- OBJECTIVE:
To describe a standard operating procedure for various types of Personal Protective Equipment, their usage and disposal.
- SCOPE:
This Procedure is applicable for handling and maintenance of personal protective equipment at {Company Name} {Company Location}.
- RESPONSIBILITY:
- Representative of SHE department
- In charge Stores
- Departments In charge.
- ACCOUNTABILITY:
QA Manager shall be accountable for Approval & Implementation of SOP.
- PROCEDURE:
- Safety Appliances, which are used in factory premises, are received and stored in store department.
- Certification of PPE:
- Safety Appliances received from supplier are checked as per specification Annexure-I.
- Defective appliances are rejected and returned to the supplier.
- Certification for effectiveness and fitness of safety appliances for intended use is to be taken from the vendors.
- Usage of PPE:
- Stores will issue the safety appliances to the user department on the issue slip.
- Note: Department had to ensure that required safety appliances are available in the department.
- Safety appliances are to be used by personnel as per the requirement of the process or operation at work.
- All personnel are trained in the correct usage of appliances by the Safety department.
- After use the following mentioned appliances are to be cleaned by wiping with cloth.
- Safety goggles.
- Online air mask. / Powder Mask
- 3M Dust Mask
- Ear muff.
- Ear plug.
- Safety helmet
- After use the following mentioned appliances are to be cleaned by wiping with water.
- Hand gloves (to be discarded after wash in appropriate bins, this is not applicable in production areas. In production areas they can be thrown directly in the assigned bins).
- Pressure suit.
- PVC apron.
- For certain items standards are available i.e. IS or EN in such case ensure the appliance is marked with such mark and carries the certificate. During disposal of the above safety appliance the following method will be followed.
- Before disposal wash all the items with water & drain the water to effluent treatment plant.
Sr. No. | Item | Method of Disposal |
1 | Acid/Alkali proof rubber hand gloves,Surgical hand glovesCotton hand glovesFoam ear plugSafety beltsPVC apron Nitrile hand gloves / Neoprene hand glovesAir pressure suit | Cut these items using suitable scissors. Collect it in a suitable polythene bag and send for scrap. |
2 | Safety Shoes | Pack it in a suitable polythene bag and send for scrap. |
3 | Safety gogglesFace shield | Detach the glass/acrylic sheet and collect in a suitable polythene bag and send for scrap. |
