- OBJECTIVE:
To lay down a procedure for perform the predetermined Preventive maintenance of Equipment’s.
- SCOPE:
This SOP is applicable for perform the predetermined Preventive maintenance of Equipment’s at {Company Name} {Company Location}.
- RESPONSIBILITY:
- Technical Assistant of Engineering / User department is responsible to carry out the Preventive Maintenance of the equipments.
- Executive- Engineering/QC department shall be responsible to prepare the Annual Preventive maintenance schedule.
- Head/Designee – Engineering, QC and QA shall ensure compliance with respect to the SOP.
- ACCOUNTABILITY:
Engineering Head
Head Quality Assurance
- PROCEDURE:
- Preparation of Preventive Maintenance Programme:Preventive Maintenance procedure shall be followed to ensure the smooth and safe operation of Equipments.
- During the qualification (IQ) of any equipment/instruments, Preventive Maintenance procedure (check list) shall be initiated.
- A draft copy of prepared for each and every equipment as per Annexure-I.
- The adequacy of same shall be verified during operational qualification (OQ).
- If the PMP is found complete and adequate during OQ, the same shall be approved and made effective after imparting necessary training.
- If any changes are suggested during OQ, the same shall be incorporated and final copy shall be taken before initiation of Performance qualification (PQ).
- During the operational qualification of the equipment all the preventive maintenance check list associated with that particular equipment shall be prepared and attached with the qualification documents.
- Personnel understand and follow PMP description and requirements and whether PMP provided adequate direction and control to ensures a uniform operation.
- Master Scheduling:
- Preventive maintenance procedures and schedules are generally based on the manufacturer’s recommendation, experience, and Engineering judgment. The schedules are categorized into fortnightly (F), Monthly (M), Quarterly (Q), Half- yearly (H), Yearly (Y) and also based on the equipment running hours.
- All equipments shall be categorised into three main categories based on the risk to the product.
- Direct Impact Equipment/Systems (D.I): Equipment/System whose failure shall have direct product quality impact.
- Indirect Impact Equipments/Systems (I.I): Those are process critical, failure of these has a direct impact on the process/System performance hence have an in direct effect on the quality of product.
- No Impact Equipments/Systems (N.I): which have no effect on product quality.
- The Engineering/User department shall prepare a master schedule of the preventive maintenance programme at the start of the year for all the equipment as per Annexure-II.
- If any new equipment is installed & qualified, the yearly preventive maintenance schedule for particular equipment shall be added & further recorded in the Annexure-V.
- Head/Designee -QA shall approve the yearly Master schedule for preventive maintenance of equipment.
- Documents ControlApproved PMP check list or master schedule shall be kept in QA Documentation.
- As per the preventive maintenance programme, a copy of the schedule for all equipment shall be given to the user department.
- The production department should give the clearance for PMP on or before the grace period.Annexure-V shall be maintained with the User Department till that year closure.
- Grace Period & Deviation
- The frequency of Preventive Maintenance program based on the categories of equipment/Systems is given below.
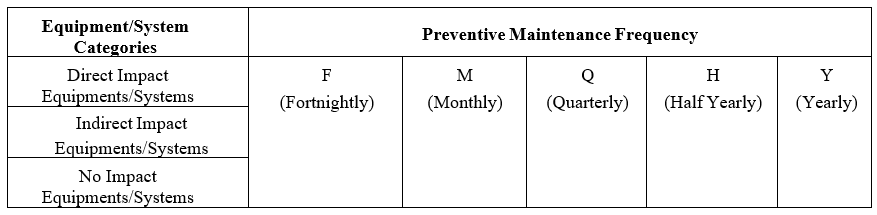
Note: Preventive maintenance of all direct impact equipment/System shall be performed ± 4 days, Indirect Impact Equipments/Systems PM shall be performed ±7 days from the PM due date and No Impact Equipments/Systems PM shall be performed ± 15 days from the PM due dates.
- If preventive maintenance is not performed within the grace period PNC (Process Non-Conformance) shall be raised as per the respective SOP same can be performed immediately after the approval of the PNC, and the same shall be mentioned in Remarks column of PMP check list.
- If the preventive maintenance cannot be taken up due to equipment breakdown/equipment or facility modification/equipment non-availability, then the User/Engineering department shall raise the Exception as per the respective SOP the same can be performed immediately after the completion of the production activity based on the Exception and the same shall be mentioned in remarks column of PMP check list.
- If any equipment is scheduled for preventive maintenance and is not in use from its last preventive maintenance, preventive maintenance need not be performed, and comments shall be written in Remarks Column of PMP check list and perform the PMP before starting the production activity.
- Revision of Preventive Maintenance Schedule
- In case incident occur (≥ 3 times) due to the same problem then the preventive maintenance schedule and PMP check list may be revised. Changes made shall be addressed through a change control procedure as respective SOP.
- If any change in PMP check list the same shall be revised as per respective SOP need not be revised.
