Definition of Airlock:
Commonly used in the pharmaceutical industry to maintain cleanliness and
prevent contamination of the manufacturing environment.
Airlocks are called PAL (Personnel Air Lock) when used for personal and MAL
(Material Air Lock) when used for transferring the material and can also use
for transfer the waste and called (waste airlock).
Airlock is a small, enclosed space that is used to transition between clean and
non-clean areas.
It typically consists of two or more doors that can be opened and closed to
allow personnel or material to pass through while maintaining a separation
between the two areas
Airlocks are an architectural device that helps implement heating, ventilation,
and air conditioning (HVAC) control of air classification or quality.
Contamination is a major factor in pharmaceutical industries. Control of
contamination is a major issue for regulatory authorities, cGMP guidances are
continuously revised to control the contamination is necessitating the use of
Cleanroom Airlocks.
Airlock is a transitional area that typically has two doors in series to separate
a controlled environment (such as a clean room, lab, operating room, or
isolation room) from a corridor or vice versa.
The two doors should be interlocked to avoid being opened at the same time.
Airlocks are called PAL (Personnel Air Lock) when used for personal and MAL
(Material Air Lock) when used for transferring the material and can also use
for transfer the waste and called (waste airlock).
Aim of Airlock:
Airlock in a pharmaceutical facility is to prevent contaminants from entering
the clean areas, where drugs are manufactured and packaged.
This is important because even small amounts of contamination can have
serious consequences, including the production of low-quality or unsafe
products.
Helps to prevent the spread of contaminants from one area to another within
the manufacturing facility.
Allow a transfer between cleanliness levels, for example, from Grade C to B.
This transfer is achieved by maintaining room pressurization (by the direction
of air flow through doors) and isolating the levels from each other Airlock
helps to protect classified area that may occur during the men and material
movement.
Operation of Airlock:
Airlocks are often equipped with features such as air showers, which use
high-pressure jets of air to remove dust and other particles from clothing and equipment before entering the clean area.
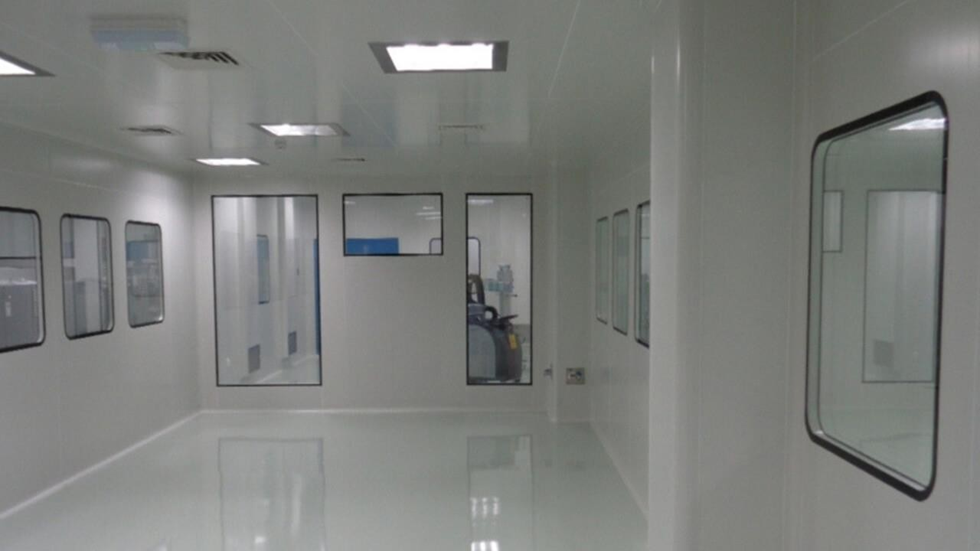
They may also include HEPA (high-efficiency particulate air) filters, which remove particles from the air to maintain a sterile environment.
Pharmaceutical facilities may also use other types of barriers and controls, such as gowning rooms and negative pressure rooms, to maintain the cleanliness and safety of their manufacturing environments.
