- OBJECTIVE:
To lay down a procedure for handling of Market Complaints in order to ensure that complaints are recorded, investigated, responded and reviewed in a timely manner to prevent further recurrence and satisfy the complainant.
- SCOPE:
This procedure is applicable for handling the Market Complaints received for the drug products manufactured at {Company Name} {Company Location}.
- RESPONSIBILITY:
- Officer/ Executive QA:
- To log the complaint received in market complaint logbook and check for serious adverse event if complained.
- To maintain the complaint record and prepare trend.
- Manager QA/ Designee:
- To investigate and identify the root cause of the complaint.
- To suggest CAPA in consultation with Marketing Authorization Holder / Customer.
- To ensure implementation of CAPA and follow up for its effectiveness.
- To reply the complainant on timely basis.
- Head Production/ Designee:
- To investigate the complaint from manufacturing point of view, prepare & submit the findings to QA along with corrective and preventive actions.
- Head QC:
- To arrange analysis of the complaint /Control sample whenever required.
- To support in investigation of complaint whenever required.
- QA Head:
- To review and approve investigation report.
- To review the complaint trend.
- To ensure implementation of CAPA
- Closure of Market complaint.
- Marketing Authorization Holder:
- To provide effective and timely intimation to site QA for notifying the complaints, to arrange for complaint samples where possible, to inform investigational feedback / outcome of the investigation to the complainant. To give feed back in case recall is warranted in that country.
ACCOUNTABILITY:
QA Head and RA shall be accountable for the compliance of this SOP
- PROCEDURE:
- Any written communication received from a complainant either through mail, post, or fax/ Genuine Verbal communication received from Distributor / Retailer / Stockiest / Field staff / Customer / Doctor/ Marketing department or any Regulatory Authority etc. regarding the defects in the product safety, identity, strength, purity, efficacy, quality, shortage or any other such complaint shall be considered as market complaint.
- The complaint shall be immediately forwarded to Head & or responsible person of the organization.
- QA Head shall acknowledge the complainant for the receipt of complaint within 3 working days from the receipt of complaint with tentative response period through any type of written communication. After acknowledge the complaint it shall be log within 3 working days.
- QA Head shall initiate investigation and form investigation team.
- QA Head shall inform about the complaint to respective section of Market Complaint handling team along with the complaint sample & its photograph (if received).
- Officer/Executive QA shall log the complaint in the logbook for receipt of Market Complaint number shall be maintained as per the Annexure-I.
- CLASSIFICATION OF MARKET COMPLAINTS :
Manager QA/Designee shall write the complaint product details and categorize the nature of complaint based on the investigation as:
- Critical: A defect having a significant impact on product quality and/or safety and likely to have serious and/or harmful effect on the patient.
The complaint shall be classified as Critical if it is related to:
- Adverse Event and Adverse drug reaction.
- Major health hazard causing permanent deficiency or death.
- Purity & safety of the product.
- Potency loss.
- Abnormal impurity level.
- Cross contamination issues.
- Complains related to stability of the product.
- Incompatibility of product and primary pack.
- Fungal/bacterial contamination.
- Non-compliances from registered specifications which are regarded as critical to the safety and/or efficacy of the product (i.e. assay, stability, target weight)
- The lead response time shall be within 24 hours of login.
Major: A defect other than a critical defect, that is likely to result in a failure or reduction in the suitability of use of a unit for its intended purpose.
Click the link for download word file copy of this document: https://pharmaguidehub.com/product/handling-of-market-complaints/
The complaint shall be classified as Major if it is related to:
- Problem with primary packaging of the product, or primary packing material.
- OOS observation reported by external laboratory.
- Dosing issues.
- Leaflet or literature with the product is incorrect or having art work issues.
- Chemical / physical attributes of the product leading to discoloration, variation in odour without affecting the safety & efficacy.
- Extraneous contamination, mix-ups.
- Problems related to labeling and coding of batch details.
- Major quality defects include non-compliances from registered specifications which are not regarded as critical to the safety and/or efficacy of a product.
- The lead response time shall be within 15 Working days after login.
