- OBJECTIVE:
To lay down a procedure for dispatching the finished product batch up to the central Warehouse/ delivery warehouse under quarantine status.
- SCOPE:
This SOP is applicable for dispatch of finished product batch under quarantine status, manufactured at {Company Name} {Company Location}.
Note: Quarantine Dispatch
In order to save transit time for the shipment of finished product batches from the manufacturing site to the warehouse in India or any other market, batch(s) of finished product may be dispatched under quarantine. Such batch(s) shall not be further distributed from the warehouse until confirmation for the final release or approval of the product is received from the QA of the manufacturing site.
- RESPONSIBILITY:
- Warehouse Head (Site): To initiate the request for dispatch of finished product under quarantine status.
- Plant Head: To authorize the request for dispatch of finished products under quarantine status.
- QA Department: To evaluate the request for dispatch of finished products under quarantine status.
- QA Head: To approve the request for dispatch of finished products under quarantine status.
- Warehouse (Delivery): To ensure that the finished product dispatched under quarantine shall not be distributed before the final release of finished products and the availability of the certificate of analysis.
- ACCOUNTABILITY:
The QA Head shall be accountable for compliance with this SOP.
- PROCEDURE:
- Based on the advice from the Marketing or Planning Department, the site warehouse head shall initiate the request (as per Annexure I) and obtain the authorization of the plant head for the dispatch of the finished product batch under quarantine status.
Click the link for download word file copy of this document: https://pharmaguidehub.com/product/dispatch-of-finished-products-under-quarantine-status/
- The following details shall be provided in the requisition:
- Finished product batch details like product name, product batch number, manufacturing date, expiry date, and A.R. number of API used in the finished product.
- Any deviation or incident associated with the finished product batch, if yes, a description of the same.
- Destination Warehouse.
- Requests for dispatch of finished products under quarantine status shall be forwarded to the QA Head for evaluation and approval. QA Head may take assistance for evaluation.
- QA shall evaluate the requisition for the following:
- Release the status of raw materials and packing materials used for the manufacturing and packing of the finished product batch in question.
- In process results.
- Critical process parameters and compliance to laid down specifications.
- Whether the batch has been manufactured & packed as per the instructions given in the batch record and relevant SOP’s.
- Any open Deviation/ incident associated with the batch that may have impact on product quality/ stability.
- QA shall ensure that the chemical test has been conducted for the requested batch of the finished product and is compliant as per the applicable specification.
- After satisfactory review and evaluation of documents, QA shall recommend for dispatch of finished product under quarantine status to QA Head.
- After approval by the QA Head, warehouse personnel shall arrange for the dispatch of such batch(s) with the COA for quarantine release.
- The analysis of the batch authorized for quarantine dispatch shall be undertaken by Quality Control, and the final results shall be forwarded to QA for their review.
- QA personnel shall review the batch record and analytical data as per the SOP on batch release of the finished product.
- After satisfactory review, QA personnel arrange to send a copy of the certificate of analysis to the warehouse. This shall be considered the release or approval of the batch received under quarantine status for its further distribution from the warehouse.
- In case any OOS result is reported during QC analysis for such batch(s), the QA Head informs the respective Warehouse to hold the distribution of the batch sent under Quarantine status.
- Post-investigation, if the OOS result is confirmed, the QA Head shall communicate with the warehouse for rejection of the batch.
- Warehouse shall confirm the receipt of this information and identify the batch as “REJECTED” at Warehouse. This batch shall be taken for its destruction.
Click the link for download word file copy of this document: https://pharmaguidehub.com/product/dispatch-of-finished-products-under-quarantine-status/
- REFERENCES:
Not Applicable.
