- PROCEDURE:
- Instrument Set Up:
- Ensure the calibration status of the instrument before planning the analysis.
- Setup the chromatographic System (HPLC / IC) as per the respective operation SOP’s.Connect the respective HPLC/IC column to chromatographic system.
- Place column storage solvent or recommended solvent reservoir on the system and run the system at the flow rate of 1 mL/min. for about 15 min. to 20 min.
- · Programme the flow rate to increase gradually to 1 mL/minute flow rate.
- Switchover the respective aqueous (For reverse phased chromatographic analysis only) and non-aqueous solvent ratio similar to Mobile phase ratio.
- Procedure to switch over HPLC instrument from Reverse phase to Normal phase:
- Wash the system with water to remove residues of buffers: pump, auto sampler, and detector. Seal wash and needle wash. Use a zero dead volume union.
- Wash with Methanol: minimum of 10 ml should pass through each line A, B, C, D, and through the injector (Purge injector) and through the detector.
- Wash with IPA: minimum of 10 ml should pass through each line A, B, C, D, and through the injector (Purge injector) and through the detector.
- Only after the entire system is flushed with IPA you can introduce the normal phase solvents.
- Procedure to switch over HPLC instrument from Normal phase to Reverse phase:
- Wash the system with Isopropanol; pump, auto sampler, detector, seal wash and needle wash with Isopropanol. Use a zero dead volume union.
- Wash with IPA: minimum of 10 ml should pass through each line A, B, C, D, and through the injector (Purge injector) and through the detector.
- Wash with Methanol: minimum of 10 ml should pass through each line A, B, C, D, and through the injector (Purge injector) and through the detector.
- Wash with water: minimum of 10 ml should pass through each line A, B, C, D, and through the injector (Purge injector) and through the detector.
- Only after the system washed with water it is ready for reversed phase.
- Water, acetonitrile and methanol do not mix with hexane
- Procedure for Issuance and In-house numbering of the GC Column:
- Prepare the mobile phase as per the procedure mentioned in respective work sheets / STP and document it in appropriate work sheets.
- Depending on the number of samples to be analysed, the volume of mobile phase shall be prepared proportionally.
- Gradient grade solvents shall be used wherever recommended for gradient methods.
- In case a mobile phase is prepared prior to receipt of sample (Due to non-availability of work sheet) the preparation details shall be recorded in Format 2 (Mobile Phase Preparation Record). The same shall be recorded in relevant sample work sheets and attach the mobile phase preparation record.
- The mobile phase shall be stored in Glass bottles or as per the recommendations in respective STP / SOP.
- Mobile phase shall be filtered through recommended 0.45 μm filters or as per the method
- Needle wash solution, seal wash solution, or rinsing solution shall be prepared in similar combination of solvents as per the mobile phase recommended in respective STP or SOP.
- The mobile phase container shall be labelled with details of Product / Material, Test, Composition, Prepared by, Prepared on and use before as per format-I.
- The validity period shall be assigned as follows:
- Solutions containing 100% Aqueous Phase: Not More than 2 days from the date of preparation.
- Solutions containing Aqueous Phase and Solvent: Not More than 7 days from the date of preparation subjected to following conditions.
- Mobile phase shall be verified visually before use. If haziness is observed within its validity it shall be discarded.
- Mobile phase shall not be used when elution pattern is not comparable in the same set of analysis.
- Bracketing standard shall comply with the acceptance criteria as per SOP for entire sample set.
- Place the mobile phase bottle, needle wash, seal wash or rinsing solvent on the system.
- Place the correct tubing / channel in the respective bottle.
- Ensure the mobile phase bottles are closed properly to avoid evaporation.
- Ensure all other bottles that do not belong to the current analysis are removed.
- Setting of the Method:
- Analyst shall verify the availability of respective method set in the respective project of chromatographic data system and set the instrument.
- If method set is not avail,
- Method set shall be prepared as per respective Standard Testing Procedure (STP) /Approved Method (as applicable).
- Method set (as applicable) shall be reviewed as per respective Standard Testing Procedure (STP) / Approved Method and it shall be Locked (wherever applicable) in Chromatographic Data system (Applicable for Empower).
- Preparation of Sample set (Sample Sequence):
- Sample set shall be prepared as per respective STP / SOP.
- Typically following sequence shall be followed while preparing the sample set;
- Equilibration
- Conditioning.
