- OBJECTIVE:
To lay down a procedure for Cleaning the service area fresh air filters.
- SCOPE:
This SOP is applicable for Cleaning the service area fresh air filters at {Company Name} {Company Location}.
- RESPONSIBILITY:
- Technical Assistant – Engineering is responsible for the SOP.
- Executive – Engineering responsible to ensure the SOP.
- Head / Designee– Engineering is responsible for compliance of the SOP.
- ACCOUNTABILITY:
Engineering Head
Head Quality Assurance
- PROCEDURE:
- PRECAUTIONS
- Filters shall be handled carefully to avoid media damage.
- Before starting filter cleaning, necessary PPE’s shall be worn.
- FILTER DISMANTLING PROCEDURE
- Open the screws and keep in a tray.
- Check the filter condition.
- Check the filter gasket and filter media, if any damage observed in filter media replace the filter.
- CLEANING PROCEDURE
- Dismantle the filters and put the filter into Poly Bag and transfer the filters to the uncleaned filter storage area.
- Filters are identified with “UNCLEANED FILTERS” status label as per Annexure-II on the polythene covers. This status label shall be verified by Engineering Technical Assistant/Executive.
Click the link to download word file copy of this document:
https://pharmaguidehub.com/product/cleaning-procedure-for-service-area-fresh-air-filters/
- Remove the filters from the poly bag and keep the poly bags in dustbin.
- Tap the filters gently by hand on floor with upstream (dirty) side facing down to floor to dislodge all loose particles.
- Check the compressed air pressure is regulated to 1.0 to 2.0 Kg/Cm².
- Clean the filters in the filter cleaning equipment with compressed air pressure at about 1.0 to 2.0 Kg/Cm² air directing at an angle towards downstream.
- Clean the filters with potable water at about 0.5 to 1 Kg/Cm² pressure.
- Transfer the cleaned filters to the filter drying equipment.
- Filters are dried in the filter drying equipment by setting the heater temperature to 50ºC.
- Ensure the filters are completely dry, transfer the dried filters to the inspection area and inspect the physical condition of the filters if found damage, replace with a new filter.
- Inspected filters area kept in the poly bags and transferred to cleaned filters hold area.
- Re-install the filters which are kept in new poly bags to the respective area.
- Filters are identified with “CLEANED FILTERS” status label as per Annexure-III on the polythene covers. This status label shall be verified by Engineering Technical Assistant/Executive.
- Record the filter cleaning details in Filter Cleaning Record in Annexure-I.
- The filter cleaning frequency shall be 30 ± 7 days.
- Filter cleaning Area Cleaning Procedure
- After completion of Filter cleaning activity, the area shall be cleaned with water.
- Floor mopping shall be done.
- All filters shall be identified with a unique numbering system.
AA/BBB/001
AA: Indicate Area Name
BB: Indicate rating of the filter
001: Serial No. start from 001, 002,003…….
- REFERENCES:
Not Applicable
- ANNEXURES:
ANNEXURE No. | TITLE OF ANNEXURE |
Annexure-I | Service area fresh air filters Cleaning Record |
Annexure-II | Status Label for Uncleaned Filters |
Annexure-III | Status Label for Cleaned Filters |
ENCLOSURES: SOP Training Record.
- DISTRIBUTION:
- Controlled Copy No. 01 Head Quality Assurance
- Controlled Copy No. 02 Head-Engineering
- Master Copy Quality Assurance Department
- ABBREVIATIONS:
SOP : Standard Operating Procedure.
Kg/Cm² : Kilograms per square centimeters.
- REVISION HISTORY:
CHANGE HISTORY LOG
Revision No. | Details of Changes | Reason for Change | Effective Date |
00 | New SOP | Not Applicable | To be written manual |
ANNEXURE-I
SERVICE AREA FRESH AIR FILTERS CLEANING RECORD
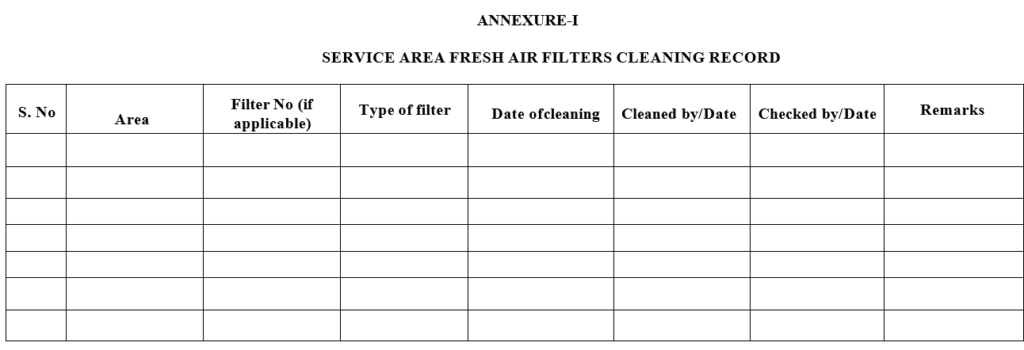
ANNEXURE-II
STATUS LABEL FOR UNCLEANED FILTERS
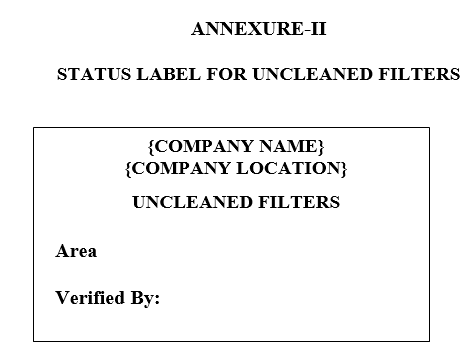
ANNEXURE-III
STATUS LABEL FOR CLEANED FILTERS
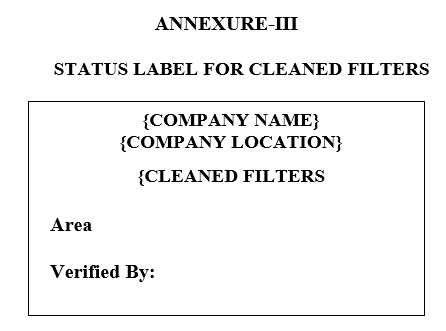
Click the link to download word file copy of this document:
https://pharmaguidehub.com/product/cleaning-procedure-for-service-area-fresh-air-filters/