OBJECTIVE:
To lay down a Procedure for Good Documentation Practices.
SCOPE:
This SOP is applicable for Good Documentation Practice at {Company Name} {Company Location}.
- RESPONSIBILITY:
- All departments shall be responsible to follow procedure for Good Documentation Practice.
- All department Head shall be responsible to supervise the GDP in all departments.
- QA Executive/Designee shall review and technical correction of SOP.
- ACCOUNTABILITY:
QA Head shall be accountable for Training, Approval & Compliance of this SOP.
- PROCEDURE:
PRINCIPLE:
“Good Documentation” constitutes an essential part of the Quality System and is related to all aspects of GMP.
- DATE FORMATING:
- Date shall be written as DD/MM/YY format:
Where:
“DD” : Represents the Date.
“/” : Represents Separator.
“MM” : Represents the Month.
“YY” : Represents the Year.
For Example: 01/12/22, 01 shall represent Date, 12 shall represent the Month and 22 shall represent the last two digits of the current Calendar Year.
- Always use two digits for all three (i.e. Date, Month and Year).
- TIME FORMATING
- Time Entry shall be done in all Documents as Twenty Four Hours Clock.
For Example: 1:30 PM shall be written as 13:30, 12:00 Midnight shall be written as 00:00 and 12:00 Noon shall be written as 12:00.
Click the link for download word file copy of this document: https://pharmaguidehub.com/product/good-documentation-practices/
- DOCUMENT ENTRIES:
- QA Department, recording / signing the documents / records shall use a ball point pen in Black ink.
- Other Department, recording / signing the documents / records shall use a ball point pen in Blue ink.
- Signing of all master documents shall be done with ball point pen in blue ink.
- Never use the symbol such as “–do-” for repeated observations.
- If any wrong entry made in documents, do not overwrite on it, strike out by single line as (_____), put actual value beside this and make a remark for justification of wrong entry adjacent to it or if there is no sufficient space, put the star mark then write anywhere, where space is available on the same page with short signature and date.
For Example: If space available within the line then
01/12/22
01/12/2022 and shall put remark wrong entry rectified with sort signature and date.
If space not available within the line then:
01/12/22
01/12/2022* and shall put where space is available * wrong entry rectified with sort signature and date
- Design and prepare documents in an orderly fashion and in accordance to the standards in such a way that they are easy to check.
- Appropriate and authorized persons shall approve the documents. Sign on the documents shall be same signatures as done in the “Specimen Signature Record”.
- To change/modify in any document shall be done as per SOP No. QA/017 (SOP on Change Control Procedure); same SOP shall be applicable if documents are required to be discontinued.
- Each document shall be review after completion of any process/activity for their completeness and correctness (within their defined review period if applicable) and keep them up to date.
- Where documents required the entry of data; entries shall be clear, legible and indelible handwriting. Provide sufficient space for such entries.
- Maintain records for the distribution of documents. Regularly update document index and document history.
- Do not over write any data and do not leave blank in process sheet, batch manufacturing records, logbooks and laboratory logbooks. If, any page/column is not used, draw line from left to right diagonally and put remark as NA (Not Applicable) with sign/date.
- For Example:
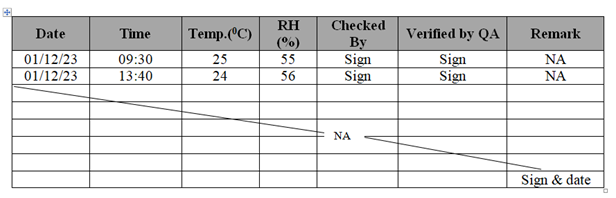
- All master documents shall be kept under lock and key.
- All files shall be labeled with appropriate information and shall be preserved in logical sequences for better accessibility as per Annexure-II.
- Corrective fluid (white ink) or erasable pens should not be used to correct the original information.
- Master documents shall not be stapled.
Click the link for download word file copy of this document: https://pharmaguidehub.com/product/good-documentation-practices/
- Refer below guideline for presenting/recording commonly used units:
S. No. | Parameter | Unit | Presentation of Unit | Example |
1. | Duration/Period | Second | Sec | — |
Minutes | Min | — | ||
Hours | Hrs | — | ||
2. | Weight | International Unit | IU | — |
Microgram | mcg | |||
Milligram | mg | — | ||
Gram | g | — | ||
Kilogram | Kg | — | ||
3. | Length | Decimeter | dm | — |
Millimeter | mm | — | ||
Centimeter | cm | — | ||
Meter | m | — | ||
4. | Volume | Micro liter | µl | — |
Milliliter | ml | — | ||
Liter | L or lit | — | ||
5. | Temperature | Degree centigrade | °C | — |
Degree Fahrenheit | °F | — | ||
6. | Pressure | Kilogram per square centimeter | Kg/cm2 | — |
Bar | Bar | — | ||
Pounds per square inch | psi | — | ||
Pascal | Pa | — | ||
7. | Quantity in Number | Number | No. | — |
Numbers | Nos. | — |
- Verification of Data, Information, Calculations and Tasks:
- Verification of data, information, calculations or tasks performed by another person means the verifier shall independently determine that the data, information, calculations, or tasks are accurate and correct. For example-when a calculation is being verified, the verifier shall repeat the calculation before signing off it.
- When a performance of a task is being verified, the verifier shall witness the task being performed.
- When data is being verified, the verifier shall witness the display or printout of the instrument providing the data.
- The entire format shall be filled by concerned department officer/executive and shall be verified by department head or as written on the format.
