- OBJECTIVE:
To define the requirements for effective measurement, assessment and reporting of the Quality performance/Quality Risk Levels using Quality Indicators/Indices.
- SCOPE:
This procedure is applicable for Quality performance review at {Company Name} {Location}.
- RESPONSIBILITY:
- QA In-Charge/ Designee shall be responsible for:
- Collection of data related to Quality Systems in prescribed format.
- Evaluate the Quality Risk and to present the data in Quality Review Meetings (QRM).
- Propose Corrective Actions in co-ordination with the respective departments.
- Ensure the effective implementation of CAPA to reduce the Quality Risk.
- Final disposition of the Risk status as High for specific Quality indices for any specific/special cause
- Head QA/PD/DesigneeFinal:
- Disposition of the Risk status as High for specific Quality indices for any specific/special cause.
- Review the performance and provide necessary support, wherever required.
- ACCOUNTABILITY:
QA Head shall be Accountable for implementation of SOP.
- PROCEDURE:
- Quality Risk Assessment is a quality risk level performance measurement process.
- Quality Risk Levels are determined by monitoring Quality Indices.
- Quality Indices are elements of the quality systems, which upon evaluation shall provide a measure of Effectiveness of Quality Management Systems
- Lead Indices measures the quality attributes which have direct impact and/or compromises the compliance to cGMP.
- Evaluation of the quality risk levels of sites shall be done using Lead Indices.
- Lag Indices does not provide direct measure, however these are monitored for information purpose as they compliment quality attributes.
- Below table represents identified quality indices for quality risk assessment:
Click the link for download word file copy of this document: https://pharmaguidehub.com/product/quality-risk-assessment-quality-metrics-in-pharmaceutical/
Lead Indices | Lag Indices |
1. Product Recalls 2. Inspection Findings · Any critical /Major findings (Regulatory related , internal/customer audits) · Regulatory letters E.x. -Warning letter 3. Product Complaints · Expedited · Recurring · Failure to notify Regulatory agencies 4. Overdue Investigation and/or CAPA 5. Non Conformances · Quality impacting/Confirmed OOS for finished product/stability (including contract testing lab) 6. Lot Dispositions 7. Product Quality Reviews (PQRs) | 1. Product Complaints (High) 2. Inspection Findings- Others(minor/ recommendations) 3. Non Conformances · QI and OOS for input materials · Recurring NCs (QI), Exc. (Major) and OOT(Stability) 4. Senior Management Controls |
- Collection of data in Quality Data Index:
- Quality Data Index in the form of protected spreadsheets shall be available to the site to record the Quality Indices data. The spreadsheets shall be controlled by QA and shall be updated as and when there is a relevant change in the SOP.
- QA personnel shall collect Quality Indices data from relevant log books/reports and record the same in individual Quality data index sheets.
- Data shall be collected and quality indices shall be updated by the seventh (+/- 2 days) of every month.
- The Quality Indices data collected shall be verified by Head QA/designee for accuracy.
- After collection of data in Quality Data Index Sheets, a monthly summary of observations specific to Quality Indices shall be updated in the Quality Metrics Form.
- This Quality Metrics Form shall be used for tracking of monthly performance of Quality Aspects.
- Risk Assessment and Quality Risk Rating:
- Predetermined risk scores are assigned for each quality risk element of Lead Indices in the Quality Risk Dashboard. In the dashboard, Quality risk elements, which are potentially high risk, are assigned greater weightage.
- The Quality indices scores/targets are set bearing sites continual conformance to cGMP and regulatory compliances in Quality Risk Assessment Guide.
- Quality Indices in the Risk Dash Board shall be updated based on data gathered in Quality Metrics, data gathered for the review period shall be verified and corresponding risk class (High risk/ Medium risk or Low risk rank) shall be selected as “Y”, when it meets stated criteria.
- Based on Risk to cGMP compliance and/or regulatory compliance, each quality indices is weighted e.g. critical lead indices such as Recalls and Inspection findings are weighted 100%, while all other indices are weighted 50%.
