OBJECTIVE:
To lay down a Procedure for Filter Cleaning, Inspection, Replacement and Discard.
SCOPE:
This SOP is applicable for Filter Cleaning, Inspection, Replacement and Discard at {Company Name} {Location}.
RESPONSIBILITY:
Technician- Follow the instruction as per procedure.
Engineering Officer/Executive- Execution as per laid down procedure.
Engineering Head- Technical correction, review, training & monitoring of SOP.
ACCOUNTABILITY:
Engineering Head
Quality Assurance Head
ABOUT FILTER CLEANING:
Cleaning AHU filters in pharmaceutical settings is a highly controlled process. Pre-filters, designed for larger particles, can often be washed or vacuumed. However, HEPA filters, which are crucial for removing fine contaminants, are usually not washable due to their delicate nature. Cleaning HEPA filters risks damaging the filter media, compromising its efficiency. Therefore, they are typically replaced at predetermined intervals or when monitoring indicates a decline in performance. Strict protocols dictate the handling and disposal of used filters to prevent contamination. Cleanroom personnel must adhere to validated cleaning procedures, wearing appropriate protective equipment, and documenting all cleaning activities. This ensures compliance with regulatory requirements and maintains the integrity of the controlled environment.
PROCEDURE:
Precautions and general conditions:
Refer the filter cleaning schedule and equipment availability for filter cleaning.
Put status board as ‘UNDER CLEANING’ on equipment.
Use necessary safety wears like proper gowning and PPE like 3M protective nose mask, goggles, gloves safety shoes if required.
Before starting the cleaning activity isolate the equipment power supply.
Check the number of filters to be cleaned with respect to size, type and number.
Handle the filters carefully during removing, cleaning and fixing the filters.
Engineering officer/executive shall prepare the filter cleaning schedule from the beginning of the year.
The filter cleaning schedule shall be prepared based on the quantity of the cleanable filters as per Annexure-II.
Filter cleaning intimation shall be given by engineering officer/executive to the user department for clearance as per Annexure-I, two days prior before starting the filter cleaning activity.
The equipments like Air handling unit, Laminar air flow, Compressor and dynamic pass box contains the filters like Pre-filter, fine filter and cartridge filter are need to be clean as per the filter cleaning schedule.
Filter cleaning shall be done as per the filter cleaning schedule as per Annexure-II.
Do not deviate filter cleaning plan for more than 5 working days, in case of equipment non availability due to use in production or in operation, get authorization from engineering head, user department head and QA head for deviating more than 5 working days and fill deviation as per deviation SOP.
List out the filters to be cleaned as per the Filter cleaning schedule.
Take the vacuum pump to clean the AHU filter plenum.
Take required poly bags to carry the opened dust filters and cleaned filters.
Click the link to download word file copy of this document:
https://pharmaguidehub.com/product/ahu-filter-cleaning-inspection-replacement-and-discard/
Filter Cleaning procedure:
Before taking out the filter for cleaning perform the below mentioned steps:
Take the vacuum cleaner.
Open the filter access door.
Switch on the vacuum pump.
Clean the filter housing and surrounding area (chamber) and the filter with the vacuum pump nozzle (through suction).
Lay down the poly bag in the filter chamber.
Remove the fasteners of the filters.
Clean the filter and its housing and surrounding area with vacuum pump again.
Switch off the vacuum cleaner.
Wrap the filter in the poly bag and close the poly bag with cable tie.
Transfer the poly bag to filter cleaning room.
Open the filter chamber hood and transfer the poly bag into the chamber.
Break the cable tie and remove the filter from the poly bag.
Close the filter chamber hood.
Check the availability of raw water & air at filter cleaning area.
Tap the filter gently by hand on tray with upstream (dirty) side facing down to filter hood (suction side) to dislodge all loose particles.
Clean the filters with compressed air at about air pressure of 1 to 1.5 Kg/cm² jet directing at an angle towards downstream.
Clean the filter with water and dry the filter in filter hood with compressed air.
Check the filter media for filter integrity visually, if any abnormality found in the filter replace with new filter as per the filter replacement intimation slip as mentioned in Annexure-VIII.
After completion of the filter cleaning put the filter in a clean poly bag and carries out the same to its respective working location.
Before fixing the filter check the gasket condition of the filter, if required adjust it or replace with new gasket.
Before fixing the cleaned filter, clean the equipment area from where the filter taken for cleaning.
