- PROCEDURE FOR THE RAW MATERIAL IDENTIFICATION, STORAGE AND TRANSFER OF DISPENSED RAW MATERIAL FROM STORES TO PRODUCTION:
- Raw material identification, storage and transfer of dispensed raw material from stores to production is a key process so a correct quantity, correct material can be transfer without any kind of mix-up, spillage and contamination.
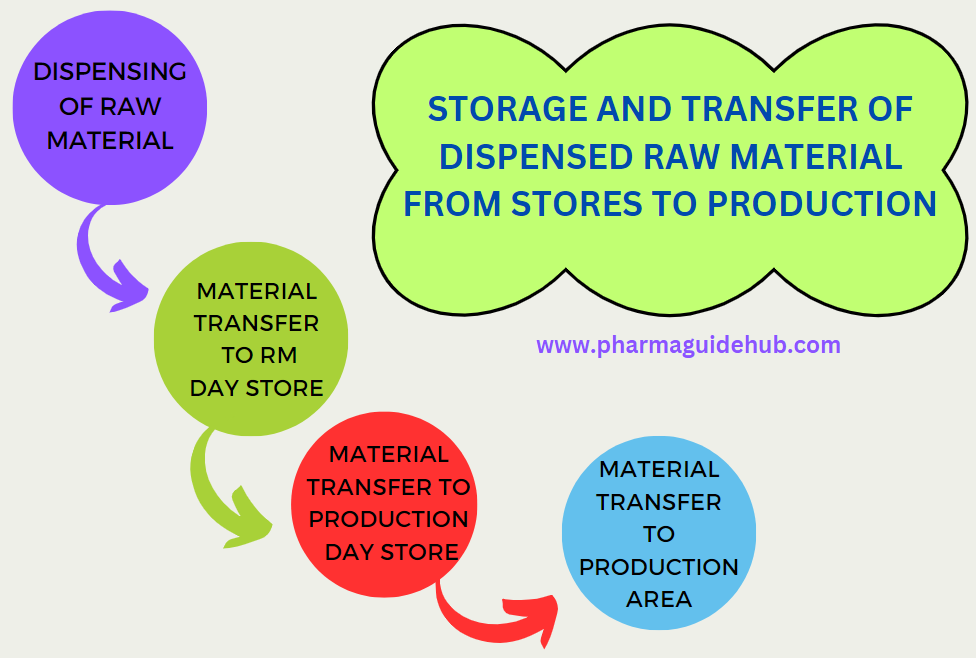
- INDENTING:
- As per the production schedule the Executive Production shall get the BMR as per the SOP and hand over the raw material dispensing sheets to the stores.
- The Executive Stores shall issue the raw material.
- TRANSFER & STORAGE:
- The raw material shall be transferred from the dispensing room to the dispensing material hold area of stores through material pass box along with the material dispensing sheets (If pass box is not available then material entry door can be used for material transfer).
- Before transferring the dispensed raw material from dispensed raw material hold of store to production raw material hold, the raw material shall be checked for proper seal integrity and correct label for the raw material as per the material dispensing sheets.
- The dispensed raw material shall be transferred from dispensed raw material hold area of stores to dispensed material hold of production through pass box along with material dispensing sheet (If pass box is not available then material entry door can be used for material transfer).
- After transferring the raw material to dispensed material hold area all materials of particular batch shall be stored in case trolley /pellet with proper status label outside the SS case trolley/Pellet.
- The details of temperature shall be recorded in the temperature and relative humidity record as per SOP.
- If any abnormality/Non-Conformance is observed while storage and transferring of dispensed raw materials. NCR shall be initiated as per SOP and shall be investigated.
- The stored raw material shall be verified by production Executive and IPQA-Executive in dispensed material hold area and same shall be signed off by Production and IPQA in BMR.
- The dispensed label shall be checked for the following details:
- Material name.
- Material Code.
- Product.
- Batch Number.
- Lot No.
- Container No.
- Tare Wt., Net Wt. and gross weight.
- UOM.
- Before doing the next weighment in the dispensing hold area, cleanliness of all the weighing balances and area shall be ensured by both production executive and IPQA executive.
- PROCEDURE FOR THE MOVEMENT OF DISPENSED RAW MATERIALS FROM DISPENSED HOLD OF PRODUCTION TO THE RESPECTIVE AREA:
- After verification of the raw materials, the cage trolley shall be securely closed and the materials shall be transferred from dispensed hold of production to the respective area through material entry.
- After transferring all the materials into the respective area, before addition in to the process, all the materials shall be checked once again with respect to BMR by the production person under the supervision of production executive.
- The dispensed labels shall be pasted in the respective BMR.
- ABBREVIATIONS:
PD | : | Production |
IPQA | : | In process quality assurance |
BMR | : | Batch Manufacturing Record |
No. | : | Number |
SOP | : | Standard Operating Procedure |