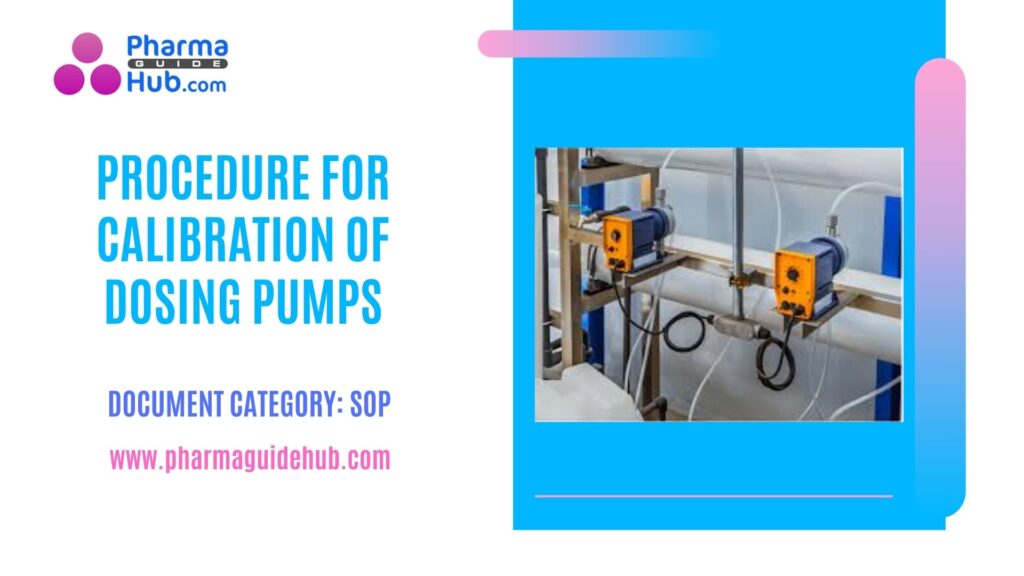
OBJECTIVE:
To lay down a procedure for Calibration of Calibration of Dosing pumps.
SCOPE:
This SOP is applicable to the procedure for Calibration of Calibration of Dosing pumps at {Company Name} {Location}.
RESPONSIBILITY:
Officer/Executive/Designee: shall be responsible for following the procedure as per SOP.
Engineering Head/designee is responsible for compliance of SOP.
ACCOUNTABILITY:
QA Head shall be Accountable for implementation of SOP.
Dosing Pump and their Key Features:
Dosing pumps, also known as metering pumps, are crucial equipment in the pharmaceutical industry. They are used to precisely control the flow rate of fluids, ensuring accurate and consistent dosing of chemicals, solutions, and other substances.
Key features and benefits of dosing pumps in pharma:
Precision: Dosing pumps offer exceptional accuracy and control over fluid flow rates, allowing for precise dosing of even small volumes.
Reliability: They are designed for continuous operation, ensuring consistent performance and minimal downtime.
Versatility: Dosing pumps can handle a wide range of fluids, including corrosive and viscous substances, making them suitable for various pharmaceutical applications.
Safety: They often come with features like leak detection and automatic shut-off mechanisms, enhancing safety in the production environment.
PROCEDURE:
Dosing pumps shall be calibrated by measuring the output quantity of solution in particular time at different % of flow shown on the pump.
Before starting the calibration keep ready calibrated timer and measuring cylinder.
Stop the Pre-treatment, RO-1 and UV-1 system before starting of the calibration of the dosing pumps.
Stop the Dosing pump by operating the Switch ON/OFF and labelled as under calibration.
Disconnect the discharge pipe from the Service line.
Set the % of flow at 100 and start the dosing pump by operating the Switch ON/OFF.
Start the timer and kept the discharge in measuring cylinder.
After 10 minutes stop the pump and record the result. Accordingly calculate the capacity for 1 hour. This shall be considered as 100% capacity of the pump.
Perform the calibration at 25%, 50% and 75% of flow and compare the results with the specifications according to the % of flow.
If the results are with in the limit of ± 5 %, pump is used for the operation.
If the results are out of limit, diaphragm of the pump shall be changed and calibration is performed.
Even though after changing the diaphragm it is not performing, the pump shall be changed and calibration performed.
After calibration completion it is labelled as calibrated. If it fails, labelled as calibration Failed.
Switch ON the dosing pumps and start the UF-1 and RO system.
The calibration of dosing pumps shall be carried out for quarterly as per the SOP.
Record the dosing pumps calibration details as per Format-I.
REFERENCES:
Not Applicable
ANNEXURES:
ANNEXURE NO. | TITLE OF ANNEXURE |
Annexure-I | Dosing pumps Calibration Record |
ENCLOSURES: SOP Training Record.
DISTRIBUTION:
Controlled Copy No. 01 : Head Quality Assurance
Controlled Copy No. 02 : Head Engineering
Master Copy : Quality Assurance Department
ABBREVIATIONS:
No. | : | Number |
UF | : | Ultra Filtration |
RO | : | Reverse Osmosis |
SOP | : | Standard Operating Procedure |
REVISION HISTORY:
CHANGE HISTORY LOG
Revision No. | Details of Changes | Reason for Change | Effective Date |
00 | New SOP | Not Applicable | To Be Written Manual |
Annexure-I
DOSING PUMPS CALIBRATION RECORD
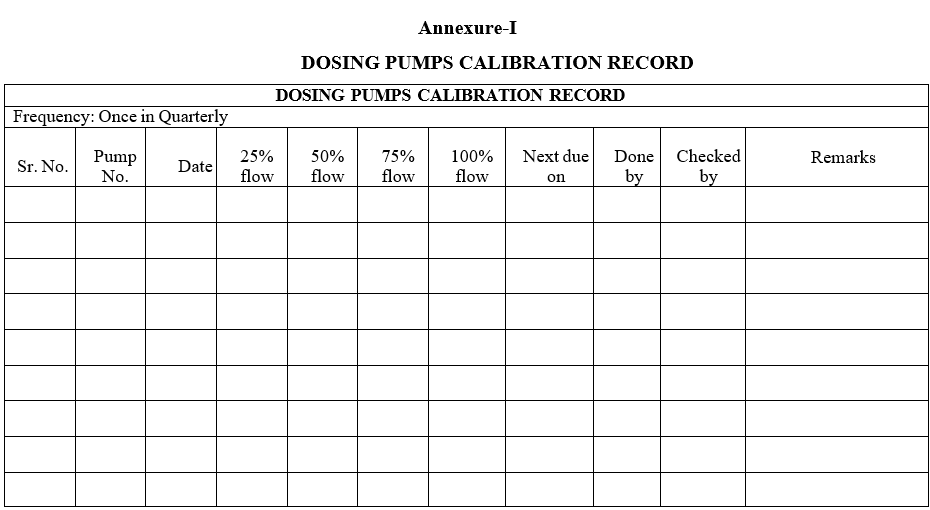