- OBJECTIVE:
To lay down a Procedure for Good Laboratory Practices (GLP) in the Quality Control Department.
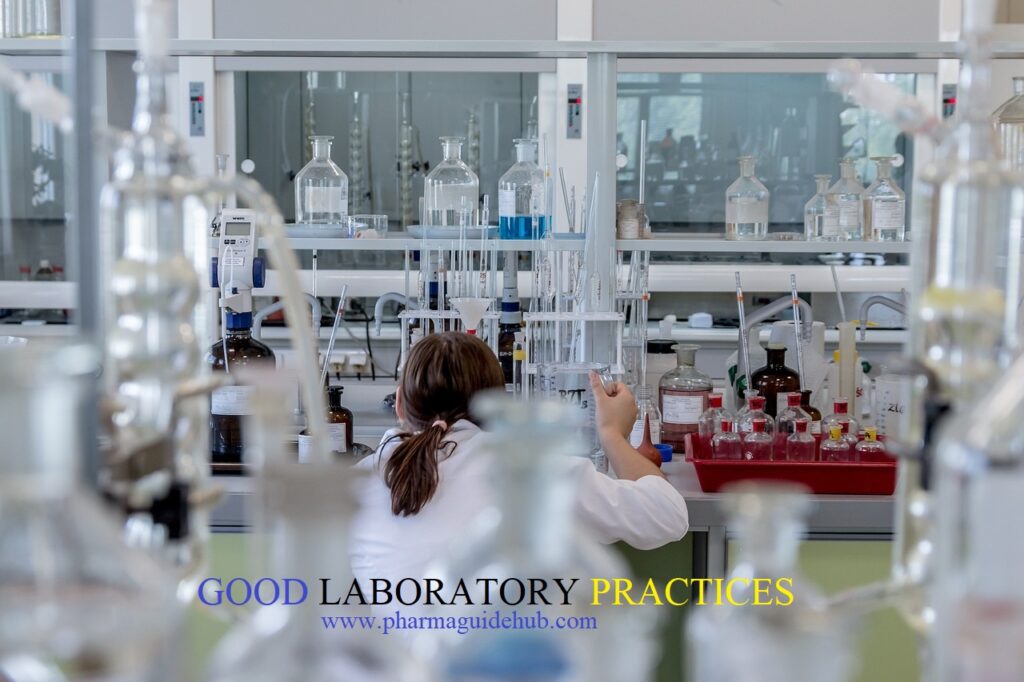
- SCOPE:
This SOP is applicable for Good Laboratory Practices (GLP) in Quality Control Department at {Company Name} {Location}.
- RESPONSIBILITY:
QC Officer/Executive – To follow the instruction as per SOP.
QC Head – Review, technical correction, training and monitoring of SOP.
QA Head – Approval and Implementation of SOP.
- ACCOUNTABILITY:
QA Head Shall be accountable for implementation of SOP.
- PROCEDURE:
- Good Laboratory Practice (GLP), in the context of pharmaceuticals, is a system of guidelines that ensures the quality and integrity of non-clinical laboratory studies. These studies are crucial for testing the safety of drugs before they can be submitted for regulatory approval.
- General Requirement:
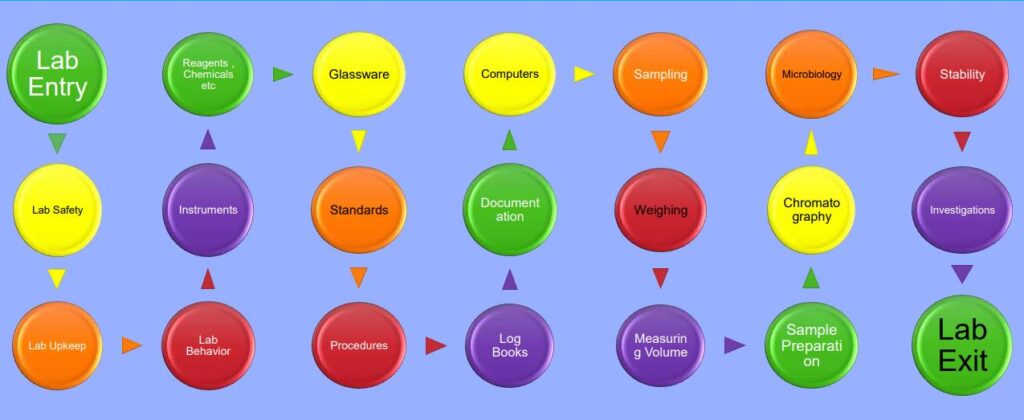
- The Laboratory or the organization of which it is a part must be an entity that is legally authorized to function and can be held legally responsible.
