- PROCEDURE FOR THE SAMPLING, REGISTRATION AND TESTING OF PURIFIED WATER FOR CHEMICAL AND MICROBIOLOGICAL TESTS:
- Purified water is essential in a pharmaceutical plant, used in various stages of manufacturing, from cleaning equipment to formulating medications. To ensure its quality and safety, regular sampling and testing are crucial.
- Operating Procedure: Sampling and Testing Plan:
- Chemical and microbiological testing shall be done for purified water at various stages of water generation and distribution.
- Follow Format -I for water sampling schedule and prepare a monthly sampling and testing schedule by using the Format-II.
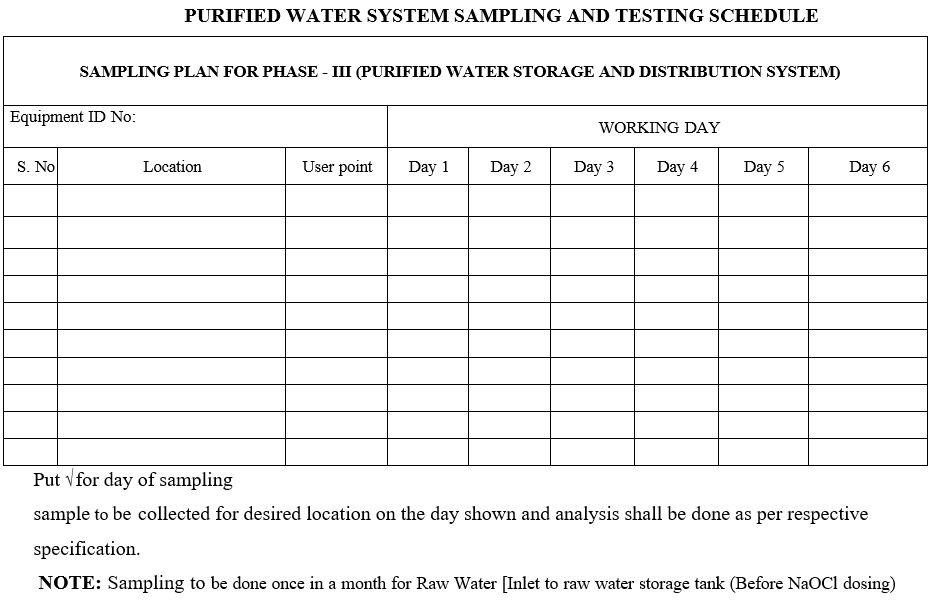
- Glassware preparation for chemical and microbiological sample collection:
- Glassware used for purified water sampling shall be rinsed with purified water and dried in an oven at 55°C-60°C.
- Collect 400 ml sample in 500 ml capacity Glass bottles shall be used for chemical analysis.
- Connect the TOC pipe to the Sampling or User point and operate the TOC analyzer as per SOP.
- Collect 100 ml sample in Sterilized glass bottles of 100 ml capacity shall be used for Microbiological analysis.
- For identification of Microbiology sampling bottles, affix the Chemical indicator tape prior to sterilization and sterilize as per validated sterilization cycle.
- For chlorine treated water samples add 0.5 ml of 5% w/v sodium thiosulphate solution in to the bottle before sterilization.
- SS sampling kit shall be sanitized with 70 % v/v IPA.
- Carry the pretreated and pre-sterilized sampling bottles, hand gloves and nose mask in a SS sampling kit to the respective locations to collect the purified water sample for chemical and microbiological testing.
Click the link for download word file copy of this document:
https://pharmaguidehub.com/product/sampling-registration-and-testing-of-purified-water-for-chemical-and-microbiological-tests/
- Procedure for sampling of purified water (chemical and microbiology):
- Prior to sampling, label the pretreated sampling bottle for chemical testing and pre sterilized bottle for Microbiological testing with details of Sampling point number, sampled by sign, date and time.
- Samples shall be collected as per specified sampling and testing Schedule.
- Sampling point’s schematic diagram.
- Open the valve completely and allow draining the purified water for 2-3 minutes and slightly closing the valve sufficient for sampling.
- Rinse the sampling bottles for 2 to 3 times with purified water to be collected from the sampling point.
- Collect 500 ml sample (Chemical and microbial in separate containers) for analysis as per USP/Ph. Eur specification.
- Immediately tighten the bottle with screw cap.