After cleaning the filter area with the help of lint free cloth, fix the cleaned filter to its respective working location and tighten the fasteners.
Close the filter access door and tighten the door fasteners.
Switch on the equipment and check the leakages through the filter access doors, if any leakage found arrest them by adjusting the door gasket.
After successfully completion of the filter cleaning activity remove the gown, nose mask, goggles and gloves at filter cleaning room and wrap them in a clean poly bag and close the poly bag with cable tie.
Transfer the poly bag to the scarp area.
After successfully completion of the filter cleaning activity close the intimation slip and take signature by the user department for satisfactory working.
Update the filter cleaning record for equipment filters as per Annexure-IV.
If any type of filter introduced into the existing facility rather than calendar year than engineering officer/executive prepare Additional Filter cleaning schedule as per Annexure-V.
Update the filter cleaning status label after the filter cleaning as per Annexure-VI.
Pre-filters and fine filter shall be cleaned in fifteen days (15 ± 03 days).
Filter Inspection and Replacement Procedure:
The equipments like Reverse laminar air flow, Laminar air flow, Dynamic pass box contains the filters like Pre-filter, fine filter, cartridge filter are need to be replaced even after cleaning the filter if the pressure differential crosses the actual limits.
Pre-filters and fine filter shall be replaced in the event of any damage to filter media or flanges and when found choked physically.
Pre filters & Fine filters shall visually inspect during regular cleaning intervals as per filter cleaning procedure refer to above step.
Check the filter physically if found any discrepancy filter shall be replaced with new one.
Identify the filter which is to be replaced and note down the type of filter, filter id number and size of the filter.
Check the availability of filter in the Engineering store.
If available take required filters and keep them in poly bags and tie the poly bag.
Take required quantity of poly bags to handle the new filters.
After taking clearance from the respective department, take the respective new filter in the specified area where new filter to be installed.
Switch off the mains of the equipment and open the filter access door.
Open the fasteners of the filter and take out the filter and keep in a poly bag.
Clean the filter area with vacuum cleaner.
Open the poly bag of new filter and affix the filter in the specified location using the fasteners.
Before installing new filter visually check the filter for integrity.
Assign new number to the new filter and record the same as per Annexure-VII.
Close the filter access door.
Update the filter master list as per SOP.
Inform to the user department after completion of the work and close the intimation slip as per Annexure-VIII.
Discard the damaged filter as per filter discarding procedure.
Filter discarding procedure:
Engineering officer/executive will take initiation for replacement of the damaged filter.
After taking out the filter from its position following procedure shall be followed for all areas:
Take the removed damaged filter in a polythene bag to the filter cleaning area.
Clean the filter as per routine filter cleaning procedure if the filter is pre-filter, fine filter and fresh air filter.
If it is a HEPA filter just shake the filter in the polythene bag only.
For pre-filter and fine filter after cleaning make the filter frame and media in to pieces and scrap the filter frame and media.
For HEPA filter, make the filter frame in to pieces.
Keep the media and filter frame in the separate polythene bag take it to scrap yard.
Take 12 liters of purified water in HDPE container and add 2.5 kg of concentrated NaOH pellets/flakes to prepare sodium hydroxide (caustic soda) solution.
Soak the filter media in the prepared NaOH solution to dissolve completely in the solution.
Put the solution in the scrap yard and make it deactivate as per the normal process.
Soak the filter frame in the NaOH solution.
Update the filter discarding record as per Annexure-IX.