- Blank or Diluent.
- System Suitability / Standard solution.
- Placebo solution (As applicable).
- Sample solute.
- Bracketing Standard / System suitability (as applicable).
- If any change to the above sequence shall be justified by the Analyst. The same shall be recorded in the work sheet.
- In sample set, enter Sample Name, Batch Number, Stability Condition / station, vial number, injection Vol (μL), # of Injections, Function, Run Time(Minutes), A.R. Number, Column ID, Level / amounts (as applicable), Next Inject Delay (minutes), any other details as per respective Operating SOP /STP and select corresponding Method Set.
- Print the Instrument method, method set and sample set. Sign with date, attach to first sample worksheet and submit to Reviewer I for review.
- Reviewer I shall review the Instrument method, method set and sample set as per respect standard test procedure / approved procedure, work sheets and sign with date.
- Any errors identified in the sample set during review shall be corrected with suitable comments (Sample set modified based on reviewer observations) in the Chromatographic Data system and same shall be saved.
- Equilibration:
- Run the sample set.
- Equilibrate the system with mobile phase approximately 30 minutes at the flow rate of 1.0 ml/min or as recommended in respective STP.
- Conditioning:
- In continuation to the equilibration the conditioning of the system shall start as per the sample set.
- Condition the system with mobile phase as mentioned below and monitor on the computer.
- In case of ‘isocratic methods’, Conditioning shall be given for about 30 minutes or as per respective STP recommendations.
- In case of ‘gradient methods’, Conditioning shall be given at least one gradient run.
- If the baseline is not satisfactory after conditioning as per the above, alter sample set to include additional conditioning until satisfactory base line is achieved (i.e., free from unwanted noise and un-acceptable peaks / drift).
- Blank and / or Diluent injection:
- Inject blank and / or diluent as mentioned in the STP (if not inject one diluent).
- Blank and / or diluent chromatogram shall have stable base line.
- Blank or diluent chromatogram shall not be considerable if unacceptable drift / extraneous peaks were found.
- If stable baseline is not achieved, alter the sample set, to include additional blank or diluent injection, save the sample set with comments (Additional blank or diluent included to ensure elution pattern) and run the sample set.
- If unacceptable drift / extraneous peaks were found in blank and / or diluent injection even after giving additional Blank and / or diluent injection the section In-charge shall take appropriate action to achieve stable baseline.
- The details of the same shall be mentioned in the comments in Chromatographic Data System.
- Preparation of Analytical Solutions:
- Parallel prepare System Suitability and / or Standard / Placebo (As applicable) / Sample Solutions as per respective standard test procedure / approved procedure.
- During the analysis, if errors are obvious, such as the spilling of a sample solution or the incomplete transfer of a sample composite, the analyst shall immediately document in the respective work sheet and shall be signed by the Reviewer-I.
- Solutions shall be filtered as recommended in the respective standard test procedure / SOP (where ever applicable) and transfer into the HPLC vials.
- All vials shall be identified with solution details and care shall be taken to ensure vials are positioned in correct place as per the sample sequence in system auto sampler.
- System Suitability and Sample analysis:
- Process the system suitability chromatogram with corresponding processing method.
- If the integration of the peaks is not satisfactory the analyst shall amend the processing method and saved with suitable com.
- Same processing method shall be applied for the integration of all the system suitability injections.
- Verify the system suitability parameters as per respective STP.
- Continue the analysis if the system suitability solution meets the Acceptance criteria.
- Handling of System Suitability Failures:
- If the suitability parameters are not meeting the acceptance criteria; then the sample sequence shall be aborted with comments (System suitability not achieved) in CDS and initiate Process Nonconformance as per the SOP.
- Conduct the investigation as per HPLC / IC Investigation check list (Format-III).
- Follow the decision tree as defined in the HPLC/Ion chromatography Analysis Flow chart for further steps;
- If obvious error is identified, correct the error and continue the analysis with next version of sample set after establishing the system suitability.
- If obvious error is not identified, include additional conditioning and repeat the system suitability.
- If analyst is not available, analysis shall be continued by the second analyst.
- If solutions are having stability, use same solutions or else prepare fresh solutions and record all the details of fresh preparations in next copy of the same A.R. No. Worksheet taken.
- After additional conditioning, if system suitability parameters are not met, follow the below.
