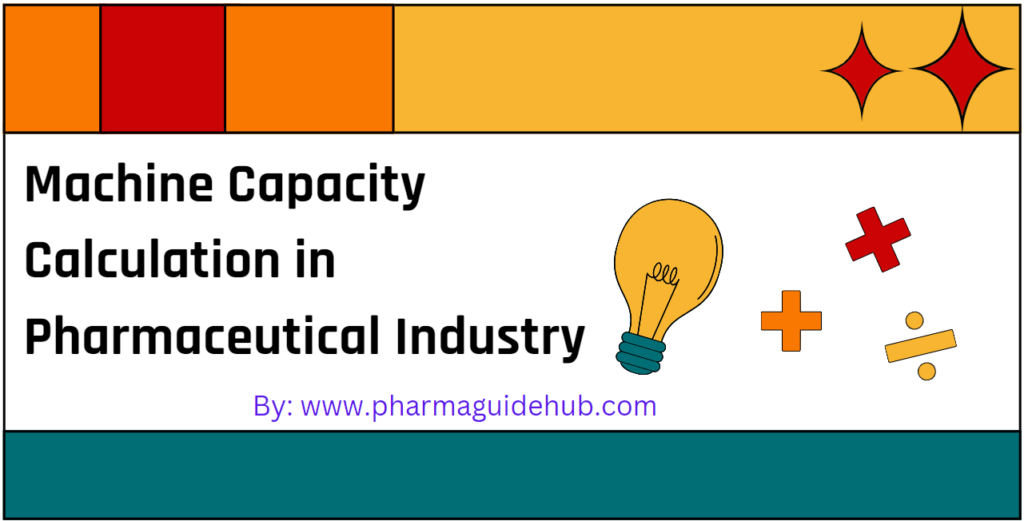
Machine capacity refers to the maximum amount of product a machine can produce within a specific time frame. In the pharmaceutical industry, accurate capacity calculations are crucial for production planning, resource allocation, and ensuring compliance with regulatory standards.
Factors Affecting Machine Capacity:
Maintenance and Calibration: Regular maintenance and calibration ensure optimal machine operation and prevent downtime.
Machine Design and Specifications: The inherent capabilities of the machine, such as its size, power, and speed, determine its maximum output.
Product Characteristics: The physical properties of the product, including its density, flowability, and particle size, can influence processing time and efficiency.
Operating Conditions: Factors like temperature, humidity, and pressure can affect machine performance.
Calculation Methods:
- Theoretical Capacity: Based on the machine’s design specifications and operating parameters, this calculation provides an ideal maximum output.
- Actual Capacity: Determined through real-world testing, considering factors like product characteristics and operating conditions. This value is often lower than the theoretical capacity due to inefficiencies and losses.
- Effective Capacity: Accounts for downtime due to maintenance, cleaning, and other factors. It represents the actual output that can be achieved under typical operating conditions.
Common Capacity Calculation Formulas:
Capacity = Feed Rate * Operating Time
For Batch Processes:
Capacity = (Batch Size / Cycle Time) * Number of Cycles per Day
For Continuous Processes:
Capacity = Feed Rate * Operating Time
Evalution of machine capacity:
To determine the capacity in kg, the volume of the machine and density of a powder are to be measured and then multiplied by liters. Capacity in terms of liters remains fixed but in kgs varies depending upon the density of powder.
For maximum capacity, usually 60–70% of the machine is considered and results are to be validated. For minimum capacity, usually 30-40% of machines are considered, and results are to be validated.
For Rapid Mixer Granulator
Maximum Machine Capacity Calculation
Determine capacity in terms of liters, for this add measured volume water in RMG.
Say it is 500 liters,
If density of powder is 0.75; then the volume of RMG will be 500×0.75=375 kg,
Now, 70% of it is = 375×70/100 = 262.50 kg,
So, the maximum capacity of RMG is 262.50 kg.
Minimum Machine Capacity Calculation
Determine capacity in term of liters, for this add measured volume water in RMG.
Say it is 500 liters,
If density of powder is 0.75; then the volume of RMG will be 500×0.75=375 kg,
Now, 40% of it is = 375×40/100 = 150.00 kg,
So, the minimum capacity of RMG is 150.00 kg.
For Coating Pan Capacity Calculation
Maximum capacity of the pan is calculated by the brim volume and the bulk density of the tablets.
Thus, Maximum Capacity of Coating Pan = Brim volume of pan (ltrs) x Bulk density of tablets (g/ml)
Let,
Brim volume = 300 ltrs.
Bulk density of tablets = 0.72 g/ml
Maximum capacity of coating pan = 300 x 0.72 = 216.0 Kg
If 60% of the maximum capacity is the minimum capacity of coating pan.
Minimum capacity of coating pan = 216.0 × 60% = 129.6 kg
Thus, Maximum Capacity of Coating Pan = Brim volume of pan (ltrs) x Bulk density of tablets (g/ml)
Let,
Brim volume = 300 ltrs.
Bulk density of tablets = 0.72 g/ml
Maximum capacity of coating pan = 300 x 0.72 = 216.0 Kg
If 60% of the maximum capacity is the minimum capacity of coating pan.
Minimum capacity of coating pan = 216.0 × 60% = 129.6 kg
Note:
Bulk density depends on the tablet shape and size.
The coating pan’s brim volume determines the coating machine’s operational capacity.