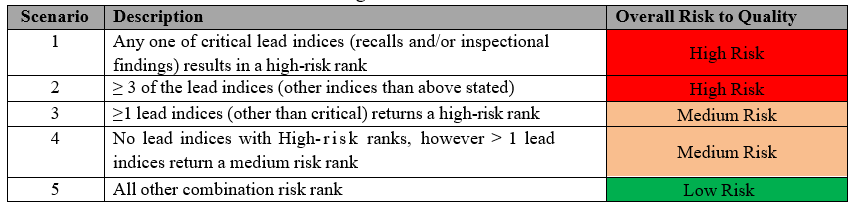
Note: Any lead quality indices, which were rated low risk due to collected data, but has a potential risk to cGMP compliance/regulatory conformance, such indices shall be assigned with high risk scoring as appropriate.
Click the link for download word file copy of this document: https://pharmaguidehub.com/product/quality-risk-assessment-quality-metrics-in-pharmaceutical/
- Data obtained from every month shall be updated in Quality Risk Dashboard and comparison of unit performance between previous months to current month shall be done.
- Based on the quality indices historical data and its review, each site shall be provided with yearly targets for each quality indices. These shall be set by January every year.
- These set yearly quality indices data shall be agreed between the site quality in-charge and senior management.
- Escalation to Senior Management & Risk Mitigation:
- The Quality Risk Assessment (Quality Risk Dashboard) shall be reviewed during Quality Review Meeting with Senior Management.
- The individual trends of Quality (Lead and Lag) Indices shall also be reviewed during the Quality Review Meetings, wherever applicable.
- Gaps/ Improvement opportunities in the system shall be discussed in QRM.
- With overall high-risk ranking for more than two consecutive periods shall be escalated to the senior management.