- Give additional washing / verify the pH of mobile phase, prepare new mobile phase new diluents, condition the column / system followed by repeat analysis and record all the details of preparations in next copy of the same A.R. No. Worksheet.
- If system suitability is not complying disregard the chromatographic data with comments.
- Based on the decision by the In charge QC /Designee, to continue the analysis by using different HPLC or the different column (above all the steps shall be followed) while the investigation is continued.
- The QC in charge/Designee can follow appropriate actions based on the failure/incident.
- Wherever System suitability failures are observed after acquisition of samples, chromatograms shall be processed, printed and investigated as per Format-III.
- Follow the relevant steps in 5.12 to address the failure and actions.
- Handling of unexpected failures due to System:
- In case if sequence is interrupted after initiating the analysis due to any system failures, a Process Non Conformance shall be initiated.
- The following but not limited shall be considered for correcting the failures.
- High pressure: Give washing to the column / system, followed by system suitability.
- Column Leakage: Arrest the leakage, followed by system suitability.
- Communication failures between system and CDS: Establish the communication between system and CDS, followed by system suitability and analysis.
- If system is stopped while gradient is running: System shall be equilibrated with additional gradient run, followed by system suitability and analysis.
- Handling of unexpected variations in Chromatographic run:
- In case if unexpected variations are occurred after initiating the analysis, a Process Non Conformance shall be initiated.
- The following are some of the unexpected variations and action to be considered.
- Retention Time variation / Shift.
- Unstable Base line / humps or drift or noise / Electronic spikes.
- Partially acquired Chromatograms.
- For all such above variations, the chromatograms shall be processed and the data shall be reported in work sheet
- If solution stability exists, the same standard / sample solution from same HPLC vial shall be re-injected after establishing system suitability.
- The re-injected results shall be compared with initial results. If results are comparable, initial chromatographic results shall be ‘DISREGARDED’ and re-injected results shall be considered for reporting of results.
- If re-injected results are not comparable with initial results, an investigation for the variation in the results shall be conducted and shall be concluded accordingly.
- During the analysis, if required to change the priority of analysis or to include any other sample, analyst shall ‘Alter the sample set’, save the sample set with appropriate comments. Printout of the altered sample set shall be reviewed by reviewer – I and run the sample set. Altered sample set shall be attached to the respective work sheet.
- In case if analysis is continued in next shift, second analyst shall prepare new sample set starting with the next vial number of initial sample set. Sample set printout shall be reviewed by reviewer. Line up the new sample set in ‘Run sample set window’ and run the sample set (applicable for Empower software). Attach the printout of sample set to the respective work sheet.
- Whenever sample sequence is completed, to analyse any additional samples; If HPLC setup and column conditioning is not disturbed, analyst shall prepare new sample sequence starting with one bracketing standard followed by samples, Bracketing Standard / system suitability as applicable. In all such cases, the time gap between last bracketing standard of initial sample sequence and beginning bracketing standard of proceeding sequence shall not be more than 4 hours. Make sure the last bracketing standard injection is completed within the solution stability as recommended in STP.
- Processing of chromatograms and Reporting of results:
- Verify the suitability of processing parameters used for processing of standard chromatograms.
- All Standard chromatograms and sample chromatograms shall be processed with the same processing method version number for assay, content of uniformity, dissolution and preservative content tests.
- In case of related substances and chromatographic purity, initial standards and bracketing standards shall be processed with the same processing method version number. Processing method shall be prepared for sample chromatograms based on the elution pattern / peak shape / peak width using integration event given in Empower.
- Sample chromatograms shall be processed after completion of subsequent bracketing standard / system suitability injection as applicable.
- All chromatograms shall be processed in order of acquisition.
- Processing of the chromatograms shall not exceed more than 1 working day from the date of acquisition of last injection in the sample set
- During review of the chromatograms, if selected integration parameters were not found satisfactory, the chromatogram shall be reprocessed or reintegrated with suitable integration parameters. Initial chromatograms shall be DISREGARDED with reasons.
- Typically, manual integration shall not be used for processing of the chromatograms; however manual integration shall only be used if the integration parameters Chromatographic Data System are not suitable for accurate quantification of peak areas. This shall only be performed by the next level personnel (Section in-charge) to analyst.
- Such manual integrations shall be documented with justification and shall be approved by the In-charge QC / designee.
- Chromatograms shall be signed off electronically by the analyst and reviewer (Wherever electronic signatures are implemented). Print the chromatograms.
