OBJECTIVE:
To lay down the procedure for Fogging/Fumigation in production areas.
SCOPE:
This SOP is applicable to the procedure for Fogging/Fumigation in production areas.
RESPONSIBILITY:
Initiator Officer/Executive/Designee: Production shall perform the operation activity as per SOP.
Executive/Designee IPQA to ensure the procedure is followed during operation as per SOP
Head/Designee: Production shall ensure the compliance of the SOP.
ACCOUNTABILITY:
QA Head shall be Accountable for implementation of SOP.
ABOUT FOGGING AND FUMIGATION:
Fogging/fumigation is a crucial step in maintaining aseptic conditions within pharmaceutical production areas. It involves the dispersion of a fine mist or vapor of a disinfectant or pesticide throughout the environment. This process aims to eliminate or significantly reduce microbial contamination, including bacteria, fungi, and insects. By effectively controlling microbial populations, fogging/fumigation minimizes the risk of product contamination, ensures product quality and safety, and protects the health of personnel working within the controlled environment.
Key Considerations:
Monitoring: Implement robust monitoring procedures to assess the effectiveness of the process and identify any potential issues.
Agent Selection: Choose appropriate agents with low toxicity, rapid action, and minimal environmental impact.
Application: Conduct fogging/fumigation during non-production hours to avoid product contamination.
Validation: Thoroughly validate the process to ensure effectiveness and demonstrate compliance with regulatory guidelines (e.g., GMP).
PROCEDURE:
Precautions to be taken during the Fogging/Fumigation process:
Update the status label as “AREA UNDER FOGGING/FUMIGATION”.
Ensure that AHU is in “ON” condition during fogging.
Determination of the volume of room for fogging and total Fogging/Fumigation time:
Determine the room volume and quantity of disinfectant to be used for Fogging/Fumigation by using the following formula:
- Total Room volume (ft 3) = Length (ft) x Width (ft) x Height (ft)
- Quantity of disinfectant (mL) = Total Room volume (ft 3 ) x 0.17
- Where 0.17 is application rate in mL/1 ft 3 in case of Bacillocid special 1 % solution.
Click the link to download word file copy of this document:
https://pharmaguidehub.com/product/fogging-fumigation-in-production-area/
Preparation of 1.0% v/v Bacillocid special solution: The required quantity of Bacillocid special & Purified water shall be measure by using the measuring cylinder as per below example.
Example: 100 ml of Bacillocid special & 9.900 ml of purified water shall be taken for Preparation of the 1.0% v/v Bacillocid special solution.
- Pour the calculated quantity of Bacillocid special and purified water in to the SS container. Stir the solution properly.
- Close the lid of the container.
- Record the activity in format II.
Fogging/Fumigation Process:
- Transfer the Cleaned fogger machine into the cleaned areas with surface sanitization using Bacillocid special 1.0% v/v.
- Bacillocid special 1.0% v/v solution for Fogging/Fumigation and prepare the disinfectant solution.
- Take the freshly prepared Bacillocid special 1.0 % v/v solution in fogger.
- Keep the fogger on floor.
- Connect the plug to the power supply.
- Fogging shall start from end of the room towards entrance door
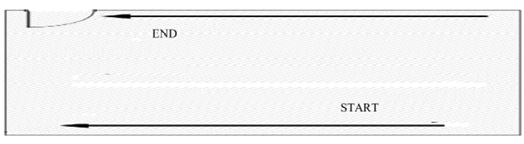
- Change the position of fogger to cover entire walls, all corners of wall and ceiling, entire area and all external surfaces of equipment’s.
- Follow the sequence room wise for fogging and record the same in Format I (Equipment Log).
- After the complete consumption of disinfectant solution equipment will stop automatically.
- Remove the plug from the electrical connection and carry the fogger to another room.
Cleaning of area:
- After completion of Fogging/Fumigation wait for NLT 1 hours in which AHU exhaust duct should be in opened condition.
- Start the cleaning of the area as per SOP with AHU exhaust open.
- Clean the equipment outer surface with lint free cloth using 70%v/v IPA.
- Remove the cautionary sign boards and declare the area suitable for use after cleaning for environment monitoring.
Cleaning of Disinfectant fogger:
- Empty the tank and clean internal surface of the fogger with Lint free cloth.
- Clean the external surface of the fogger with dry lint free cloth followed by lint free cloth dipped in 70 % IPA.
Frequency:
The fogging of clean area shall be carried out in the following cases:
- Before start-up of new facility or after major modification of the production area.
- After a long shutdown of AHU.
REFERENCES:
Not Applicable
ANNEXURES:
Annexure Number | Title of annexure |
Annexure-I | Fogging Log |
Annexure-II | 1.0 % V/V bacillocid special preparation and usage log sheet |
ENCLOSURES: SOP Training Record.
