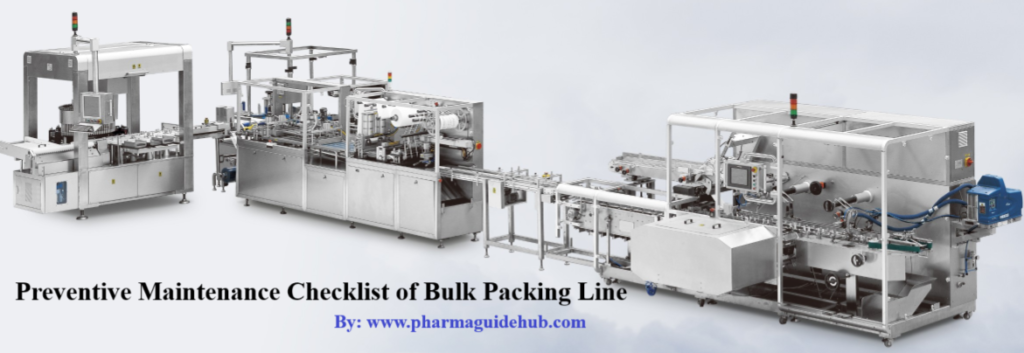
A Bulk Packing Line is a specialized production line designed for the efficient packaging of large quantities of pharmaceutical products. The term “200 BPM” refers to the line’s capacity to process 200 bottles per minute.
These lines typically involve several stages, including:
Cartoning: The labeled containers are placed into cartons for secondary packaging.
Product Infeed: The pharmaceutical products, such as tablets, capsules, or powders, are fed into the line from bulk containers.
Counting and Filling: The products are counted accurately and filled into appropriate containers, such as bottles or blister packs.
Inspection: Quality control measures are implemented to ensure that the filled containers meet the required specifications.
Labeling: The containers are labeled with necessary information, including product name, dosage, and expiration date.
Department: Engineering Equipment Name: Bulk Packing Line (Pharma Pack 200BPM) Equip. No./ID: Frequency: Half Yearly |
S. No | Check Points | Procedure | Activity | Done By / Date |
UNSCRAMBLER | ||||
1 | Check the wear and tear of the rollers. | Physical check the condition of rollers for damage, if observed replace it. | ||
2 | Check the condition of feeding and washer belt and out feed belt. | Physical check the condition of all belts for abnormality, if observed replace the belts. | ||
3 | Check the condition of vacuum filter if necessary. | Physical check the condition of vacuum filters for abnormality, if observed replace the belts. | ||
4 | Check the condition of all the relays. | Check the working condition of all the relays by operating the functions, if not found properly, replace it. | ||
5 | Check the condition of air filter. | Physical check the condition of air filter for choke, if observed clean/replace it. | ||
6 | Check the condition of the love joy coupling, replace if necessary. | Check the love joy coupling by rotating the motor. If any damage observed, replace it. | ||
7 | Check the working condition of solenoid valves. | Check the working condition of solenoid valves. If required, lubricate it. | ||
8 | Check the all electrical connections. | Check and tight electrical terminals by using the proper tools and check the voltages and earth connections with multi meter. | ||
SACHET DESICANT INSERTER | ||||
1 | Check the seal kit for pneumatic cylinder, replace if required. | Physically check the condition of the seal kit, If required, replace it. | ||
2 | Check the contactor kits clean/replace if required. | Check the working condition of contractor kit. If required, clean with CRC/ replace it. | ||
3 | Check all the safety interlocks working condition. | Run the machine and check the interlocks by open one by one and check for alarm and machine stoppage, if not check the wiring. | ||
4 | Check all indication lamps replace them if necessary. | Check the working condition of all the indication lamps for glow, if not check the connections/ replace. | ||
COUNTING MACHINE | ||||
1 | Check the condition of emitter and receivers. | Check the working condition of emitter and receiver, if required replace it. | ||
2 | Check all the push buttons and emergency button, replace if required. | Check the working condition of push buttons and emergency button for operating the machine. If not found properly, replace it. | ||
3 | Check the all proximity and optical sensors. | Check the working condition of proximity and optical sensor by passing the bottle, if not found properly replace it. | ||
4 | Check the condition of vibrating plates. | Physical check the condition of vibrating plates, if not found properly replace it. | ||
CHECKWEIGHER | ||||
1 | Check and lubricate the transporting/conveyor roller bearings, replace if necessary. | Check the working condition of transporting conveyer and check the roller bearing condition required, lubricate/replace if required. | ||
2 | Check the condition and tension of the toothed belt drive, replace if required. | Check the working condition of toothed belt drive and check the tension of the belt. If required, replace it. | ||
3 | Check the leveling of machine, leveled if required. | Check the levelling of machine with spirit level by operating adjustment port. | ||
4 | Check the all electrical terminals. | Check and tight electrical terminals by using the proper tools and check the voltages and earth connections with multimeter. | ||
5 | Check the Working condition of pneumatic cylinder for rejection. | Physically check the condition of pneumatic cylinder and check the working condition at machine time. If required, lubricate/replace it. | ||
COTTON INSERTER | ||||
1 | Replace the timing belts if required. | Physically check the condition and tension of timing belt and check the alignment of pullys. If required, replace it. | ||
2 | Check the seal kit for pneumatic cylinder, replace if required. | Physically check the condition of the seal kit, If required, replace it. | ||
3 | Check the all sensors working conditions. | Check the working condition of all sensors by operating the function through HMI and clean with dry cloth. | ||
ROTARY SCREW ON CAPPER | ||||