- If any equipment discontinues from it use, the PMP schedule and check list on that particular equipment shall be cancelled and reason for the same shall be written in the remark column of Check list and Equipment Log sheet.
- However before discontinuing, PMP shall be carried on that equipment to ensure that equipment was in proper condition.
- Execution of Preventive Maintenance
- Engineering/concerned personnel shall ensure the equipment clearance as per PMP schedule.
- Preventive maintenance activities shall be carried out as per Annexure-I by Technical Assistant/Executive and the checking shall be done by second Executive/ second technical assistant.
- If any components worn-out, cracks, etc., observed those things shall be Replaced/rectified and same shall be recorded in Equipment History Log (Annexure-II).
- During the preventive maintenance the equipment shall be labelled as“ UNDER PREVENTIVE MAINTENANCE”, . Any Equipment labelled with “Under Preventive maintenance” shall not be used.
- After completion of PMP, “PREVENTIVE MAINTENANCE STATUS LABEL”, shall be updated.
- REFERENCES:
Not Applicable
- ANNEXURES:
ANNEXURE No. | TITLE OF ANNEXURE |
Annexure-I | Preventive Maintenance Check list |
Annexure-II | Master schedule for preventive maintenance of equipment |
Annexure-III | Under Preventive Maintenance Label |
Annexure-IV | Preventive Maintenance Status Label |
Annexure-V | Master schedule for preventive maintenance of add on equipment |
ENCLOSURES: SOP Training Record.
- DISTRIBUTION:
- Controlled Copy No. 01 Head Quality Assurance
- Controlled Copy No. 02 Head-Engineering
- Master Copy Quality Assurance Department
- ABBREVIATIONS:
SOP : Standard Operating Procedure.
PMP : Preventive Maintenance Programme
PNC : Process Non Conformance
QC : Quality Control
QA : Quality Assurance
- REVISION HISTORY:
CHANGE HISTORY LOG
Revision No. | Details of Changes | Reason for Change | Effective Date |
00 | New SOP | Not Applicable | To be written manual |
ANNEXURE-I
PREVENTIVE MAINTENANCE CHECK LIST
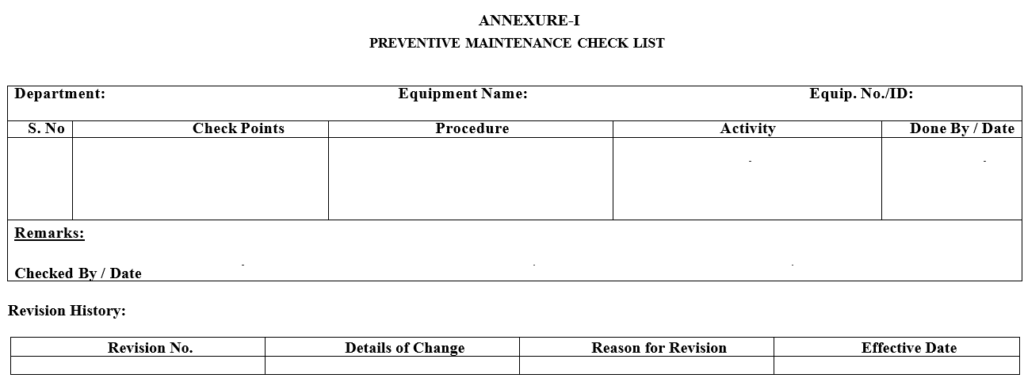
ANNEXURE-II
MASTER SCHEDULE FOR PREVENTIVE MAINTENANCE OF EQUIPMENT
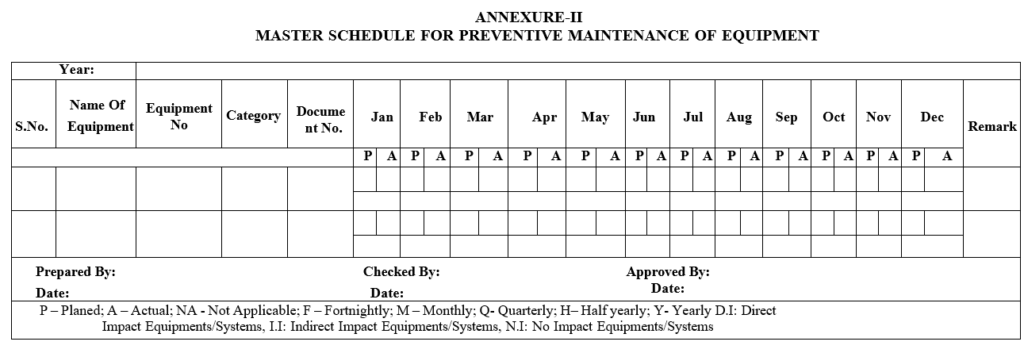
ANNEXURE-III
UNDER PREVENTIVE MAINTENANCE LABEL

ANNEXURE-IV
PREVENTIVE MAINTENANCE STATUS LABEL
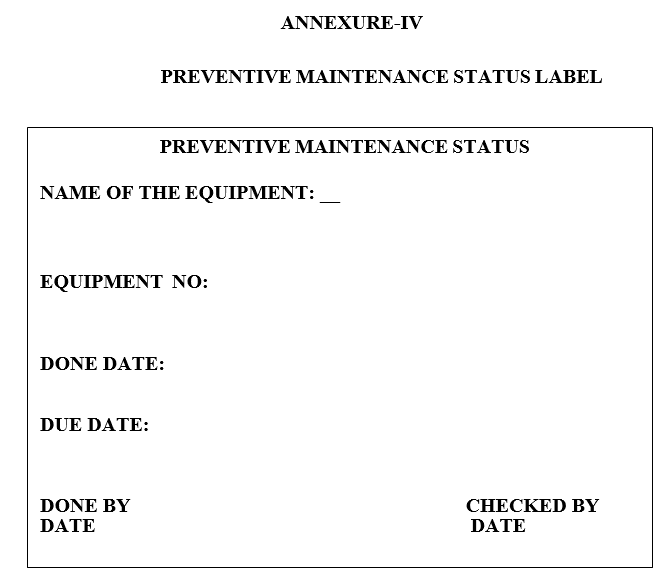
ANNEXURE-V
MASTER SCHEDULE FOR PREVENTIVE MAINTENANCE OF ADD ON EQUIPMENT
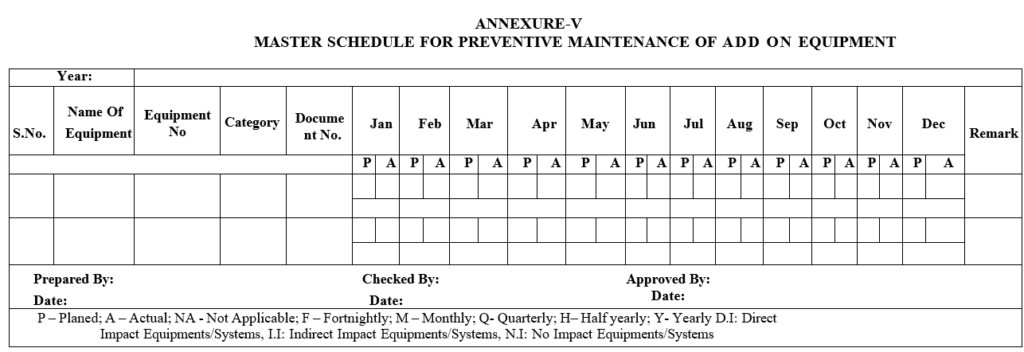
Frequently Asked Question?
1. What is the purpose of the Preventive Maintenance Programme (PMP)?