DISTRIBUTION:
Master Copy : Quality Assurance Department
Controlled Copy No. 01 : Head Quality Assurance
Controlled Copy No. 02 : Head Production
ABBREVIATIONS:
PD | : | Production |
No. | : | Number |
SOP | : | Standard Operating Procedure |
BMR | : | Batch manufacturing record |
HDPE | : | High density polyethylene |
IPQA | : | In process Quality Assurance |
REVISION HISTORY:
CHANGE HISTORY LOG
Revision No. | Details of Changes | Reason for Change | Effective Date |
00 | New SOP | Not Applicable | To Be Written Manual |
Annexure-I
Fogging Log
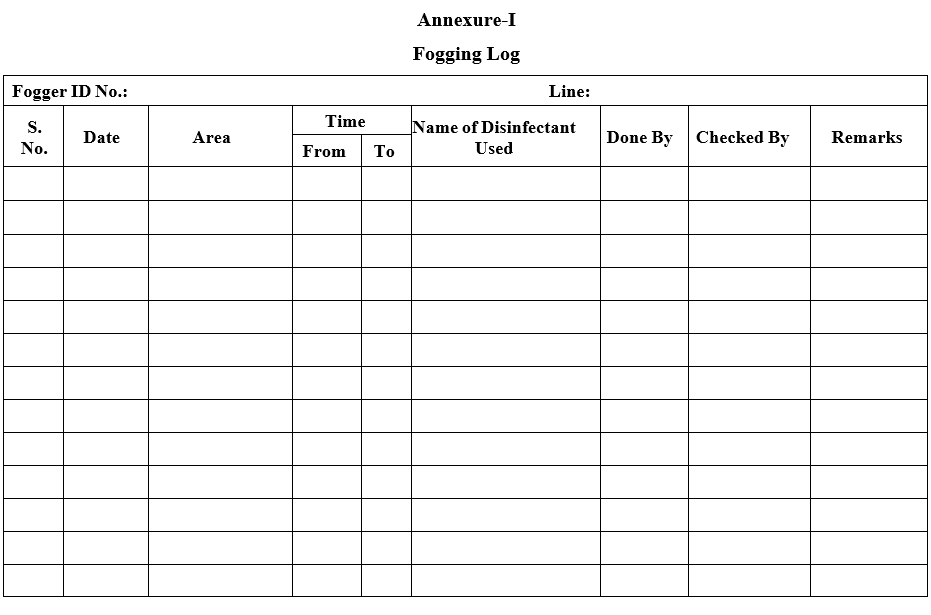
Annexure-II
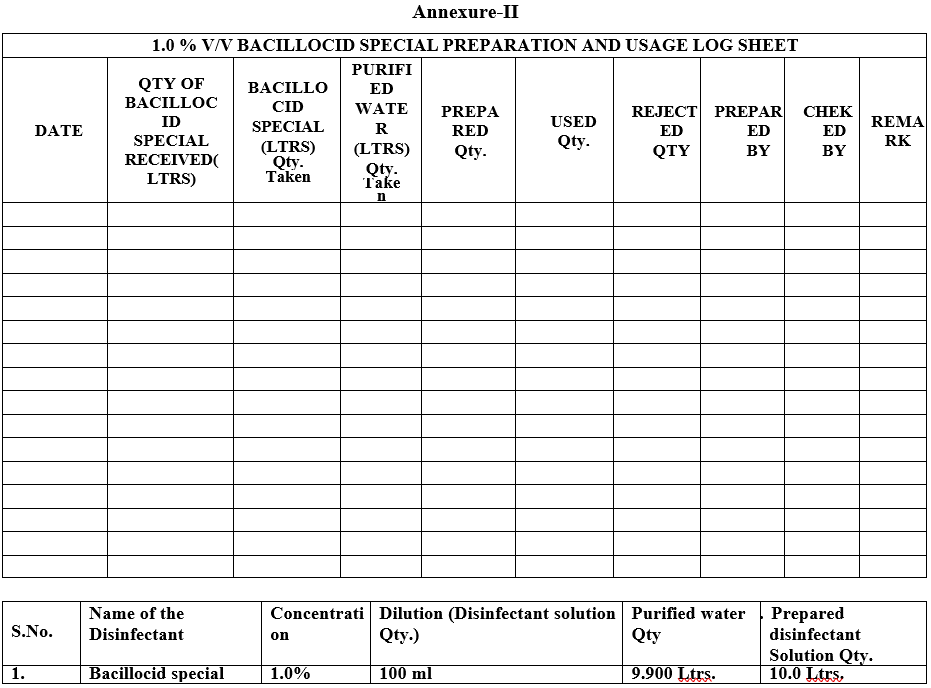
Click the link to download word file copy of this document:
https://pharmaguidehub.com/product/fogging-fumigation-in-production-area/