circulation is insufficient, turbulent airflow patterns that may lead to cross-contamination, and areas with inadequate filtration. These studies help pharmaceutical companies address potential problems, optimize cleanroom design, and improve manufacturing processes to ensure product quality and safety.
Q: How often should air flow visualization studies be conducted in pharmaceutical manufacturing?
A: The frequency of air flow visualization studies in pharmaceutical manufacturing depends on factors such as the type of manufacturing processes, the level of cleanliness required, and regulatory guidelines. Typically, these studies are conducted during the initial qualification of cleanrooms and then periodically as part of routine monitoring and validation protocols. Regular assessments ensure ongoing compliance with quality standards.
Click the link to download word file copy of this document: https://pharmaguidehub.com/product/air-flow-visualisation-studies-in-pharmaceutical/