The PMP aims to ensure the smooth and safe operation of equipment by preventing unexpected failures through regular maintenance activities.
2. How is the PMP established?
- During equipment qualification, a draft PMP checklist is created for each piece of equipment.
- The adequacy of the checklist is verified during operational qualification. If necessary, changes are incorporated before finalizing the PMP.
- The final PMP checklist is attached to the qualification documents.
3. How are maintenance schedules determined?
- Schedules are based on manufacturer recommendations, experience, and engineering judgment.
- They are categorized by frequency (fortnightly, monthly, etc.) and running hours.
- Equipment is further categorized based on its impact on product quality:
- Direct Impact (D.I.): Equipment failure directly affects product quality.
- Indirect Impact (I.I.): Equipment failure impacts process performance, indirectly affecting product quality.
- No Impact (N.I.): Equipment failure has no impact on product quality.
4. Who is responsible for the PMP?
- The Engineering/User department prepares the yearly master schedule for all equipment.
- The Head/Designee-QA approves the yearly master schedule.
- Approved PMP checklists and master schedules are kept in QA documentation.
- Copies of the schedule are provided to the user department for execution.
5. What happens if preventive maintenance is not performed on time?
- A grace period is provided for each equipment category (D.I., I.I., N.I.).
- If maintenance is not performed within the grace period, a Process Non-Conformance (PNC) is raised.
- Exceptions can be raised if equipment breakdown, modification, or non-availability prevents maintenance.
- If unused equipment is scheduled for maintenance, it can be skipped with comments recorded.
6. How is the PMP revised?
- The schedule and checklist may be revised if the same equipment failure occurs three or more times.
- Changes are implemented through a change control procedure.
- If equipment is discontinued, the PMP and checklist are cancelled with reason documented.
7. Who executes the preventive maintenance?
- Engineering/concerned personnel ensure equipment clearance for maintenance.
- Technical Assistants/Executives perform maintenance activities based on the checklist.
- A second individual verifies the completed work.
8. What happens during preventive maintenance?
- Worn-out components or defects are identified and addressed.
- The equipment is labelled “UNDER PREVENTIVE MAINTENANCE” while work is ongoing.
- Upon completion, a “PREVENTIVE MAINTENANCE STATUS LABEL” is updated.