- While collecting the microbiological samples, wear the hand gloves and nose mask.
- Disinfect the glove hands with the 70% IPA.
- Sanitize the sampling point with 70% IPA.
- Fill the pre-sterilized bottle without rinsing. Keep the sufficient air space in bottle and immediately close the bottle.
- Wherever the user points have hose pipe, collect the sample from the end of the hose pipe.
- Collect the sample of 100 ml with minimal headspace and close the bottle tightly.
- Affix the sampling status label to the sampled bottles immediately and update water sampling status label.
Note: Sterilized glassware shall only be used for microbiological sampling.
- REGISTRATION OF SAMPLES:
- Purified water samples shall be registered as per SOP.
- Section in charge shall approve the samples, senior executive /Group leader shall in turn delegate individual tests to concerned analyst.
- After delegation the analyst shall take worksheets.
- Analyst shall perform the tests as per approved analytical testing procedures.
- After completion of analysis analyst shall enter the test results in worksheet.
- Completed worksheet shall be handed over to Group leader/Designee.
- Group leader/Designee shall review and approve the delegated tests after checking the work sheet and final approval shall be given by section in charge / Designee.
- All the samples A.R. No shall be generated in water samples inward register as per Format-III. The A.R. No. Shall have a unique numbering system. Batch / Lot No. Shall be given as “QCPW/DDMMYY” signifying the day of sampling.
- A.R. No. shall comprise of Twelve characters as shown below E.g.: QCPW2500001 is the first sample for
- First Two characters “QC” for department quality control
- Next Two characters “PW” indicates Purified water
- Next two characters “25” represents the year 2025
- Last five characters “00001” represents sequential number for each sample.
- Note: Batch / Lot No. Shall be given as “QCRW/DDMMYY” signifying the day of sampling For Raw water. RW indicates Raw water
- For validation of purified water samples A.R. No. Shall be given as QCVW2500001.
- First Two characters “QC” for department quality control
- Next Two characters “VW” indicates Validation purified water sample
- Next two characters “25” represents the year 2025
- Last five characters “00001” represents sequential number for each Sample.
- The manual Batch / Lot No. shall be referred to in the production batch records.
- TESTING:
- Chemical and microbiological samples:
- Analyze the samples within 2 hour after sample collection.
Click the link for download word file copy of this document:
https://pharmaguidehub.com/product/sampling-registration-and-testing-of-purified-water-for-chemical-and-microbiological-tests/
- In case of any delay in analysis, store the samples at 2-8°C and analyze the samples within 12 hours in case of any delay in analysis after 12 hours discard the samples and collect fresh samples for analysis.
- If stored at 2-8°C, allow the samples to attain the ambient temperature before analysis.
- Samples collected from different user points as per sampling schedule shall be analyzed for chemical and microbiological test parameters.
- Analyze the Chemical samples (Raw water and Purified water) as per specification.
- Analyze the microbiological samples as per SOP.
- Samples for TOC shall be analysed using TOC Instrument as per SOP
Note: On unscheduled breakdowns and holidays, samples from the stipulated sampling points shall not be collected for the week.
- The PU Tube (PU tube is using for purified water online TOC analysis) shall be replaced at a frequency of once in 3 months and record the details in Format -V.
- RELEASE OF SAMPLES:
Chemical and microbiological Samples:
- Partial COA shall be generated based on chemical test parameter results for the samples of storage tank.
- Water release shall be as per partial COA for Sampling Points of storage tanks.
- COA shall be sent to the Production department and Maintenance department. Maintain the QC Copy along with work sheet.
- Affix an approved label on the purified water storage tanks.
- Enter the chemical test results in work sheet on the same day.
- Enter the microbiological test results in work sheet after completion of specified incubation period.
- After approval, full COA as per specification shall be attached to the work sheet.
- Interpretation of Alert and Action limits and action recommended:
Chemical and Microbiological test parameters:
- If any test result exceeds the Alert limit, alert the Quality assurance department and Maintenance department.
- Alert limit 25 cfu /mL and Action limit will be 50 cfu /mL. If any test result exceeds the Action limit, immediately inform the Quality assurance and Production Department for further necessary corrective Action.
- If any test result exceeds specification limit, Inform to Quality Assurance, Maintenance and Production department to stop usage of purified water from the respective point.
- Quarantine the products manufactured during the period.
- Products shall be subjected to Microbiological testing and release the products if they meets the requirement.Investigation shall be done as per SOP.