- QA Head/In-charge shall provide proper justification along with the supporting data for such performance. He/she shall conduct an assessment and shall propose appropriate corrective measures to mitigate the risk.
- Appropriate Corrective and Preventive Actions undertaken shall aim at preventing recurrence of such events. Wherever applicable, these actions shall be extended to manufacturing sites by QA.
- REFERENCES:
Not Applicable
- ANNEXURES:
Annexure Number | Title of annexure |
Annexure-I | Quality Data Index |
Annexure-II | Quality Metrics Form |
Annexure-III | Quality Risk Assessment Guidance Form |
Annexure-IV | Quality Risk Dash Board |
- DISTRIBUTION:
- Controlled Copy No. 01 : Head Quality Assurance
- Controlled Copy No. 02 : Head Production
- Controlled Copy No. 03 : Head Quality control
- Controlled Copy No. 04 : Head Engineering
- Master Copy : Quality Assurance Department
- ABBREVIATIONS:
PNC | : | Process Non Conformance |
No. | : | Number |
SOP | : | Standard Operating Procedure |
MNC | : | Material Non Conformance |
CAPA | : | Corrective And Preventive Actions |
NA | : | Non Conformance |
IA | : | Internal Audits |
PQR | : | Product Quality Review |
CC | : | Change Control |
QA | : | In process Quality Assurance |
PGH | : | Pharmaguide Hub |
- REVISION HISTORY:
CHANGE HISTORY LOG
Revision No. | Details of Changes | Reason for Change | Effective Date |
