- OBJECTIVE:
To lay down a procedure for Control of Required Temperature, Humidity and Differential Pressure in the QC, Manufacturing and Packing Areas.
- SCOPE:
This SOP is applicable for Control of Required Temperature, Humidity and Differential Pressure in the QC, warehouse (including RM/PM/FG), manufacturing and packing areas at {Company Name} {Company Location}.
- RESPONSIBILITY:
Respective Department Officers/Executives/Designee and Quality Assurance Officers/Executives/
Designee.
Concern Department Head –Training, approval & implementation of SOP.
- ACCOUNTABILITY:
Concerned Department Heads.
- PROCEDURE:
- Precautions:
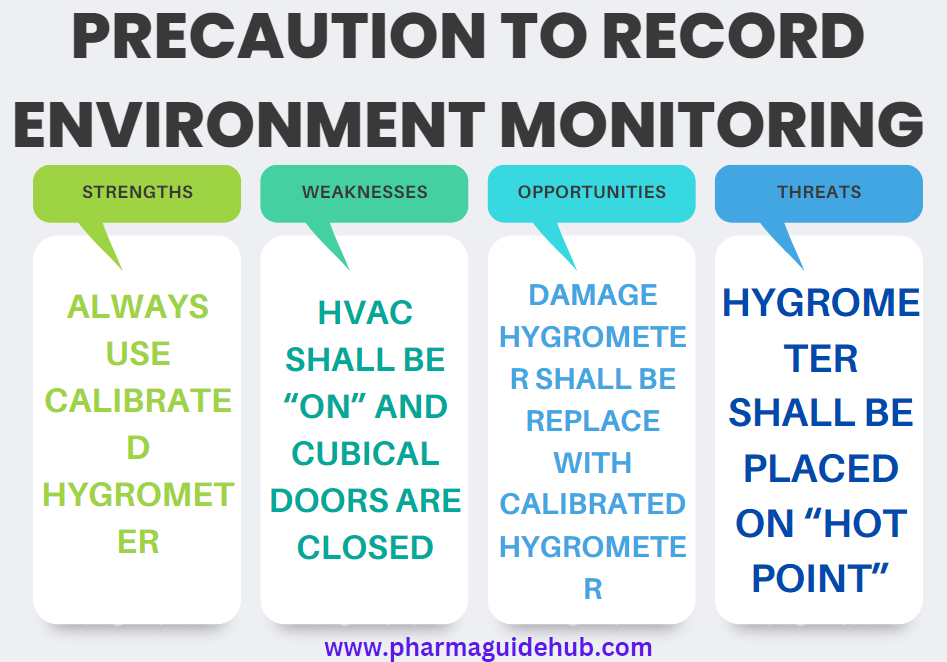
- Always use calibrated instruments for recording of Temperature, Relative Humidity and Differential Pressure.
- Before recording the Temperature, Relative Humidity and Differential Pressure ensure that HVAC Shall be “ON” and cubical doors are closed.
- In case of damage of digital hygrometer, digital hygrometer shall be replaced by QA only with calibrated digital hygrometer.
- Digital hygrometer shall be placed on “Hot Point” location as identified during Temperature mapping.
Click the link for download word file copy of this document: https://pharmaguidehub.com/product/environment-monitoring-procedure/
- Procedure for Monitoring of Temperature and Relative Humidity:
- Ensure that the digital Temperature and Relative Humidity indicator shall be clean, and no dust accumulated on the sensor.
- Don’t cover the digital hygrometer with any type of polythene or PVC.
- Record the Temperature and Relative Humidity of the concerned cubicle as displayed on the screen in Annexure-I.
- Verification of the Temperature and Relative Humidity of the area shall be done by the concerned department and random verification shall be carried out by IPQA.
- Limits:
The limit for Temperature is 10-25 ˚C and Relative Humidity is 30-65%. The Temperature and RH can be vary based on dosage form.
- Temperature gauge Id. No. shall be assigned as follows:
Where,
AAA | : | It indicated Company Name abbreviation |
“/” | : | It indicated Separator |
XX | Department Name (QA, PD, QC, WH, EG. HR) | |
HM | : | It indicate Hygrometer |
ABC | : | It indicate three digit serial number e.g. 001, 002, 003 |
Example: AAA/PD/HM/001, AAA/PD/HM/002, AAA/WH/HM/002,
- If temperature or relative humidity is out of limit, inform QA and maintenance for rectification. After rectification the same shall be monitored again, if it is within the limit, activity can be started.
- Frequency for monitoring of Temperature and Relative Humidity
- During the start of shift first record the Temperature & Relative Humidity as displayed in digital hygrometer.
- When no activity is in the area then record the Temperature & Relative Humidity twice in a shift or it can be mark as Not Applicable and mention No Activity.