- PREPARATION OF TRENDS:
Chemical and Microbiological test parameters:
- Monthly trends shall be prepared for all sampling points.
- Prepare the trends for test parameters pH, TOC, Conductivity and TMC.
- Submit the trends monthly to Quality assurance Department for further review.
- ANNEXURES:
ANNEXURE NO. | TITLE OF ANNEXURE |
Annexure-I | Purified water system sampling and testing schedule |
Annexure-II | Monthly water sampling schedule template |
Annexure-III | Water Samples Inward Register |
Annexure-IV | Water sampling status label. |
Annexure-V | PU Tube replacement record. |
- ABBREVIATIONS:
No. | : | Number |
cfu | : | Colony Forming Uni |
TOC | : | Total Organic Carbon |
OOS | : | Out Of Specification |
COA | : | Certificate of Analysis |
TMC | : | Total Microbial Count |
SS | : | Stainless steel |
A R No. | : | Analytical Report Number |
SOP | : | Standard Operating Procedure |
QC | : | Quality Control |
Click the link for download word file copy of this document:
https://pharmaguidehub.com/product/sampling-registration-and-testing-of-purified-water-for-chemical-and-microbiological-tests/
Annexure-I
PURIFIED WATER SYSTEM SAMPLING AND TESTING SCHEDULE
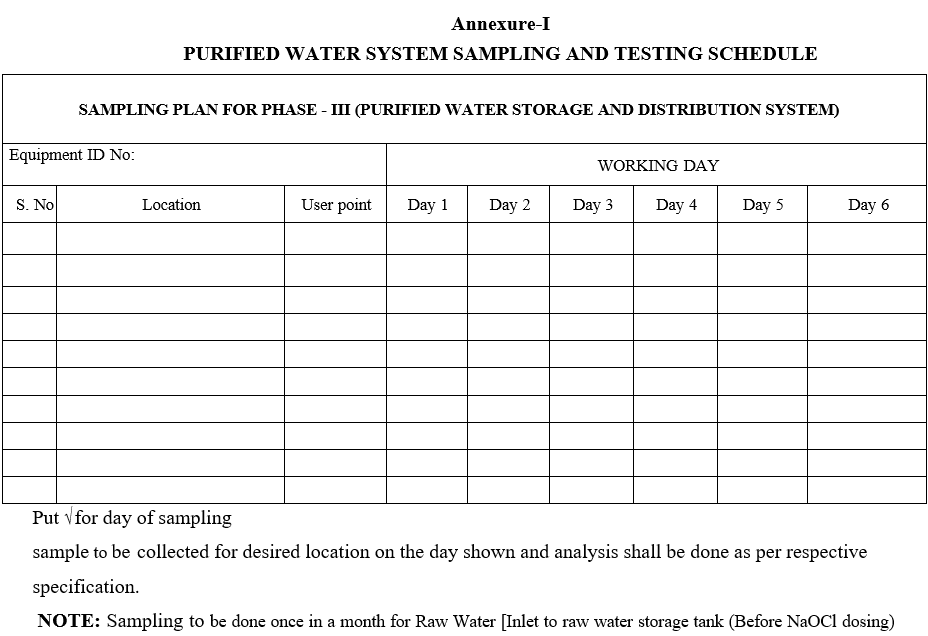
Annexure-II
Monthly water sampling schedule template
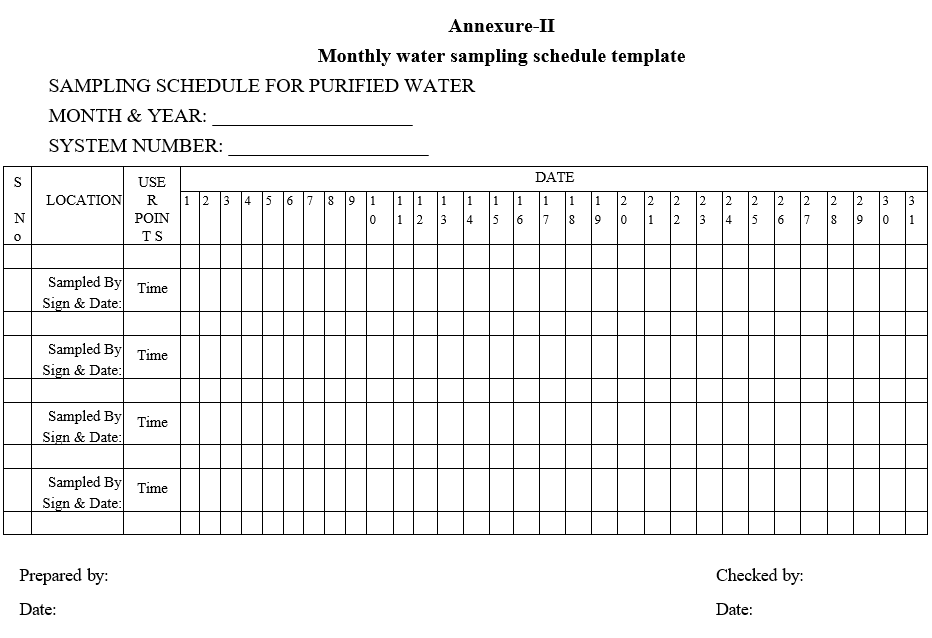
Annexure-III
WATER SAMPLE INWARD REGISTER
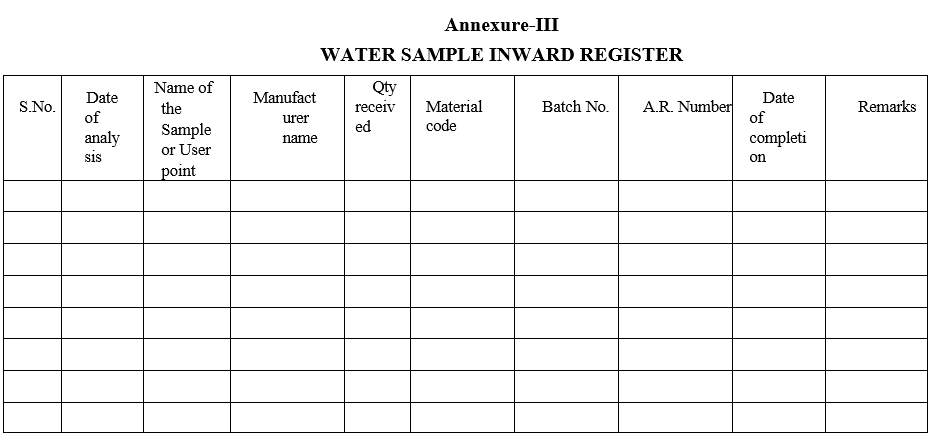
Annexure-IV
WATER SAMPLING STATUS LABEL
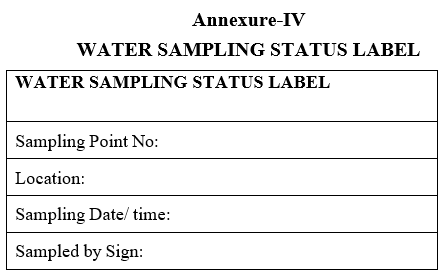
Annexure-V
PU TUBE REPLACEMENT RECORD
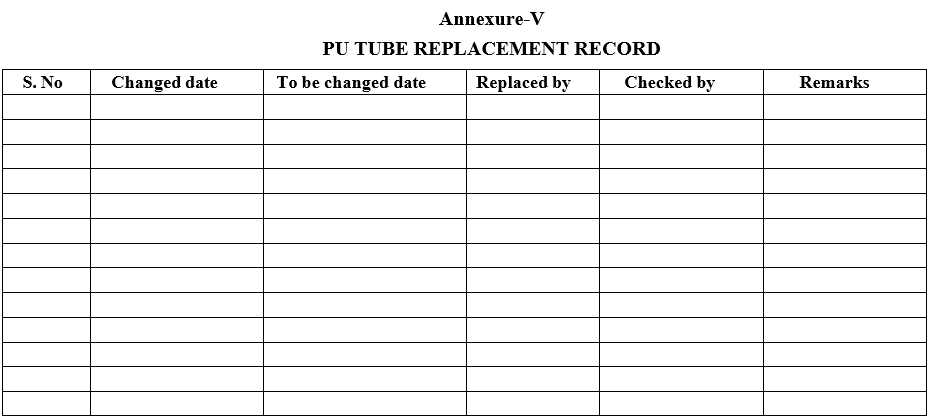
Click the link for download word file copy of this document:
https://pharmaguidehub.com/product/sampling-registration-and-testing-of-purified-water-for-chemical-and-microbiological-tests/