00 | New SOP | Not Applicable | To Be Written Manual |
Click the link for download word file copy of this document: https://pharmaguidehub.com/product/quality-risk-assessment-quality-metrics-in-pharmaceutical/
Annexure-I
Quality Data Index
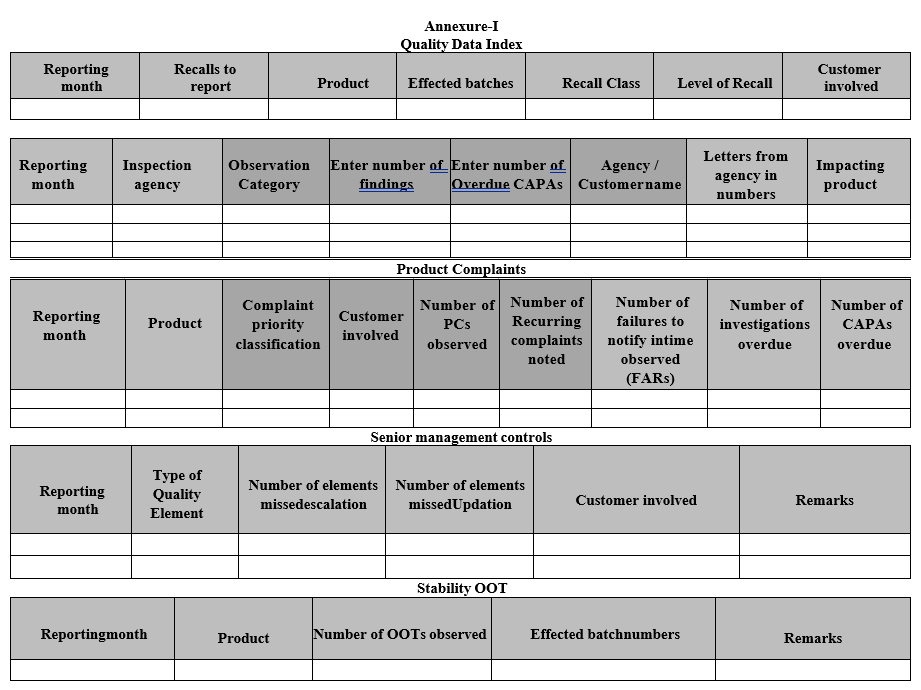
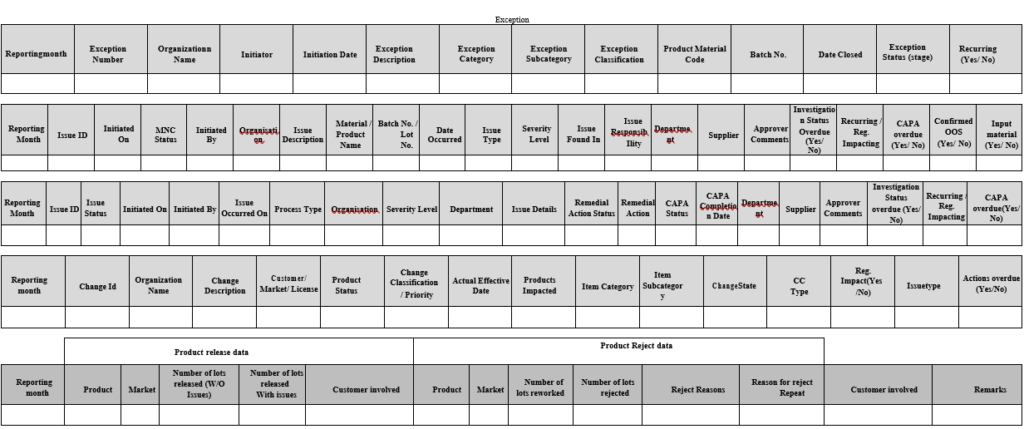
Annexure-II
Quality Metrics Form

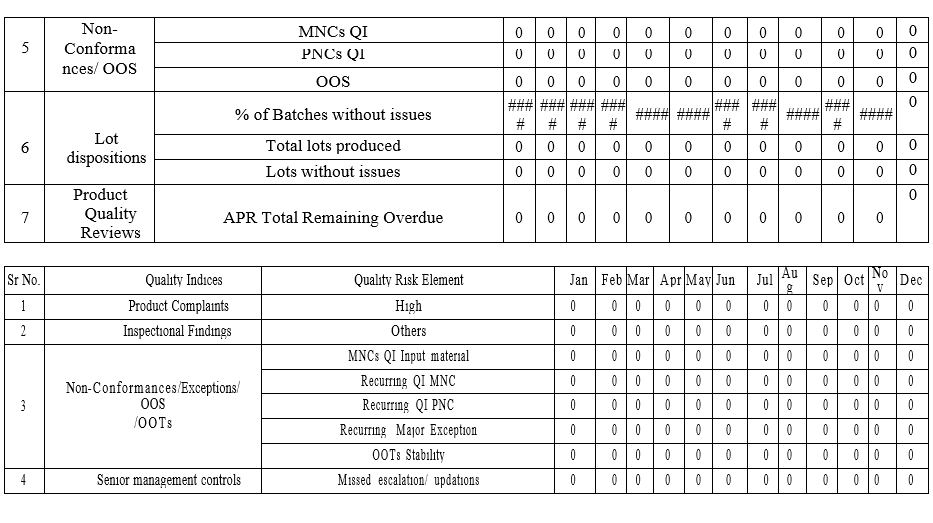
Annexure-III
Quality Risk Assessment Guidance Form
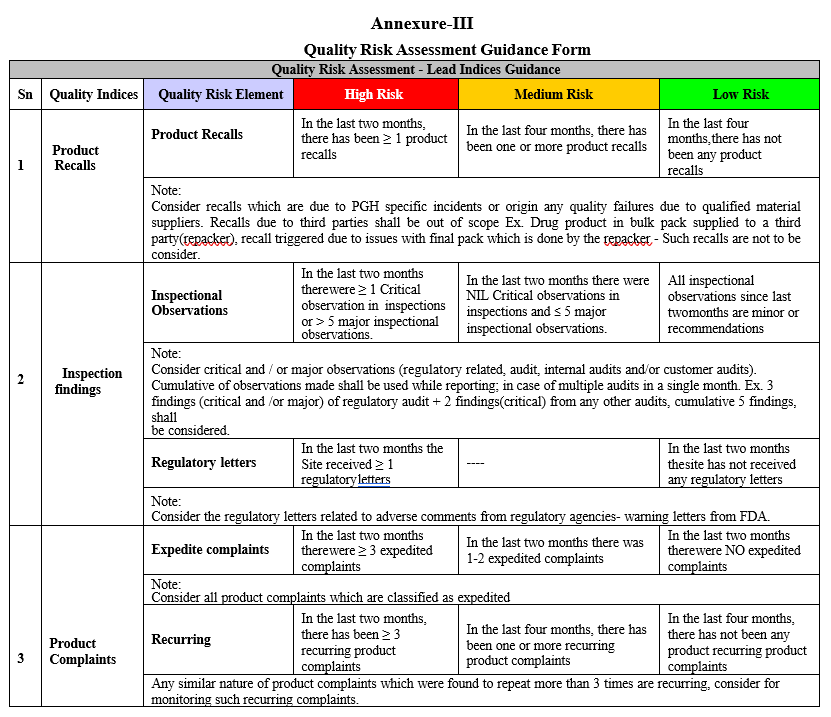
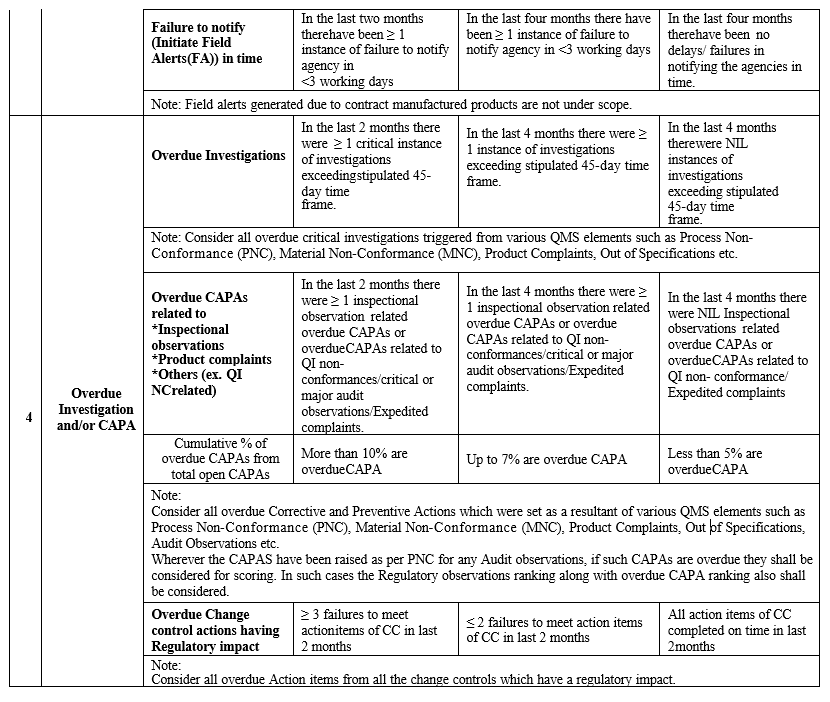
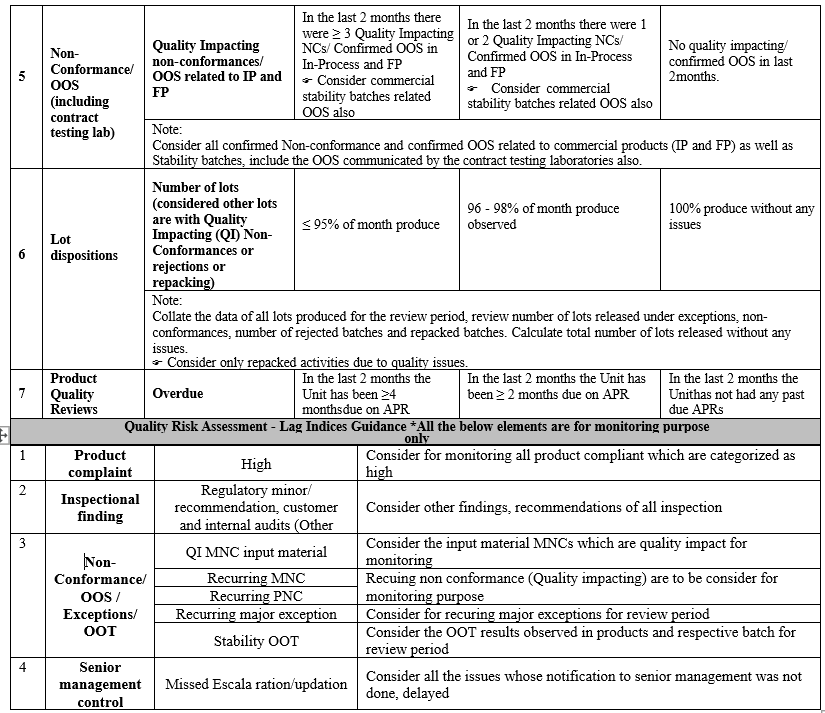
Annexure-IV
Quality Risk Dashboard
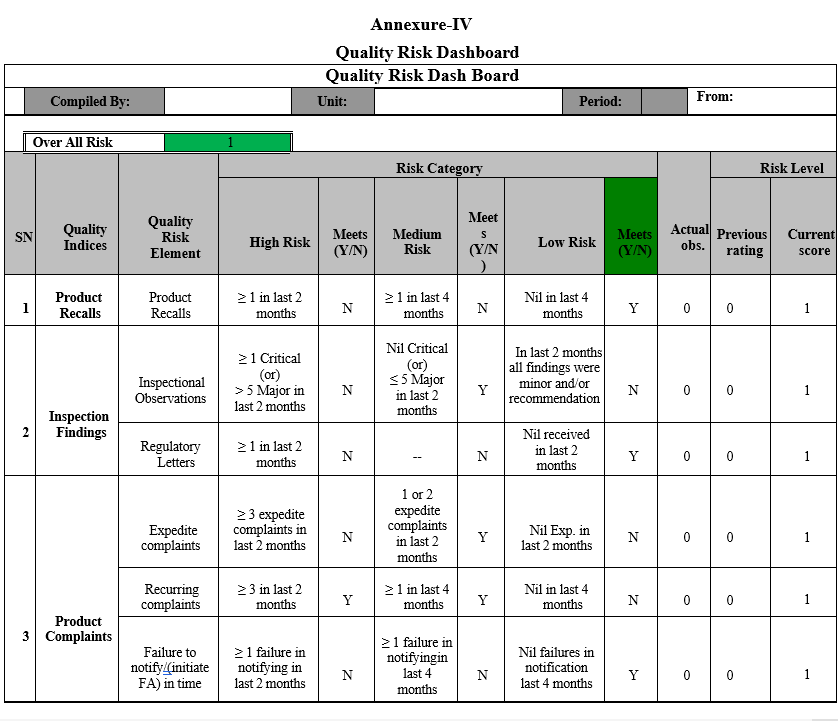
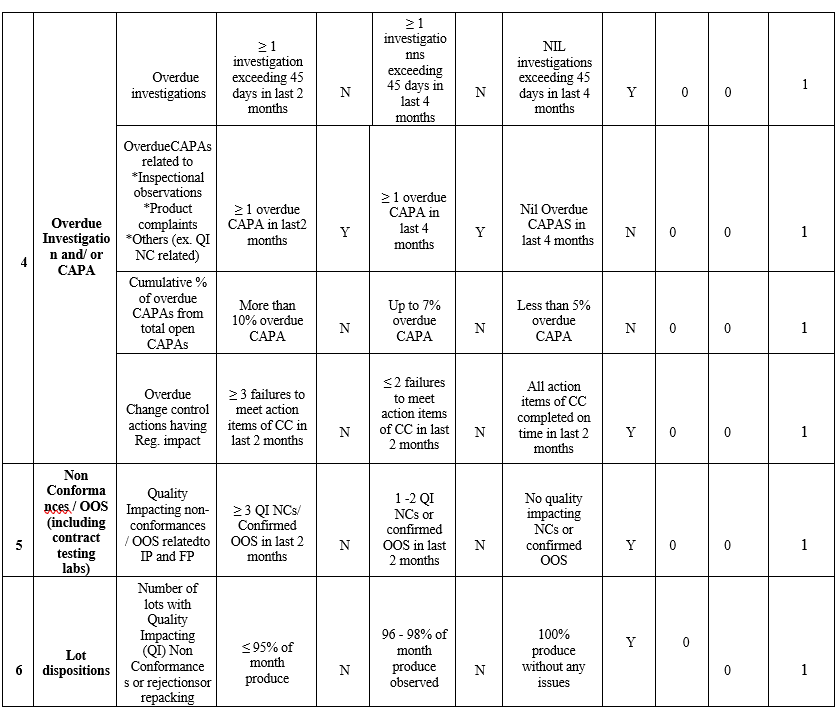

Click the link for download word file copy of this document: https://pharmaguidehub.com/product/quality-risk-assessment-quality-metrics-in-pharmaceutical/
Frequently Asked Question?
Q1: What is the main objective outlined in the document?
A1: The main objective is to establish the requirements for the effective measurement, assessment, and reporting of Quality performance and Quality Risk Levels using Quality Indicators/Indices.
Q2: Where is the scope of this procedure applicable?
A2: The procedure is applicable for Quality performance review at a specific location of the company.
Q3: What responsibilities does the QA In-Charge/Designee have in the process?