- During the Activity it can be recorded at the frequency of two hrs or it can be extend based on the AHU qualification report.
- Verification of Temperature and RH in non-critical areas where no direct impact on product and batch such as FG Store, PM Store, PM receiving overprinting stages is done by concerned department supervisor.
- Cleaning of Digital Temperature & Relative Humidity Indicator:
- Ensure that Digital Temperature & Relative Humidity Indicator is cleaned by mopping with lint free cloth during cleaning.
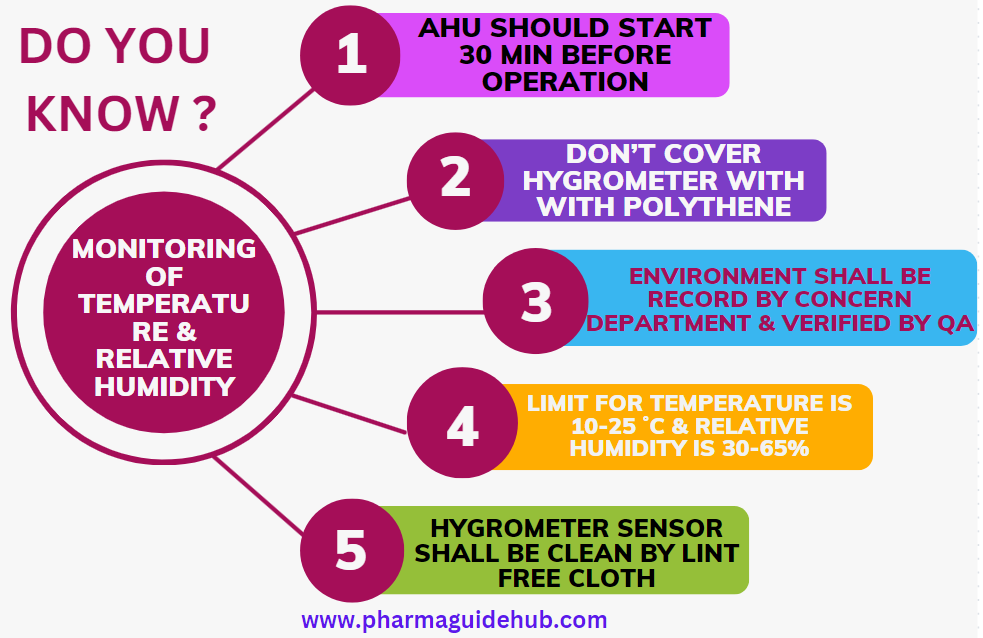
- Calibration of Digital Temperature & Relative Humidity Indicator and magnehelic Gauge:
- Ensure the calibration of Digital hygrometer is done as per calibration schedule.
- Calibration tag shall always be affixed with the instrument.
Click the link for download word file copy of this document: https://pharmaguidehub.com/product/environment-monitoring-procedure/
- MONITORING AND RECORDING OF DIFFERENTIAL PRESSURE
- Differential gauge Id. No. shall be assigned as follows:
Where,
AAA | : | It indicated Company name abbreviation |
“/” | : | It indicated Separator |
XX | Department Name (PD, QC, WH, EG. HR) | |
MG | : | It indicates Magnehelic gauge |
ABC | : | It indicates three digit serial number e.g. 001, 002, 003 |
Example: AAA/PD/MG/001, AAA/PD/MG/002.
- Ensure that calibrated Magnehelic gauges are provided to check the differential pressure.
- Observe the differential pressure displayed on the Magnehelic gauge and record the same in the Annexure-I.
- Ensure that the Air handling units are switched on 30 minutes prior to start any manufacturing operation.
- All the doors shall be kept closed. Check the cleanliness of the area visually.
- Open the door of respective area and ensure Differential Pressure is set at ZERO (0), while door is opened.
- For QC, warehouse (general storage areas) & manufacturing area, secondary packing area Differential Pressure is not applicable.
- Differential pressure is monitored by a Magnehelic gauge. Differential pressure shall be monitored twice a day.
- If differential pressure is out of limit, inform QA and maintenance for rectification. After rectification the same shall be monitored again, if it is within the limit, activity can be started.