Types of airlocks system
Cascade airlock:
Bubble airlock
Sink airlock
Potent compound airlock
Cascade Airlocks
Definition :
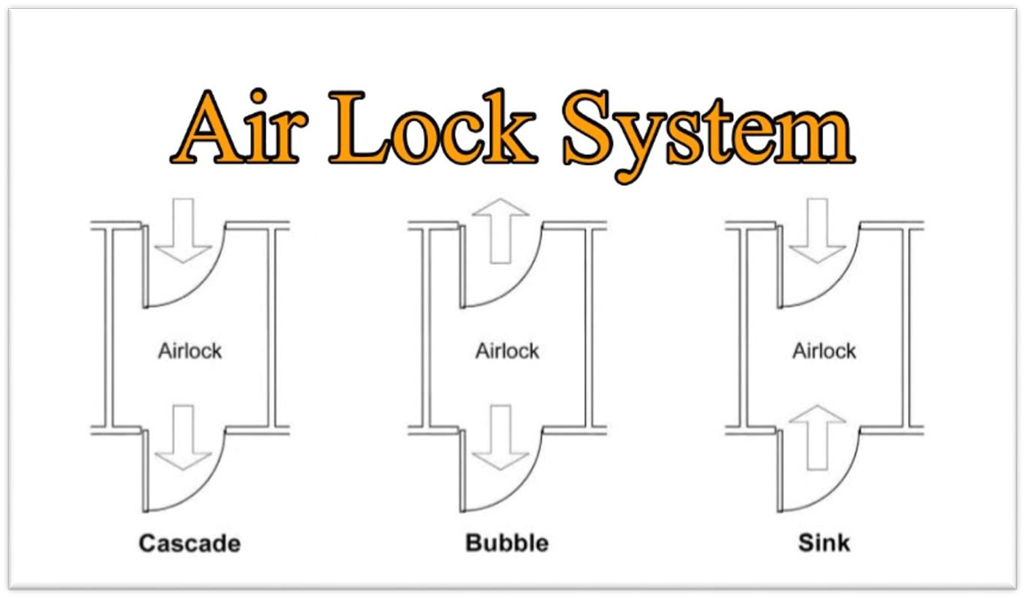
These airlocks are very common having higher pressure on one side and lower pressure on another side.
In this type, positive air pressure flows from the higher pressure internal zone to be airlock and from the airlock to the lesser lower pressure grade area.
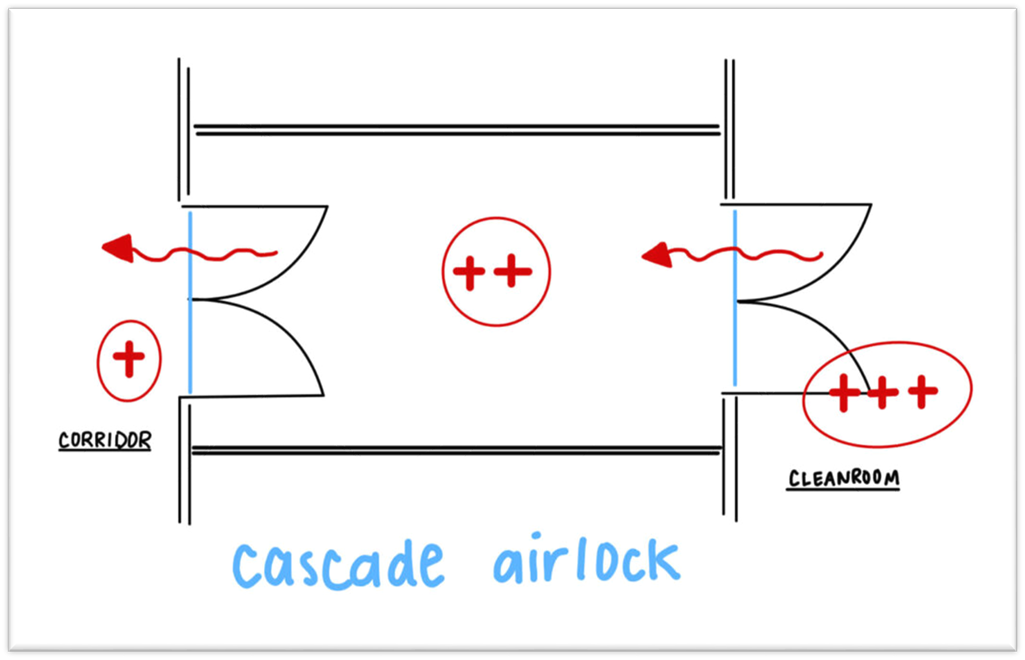
Applications :
Prevents entry dust and contamination from outside to airlock and from airlock to inner side.
Where the product requires protection from particulate but the people outside the clean-room do not need protection from the product in the clean room.
Bubble Airlocks:
Definition :
These types of airlock having higher pressure inside the airlock and lower pressure both outside.
As it runs at positive pressure to both areas it creates a barrier where contaminants within either area are pushed back into their own respective areas.