4 | On line air mask.Safety helmet | Break these items with a hammer, collect it in a suitable polythene bag and send for scrap |
- Maintenance:
- All safety appliances are checked prior to use by user & periodically crosschecked by safety department for its suitability and working condition.
- If any of the appliances are found defective, it should be discarded.
- REFERENCES:
Not Applicable
- ANNEXURES:
ANNEXURE No. | TITLE OF ANNEXURE |
Annexure-I | Personal Protective Equipment Specifications |
ENCLOSURES: SOP Training Record.
- DISTRIBUTION:
Controlled Copy No. 01 | : | Safety Health & Environment |
Master Copy | : | Quality Assurance Department |
- ABBREVIATIONS:
PPE | : | Personal Protective Equipment. |
SOP EN IN | : : : | Standard Operating Procedure European Norms. Indian Standard. |
- REVISION HISTORY:
CHANGE HISTORY LOG
Revision No. | Details of Changes | Reason for Change | Effective Date |
00 | New SOP | Not Applicable | To be written manual |
ANNEXURE-I
PERSONAL PROTECTIVE EQUIPMENTS SPECIFICATIONS
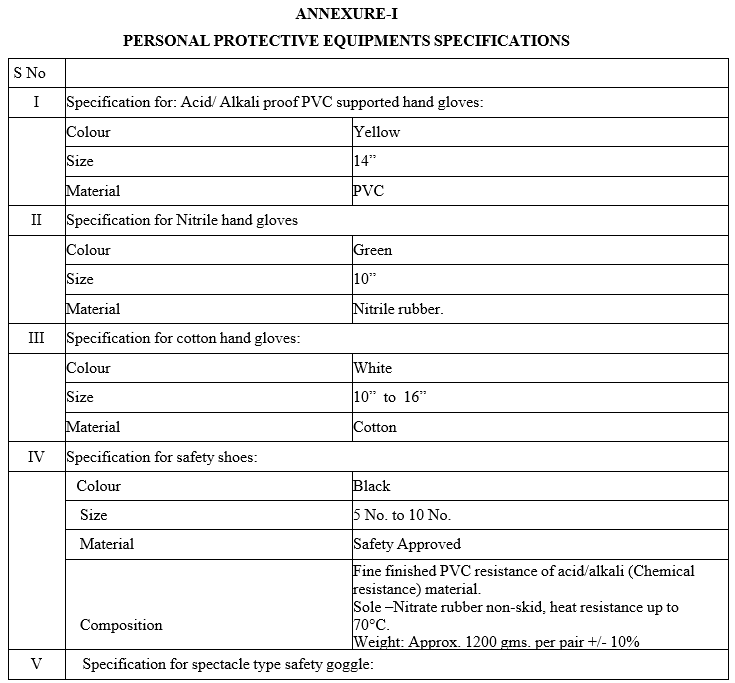
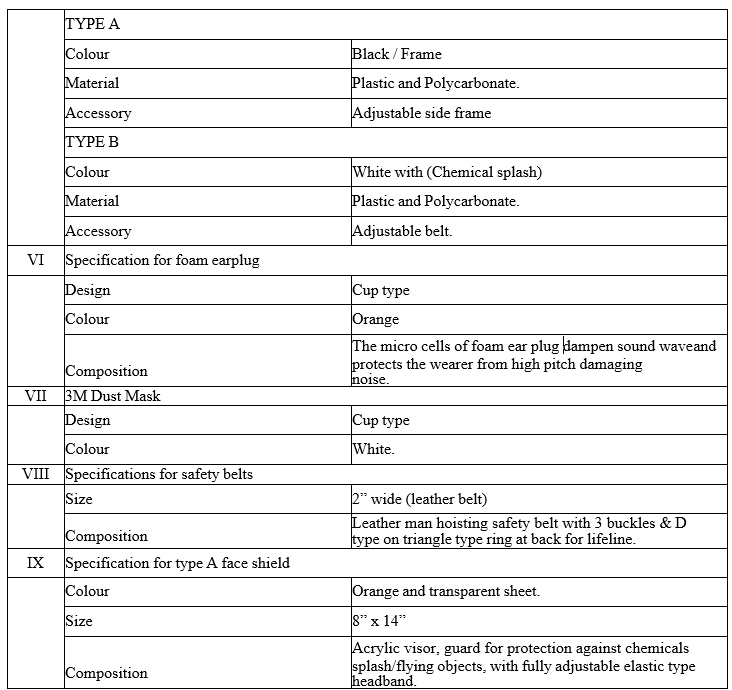
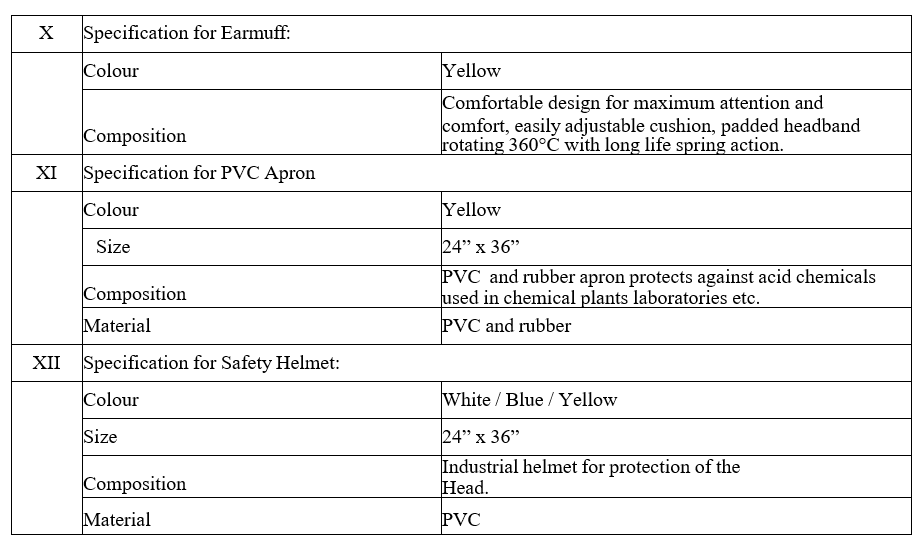
Frequently Asked Question?
Q: What is the purpose of safety appliances in the factory?
A:Safety appliances are used to protect workers from hazards in the factory.
Q: How are safety appliances certified?
A: Safety appliances are checked against specifications and certified for effectiveness and fitness for use.
Q: How are safety appliances issued to users?
A: Safety appliances are issued to users on an issue slip, and departments are responsible for ensuring they have the required appliances.
Q: How are safety appliances used?
A: Safety appliances are used as per the requirements of the process or operation, and all personnel are trained in their correct usage.
Q: How are safety appliances cleaned?
A: Specific cleaning methods are outlined for different types of safety appliances, such as wiping with a cloth for goggles and ear protection, and washing with water for gloves and suits.
Q: How are safety appliances disposed of?
A: Safety appliances are disposed of by cutting them up and sending them for scrap, with some exceptions like safety shoes and helmets which are sent whole.
Q: How are safety appliances maintained?
A: Safety appliances are checked before use by users and periodically by the safety department to ensure they are suitable and in good working condition. Defective appliances are discarded.