Minor: A defect that is not likely to reduce usefulness of a product unit for its intended purpose, but which is a departure from established standards, having little bearing on the effective use or operation of the unit.
The complaint shall be classified as Minor if it is related to:
- Shortages.
- Breakages, sealing defects not impacting product quality/safety.
- Secondary packing materials such as Label etc.
- Color shade variation etc.
- Tertiary packing not affecting primary pack.
- The lead response time shall be within 30 Working days after login.
Non substantiated: Those complaints which are not due to any problem in manufacturing, analysis, packing or stability and may be due to mishandling at customer’s end, incorrect storage/ usage not following the instructions given in the literature of the product by the customer, incorrect method of analysis used or wrong interpretation of the information/data and where no corrective /preventive action is required at the manufacturing site. The lead response time shall be within 30 Working days after login..
NUMBERING OF MARKET COMPLAINTS:
For each market complaint, a unique “market complaint number” shall be assigned by QA. The Market Complaint number shall consist of nine (09) alphanumeric characters.
Numbering of market complaint shall be assign in following way: MC/YY-NNN.
In the market complaint number, the first two (02) characters “MC” represent market complaint.
The 3rd character “/” is a forward slash.
The 4th,5th characters represent the last two digit of the calendar year.
The 6th character ‘-‘is a hyphen (as a separator)
The last three numeric characters represent the sequential number of the market complaint for the calendar year.
Officer QA shall issue the Complaint Investigation form as per Annexure-II. The necessary details related to complaint shall be filled by QA. Preliminary investigation report may be shared covering immediate observations.
In-case complaint is received directly for products of Contract Giver, complaint will be acknowledged to the complainant with intimation to Contract Giver/Manufacturing authorization holder within 3 working days.
Click the link for download word file copy of this document: https://pharmaguidehub.com/product/handling-of-market-complaints/
We shall not consider the market complaint in case of complainant shall unable to provide the batch number details of suspected product.
QA Head shall initiate in house investigation including necessary analysis of complaint sample and the control sample, if applicable.
A copy of the complaint along with complaint sample (if any) shall be sent to the respective department for investigation.
The respective department shall further investigate the complaint with respect to their area and shall submit their comments to QA Head.
On receipt of the complaint preliminary categorization of nature of complaint as Critical, Major, Minor or Non substantiated will be done by QA Head. The status of this initial classification done may get changed based on the outcome of the investigation conducted as per Annexure-II.
QA Head initiates special monitoring of operation or in process inspection or final product testing as appropriate based on nature of complaint.
History for the similar nature of complaint shall be assessed for last one year.
Depending on the nature of complaint, Following or selected checks shall be performed as appropriate during investigation:
Control samples shall be inspected visually and analyzed (if applicable) & compared with the complaint sample if available. Pre and Post batches may be tested.
The batch manufacturing & packing record and analytical record shall be checked with respect to complaint.
If required during the investigation detailed discussion shall be carried out with concerned officer & workmen with respect to complaint.
Complaint sample from the customer shall be requested.
Click the link for download word file copy of this document: https://pharmaguidehub.com/product/handling-of-market-complaints/
QA, in consultation with concerned department head, shall carry out the investigation and prepare the investigation report.
If the complaint is critical/major regarding the quality and efficacy of the product, Manager QA/Designee shall send the control sample of same batch to Head QC for analysis.
If any OOS found in the complaint sample/control sample, before the shelf life of sample then investigation to be carried out as per Current version of SOP.
QA Head shall decide the extension of investigation if similar type of complaint for same product or different product has been received.
For Investigation methodology and root cause analysis, Investigational tools like fish bone analysis, why-why analysis or other investigation tools as appropriate shall be used.
Manager QA/Designee shall suggest CAPA against the identified root cause and investigation report shall forward to Plant operation.
QA Head shall send the investigation report to all concerned with the CAPA action in details along with target completion date of action.
QA Head shall review & approve the investigation report & accordingly reply to the complainant. If found necessary, replacement samples shall be sent to the complainant.
After complete investigation of market complaint QA Head shall confirm the final categorization of complaint as Critical, Major and Minor.