A3: The QA In-Charge/Designee is responsible for collecting data related to Quality Systems, evaluating Quality Risk, presenting data in Quality Review Meetings (QRM), proposing Corrective Actions, ensuring effective CAPA implementation to reduce Quality Risk, and making the final disposition of Risk status as High for specific Quality indices for any specific/special cause.
Q4: What is the accountability of the QA Head in this procedure?
A4: The QA Head is accountable for the implementation of the Standard Operating Procedure (SOP).
Q5: How is Quality Risk Assessment performed in terms of measuring performance?
A5: Quality Risk Assessment involves measuring performance through Quality Indices, which are elements of the quality systems providing a measure of the effectiveness of Quality Management Systems. It includes Lead Indices that directly impact compliance to cGMP and Lag Indices monitored for informational purposes.
Q6: How is data collected for Quality Indices, and what is the frequency of updating Quality Data Index Sheets?
A6: QA personnel collect data from relevant log books/reports and record it in individual Quality data index sheets. Data is collected and updated by the seventh (+/- 2 days) of every month.
Q7: What is the purpose of the Quality Metrics Form, and how is it used?
A7: The Quality Metrics Form is used for tracking the monthly performance of Quality Aspects. It is updated with a monthly summary of observations specific to Quality Indices after collecting data in Quality Data Index Sheets.
Q8: How is Risk Assessment and Quality Risk Rating determined in the Quality Risk Dashboard?
A8: Predetermined risk scores are assigned for each quality risk element of Lead Indices in the Quality Risk Dashboard. Quality indices scores/targets are set, and each quality index is weighted based on its risk to cGMP compliance and/or regulatory compliance.
Q9: What criteria are used to categorize the overall risk to Quality in the Quality Risk Dashboard?
A9: The overall risk to Quality is categorized based on scenarios and criteria. For example, any one critical lead index (recalls and/or inspection findings) resulting in a high-risk rank is classified as High Risk.
Q10: How is the escalation to Senior Management and Risk Mitigation handled in the procedure?
A10: The Quality Risk Assessment (Quality Risk Dashboard) is reviewed during Quality Review Meetings with Senior Management. Overall high-risk rankings for more than two consecutive periods are escalated to senior management, and appropriate corrective and preventive actions are proposed and implemented by QA Head/In-charge.
Click the link for download word file copy of this document: https://pharmaguidehub.com/product/quality-risk-assessment-quality-metrics-in-pharmaceutical/