- It is the responsibility of the management to ensure that the Laboratory carry out its testing, calibration, validation and all other technical activities in such a way as to meet Good Laboratory Practices (GLP) requirements.
- Laboratory Management shall have a qualified individual to be known as quality manager or technical manager for carrying out all technical activities and for the implementation of documented quality system.
- The quality manager shall report to the top management directly.
- Premises:
- The laboratory shall be designed, constructed and maintained so as to prevent entry of insect and rodents besides cross contamination.
- Interior surface i.e. walls, floor and ceiling of the laboratory shall be smooth free from cracks and permit easy cleaning and disinfection.
- Adequate provision is made not only for space and equipment for carrying out necessary test but also for utilities like water, power and gas.
- Air ventilation system shall be provided to ensure dust for environment.
- The laboratories shall be provided with adequate lighting and ventilation and if necessary air-conditioning to maintain satisfactory temperature and relative humidity that will not adversely affect the testing and storage of drugs or the accuracy of the functioning of the laboratory equipment and instruments.
- The drainage system facilities shall be such as to facilitate proper maintenance and prevent water logging in the laboratory.
- Table tops shall be constructed with acid alkali and solvent resistant material and shall be smooth and free from cracks as far as possible.
- Adequate space with proper storage conditions in the laboratory shall be provided for keeping reference and working standards and be maintained by quality control department.
- Standard operating procedure (SOP) for the maintenance of reference standards and evaluation of working standards shall be prepared by the laboratory.
- Personal:
- Staff in the laboratory shall possess necessary qualification, proper training and shall have adequate, experience for the assigned duties.
- A training record of all the personnel shall be maintained.
- Head of the laboratory must be of high professional standing with experiences in drug analysis and laboratory management who is responsible for:
- Ensuring the control and maintenance of documents including the quality system as per the requirement of regulatory authorities which involves all raw data, SOP’s, documentation exhibits, protocols, training charts etc.
- Planning and organizing the audit of the quality system and initiation as well as follow up action of the corrective action if any.
- Investigation of technical complaints.
- Taking final responsibilities for recommending and regulatory action in the event of noncompliance of tested samples.
- Equipment:
- The laboratory shall be furnished with all types of equipment as may be necessary for carrying out the different activities within the laboratory.
- The analytical instruments shall be housed in dust-free environment and whenever required, conditions of temperature and humidity shall be maintained and periodic checks on temperature and humidity is made and recorded.
- The instruments, instrument benches and surrounding areas shall be kept clean and tidy at all times.
- Instruments requiring calibration shall be calibrated at regular Intervals.
- Records of such calibration or maintenance shall be maintained.
- There shall be written instruction in the form of standard operating procedures for the operation and calibration of instruments.
- A standard operating procedure for preventive maintenance of machine or equipment or apparatus shall be prepared by the laboratory.
- Class “A” with certificate volumetric glassware (burette, pipettes, volumetric flasks, measuring cylinder etc.) shall be used in laboratory.
- Other equipment such as thermometer, weight box and component of equipment such as timer, thermostatic controller shall be calibrated by authorized competent external agencies.
- Maintenance procedure in the form of standard operating procedures must be prepared and servicing must be performed by the maintenance engineer or specialist.
- Equipment, instruments giving anomalous results or defective must be labeled as “OUT OF ORDER” till they are repaired.
