- OBJECTIVE:
To lay down a procedure for destruction/disposal of rejected, non-moving and obsolete materials.
- SCOPE:
This SOP is applicable for destruction/disposal of rejected, non-moving and obsolete materials at {Company Name} {Company Location}.
- RESPONSIBILITY:
- All department personnel – Follow the instruction as per procedure.
- QA Executive/ Designee – Review and technical correction of SOP.
- ACCOUNTABILITY:
QA Head shall be accountable for compliance of this SOP.
- PROCEDURE:
- Rejected, non-moving and obsolete materials for destruction/disposal shall be stored separately in a dedicated area with proper labeling showing the status of the materials.
- As per the requirement, destruction initiator shall fill the destruction request as per relevant SOP for issuance of destruction report as per Annexure-II.
- QA executive/officer shall make the photo copy of destruction report and put the sign along with date in “Issued by” box and issue to destruction initiator.
- QA officer/executive shall log the details in “Log book for destruction record” (As per Annexure-I) with the required details such as product/ item and manufacturer name and give destruction report number to the respective destruction report.
- The destruction report number shall be assigned as: XXX/YY-ABC
Where:
XXX | : | Indicates to Company Name | |
/ | : | Indicates to Separator | |
YY | : | Indicates to year e.g. 22, 23 | |
– | : | Indicates to Hyphen | |
ABC | : | Indicates to three-digit serial numbers e.g. 001, 002, 003, 004 |
For e.g the first destruction Report No. in year 2023 shall be given as XXX/23-001
- If manufacturing of any product is discontinued at site and printed packing material is available at site in approved stock, HO Purchase shall communicate through e-mail at site for the destruction of material with proper reason. The warehouse shall prepare a list of materials to be destroyed and initiate for the destruction.
- The destruction initiator shall fill in the required details in the destruction report and forward to the department head for signature.
- After signature by the departmental head, the destruction report shall be forward to the planning head, marketing head/purchase head or other (if required) to take their comment (if any).
- Finally, the destruction report shall be reviewed and signed by QA officer/ executive and forward to QA head for approval.
- After approval from QA head, destruction process is carried out by concerned department in presence of QA Officer/Executive, but in case of discontinuation of product at site in which material is lying in approved stock, QA shall verified the material stock prior to destruction activity.
- Consult concerned EHS Head/ officer for safety issue, if any and for disposal pathway, wherever applicable.
- Concerned department shall give a copy of this approved destruction report to Warehouse in-charge to return the excise duty, if any.
- Printed packing material sample shall be attached with destruction report for reference.
Click the link for download word file copy of this document: https://pharmaguidehub.com/product/destruction-disposal-of-rejected-non-moving-and-obsolete-materials/
Method of Destruction:
- Destruction of Raw materials:
- For the destruction of raw materials, the materials areput into the container having RO water or by appropriate method depending on nature of material. Close the container and keep it for overnight, till it become slurry and then transfer the container’s material to Effluent Storage Tank.
- Destruction of Packing Material:
- For printed packaging material and obsolete materials: – Labels, Cartons, Foils obsolete materials and literatures shall be shredded in shredding machine or manually and send to scrap area in presence of QA executive/Designee.
- Destruction of General Pharmaceutical Products:
- For the destruction of general pharmaceutical tablets firstly the tablets are crushed then put into the container having RO water. Close the container and keep it for overnight, till it become slurry and then transfer the container’s material to Effluent Storage Tank. Finished products packing material destroyed as per point no. 5.14.2.
- Destruction of Potent and Narcotic Drugs:
- Collected all rejected tablet, capsule powder in a container bucket measures the weight and dissolve it in 10 Times volume water. Then add 10 % sulphuric acid solution slowly with continuous stirring of the solution and ensure the same is dissolved completely. For disposal of 10 liter of diluted solution add 1000 ml of 10 % sulphuric acid.
- Measure the pH Value of the solution by using litmus paper adjust the pH between 6.0 to 7.0 by using 1 M Sodium Hydroxide (4.2 gm NaOH flakes dissolve in 1 liter water) solution.
- Dispose of the above material by adding it into the input water tank of the Effluent treatment Plant (ETP) for further treatment action as per the SOP of ETP.
- The details of destruction shall be filled in Annexure -II.
- REFERENCES:
Not Applicable.
