- OBJECTIVE:
- To lay down the procedure for Receipt, Storage and Handling of Raw Material and Packing Material.
- SCOPE:
- This SOP is applicable for the procedure of Receipt, Storage and Handling of Raw Material and Packing Material in warehouse department at {Company Name} {Location}.
- RESPONSIBILITY:
- WH Executive/Designee – shall be responsible to follow the procedure as per SOP.
- Executive/Designee Quality Control– shall be responsible for sampling of the material.
- Executive/Designee Quality Assurance– shall be responsible for verify the discrepancy, if any observed during receipts.
- Head Warehouse – is responsible for compliance of the SOP.
- ACCOUNTABILITY:
QA Head shall be Accountable for implementation of SOP.
- PROCEDURE:
- Receipt:
- Security personnel shall verify the documents and inform to the stores about the arrival of the material by forwarding documents.
- Documents shall be verified by the store Executive/designee for the address, PO No. Approved vender, Material Name, COA and Excise documents.In case the received quantity is more than 10 % of the PO qty, communication shall be made to the Purchase department.
- The purchase department shall amend the PO to the received quantity.
- Ensure that COA of vender is legible and signed by the competent person of the respective company.
- If not, immediately arrange to get a legible copy from the vendor.If the documents are satisfactory inform the security to allow the vehicle inside and direct the vehicle to the concerned receiving bag.
- The vehicle driver shall be instructed to position the vehicle in such a way that the rear side is towards the receiving end.
- Physical Inspection:
- Check the inside condition of the vehicle before the start of unloading.
- The number of containers received shall be checked against the delivery challan.
- The integrity of the containers shall be checked for any physical damage/leakage.
- Check the manufacturer’s batch number/lot number, lot quantity, date of manufacturing, date of expiry, name and address of the manufacturer.
- Check the manufacturer’s description/pharmacopeial grade.
- Check whether the supplier is on the Approved vendors list.
- Ensure the availability of the MSDS of the material.
- In case of any new material received, MSDS of the material shall be provided by vendor along with material.
- Verify the manufacturer COA and if there are any specific instructions for storage condition then transit temperature shall be verified through downloaded data of the data logger and after ensuring the satisfactory temperature condition during transit the material shall be in warded.
- In case of discrepancy the same shall be communicated to the concerned vendor and Quality Assurance and the material shall be kept under hold.Record the checks in the physical verification check record.
- Unloading:
- Ensure the cleanliness of the unloading area.
- Ensure the condition of the truck and the material shall be intact condition.Handle the container/packs carefully to avoid damage or loss of seals.
- After unloading the material, Quantities shall be cross verified against invoice.After unloading the material clean the surface of the container by using vacuum cleaner/lint free cloth.
- All raw material and primary packing materials like aluminum foil, PVC/PVDC films and rayon shall be checked on a weight basis. Tolerance limit for received materials.
API = ± 0.5% per consignment/batch wise
Excipients = ± 1% per consignment
Aluminum FOIL/PVC/PVDC =± 1% per consignment
- All the cartons, shippers, leaflets, containers, closures and self-adhesive tapes etc. Shall be checked on count basis.
- After the completion of the physical verification enter the details in format, Physical Verification Check Record and weight details shall be enter in the format-I, Manual Weighment Record.
Click the link to download word file copy of this document:
https://pharmaguidehub.com/product/receipt-storage-and-handling-of-raw-material-and-packing-material/
- Material Received Report shall be prepared after completion of weight and checklist preparation.
- Generate the required number of “UNDER TEST” labels.
- Deface the suppliers/manufacturer’s approved/passed label on the container by using a marker pen, if any and ensure all details on the “UNDER TEST” label before affixing to all containers.
- Send the vendor COA And Lot. No. To QC department for sampling purpose.
- Handling of materials received in damaged/wet/torn condition:
- In case if any material received in damaged condition, and if the damage is only on external of the containers, which has no impact on the material quality, then the material can be accepted.