1 | Check the condition of Spindle movement mechanism. | Run the machine in Manual/Auto mode. Check the movement of spindle and open the door and check the bearing condition of spindle. | ||
2 | Replace the bearings if necessary. | Run the machine and observe for abnormal sound, if observed replace/lubricate the bearing. | ||
3 | Check the condition of cam followers. | Physical check the condition of cam followers for abnormality, if observed replace it. | ||
4 | Check the all electrical terminals. | Check and tighten electrical terminals by using the proper tools and check the voltages and earth connections with multi meter. | ||
5 | Check the condition of cap elevator running. | Check the physical movement of cap elevator in running condition and check the bearing and screws. If required, replace/lubricate. | ||
INDUCTION SEALER | ||||
1 | Check the seal kit for pneumatic cylinder, replace if required. | Physically check the condition of seal kit for pneumatic cylinder, replace if required. | ||
2 | Check if any abnormal sound from machine. | Run the machine in Manual /Auto mode and observe for abnormal sound, if observed lubricate. | ||
3 | Check the functioning of the sensors. | Check the working condition of sensors by operating the function through HMI and clean with dry cloth, if required replaces the sensors. | ||
4 | Check the functioning of hot air fan. | Check the working condition of hot air fan in running condition and check the connection and physical condition of fan. If required, replace it. | ||
RETORQUER | ||||
1 | Replace the gripper belt if necessary. | Check the physical condition of gripper belt. If required, replace it. | ||
2 | Replace the synchronous belt if necessary. | Check the physical condition of synchronous belt and check the tension of the belt. If required, replace it. | ||
3 | Clean the electrical panel with vacuum cleaner. | Check the electrical panel. Clean the electrical panel with vacuum cleaner. | ||
4 | Check the functioning of the solenoid coil. | Check the working condition of solenoid coil by operating the functions. If required, replace it. | ||
5 | Check the condition of torque sensor. | Check the working condition of torque sensor. If required, replace it. | ||
LABELING MACHINE | ||||
1 | Check and replace seal kit for pneumatic | Check the physical condition of seal kit for pneumatic | ||
cylinder if required. | cylinder. If required, replace it. | |||
2 | Replace the bearing if necessary. | Check the physical condition of the bearing. If required, lubricate/replace it. | ||
3 | Replace the driving gear if necessary. | Check the physical condition of driving gear and check the bearing condition. If required, replace it. | ||
4 | Check the condition of hot stamping unit. | Check the working condition of hot stamping unit and check the cylinder. If required, replace it. | ||
5 | Check the condition of all safety switches and sensors. | Check the sensors working condition by operating machine. If any sensor not found properly, replace it. | ||
LEAFLET OUTSERTER | ||||
1 | Check all functioning of all solenoid valves. | Check the working of solenoid valves. If required, lubricate it | ||
2 | Check and service the vacuum pump, if necessary. | Check the physical condition of vacuum pump. If required, service it. | ||
3 | Replace the filter in vacuum pump, if necessary. | Check the physical condition of filter. If required, replace it. | ||
4 | Check the ‘O-ring of filter unit, replace if necessary. | Check the physical condition of “O” of ring filter. If required, replace it. | ||
5 | Check the condition of suction cup bellows, replace if necessary. | Check the condition of suction cup bellows. If required, replace it. | ||
6 | Service the glue head. | Check the physical condition of glue head. If required, service it. | ||
7 | Check the sensor and bottle head. | Check the sensor condition by passing the bottle through bottle head. If not function properly, replace it. | ||
GENERAL CHECK POINTS | ||||
1 | Check the contactor kits clean/replace if required. | Check the working condition of contractor by operating the contractor and clean the contractor kit. If required, replace it. | ||
2 | Check all the safety interlocks working condition. | Check the working condition of all the safety interlocks by operating the interlocks one by one and observe the condition in HMI. | ||
3 | Check all indication lamps replace them if necessary. | Check the working condition of all indication lamps by operating the machine. If required, replace it. | ||
4 | Check and tighten all electrical terminals. | Check and tighten electrical terminals by using the proper tools and check the voltages and earth connections with multimeter. | ||
5 | Check the condition of pressure gauges. | Apply the air to pressure gauges and observe the pressure indication in pressure gauges. | ||
6 | Check all the push buttons and emergency button, replace if required. | Check the push buttons and emergency button condition to operate the machine. If required, replace it. | ||
7 | Clean the electrical panel with vacuum cleaner. | Open the electrical panel and clean the vacuum cleaner. | ||
Remarks: Checked By / Date |