Click the link to download word file copy of this document:
https://pharmaguidehub.com/product/ahu-filter-cleaning-inspection-replacement-and-discard/
REFERENCES:
Not Applicable
ANNEXURES:
ANNEXURE No. | TITLE OF ANNEXURE |
Annexure-I | Filter Cleaning Intimation Slip |
Annexure-II | Filter Cleaning Schedule For AHU Pre Filter and Fine Filter |
Annexure-III | Pressure Differential Log Sheet |
Annexure-IV | AHU Filter Cleaning Record (All Types of Filters) |
Annexure-V | Additional Filter Cleaning Schedule For AHU Pre Filter and Fine Filter |
Annexure-VI | Filter Cleaning Status Label |
Annexure-VII | Filter Replacement Record |
Annexure- VIII | Filter Replacement Intimation Slip |
Annexure- IX | Filter Discarding record |
ENCLOSURES: SOP Training Record
DISTRIBUTION:
Master Copy Quality Assurance Department
Controlled Copy No. 01 Quality Assurance Head
Controlled Copy No. 02 Engineering Head
ABBREVIATIONS:
SOP | : | Standard Operating Procedure |
QA | : | Quality Assurance |
Kg/cm² | : | Kilogram per centimeter square |
AHU | : | Air Handling Unit |
HDPE | : | High density polyethylene |
HEPA | : | High efficiency particulate air |
NaOH : Sodium hydroxide
REVISION HISTORY:
CHANGE HISTORY LOG
Revision No. | Details of Changes | Reason for Change | Effective Date |
00 | New SOP | Not Applicable | To Be Written Manual |
ANNEXURE-I
FILTER CLEANING INTIMATION SLIP
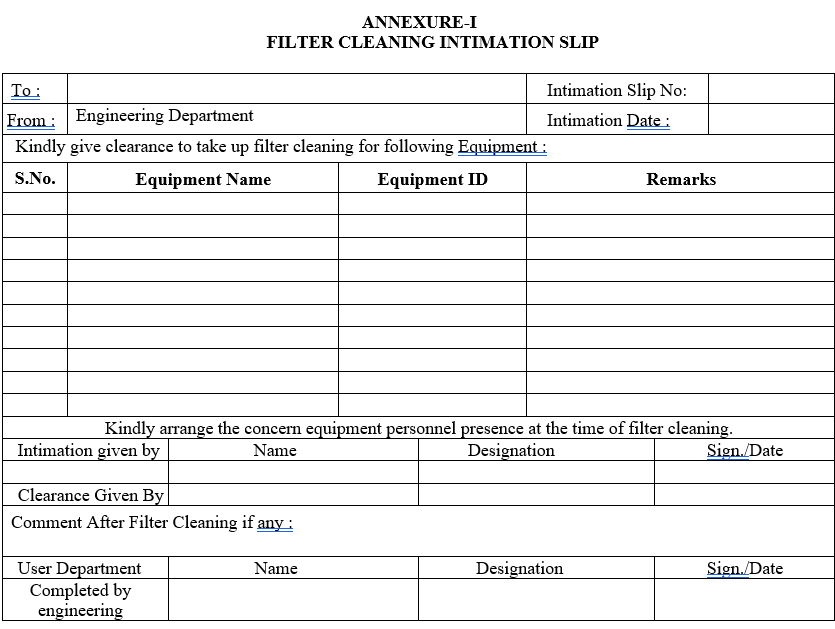
ANNEXURE-II
FILTER CLEANING SCHEDULE FOR AHU PRE FILTER AND FINE FILTER
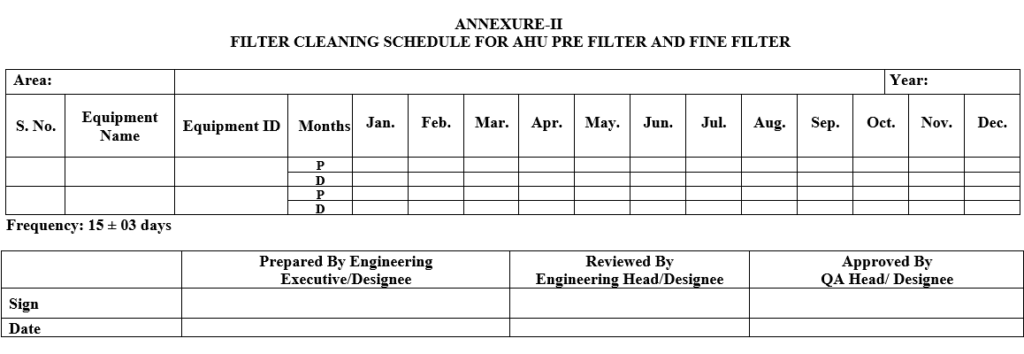
ANNEXURE-III