- However, a communication shall be made with the vendor through the Purchase Department for the external damage observed and the material will be further protected.
- If any damage is observed during the receipt and material is exposed to the environment then, immediately segregate the damaged containers and mention same on the transporters lorry receipt copy and insist the driver to endorse in the lorry receipt copy about the damage and inform IPQA through ‘Intimation regarding receipt of materials in damaged/wet/torn condition’ and in such cases, MRR shall be prepared by providing the second line item for the quantity rejected with separate lot no.
- Once the information shall be given to IPQA regarding the damage, IPQA personnel shall inspect the condition of the material and decide whether the consignment shall be accepted or not.
- If the consignment is received in unusable condition, then it shall be rejected based on IPQA comments on the check list and stores personnel shall initiate the process Non- Conformance /Material Non-Conformance whichever is applicable as per the SOP respectively and shall be investigated.
- Warehouse shall communicate same to purchase department and PPIC for further action.
- The damaged containers/bags shall be transferred to rejected material stores after affixing damaged container label by QA.
- After getting the supply chain/PPIC instructions materials shall be sent back to the supplier or destructed by completing the customs formalities.
- Printed packing materials shall be destructed at site and should not send back to the supplier.
- Assigning of Expiry and Retest Date During Preparation of MRR:
- Check the Manufacturing date and Expiry/Retest date of material received with Vendor COA.
- If the Manufacturer label or COA does not have the expiry date, and retest date is less than 3 years consider shelf life as 3 years for all API from the date of manufacturing and 5 years for excipients (in order to control on number of re testing for API an Excipients).
- In case Expiry date is not given by manufacturer on COA and Container labels and if vendor has mentioned the Retest/Revaluation date less than one year for API and excipients, then the Retest /Revaluation date mentioned by the vendor shall be considered as retest date while preparing the MRR.
- The shelf life shall be considered 3 years for API and 5 years for excipients (in order to control the number of re testing for API and Excipients).
- If the Retest/Re evaluation date on the COA or on the container label is greater than 3 years for API and 5 years for excipients from the date of manufacturing, then the Retest/Re evaluation date mentioned by the vendor shall be considered as expiry date while preparing the MRR.
- If vendor has provided shelf life/Exp. date more than three years for API and five years for excipients, then vendor shelf life shall be considered as the shelf life of the material.
- Retesting date shall be considered as 1 year while preparing MRR.
- In case of primary packaging materials, if the supplier/manufacturer is giving any expiry date same shall be considered while preparing MRR.
- If expiry date is not given in COA or on label then, consider expiry date as 5 years from the date of manufacturing.
- In case of the Manufacturer is giving manufacturing date and expiry date in the form of month and year then consider the manufacturing date as the last day of the given month and expiry date as the last date of the given month (i.e. if manufacturing date given as june-24 and expiry date given as May 29 then manufacturing date shall be considered as 30-Jun-2024 and expiry date shall be considered as 31-May-2029.
- If vendor label or COA shows the terminology like “Use before”, “Use by”, “Best before”, “Shelf Life”, ‘Minimum shelf life’, “stability at least until end of “consider all these as expiry.
Discrepancy:
- If any discrepancy observed stores personnel shall raise the process Non- Conformance /Material Non-Conformance whichever is applicable as per the SOP and shall be investigated.
- Warehouse shall communicate same to purchase department and PPIC for further action.
- STORAGE:
- After pasting under test label, the material shall be stored in the respective storage area for sampling.
- The QC Executive shall ensure the vendor COA results meets the requirement of our specification. If any discrepancy noticed shall forward the MRR with vendor COA to Quality Assurance for the further corrective action in coordination with purchase department by initiating the NCR.
- If the result of vendor COA meets the requirement of our specification, QC Executive shall sample the materials.
NOTE: Hormones shall be sampled under Isolator as per the current version of SOP
- After completion of sampling, QC Executive shall paste ‘SAMPLED’ label on the sampled container with sign and date.
- Sampled material containers shall be transferred to respective area with respect lot wise separately.