- After instrument is repaired it should be calibrated before use.
- The maintenance of equipment for services like electricity, gas, water and compressed gas shall be handled by competent person.
- Autoclaves must meet the requirements described for operations, safety and validation procedures. The validation carried out by the laboratory shall be recorded.
- Fume Hood: Work involving the evolution of harmful and obnoxious vapours shall be carried out in fume hood.
- The exhaust system of the fume hood shall be checked frequently to ensure that it is order.
- There should be a water drainage system inside the fume hood and shall be checked frequently to ensure that there is no water logging and it is in order.
- Chemical and reagents:
- The storage and handling of chemical and regents shall be done in a manner considering the physicochemical properties of these substances and the hazards involved in their use.
- All reagents and solutions in the laboratory shall be properly identified with a label.
- Reagent or solvent in use shall be labeled with details such as reagent received on, opening date and use before date.
- Standard operating procedure for preparation of stock solution, standard solution preparation and standardization of volumetric solutions must be prepared for the guidance of staff.
- A register shall be maintained by the laboratory.
- Validity of volumetric solution shall be validated.
- Containers of stock solution and of standard solutions shall bear the following details.
- Name of analytical chemist who prepared the solution.
- Date of preparation.
- Each solution shall have “USE BEFORE DATE” depending upon the stability of the solution.
- Standardization record of volumetric solution shall be maintained by the laboratory.
- Good housekeeping and safety:
- General and specific written down instruction for safety shall be circulated to each staff member and the instructions be revised periodically as appropriate i.e. poster displays, and by seminars/conferences.
- Standard operating procedure for safety, housekeeping shall be prepared in accordance with various rules and regulations of Government of India and include the following requirements namely.
- Material safety data sheets (MSDS) must be made available to staff before testing is carried out.
- Drinking, eating and smoking shall not be permitted in the laboratories.
- Food for human consumption shall not be kept in working or storage areas.
- Staff must wear laboratory coats and other protective clothing including gloves and face masks and eye protection whenever required.
- The laboratories shall have adequate first aid kit and fire fighting equipments located at the right place.
- The staff must be familiar and trained with the use of firefighting equipment including fire extinguishers and gas masks.
- The staff must be educated in the first aid techniques, emergency care.
- The staff must be familiar with relevant colour identification codes.
- Microbiologist carrying out sterility test shall wear sterilized garments including headgear, face masks and shoes.
- Protective precautions to be taken in laboratories.
- Eye washers and water shower shall be installed at appropriate places in the laboratory.
- Rubber suction bulbs must be used on manual pipettes.
- Warning precautions and written instructions must be given for work with violent uncontrollable or dangerous reactions i.e. mixing water and acids.
- Appropriate facilities for the collection, storage and disposal of wastes shall be made available.
- Staff must be aware of methods for safe disposal of corrosive or dangerous products by neutralization or deactivation.
- Staff must also be aware about the safety precautions to be adopted which handling corrosive, dangerous or onco products.
- Standards operating procedure for handling collection & disposal of laboratory wastes must be available.
- Maintenance, Calibration and validation of equipment:
- All equipments, instruments and other devices used in the laboratory shall use appropriate methods and procedures for all tests or calibrations.
- All equipment, instruments shall be regularly calibrated and validated.
- The frequency of calibration may differ from instrument to instrument.
- The original equipment manufacturers recommendation along with the experiences of the laboratory staff and the use of equipment per day may be considered while fixing the frequency of calibration.
- Standard Operating Procedures for calibration and calibration schedule shall be prepared by the laboratory for most of the equipment and instrument.
- A log book shall be prepared by laboratory for day to day usage of equipments and calibration status.
- Reference materials:
- Reference materials are necessary for the testing and/or calibration, validation, verification of a sample or of equipments, instruments.
- Type of reference material
- Reference standards
- Working standards
- Primary standards
- Reference standard shall be traceable to agency authorized by Government of India or any other international body.
- Whenever any new reference standards are received by the laboratory, a code number shall be quoted on the laboratory register.