- Attachments, Printouts and Charts:
- Identify all printouts, charts attachments that are used to support an analytical record or process with the applicable batch number, time, and date and operator initial. Confirm that there is enough ink supply for all print out and chart devices to make the printout easily readable. Print outs need to be continuous and if broken there needs to be an explanation included.
- Missed information / data and blank spaces in documents:
- There should be no gaps in information on a document. Always complete all required information and be consistent when documenting units of measure, dates, acronyms and abbreviations.
- Document Ratification:
To agree for correction in master document for the errors identified during review or operational use with proper scientific rationale / justification.
Click the link for download word file copy of this document: https://pharmaguidehub.com/product/good-documentation-practices/
- Ratification:
- Ratification shall be made in the master document for errors identified during final review or during operational use.
- If there are any minor corrections like typographical errors, then the concerned department personnel shall raise the ‘Request for Document Ratification” as per Annexure-I.
- The request shall be justified by concern HOD and shall be forwarded to QA Head or designee for evaluation and approval.
- During the evaluation QA Head or designee shall assess the impact of the required correction in the master document and earlier records that might have been affected.
- In case the rationale for ratification is not scientific and justified, the request shall be rejected by QA Head or designee and appropriate change control shall be initiated.
- Once the request is approved ratification shall be done by the Head of the concerned department and by QA Head or designee in the master document and the controlled/issued user copies. The ratification shall be signed and dated.
- All this ratification shall be made at the same time in master copy along with controlled or issued user copies.
- The information for the ratification shall be sent to the original signatories.
- The indicated ratification shall be made in the soft copy after approval by QA Head and shall be implemented on upcoming revision of master document.
- Once all controlled/issued user copies/master copies are ratified, the request shall be closed by QA Head or designee and filled along with the master document.
- REFERENCES:
Not Applicable
- ANNEXURES:
ANNEXURE No. | TITLE OF ANNEXURE | FORMAT No. |
Annexure- I | Request For Document Ratification | QA-013/F01-00 |
Annexure- II | Format for Label | QA-013/F02-00 |
ENCLOSURES: SOP Training Record.
- DISTRIBUTION:
Controlled Copy No. 01 | : | Head Quality Assurance |
Controlled Copy No. 02 | : | Head Quality Control |
Controlled Copy No. 03 | : | Head Production |
Controlled Copy No. 04 | : | Head Engineering |
Controlled Copy No. 05 | : | Head Human Resource |
Controlled Copy No. 06 | : | Head Warehouse |
Master Copy | : | Quality Assurance Department |
- ABBREVIATIONS:
SOP | : | Standard Operating Procedure |
No. | : | Number |
Ltd. | : | Limited |
QA | : | Quality Assurance |
P & A | : | Personnel and Administration |
HR | : | Human Resource |
- REVISION HISTORY:
CHANGE HISTORY LOG
Revision No. | Details of Changes | Reason for Change | Effective Date |
00 | New SOP | Not Applicable | To be written manually |
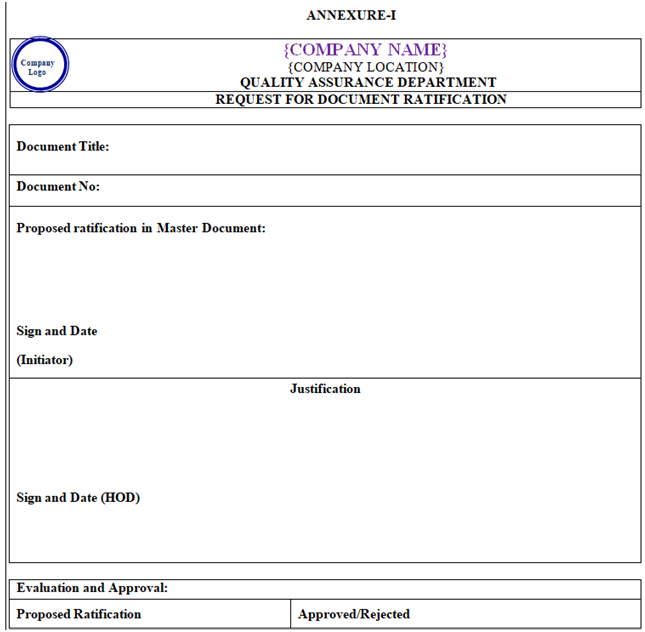
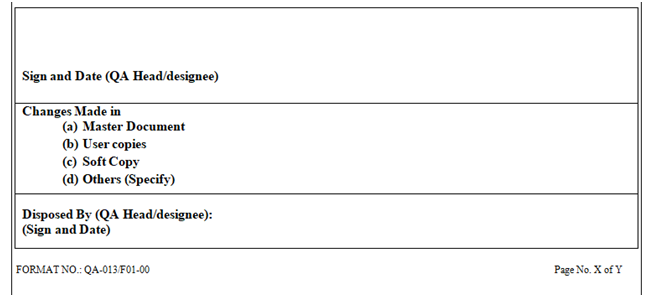
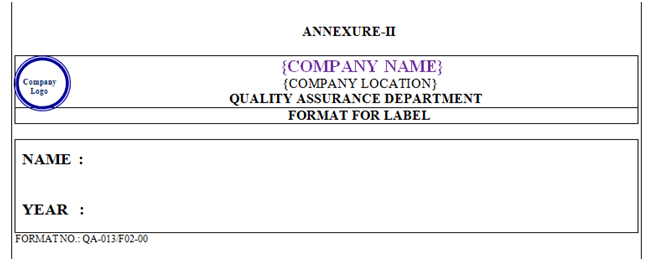
Click the link for download word file copy of this document: https://pharmaguidehub.com/product/good-documentation-practices/