- ANNEXURES:
ANNEXURE No. | TITLE OF ANNEXURE |
Annexure-I | Log book for destruction record |
Annexure-II | Destruction report |
- DISTRIBUTION:
Controlled Copy No. 01 | : | Head Quality Assurance |
Controlled Copy No. 02 | : | Head Quality Control |
Controlled Copy No. 03 | : | Head Production |
Controlled Copy No. 04 | : | Head Engineering |
Controlled Copy No. 05 | : | Head Warehouse |
Master Copy | : | Quality Assurance Department |
- ABBREVIATIONS:
QA | : | Quality assurance |
SOP | : | Standard operating procedure |
EST | : | Effluent storage tank |
EHS | : | Environment health and safety |
HO | : | Head Office |
RO | : | Reverse Osmosis |
- REVISION HISTORY:
CHANGE HISTORY LOG
Revision No. | Details of Changes | Reason for Change | Effective Date |
00 | New SOP | Not Applicable | To be written manual. |
Click the link for download word file copy of this document: https://pharmaguidehub.com/product/destruction-disposal-of-rejected-non-moving-and-obsolete-materials/
ANNEXURE-I
LOG BOOK FOR DESTRUCTION RECORD
S. No. | Issued date | Issued by Name | Issued to Depart. | Name of Item | Manufac turer | Destruction report no. | Quantity received | Quantity rejected | Total value (Rs.) | Quantity destroyed | Destroyed by Name | Rem arks |
ANNEXURE-II
DESTRUCTION REPORT
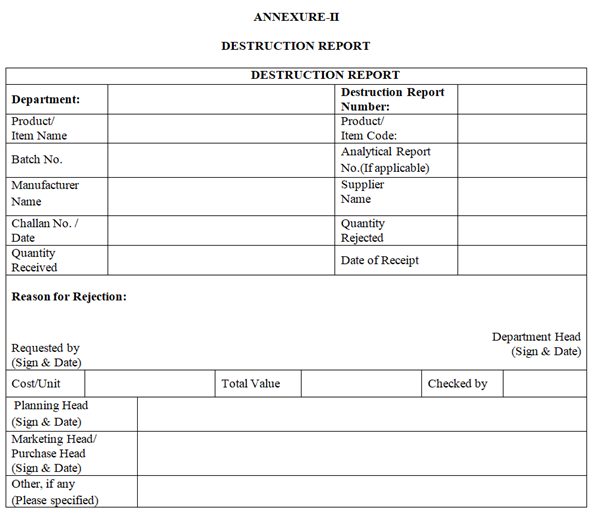
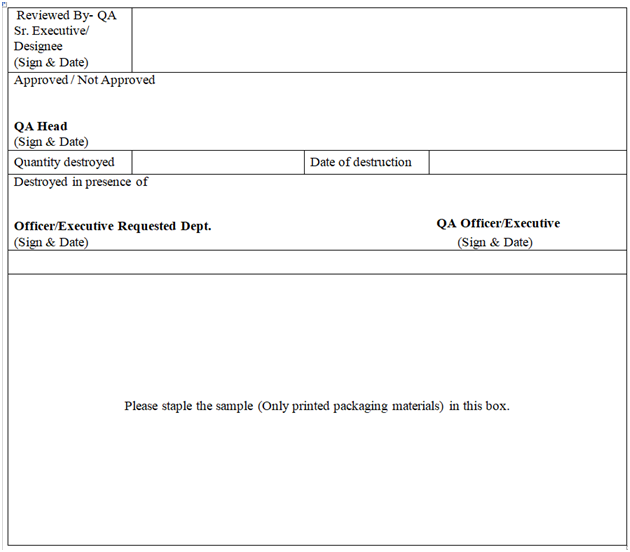
Click the link for download word file copy of this document: https://pharmaguidehub.com/product/destruction-disposal-of-rejected-non-moving-and-obsolete-materials/
Frequently Asked Question ?
1. Who is responsible for the destruction and disposal of these materials?
- Responsible personnel vary depending on the company’s SOPs, but typically involve a team from Quality Assurance, Stores, Production, and Environmental Health & Safety.
2. What documentation is required for the process?
- A detailed Standard Operating Procedure (SOP) outlining the procedures for segregation, labeling, documentation, and destruction methods is crucial. Additionally, records of destruction, disposal certificates, and waste manifests must be maintained.
3. How are different types of materials categorized for destruction?
- Categorization often follows regulatory guidelines based on potential hazards. Typical categories include expired and short-expiry products, contaminated materials, rejected materials, non-moving inventory, and obsolete packaging materials.
4. What are the acceptable methods for destruction?
- Accepted methods depend on the material type and local regulations. Examples include incineration, chemical treatment, shredding, and secure landfilling. Each method should effectively render the material unusable and pose no environmental risk.
5. Are there any special considerations for controlled substances?
- Yes, strict regulations govern the destruction of controlled substances. Witnessing by authorized personnel, specific destruction methods like incineration with witness and temperature logs, and documentation of the entire process are mandatory.
6. How can environmental impact be minimized during disposal?
- Choosing energy-efficient destruction methods, using environmentally friendly solvents for chemical treatment, and recycling appropriate packaging materials are all crucial for minimizing environmental impact.
7. How often should outdated inventory be reviewed and disposed of?
- Regular inventory reviews are essential, typically quarterly or semi-annually. The frequency may vary depending on the product’s shelf life and production turnover.
8. What happens to non-pharmaceutical waste generated during the process?
- Proper disposal of non-pharmaceutical waste like gloves, packaging materials, and cleaning supplies needs to comply with general waste management regulations. Segregation and disposal based on waste type (hazardous, non-hazardous) is crucial.
9. How are training and awareness programs implemented for personnel involved?
- Regular training on SOPs, relevant regulations, and safe handling procedures ensures proper execution and compliance. Raising awareness about the importance of responsible disposal among all personnel is also essential.
10. What are the potential consequences of improper disposal?
- Improper disposal can lead to environmental contamination, product counterfeiting, regulatory non-compliance, and reputational damage. It’s crucial to prioritize safe and responsible disposal processes.
Click the link for download word file copy of this document: https://pharmaguidehub.com/product/destruction-disposal-of-rejected-non-moving-and-obsolete-materials/