- The laboratory shall prepare working standards for their purity using selected parameters such as identity, loss on drying or water, impurity and assay etc.
- All working standards shall be checked at appropriate intervals or before use to ensure that it has not deteriorated or decomposed during storage. These observations shall be recorded.
- A register pertaining to reference and working standards must be maintained by the laboratory. The following details may be mentioned in the register.
- Source of supply
- Code number of the reference material.
- Date of receipt/Date of preparation.
- Batch number or identification number of the supplying agency.
- Details like assay value, water content or any other information provided.
- Storage condition of the materials.
- Date of expiry/validity if any.
- Date of manufacturing if possible.
- Primary standards shall be prepared by testing the material as per specification.
- Validity of working standards and primary standard is one year.
- All reference materials shall be stored at appropriate storage conditions, those requiring storage below 25°C shall be stored at controlled room temperature, those requiring between 2°C to 8°C shall be stored in refrigerator and those requiring storage in freezer less than -10°C shall be stored in freezer.
- Microbiological cultures:
- Standard operating procedure for maintenance of microbial culture and sub-culture must be prepared by the laboratory.
- If the cultures have become non-viable or mutant, proper procedure shall be followed to destroy these cultures by autoclaving in presence of authorized personnel for biological testing.
- Not more than five passages may be prepared.
- The laboratories shall perform standard biochemical tests on the sub-culture to ensure their viability.
- Standard operating procedure:
- Standard operating procedures are written procedures for different activities being conducted in a laboratory.
- Standard operating procedure shall be user friendly documents and shall included designation of the person responsible for intended activity.
- Standard operating procedure for all various types of activities in the laboratory shall be prepared.
- Protocols and specifications:
- The laboratory shall have a specification archive.
- Current version of all necessary specification and the pharmacopoeias shall be kept as per the requirement of the Act and the rules made there under.
- All updates and corrections must be noted in the master volumes of pharmacopoeias to prevent the use of obsolete section; supplement and addendum shall also be made available in the laboratory.
- For specification of patent and proprietary medicines (non-pharmacopoeia products), test methods shall be prepared and validated by the manufacturer or by the laboratory itself.
- The validated test methods developed by the manufacturer or the laboratory shall stand to the requirement of compendia parameters in regard to its precisions, accuracy, reproducibility, specificity, linearity and ruggedness etc.
- Raw data:
- Raw data refers to the laboratory work sheet, note book or analysis sheet (test data sheet), records there of that may be the results of general observations and other activities.
- The raw data shall include hand written notes, software, computer printouts, dictated observations and recorded data from automated equipment.
- The raw data also includes record on receipt of reference materials, reagent and chemicals, results of environmental monitoring calibration, records of equipments, including work-sheet to read a note.
- A single line shall strike through the data being changed. The analyst making the change shall be identified by his signature with date. The correct information shall be recorded along with the old data.
- In case of automated data collection system, the person responsible shall be identified at the time of data output. The original entry must be saved.
- Data integrity and security shall be maintained and the data shall not be accessible to any unauthorized person.
- Storage and archival:
- The retention samples of finished product shall be retained in proper storage conditions for a period of one year after its expiry.
- The retention samples of raw material shall be retained in proper storage condition for at least one year beyond the expiry date of the corresponding finished product.
- The Laboratory must establish and maintain procedures for the identification, collection, indexing, retrieval, storage, maintenance and disposed of all quality documents.
- All the raw data’s, documentation, standard operating procedures, protocols and final reports are to be retained.
- The archive shall provide a suitable environment that will prevent modification, damage or deterioration and/or loss.
- The conditions under which the original documents are stored must ensure their security and confidentiality.
- Paper documents shall not be kept for long periods under high humidity and raw data in the form of tape and discs are to be preserved with care.
