- The BQS blister packing machine is a high-speed and versatile machine manufactured by ACG Worldwide . It is a popular choice for pharmaceutical companies that need to package tablets, capsules, and other solid dosage forms.
- PROCEDURE:
- Type “A” Cleaning procedure:
- After completion of batch update the status label as “TO BE CLEANED”.
- Put the main power supply “OFF”.
- Turn the compressed air valve and chilled water outlet valve to “OFF” position.
- Disconnect the electrical supply to from main electrical supply.
- Remove the base foil and lidding foil material from the machine.
- Remove the rubber / metal stereos from the machine of previous batch.
- Keep the stereos in a fresh polythene bag and label it as (TO BE DESTROYED), in case of metallic stereos (embossing letter) keep in a polythene bag and hand over to the packing in charge.
- Clean the spilled material like PVC/PVDC foil from the floor.
- Remove the scraps and send it to the scrap yard.
- Clean the hopper and vibrator with a dry lint free cloth.
- Clean the machine with dry lint free cloth.
- Check for the absence of previous batch spilled material like PVC/PVDC on the floor inside hopper, vibrator, on floor etc.Clean the floor with a vacuum cleaner.
- Update the status label as “CLEANED“.
- Take line clearance from IPQA.
- Record the cleaning operation in equipment log sheet as per SOP.
- Frequency: After every batch change over (Of same product).
- Type “C” Cleaning procedure:
- After completion of the batch update the status label as “TO BE CLEANED”.
- Put the main power supply OFF.
- Isolate the electrical connection.
- Turn the compressed air valve and chilled water outlet valve to “OFF” position.
- Remove the rubber /metal stereos from the printing unit and labelled as “TO BE DESTROYED” (For metallic stereos remove it and return back to packing in charge.)Inspect the area for the absence of previous packing material.
- Remove the base foil and lidding foil from the machine.
- Remove the residue product from the machine immediately.
- Remove hopper, bowl from the machine, and also change parts.
- Transfer the dismantled change parts vibratory bowl, hopper, feeding channel/box, guide track and dust collector pipe covered with polythene cover status as “TO BE CLEANED” label to the washing area through the SS trolley.
- NOTE: If the feeding channel is fitted with Electrical motor then clean the change part by vacuum cleaner followed by wiping with dry lint free cloth dipped in 70% IPA.
- Scrub the vibratory bowl and hopper with sponge using potable water 10 L.
- Rinse these above parts with purified water 10 L.
- Scrub the feeding channel and the brushes of feeding box with sponge using potable water 10 L.
- Rinse these above parts with purified water 10 L.
- Wipe out adhered material from the outer surface of dust collector pipe.
- Flush the pipe with 5 L potable water until the adhered materials are removed completely then rinse with 5 L purified water.
- Then drain the whole water by hanging the dust collector pipe and then rinse with 70% IPA.
- Finally inspect properly for the absence of product residue. If required, take an additional 10L of purified water to get cleared.
- Then wipe the cleaned change parts with clean dry lint free cloth dipped in 70% IPA.
- Wipe the guide track with lint free cloth dipped in 70% IPA.
- Clean the sealing plate with soft metal wire brought to remove any lumps of moulted polythene. Inspect the plate for no damage on the knurling surface.
- NOTE:
- Before cleaning of hot plates allow them for cooling completely.
- While handling the sealing plater special care should be taken to avoid damage on knurling surface.
- Clean the blister forming plate by using lint free cloth with 70% IPA and check the cavities for proper cleaning. Remove the “TO BE CLEANED “label and affix the “CLEANED” label to the machine and transfer all the parts to the designated area covered with polythene cover.
- Record the cleaning in the equipment log sheet.
- Frequency of cleaning:
- Product to product change over.
- If continuous production of same production is running more than 6 days.
- After rectification of major breakdown.
- REFERENCES:
- Not Applicable
- ANNEXURES:
Annexure No | Title of annexure |
Annexure-I | Type C cleaning Work Sheet |
- ENCLOSURES: SOP Training Record.
- DISTRIBUTION:
- Controlled Copy No. 01 : Head Quality Assurance
- Controlled Copy No. 02 : Head Production
- Master Copy : Quality Assurance Department
- ABBREVIATIONS:
No. | : | Number |
SOP | : | Standard Operating Procedure |
PVC | : | Polyvinyl Chloride |
IPA | : | Iso Propyl Alcohol. |
IPQA | : | In Process Quality Assurance |
PVDC | : | Polyvinyl Di-chloride |
- REVISION HISTORY:
- CHANGE HISTORY LOG
Revision No. | Details of Changes | Reason for Change | Effective Date |
00 | New SOP | Not Applicable | To be written manual |
ANNEXURE-I
TYPE C CLEANING WORK SHEET
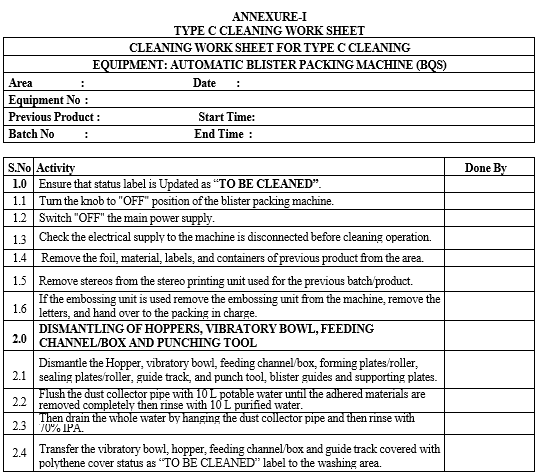
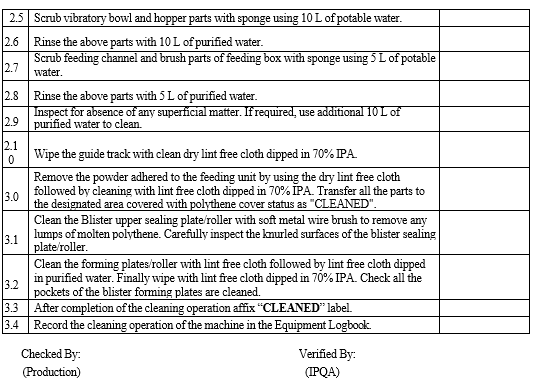