If the complaint is categorized as Critical, QA Head / Manager QA/Designee shall intimate to customer (Contract giver) to stop further distribution of the batch till the completion of investigation.
QA Head shall ensure that the recommended corrective/preventive actions are implemented to prevent the recurrence of any similar/same problem.
The CAPA for all the complaints shall be tracked as per of SOP on CAPA (QA/021).
Any change recommended shall be initiated through proper change control system.
The investigation report along with the reply to the customer has to be maintained in quality assurance.
If the cause is found to be with the quality of input material (RM or PM) the same shall be communicated to the vendor for corrective actions at their end, through purchase department.
In the case it is established that defect has occurred during transit, the Supply Chain/Export Logistics shall be requested to investigate and submit the report to QA.
If there is reason to believe that the batch in question fails to meet any of its specification or if the complaint represent a serious and unexpected drug experience then a report shall be prepared, process for ‘Recall’ (if necessary) shall be initiated as per Current version of SOP on product recall.
Decision for product recall / withdrawal may be taken by QA Head, {Company Name} {Company Location} based on the review of investigation report / observations.
Warehouse shall also be inspected for complaint batches if found necessary.
HANDLING OF COMPLAINT SAMPLES:
If the product sample is received along with the market complaint, it shall be thoroughly examined for the integrity of pack, physical appearance, printed text matter, quantity and evidence of deterioration. The details shall be filled in Annexure-II and shall also be mentioned in the investigation report.
QA shall ensure storage of complaint sample remaining after analysis in secured manner under desired storage condition as per product requirement.
Complaint sample shall be destroyed after closer of Market Complaint as per Current version of SOP on Standard Operating Procedure on Disposal of samples.
Destruction record of the complaint samples shall be maintained as per the Annexure-III.
RESPONSE TO CUSTOMERS:
Preliminary Investigation Report shall be sent to the complainant within 10 working days with the details of investigation done till date and further course of action.
Tentative date of Final Investigation Report shall be mentioned in the Preliminary Investigation Report along with the justification for extension of the investigation (such as requirement of complaint sample, period required for micro analysis, period required to receive clarification of queries raised against complaint details etc.).
The investigation shall be completed and response to customer about investigation findings shall be made as per lead time depending on the nature of the complaint along with the proposed Corrective and Preventive Action plan.
CLOSURE OF MARKET COMPLAINTS:
QA Head shall state the complaint closed and sign only if :
- Compliance to the proposed corrective action and preventive action has been done.
- Customer does not reply within 30 days after response made by {Company Name}{Company Location}.
REVIEW OF MARKET COMPLAINTS AFTER RESPONSE SENT TO COMPLAINANT:
QA Head shall review the complaint status every quarter to evaluate specific or recurring problem which require further action. This summary shall be shared with higher management in quality management review report as per current version of SOP No.
TREND OF MARKET COMPLAINTS:
Designated QA person shall prepare complaint trend including the product quality, shortage, labeling, empty Jar/bottle, packing material & sealing defects.
Click the link for download word file copy of this document: https://pharmaguidehub.com/product/handling-of-market-complaints/
Trends shall be reviewed by QA Head / Manager QA/Designee and require action shall be taken accordingly for indication of specific or recurring problem requiring attention and possible recall of marketed products. The trend report shall be prepared in order to take CAPA to avoid recurrence.
Trend shall be prepared after calendar year but before first quarter of next year.