- Bracketing of Standards during Content Uniformity, Assay, Dissolution and Related Substances Test:
- During content uniformity analysis by HPLC, one injection to be made for all test samples. After the completion of five replicate injections of standard, consider the last standard injection as a 1st bracketing standard to calculate the difference factor of bracketing standard, inject five sample injections followed by one standard injection. The difference of area between the 1st bracketing standard (5th standard) and 2nd bracketing standard injection made after five test injections should not be more than 2%, and then inject next five samples followed by again one injection of Bracketing standard. The difference of area between the 1st bracketing standard (5th standard) and the 3rd Bracketing standard injection should not be more than 2%. Similarly continue the testing of other samples if any.
- Ensure that the standard solution is stable throughout the analysis.
- Schematically it is represented as follows:
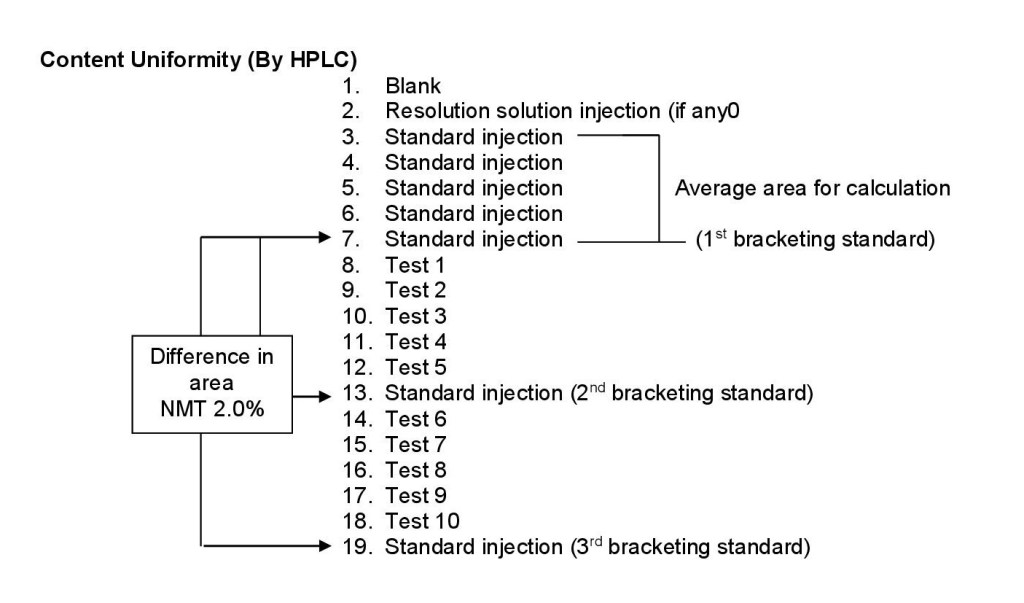
- During assay analysis by HPLC, the tests to be performed by using single solution preparation with duplicate injection. After the completion of five replicate injections of standard, consider the last standard injection as a 1st bracketing standard to calculate the difference factor of bracketing standard, inject two injections from single trail followed by one standard injection. The difference of area between the 1st bracketing standard injection and 2nd bracketing standard injection should not be more than 2%. Calculate assay for the average. Similarly continue the testing of other samples if any, followed by the same sequence of every three batches one bracketing standard.
- Ensure the standard solution is stable, throughout the analysis.
- Schematically it is represented as follows;
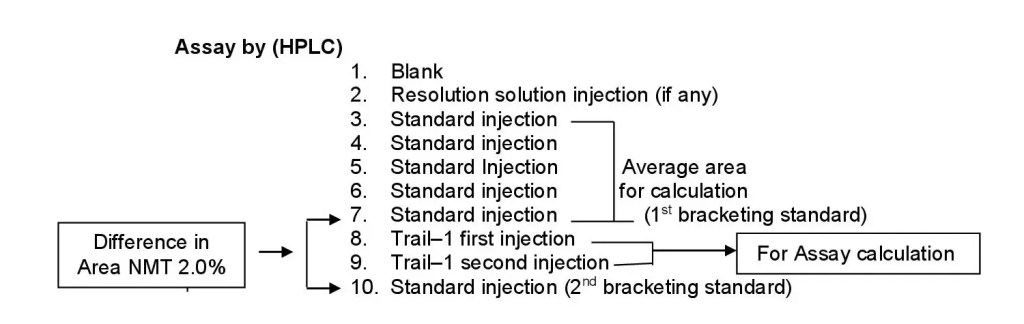
- During dissolution analysis by HPLC make one injection of sample from each vessel. After the completion of five replicate injections of standard, consider the last standard injection as a 1st bracketing standard to calculate the difference factor of bracketing standard, inject the sample injection from six vessels followed by one standard injection. The difference of area between the 1st bracketing standard injection and the 2nd bracketing standard injection should not be more than 3%. Similarly continue the testing of other samples if any.