PRESSURE DIFFERENTIAL LOG SHEET
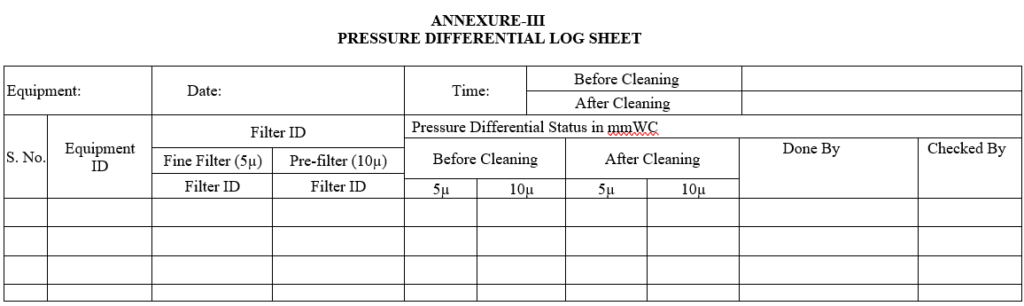
ANNEXURE-IV
CLEANING RECORD (ALL TYPES OF FILTERS)
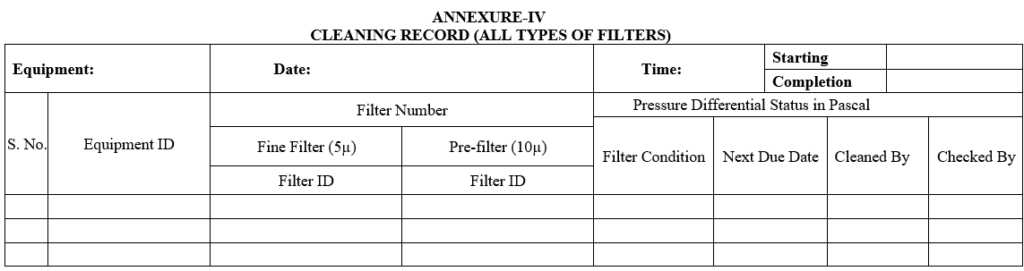
ANNEXURE-V
ADDITIONAL FILTER CLEANING SCHEDULE FOR AHU PRE FILTER AND FINE FILTER
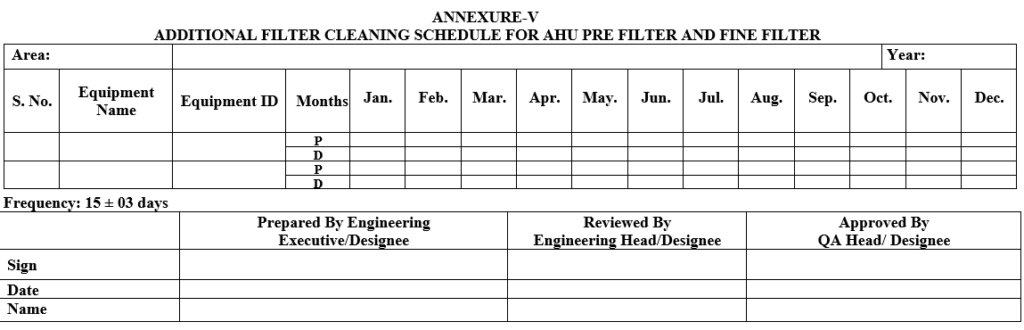
ANNEXURE-VI
FILTER CLEANING STATUS LABEL
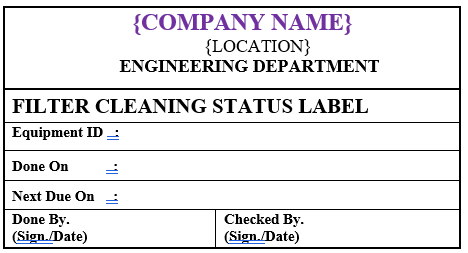
ANNEXURE-VII
FILTER REPLACEMENT RECORD
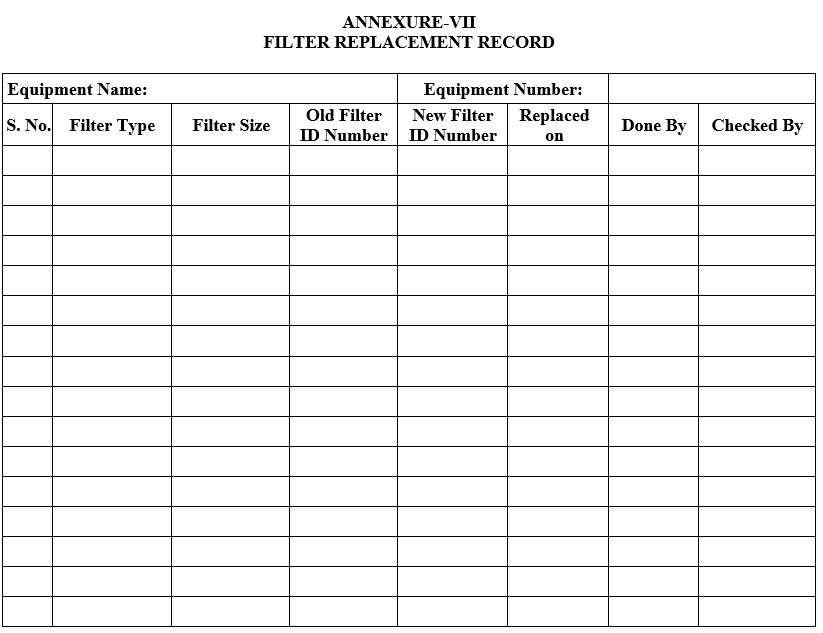
ANNEXURE-VIII
FILTER REPLACEMENT INTIMATION SLIP
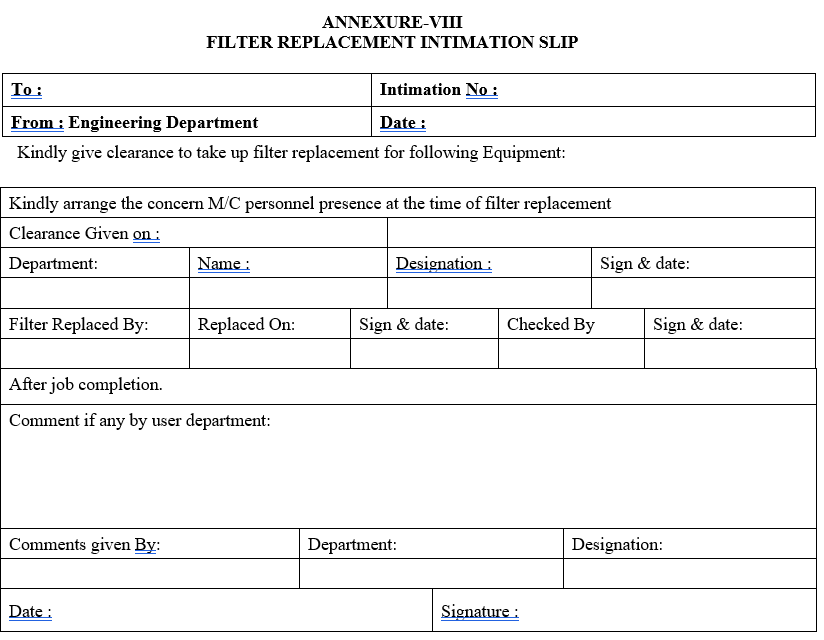
ANNEXURE-IX
FILTER DISCARD RECORD
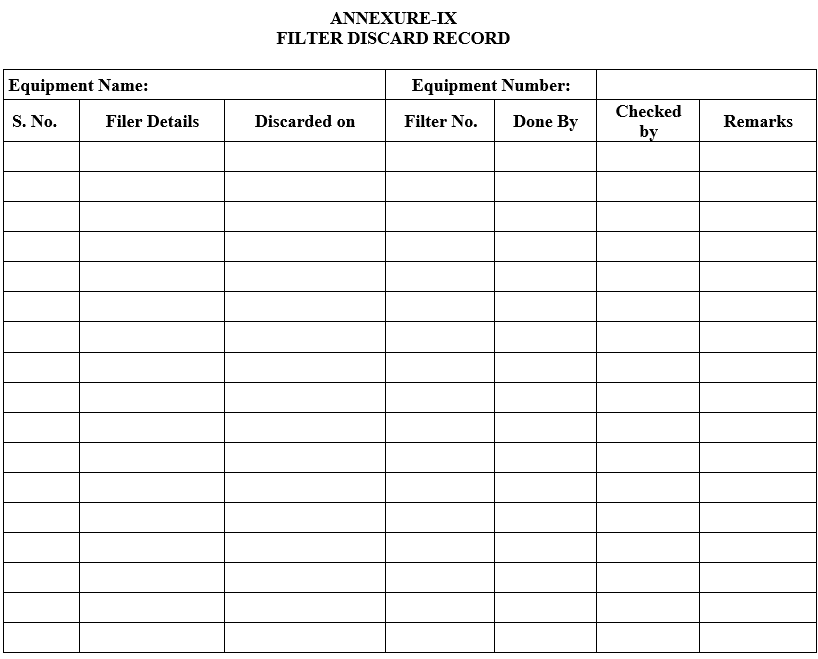
Click the link to download word file copy of this document:
https://pharmaguidehub.com/product/ahu-filter-cleaning-inspection-replacement-and-discard/