Investigation of complaint can be carried out as follows but not limited to:
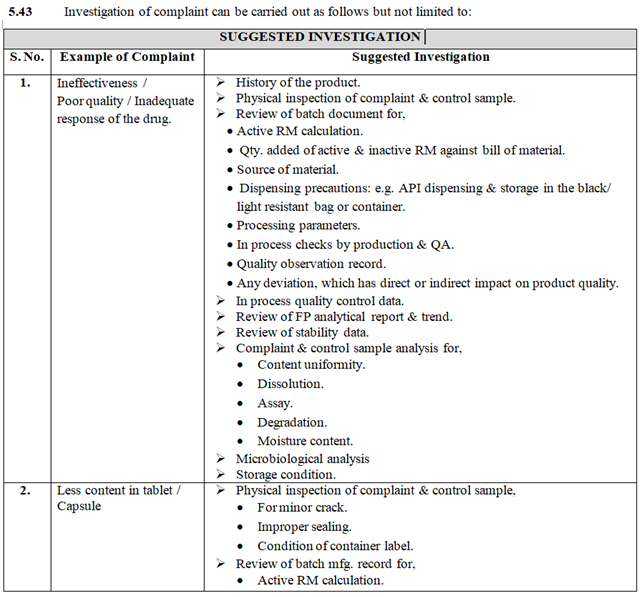
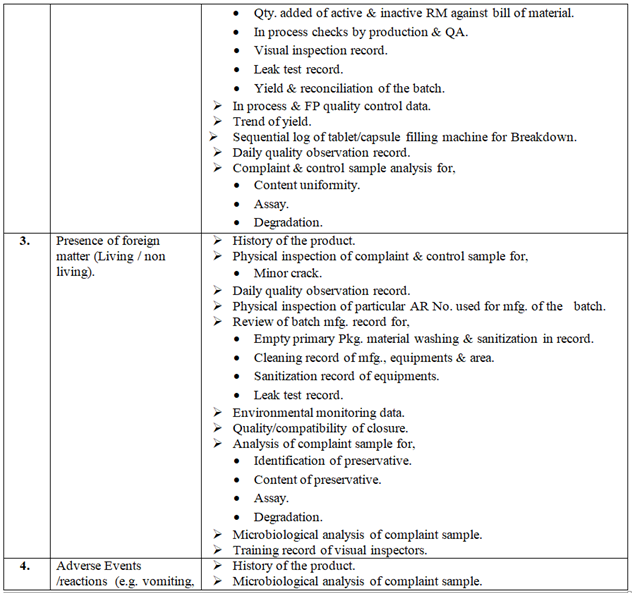
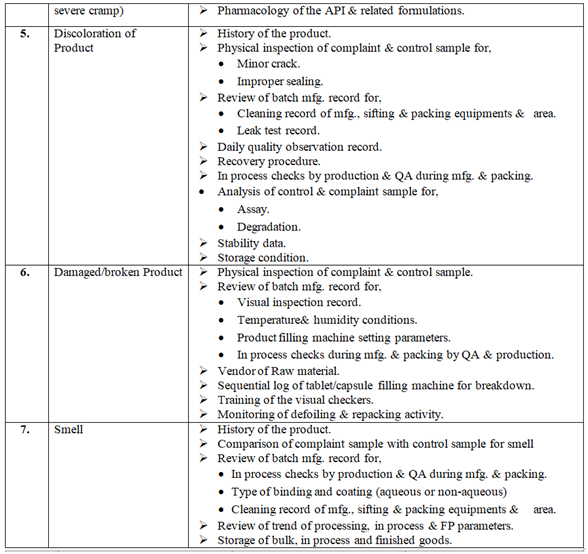
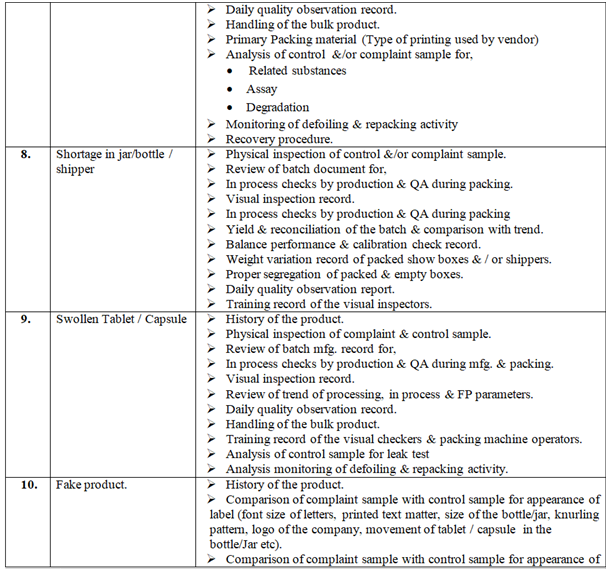
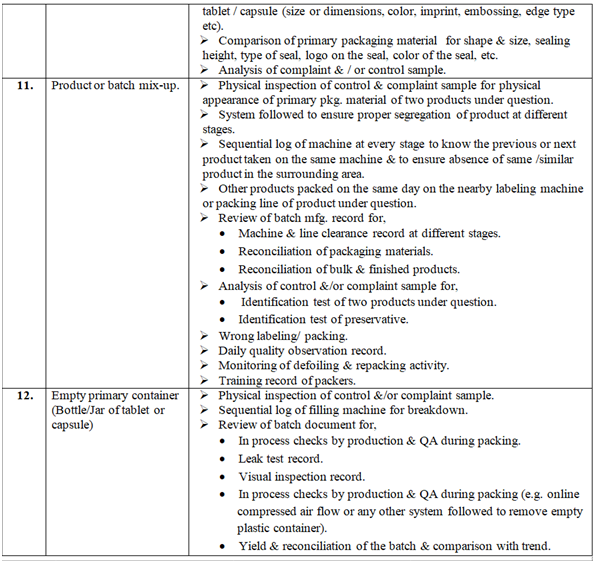
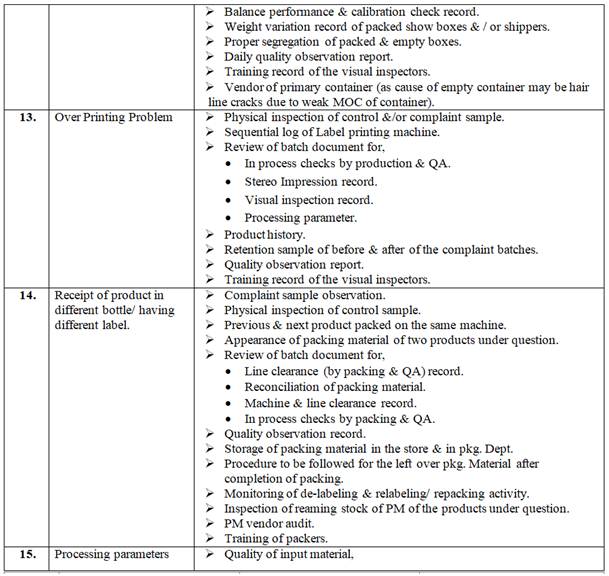
Click the link for download word file copy of this document: https://pharmaguidehub.com/product/handling-of-market-complaints/
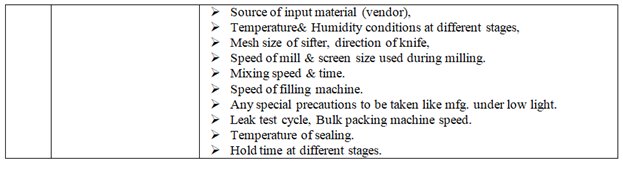
REFERENCES:
- PIC/S “Guide to Good Manufacturing Practice for Medicinal Products” PE 009-10.
- Drug & Cosmetics Act & Rules, India.
- 21 CFR 211.198
- ANNEXURES:
ANNEXURE No. | TITLE OF ANNEXURE | FORMAT No. |
Annexure-I | Logbook for Receipt of Market Complaint | QA-020/F01-00 |
Annexure-II | Complaint Investigation Report | QA-020/F02-00 |
Annexure-III | Destruction record of complaint sample | QA-020/F03-00 |
Annexure-IV | Trend of Market Complaint for Year | QA-020/F04-00 |
Annexure-V | Preliminary Investigation Report | QA-020/F05-00 |
ENCLOSURES: SOP Training Record.