- Chromatograms generated from Empower software shall have the following details:
- Header of Chromatogram:
- Empower logo
- Organization name and department
- Report template name
- Sample Information Table:
- Instrument name
- Column ID
- A.R. No. (If Any)
- Sample description
- Sample set Name
- Acquired by
- Acquired Method set
- Instrument method
- Processing Method
- Proc. Chnl Descr
- Chromatogram:
- Peak
- Appropriate scale (All peaks shall be clearly visible). Zoomed chromatogram of particular section of main chromatogram shall also be taken if peaks of interest are very closely eluted and not visible
- Legend of Chromatogram:
- Sample Name
- Vial Number
- Injection volume
- Injection number
- Date Acquired
- Date Processed
- Peak Results:
- Vial
- Injection No.
- Sample description
- Sample name
- Name of Peak
- Retention Time (min)
- Area (μV*sec)
- Integration type
- Required System suitable parameters
- Sum, Average (If any)
- Area%(In case of Chromatographic purity)
- Footer of Chromatogram:
- Report Method Name
- Printed Time and Date
- Page Number
- Project name
- All processed chromatograms shall be printed and E-signature of analyst and reviewer.
- After reviewing and E-signature of the processed chromatograms, the reviewer/group leader shall be locked each processed result of the chromatogram.
- Analyst shall print ‘audit trail brief report’ for each sample set.Audit trail report generated from Empower software shall have the following details.
- Header:
- Empower logo
- Organization name and department
- Report template name
- Sample Information Table:
- Instrument name
- Sample set name
- Column ID
- Acquired by
- Injection volume
- Acquired Method set
- Instrument method ID
- Proc. Chnl Descr
- Component Summary Table:
- Sample name
- Vial
- Injection no
- Integration type
- # of Results Stored
- Altered
- Processing Method Id
- Processing locked
- Footer of Chromatogram:
- Report Method Name
- Printed Time and Date
- Page Number
- Project name
- The reviewer shall verify the ‘audit trail brief report’ for each sample set to know the history of sample sequence.
- Attach the chromatograms with respective work sheet.
- Report the data in work sheet.
- Print and sign the Processing method, Completed Sample set with date and attach with 1streport of the sample set or respective work sheet.
- In the absence of the acquired analyst, second analyst shall process the chromatograms and report the data after transferring test from 1st analyst to second analyst.
- All affected chromatograms shall be disregarded by stamping as “DISREGARDED” with signature and indicating the reason for disregarding. Such chromatograms shall be attached along with the report and same shall be verified by the reviewer.
- Chromatographic data shall be reviewed as per respective SOP.
- Respective Logbook entries shall be made while performing the respective activity.
- After completion of analysis, column shall be washed with appropriate solution for a minimum of 30 minutes or as per the recommendations of STP/approved procedure.
- Store the column as per the recommendations in STP or by manufacturer or as appropriate solvents.
- Complete the investigation with final conclusions and corrective actions in Format-III.
- QC In-charge / Manager shall review the investigation report, corrective actions taken, proposed preventive actions and submit the PNC.
- Head-QA / Designee shall evaluate the final conclusions and approve the PNC.
- All chromatographic PNC’s shall be trend quarterly to identify the recurring PNC’s.