- REFERENCES:
Schedule-M
- ANNEXURES:
ANNEXURE No. | TITLE OF ANNEXURE |
Annexure-I | Temperature, Relative humidity and Pressure Differential Record |
- DISTRIBUTION:
Controlled Copy No. 01 | : | Head Quality Assurance |
Controlled Copy No. 02 | : | Head Quality Control |
Controlled Copy No. 03 | : | Head Production |
Controlled Copy No. 04 | : | Head Warehouse |
Master Copy | : | Quality Assurance Department |
- ABBREVIATIONS:
QA | : | Quality Assurance |
SOP | : | Standard Operating Procedure |
RH | : | Relative Humidity |
DP | : | Differential Pressure |
- REVISION HISTORY:
CHANGE HISTORY LOG
Revision No. | Details of Change | Reason for Change | Effective Date |
00 | New SOP | Not Applicable | To be written manual |
Click the link for download word file copy of this document: https://pharmaguidehub.com/product/environment-monitoring-procedure/
ANNEXURE-I
TEMPERATURE, RELATIVE HUMIDITY AND PRESSURE DIFFERENTIAL RECORD
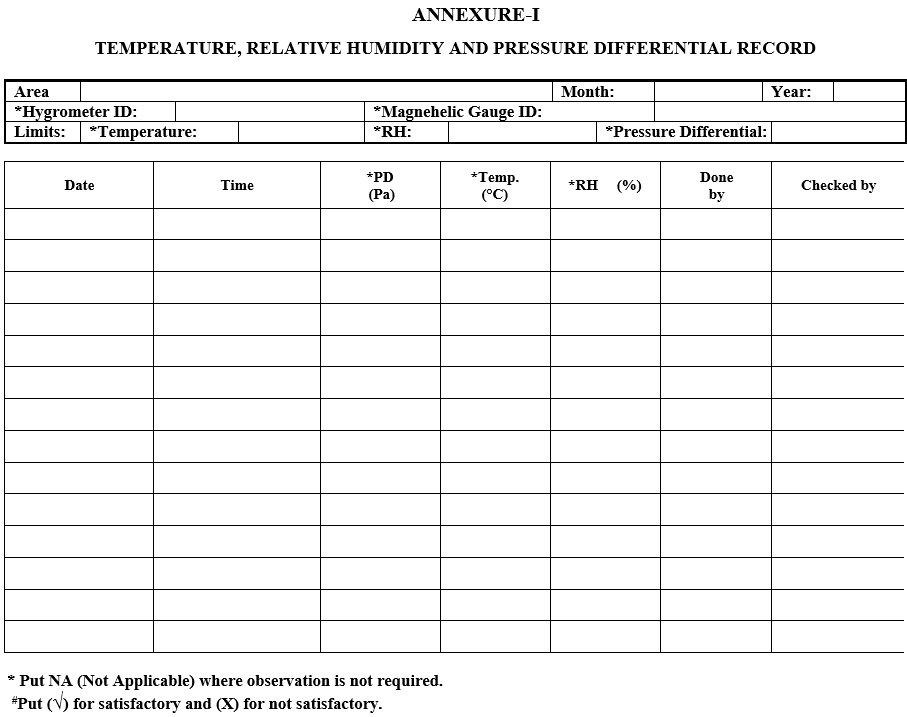
Frequently Asked Question?
- Why is it important to monitor temperature, humidity, and differential pressure in the controlled area?
The temperature, humidity, and differential pressure can affect the stability and quality of pharmaceutical products. Monitoring these parameters ensures that the environment is suitable for safe and effective production. - What are the acceptable ranges for temperature and humidity in the controlled area?
The acceptable ranges are 10-25°C for temperature and 30-65% for relative humidity. However, these may vary depending on the specific dosage form being handled. - What happens if the temperature or humidity is out of range?
If the temperature or humidity is out of range, it could impact the product’s quality and stability. If this happens, QA and maintenance should be notified for rectification. - How often should temperature and humidity be monitored?
Temperature and humidity should be recorded: * At the beginning of each shift * Twice per shift if no activity is ongoing * Randomly by IPQA
5. What should be done before recording temperature and humidity?
Ensure the HVAC system is on and the cubicle doors are closed.
6. What to do with the digital hygrometer?
- Ensure it is clean and free of dust.
- Do not cover it with plastic or PVC.
- Place it at the designated “hot point” location.
7. Who is responsible for verifying the readings?
- The concerned department initially verifies the readings.
- IPQA conducts random verification.
8. Why is differential pressure monitored?
Differential pressure ensures proper air flow and prevents contamination from entering the controlled area.
9. What equipment is used to measure differential pressure?
Calibrated Magnehelic gauges are used.
10. How is differential pressure monitored?
- Check if the calibrated Magnehelic gauge is available.
- Observe and record the displayed pressure in Annexure-I.
- Ensure the Air Handling Units are on 30 minutes before starting operations.
- Check that all doors are closed and the area is clean.
- Open the door of the area and confirm the pressure is 0.
- Differential pressure is not applicable for specific areas like QC, warehouse, and secondary packing.
11. How often is differential pressure monitored?
Differential pressure is monitored twice a day.
12. What happens if the differential pressure is out of range?
Inform QA and maintenance for rectification and re-monitor after rectification.
Click the link for download word file copy of this document: https://pharmaguidehub.com/product/environment-monitoring-procedure/