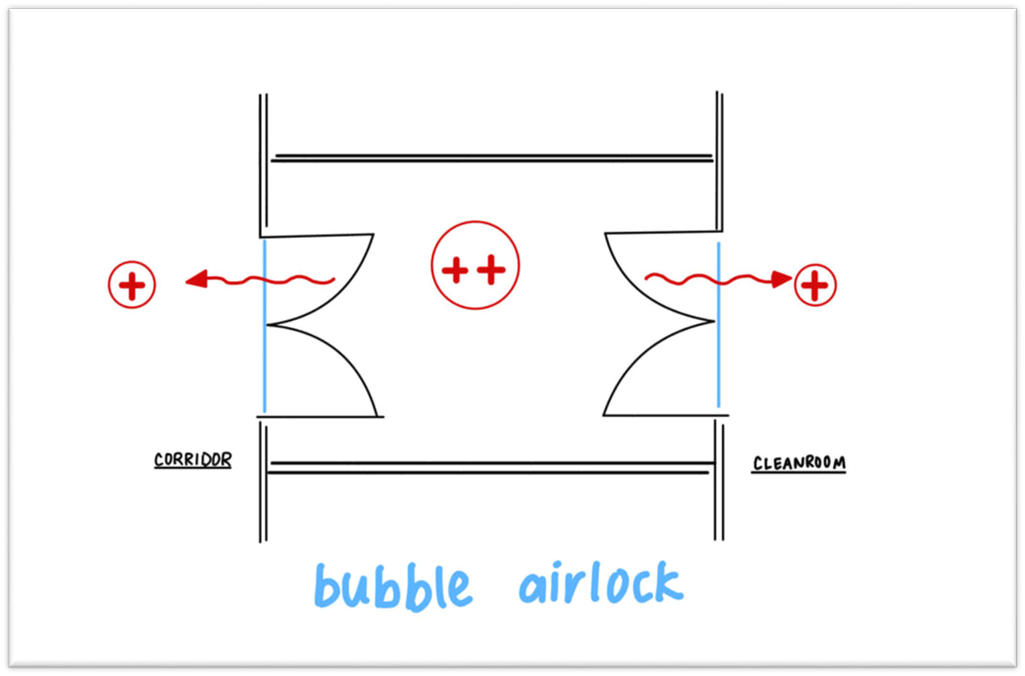
Applications:
Where the product needs protection and the people external to the clean rooms require protection from the product, to reduce the possibility of viable articulate from entering the lesser pressure clean-room. Area such as higher potency, compounding areas terminal sterilization is not an option.
Sink Airlocks:
Definition :
Airlocks having lower pressure inside the airlock and higher pressure on both sides of the airlock.
This airlock pulls air from both adjacent areas creating a low-pressure barrier and reduces the opportunity of contamination passing to the internal zone.
Applications :
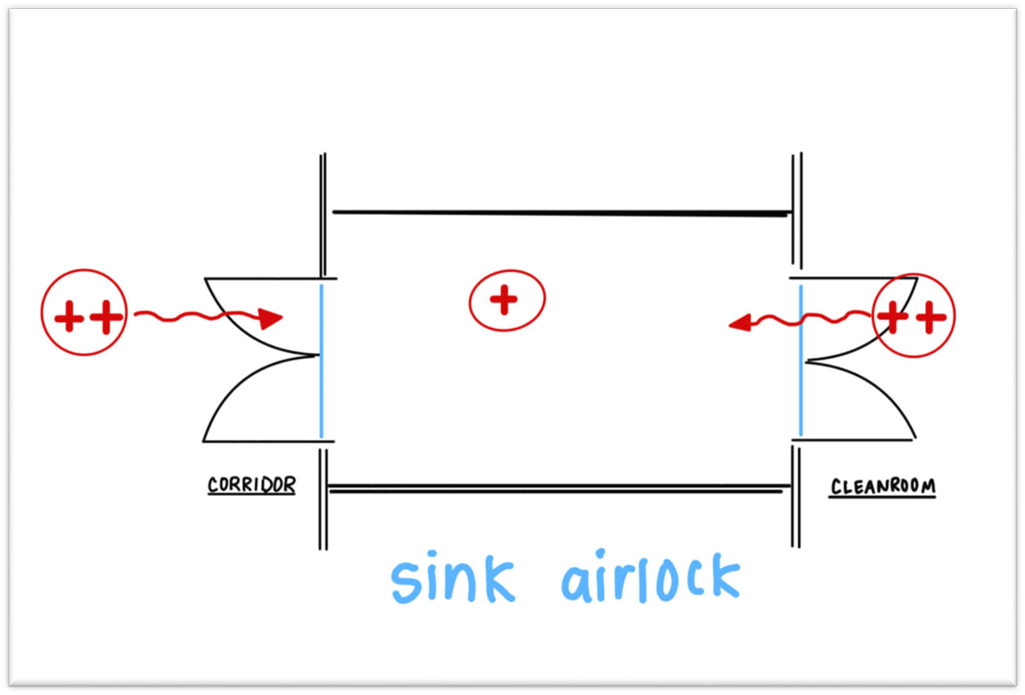
Where substances that are experimented on are highly dangerous, and it is essential to keep them from being exposed.
During a few types of production processes in a clean-room, air from a contaminated area has to be contained in one place.
Potent Compound Airlocks:
Definition and Applications :
Combination of the pressure bubble and pressure sink airlocks.
This two-compartment airlock arrangement allows personnel to protect (gown/respirator) themselves before coming into contact with any dangerous materials while at the same time.
The product (potent compound) is protected from contamination from adjacent, connected areas.
All conditioned, clean air supplied to the gown room is dissipated into the adjacent rooms while all the conditioned, clean air supplied to the airlock room (as well as all infiltration air into that room) is exhausted.

Important Notes:
The air lock door should be open to higher differential pressure side which helps to close the door.
An interlocking system should be there to prevent both doors from opening once at a time.
An alarm system should be there to indicate one door is open at once.
A Higher ACPH rate should be maintained in the airlock.
It should be a minimum of ACPH of it relevant classification.
It helps to remove the contamination entered from the outside easily.
The air lock should be kept empty, and materials such that garments, shoe covers, etc. should not be kept in the air lock.