- ANNEXURES:
ANNEXURE NO. | TITLE OF ANNEXURE |
Annexure-I | Mobile Phase Container Label |
Annexure-II | Mobile Phase Preparation Record |
Annexure-III | Liquid Chromatography Investigation Check List |
Annexure-I
MOBILE PHASE CONTAINER LABEL
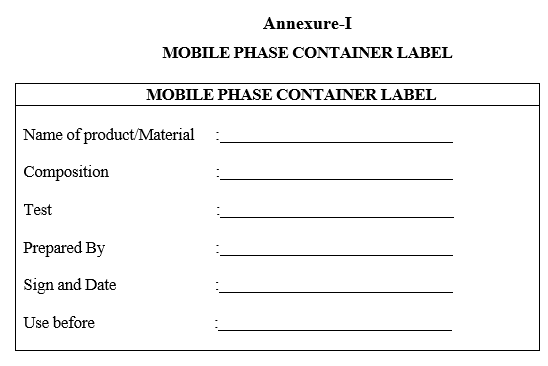
Annexure-II
MOBILE PHASE PREPARATION RECORD
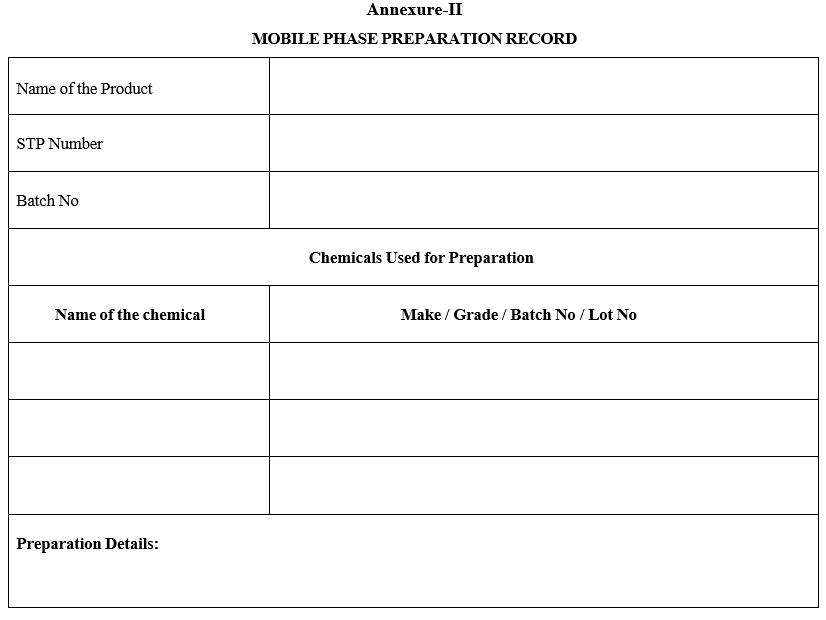
Annexure-III
LIQUID CHROMATOGRAPHY INVESTIGATION CHECK LIST
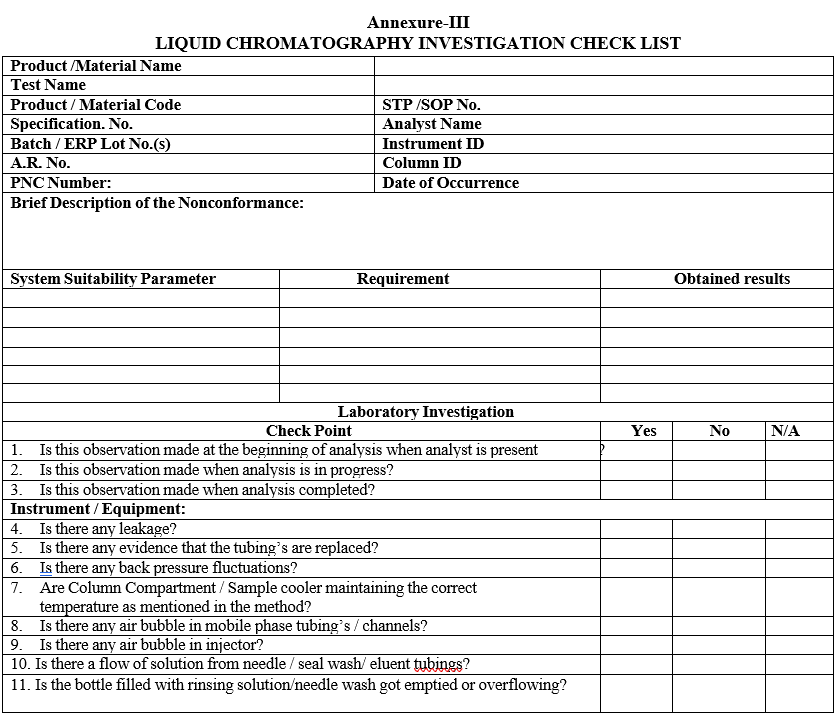
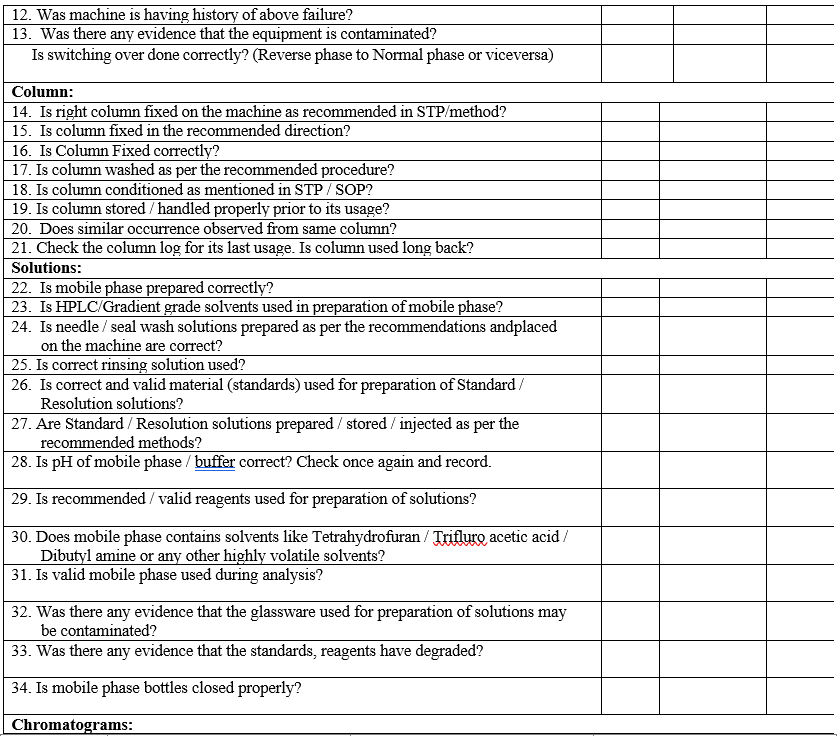
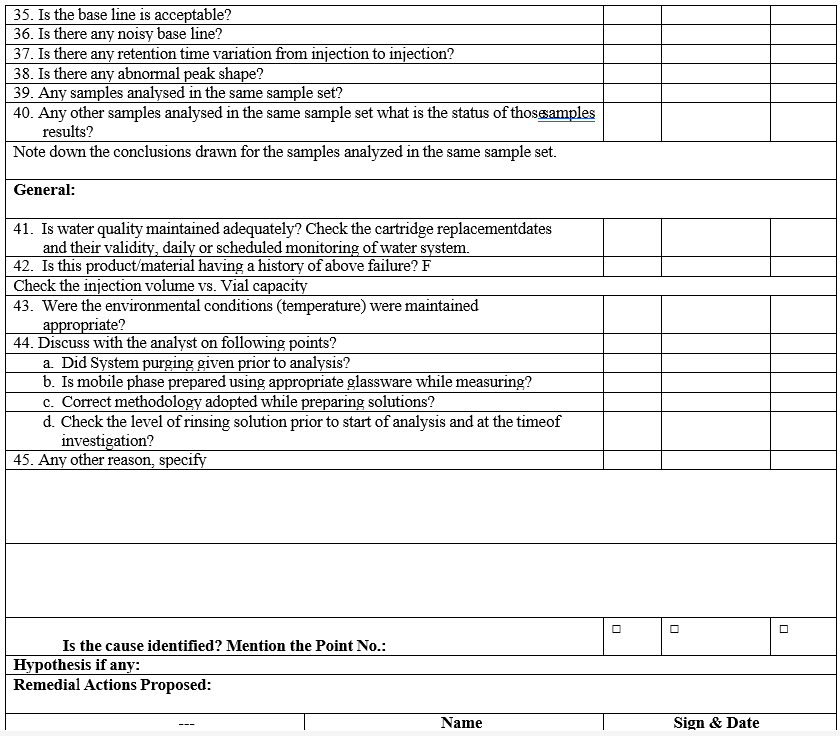
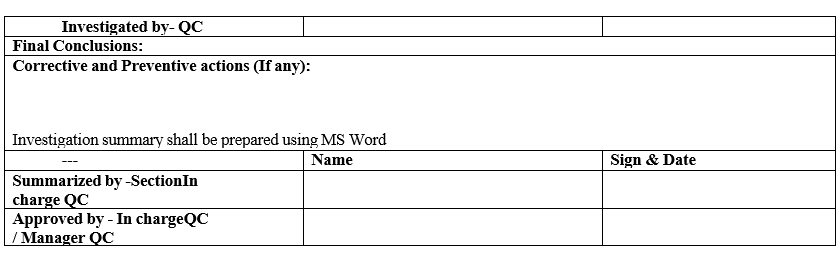