- Ensure the standard solution is stable, throughout the analysis.
- Schematically it is represented as follows;
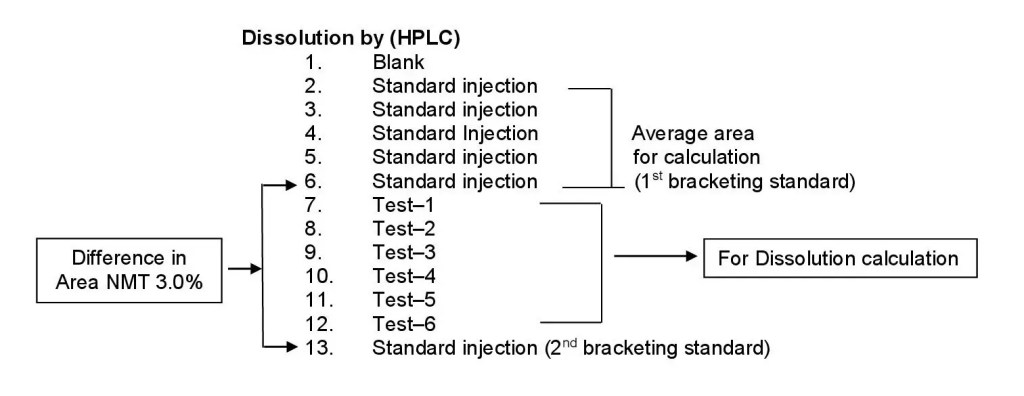
- Daily works distribution:
- All section heads will have working plan of the section.
- Works which shall be performed for next day and/or night shift shall be assigned at the end of shift to the analyst/performer by section heads.
- Samples, Specification, test data sheet shall be made available to analyst by section head before testing is carried out.
- Analyst/Performer shall be entered out time and status of works assigned at the end of completion of his/her shift.
- Section heads shall check the status and give comment on work done by Analyst/Performer on daily basis.
- If section heads shall observe injustice with work by Analyst/Performer, justification should be given by Analyst/Performer.
- Daily works schedule shall be approved by Department Head.
- Microbiology:
- Good laboratory practices in a microbiology laboratory consist of activities that depend on several principles: aseptic technique, control of media, control of test strains, control of equipment, diligent recording and evaluation of data, and training of the laboratory stuff.
- Clean spills immediately according to established protocols and disinfect the area thoroughly.
- Keep bench top uncluttered.
- Minimize traffic and unnecessary movements around the work area (movement can stir up air currents which can carry contaminants into the work area).
- All work with infectious material should be carried out in a specific area, and the material should not be carried throughout or out of the lab unless in a closed or capped container.
- Minimize aerosol generation; if unavoidable, activities should be carried out in a biological safety cabinet.
- Use proper aseptic technique for the transfer and handling or microorganisms and instruments.
- Keep sterile and non-sterile objects separate.
- Minimize exposure to outside air (i.e. keep lids off sterile containers for as little time as possible).
- Avoid contact with non-sterile surfaces and items (i.e. never place lids/caps onto a work surface, hold lids in an opening-down position), and hold open containers at an angle whenever possible to prevent contaminants from falling in.
Media, Reagents Preparation, Storage, Qualification:
- It’s important to choose the correct media or components in making media based on the use of accepted sources or references for formulas.