- ANNEXURES:
ANNEXURE No. | TITLE OF ANNEXURE |
Annexure-I | Request for dispatch of finished products under quarantine status. |
- DISTRIBUTION:
Controlled Copy No. 01 | : | Head Quality Assurance |
Controlled Copy No. 02 | : | Head Quality Control |
Controlled Copy No. 03 | : | Head Production |
Controlled Copy No. 04 | : | Head Warehouse |
Master Copy | : | Quality Assurance Department |
- ABBREVIATIONS:
QA | : | Quality assurance |
SOP | : | Standard operating procedure |
QC | : | Quality Control |
COA OOS | : : | Certificate of Analysis Out of specification |
- REVISION HISTORY:
CHANGE HISTORY LOG
Revision No. | Details of Changes | Reason for Change | Effective Date |
00 | New SOP | Not Applicable | To be written manual |
Click the link for download word file copy of this document: https://pharmaguidehub.com/product/dispatch-of-finished-products-under-quarantine-status/
ANNEXURE-I
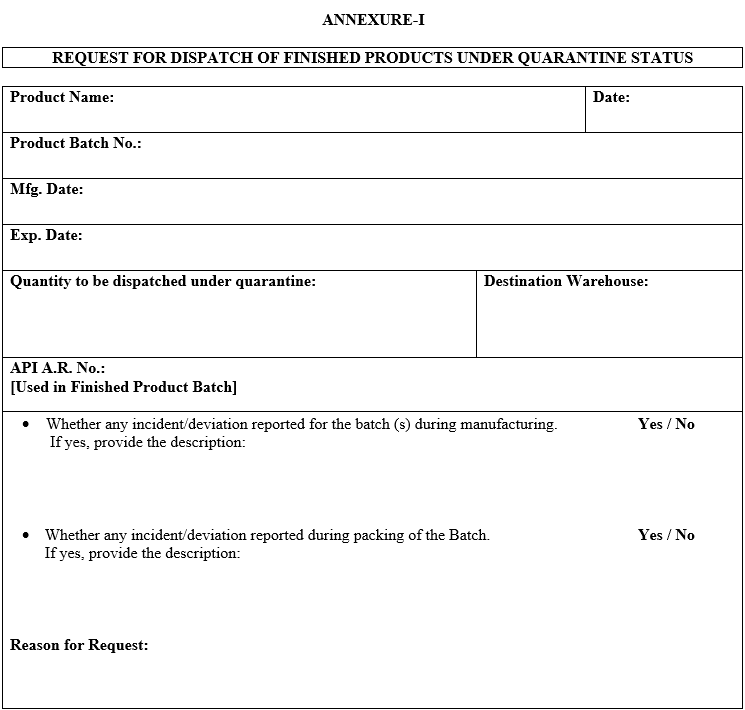
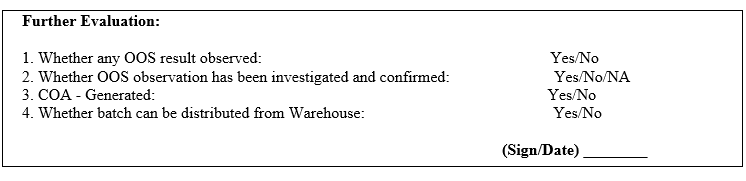
Frequently Asked Questions?
1. What is “quarantine status” for finished pharmaceutical products?
Quarantine status indicates that a finished product batch has not yet been fully released for distribution. It is typically held in a designated area for further testing, analysis, or potential recall.
2. Why are finished products placed under quarantine?
There are several reasons for quarantining finished products:
- Incomplete quality control (QC) testing: Not all QC tests may be completed by the time the product is packaged and labeled.
- Suspected stability or safety issues: If there are concerns about the product’s stability or potential safety risks, it may be quarantined for further investigation.
- Regulatory hold: Authorities may hold a batch due to concerns about its compliance with regulations or manufacturing practices.
3. Under what circumstances can quarantined finished products be dispatched?
Dispatch can only occur after the reason for quarantine has been addressed and the product meets all release criteria. This typically involves:
- Completion of all required QC testing and confirmation of satisfactory results.
- Resolution of any safety or stability concerns.
- Formal release authorization from the quality unit.
4. What specific procedures must be followed for dispatching quarantined products?
Strict procedures must be followed to ensure proper segregation, handling, and documentation. These procedures should be documented in a Standard Operating Procedure (SOP) and may include:
- Clear labeling and identification of quarantined products.
- Controlled access to the quarantine area.
- Specific handling and transportation requirements.
- Detailed records of dispatch, including batch number, quantity, and destination.
5. What are the regulatory requirements for dispatching quarantined products?
Pharmaceutical regulations vary by country, but most require compliance with Good Distribution Practices (GDP) and Good Manufacturing Practices (GMP). These regulations typically specify requirements for:
- Documentation and traceability of quarantined products.
- Proper control and handling throughout the dispatch process.
- Notification to relevant authorities, if necessary.
6. What are the potential risks associated with dispatching quarantined products?
Dispatching quarantined products without proper authorization or procedures can lead to serious consequences, including:
- Distribution of potentially unsafe or ineffective products.
- Product recalls and market disruptions.
- Regulatory sanctions and fines.
7. What roles do different departments play in the dispatch process?
Several departments may be involved in the dispatch of quarantined products, including:
- Quality Assurance (QA): Responsible for authorizing release and ensuring compliance with regulations.
- Manufacturing: Responsible for product preparation and packaging.
- Warehouse: Responsible for storage and handling of quarantined products.
- Logistics: Responsible for transportation and delivery.
8. What are the best practices for communication and coordination during the dispatch process?
Clear communication and coordination between all involved departments are crucial to ensure a smooth and compliant dispatch process. This includes:
- Regular updates and information sharing about quarantined products.
- Clearly defined roles and responsibilities for each department.
- Transparent documentation of all steps in the dispatch process.
9. How can technology be used to improve the management of quarantined products?
Technology can play a significant role in improving the management of quarantined products, such as:
- Warehouse management systems (WMS) for tracking and tracing quarantined products.
- Electronic quality assurance (eQA) systems for documenting release procedures and approvals.
- Real-time communication and collaboration tools for efficient coordination.
10. What are some additional resources for information on dispatching quarantined products?
Several resources can provide further information on the regulations and best practices for dispatching quarantined products. These include:
- **Regulatory agencies websites (e.g., FDA, EMA, PHARMA) **
- Industry associations (e.g., Pharmaceutical Manufacturers Forum)
- Consulting firms specializing in pharmaceutical compliance
Click the link for download word file copy of this document: https://pharmaguidehub.com/product/dispatch-of-finished-products-under-quarantine-status/