DISTRIBUTION:
- Controlled Copy No. 01 : Head Quality Assurance
- Controlled Copy No. 02 : Head Quality Control
- Controlled Copy No. 03 : Head Production
- Controlled Copy No. 04 : Head Warehouse
- Controlled Copy No. 05 : Head Engineering
- Controlled Copy No. 06 : Head Purchase
- Master Copy : Quality Assurance Department
ABBREVIATIONS:
SOP | : | Standard Operating Procedure |
No. | : | Number |
Ltd. | : | Limited |
QC | : | Quality Control |
QA | : | Quality Assurance |
AR No. | : | Analytical Report Number |
Ref. | : | Reference |
Mfg. | : | Manufacturing |
Exp. | : | Expiry |
FP | : | Finished Product |
REVISION HISTORY:
CHANGE HISTORY LOG
Revision No. | Details of Changes | Reason for Change | Effective Date |
00 | New SOP | Not Applicable | To be written manual |
ANNEXURE – I
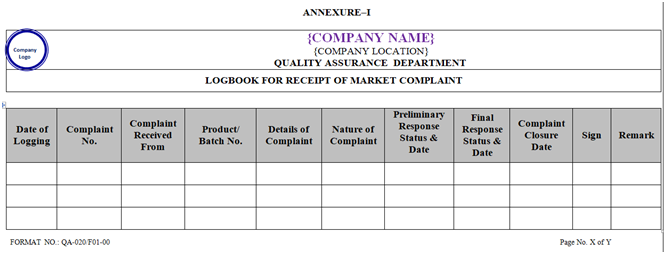
ANNEXURE – II
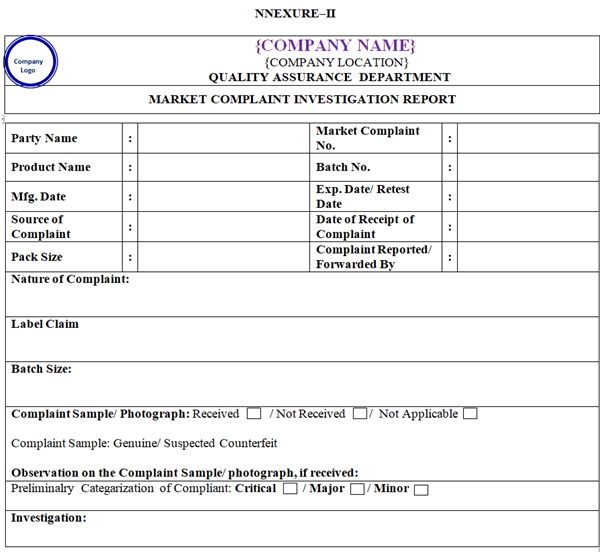
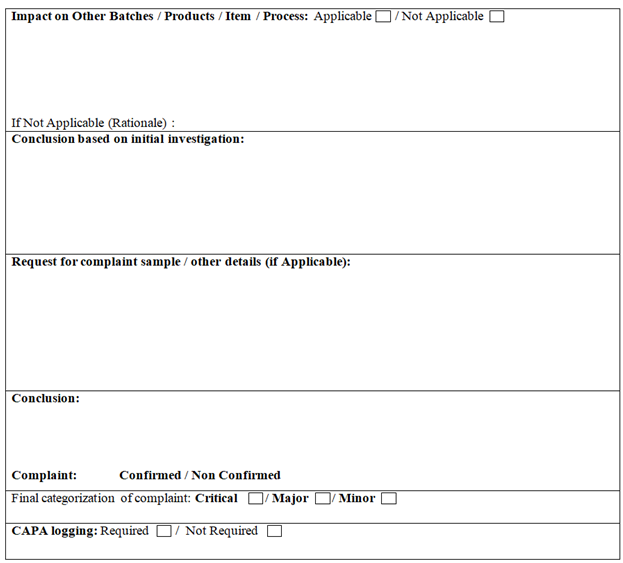
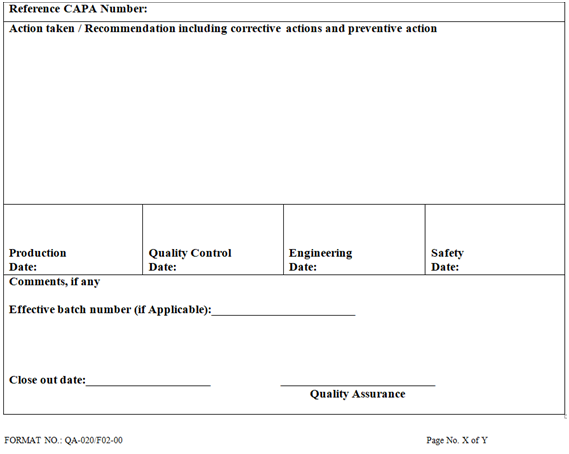
Click the link for download word file copy of this document: https://pharmaguidehub.com/product/handling-of-market-complaints/
ANNEXURE – III
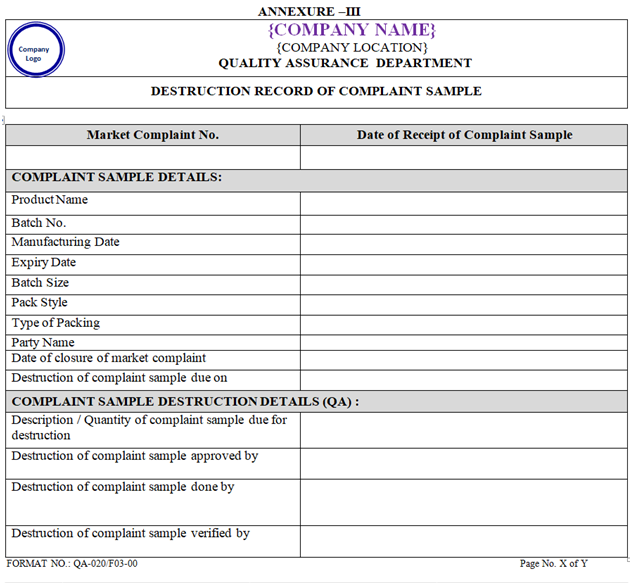
ANNEXURE – IV
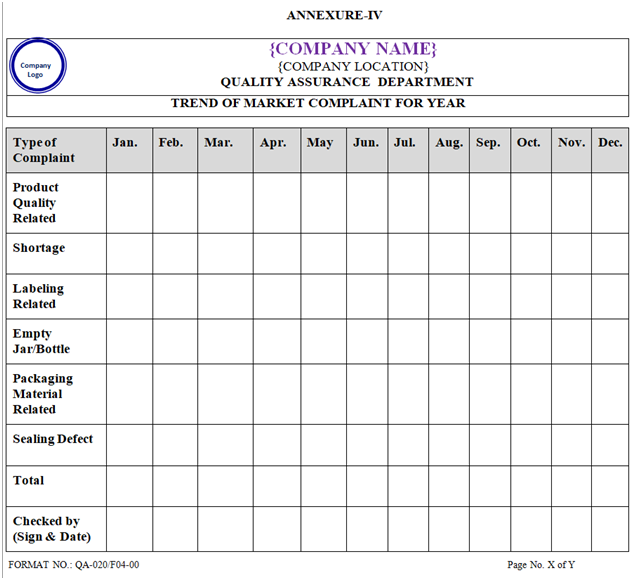
ANNEXURE – V
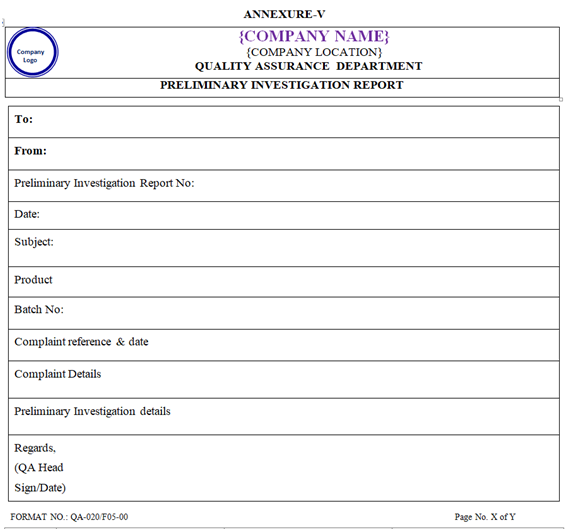
Click the link for download word file copy of this document: https://pharmaguidehub.com/product/handling-of-market-complaints/