- The LAL reagent is critical in Endotoxin testing, and must be well controlled.
- When the LAL reagent (lot) changes, the Micro Lab must confirm the labeled LAL reagent sensitivity λ (EU/ml). This is to re-calculate the Maximum Valid Dilution (MVD), which is the maximum allowable dilution of a sample to determine the endotoxin limit.
Laboratory Operations/Housekeeping:
- Safety first. The Micro Lab should practice aseptic techniques during testing in general, to avoid microbial contamination and false positives.
- In the Micro Lab, areas where EM, water, or product samples are handled / incubated must be adequately separated from areas where there are tests that involve live cultures or sub-culturing, microbial ID or investigations.
- Housekeeping must be properly maintained to prevent use of expired or contaminated testing mats.
- Verify cleanliness of work stations, cleared of extraneous or previous test residue, prompt removal of refuse, and clean utensils and equipment
- Laboratory Upkeep – 5 S principle:
- Follow 5 S principles in the laboratory.
- The 5S system is a tool that supports an operating philosophy that emphasizes discipline, efficiency, and attention to detail:
- Sort
- Set in Order
- Shine
- Standardize
- Sustain
- Benefits of 5S:
- Safety
- Employee involvement
- Organization/Efficiency
- Cleanliness
- Space Savings
- Lower inventories
- More consistent experiments
- Faster on-boarding of new employees
- Timely delivery of supplies
- Additional funding
- Sort (Sorting Methodology):
- Perform the initial cleaning of the work area.
- Separate the necessary items from unnecessary items
- Remove unnecessary items from the work area
- Establish a holding area for items (Red tag area).
- Identify items not required at the
- current location, if at all
- Team members evaluate items in Red Tag area
- Dispose of items with team approval
- Set in Order:
- Identify necessary tools, equipment, supplies, etc.
- Determine location for necessary items
- Designate & outline permanent locations for items
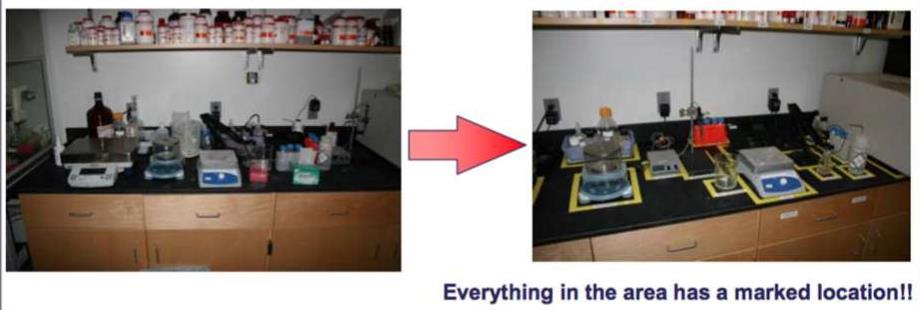
How to set in order:
- Define the major processes performed
- For each process, draw a map of the locations of each activity
- Identify sources of waste and corrective measures
- Position items where they are needed based on frequency
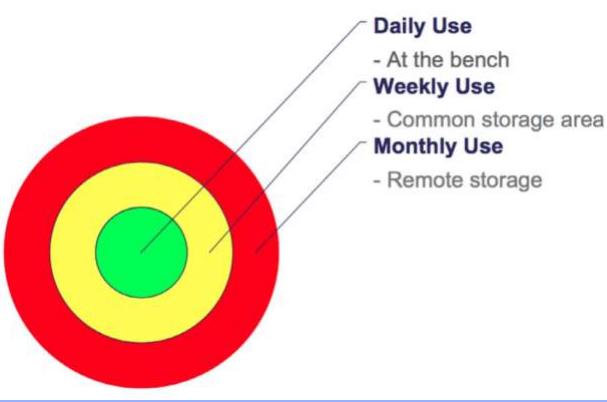
- Shine:
- Clean area thoroughly – Make it shine!