- Ensure that material shall be stored under prescribed storage conditions.
- The copy of the delivery challan/invoice shall be filed in the respective file along with receipt check list, COA and other relevant document if any.
- Approval and rejection:
- After analysis of materials, QC shall return duly filled and signed MRR along with the COA to stores.
- Approved/Rejected labels shall be affixed over the under-test labels, by Quality Control Executive/Designee in presence of stores Executive/Designee.
- Based on the status label affixed by QC Executive/Designee the material shall be transferred to respective designated storage area (Approved/Rejected).
Click the link to download word file copy of this document:
https://pharmaguidehub.com/product/receipt-storage-and-handling-of-raw-material-and-packing-material/
- REFERENCES:
Not Applicable
- ANNEXURES:
ANNEXURE NO. | TITLE OF ANNEXURE |
Annexure-I | Manual Weighment Check Record |
Annexure-II | Physical Verification Check Record |
Annexure-III | Intimation regarding receipt of materials in damaged/wet/torn condition |
Annexure-IV | Damaged Container Label |
Annexure-V | Under Test Label |
ENCLOSURES: SOP Training Record.
- DISTRIBUTION:
- Controlled Copy No. 01 : Head Quality Assurance
- Controlled Copy No. 02 : Head Warehouse
- Master Copy : Quality Assurance Department
- ABBREVIATIONS:
No. | : | Number |
SOP | : | Standard Operating Procedure |
QA | : | Quality Assurance |
MRR | : | Material Received Report |
COA | : | Certificate Of Analysis |
NCR | : | Non Conformance Report |
- REVISION HISTORY:
CHANGE HISTORY LOG
Revision No. | Details of Changes | Reason for Change | Effective Date |
00 | New SOP | Not Applicable | To Be Written Manual |
Annexure-I
Manual Weighment Check Record
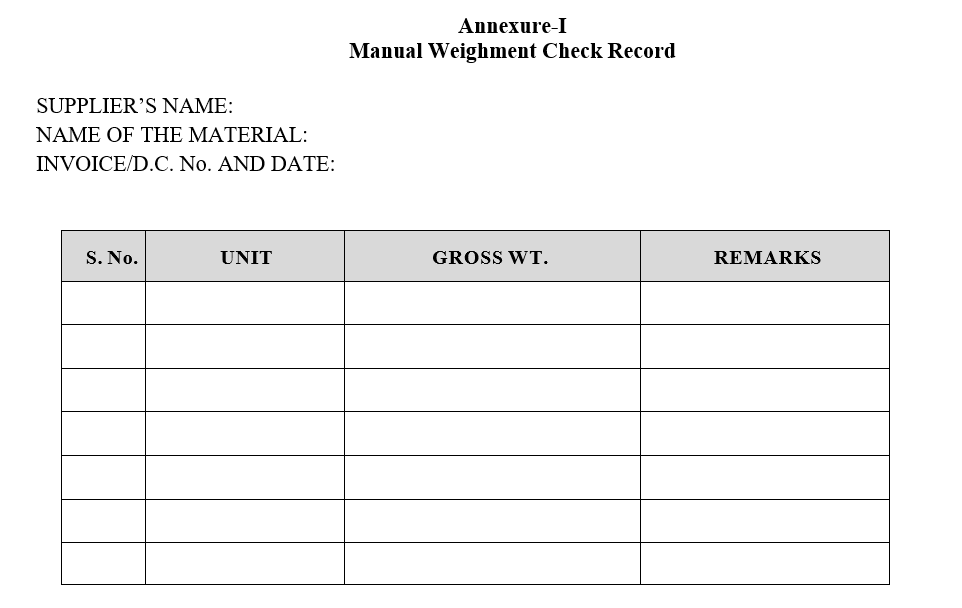
Annexure-II
Physical Verification Check Record
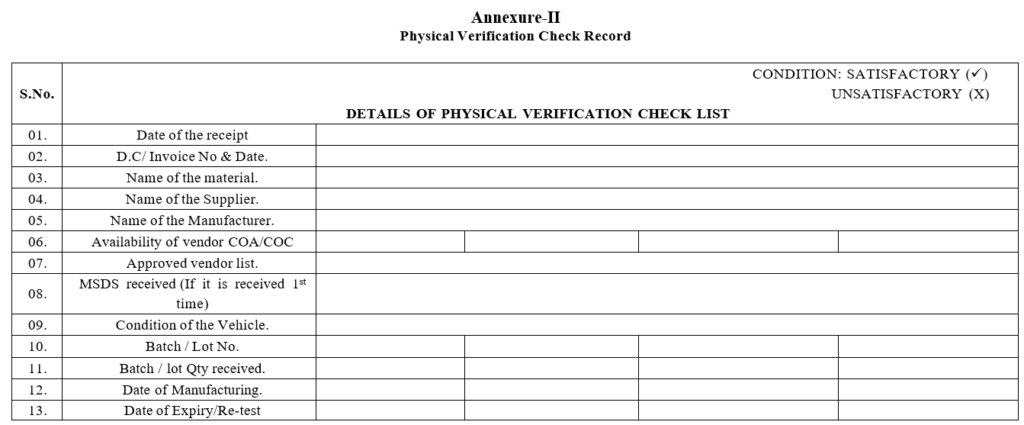
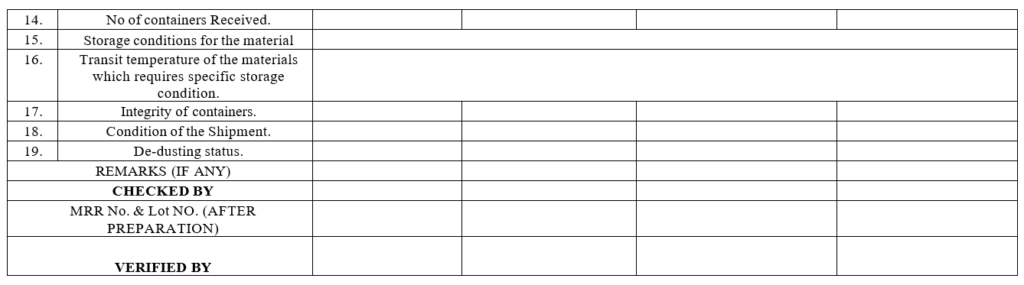
Annexure-III
INTIMATION REGARDING RECEIPT OF MATERIALS IN DAMAGED/WET/TORN CONDITION
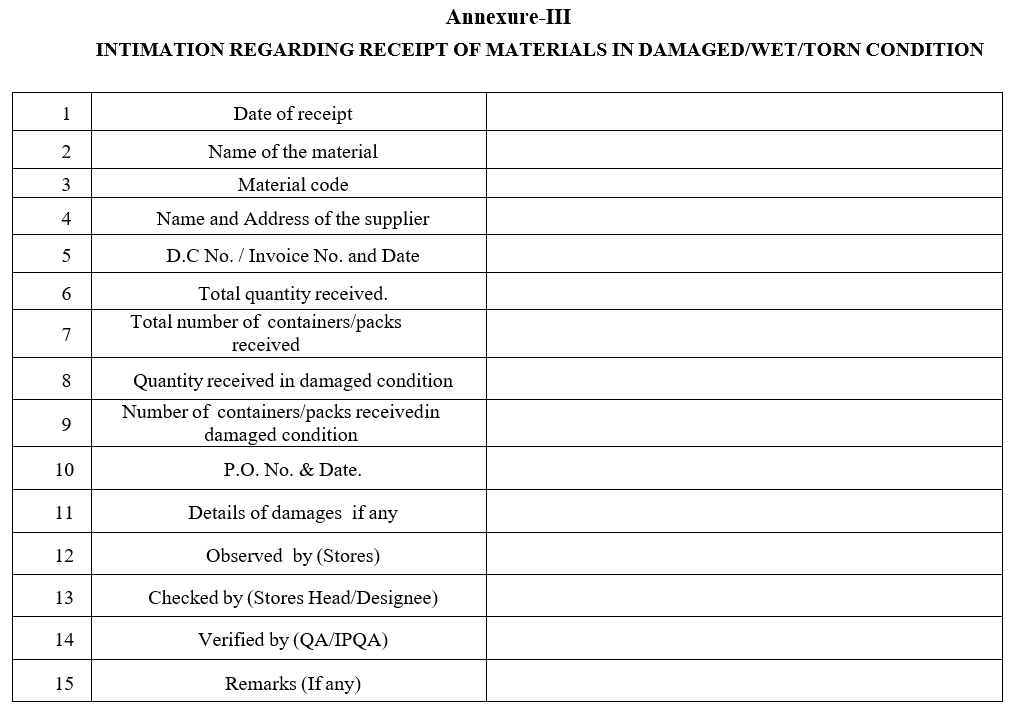
Annexure-IV
Damaged Container Label
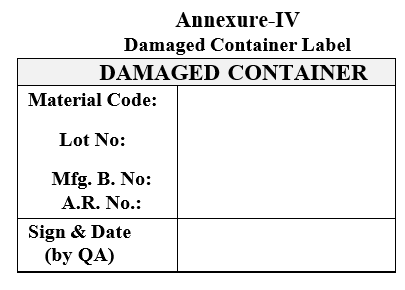
Annexure-V
Under Test Label
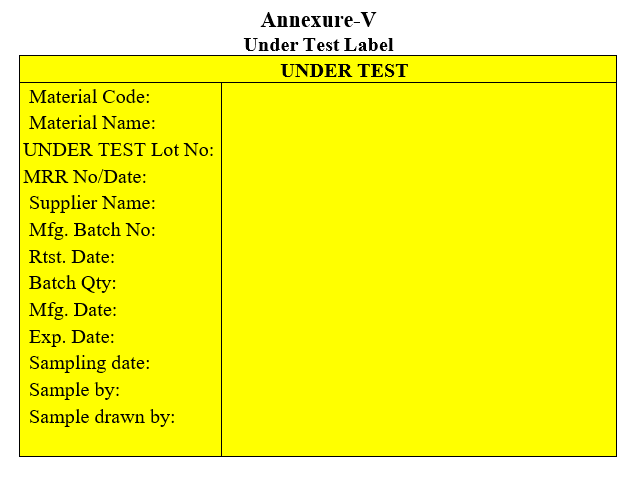
Frequently Asked Question?
Question 1: What documents need to be verified upon receiving materials?
Answer: Security personnel verify arrival documents and inform stores. Stores personnel then verify documents for address, PO number, approved vendor, material name, COA, and excise documents. Discrepancies require communication with the purchase department.
Question 2: How is a physical inspection conducted?
Answer: The vehicle interior, container number, container integrity, manufacturing details, supplier approval, and MSDS availability are checked. For new materials, the vendor must provide the MSDS. Transit temperature is verified for temperature-sensitive materials. Discrepancies are documented and communicated.
Question 3: What happens to materials received in damaged/torn condition?
Answer: If damage is external and doesn’t impact quality, the material is accepted with communication to the vendor. Exposed materials are segregated, documented, and reported to IPQA. IPQA decides acceptance or rejection. Rejected materials are transferred to designated storage and returned to the supplier or destroyed.
Question 4: What is the storage process after receiving materials?
Answer: “Under test” labels are affixed, and materials are stored for sampling. QC verifies vendor COA and samples materials . “Sampled” labels are applied, and materials are transferred to designated areas under prescribed storage conditions. Delivery documents are filed.
Question 5: How are materials approved or rejected?
Answer: QC analyzes materials and returns a completed MRR with COA to stores. “Approved” or “Rejected” labels are affixed based on QC analysis. Materials are transferred to designated storage areas accordingly.
Click the link to download word file copy of this document:
https://pharmaguidehub.com/product/receipt-storage-and-handling-of-raw-material-and-packing-material/