- Clean & inspect areas daily
- Machines & Equipment
- Fix leaks & other problems
- Prevent contamination
- Inspect daily
- Fix potential issues before they become major problems
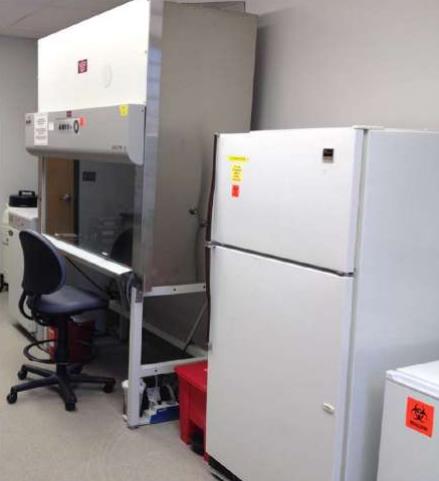
- Standardize:
- Develop SOPs
- Document equipment & processes
- Develop audit schedule and assign tasks to individuals
- Establish a methodology to ensure consistent strategy for 5S implementation
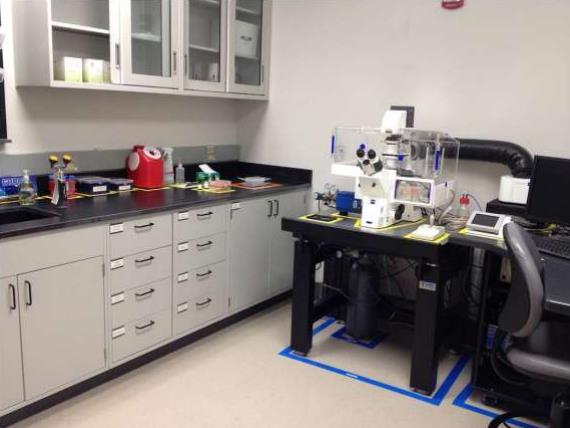
- Sustain:
- Establish procedures on 5 S.
- Maintain established procedures.
- Ensure 5 S is a long term, laboratory wide goal.
- Analyze results, hold team meetings and train scientists on the importance of 5 S.
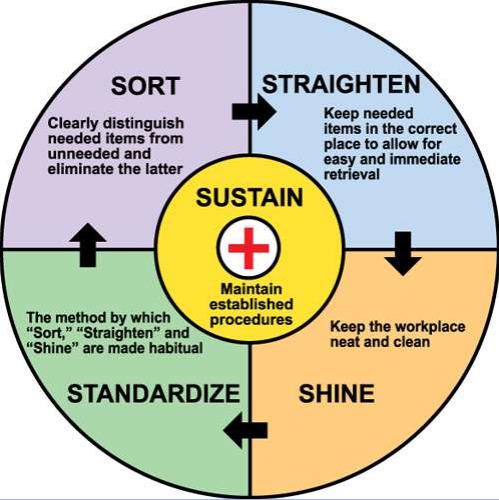
- REFERENCES:
Schedule L-I, Drug and Cosmetics (Third Amendment) Rules, 2008, Ministry of Health and Family Welfare (Department of Health)
- ANNEXURES:
Not Applicable
- DISTRIBUTION:
Controlled Copy No. 01 | : | Head Quality Assurance |
Controlled Copy No. 02 | : | Head Quality Control |
Master Copy | : | Quality Assurance Department |
- ABBREVIATIONS:
Abbreviation | Expanded form |
SOP | Standard Operating Procedure |
No. | Number |
Q.C. | Quality Control |
QA | Quality Assurance |
Dept | Department |
No. | Number |
MSDS | Material Safety Data Sheet |
°C | Degree Celcius |
% | Percentage |
NMT | Not more than |
HPLC | High Performance Liquid Chromatography |
GC | Gas Chromatography |
- REVISION HISTORY:
CHANGE HISTORY LOG
Revision No. | Details of Changes | Reason for Change | Effective Date |
00 | New SOP | Not Applicable | To Be written Manual |