- PROCEDURE FOR VISUAL INSPECTION OF AMPOULES AND PARENTERAL PRODUCTS:
- Visual inspection of parenteral products is a critical quality control step in the pharmaceutical industry. It involves examining filled containers like vials, ampoules, or syringes for any physical defects or abnormalities that could compromise the product’s sterility, safety, or efficacy.
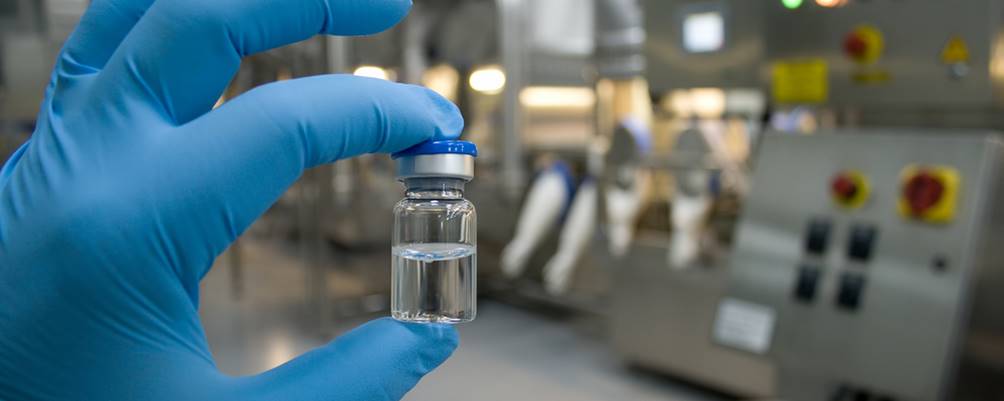
- Requirement of material to perform the inspection procedure:
- Inspection light source with adjustable intensity (preferably with black and white backgrounds)
- Magnifying glass (optional)
- Inspection trays
- Rejection container
- Personal Protective Equipment (PPE) (e.g., gloves, safety glasses)
- Batch records
- Inspection record form
- Prerequisite Preparation:
- Inspector Qualification: Ensure the inspector is trained and qualified for visual inspection of ampoules. Records of training and qualification must be maintained.
- Preparation of Inspection Area: Set up the inspection area with proper lighting (adjustable intensity) and a clean, well-lit workspace with black and white backgrounds.
- Wear PPE: Wear gloves and safety glasses during the inspection process.
- Review Batch Records: Review the batch record for relevant information such as product name, lot number, and acceptance criteria.
- Check the cleanliness of the Visual Inspection / Area Booth and take line clearance from QA department before operation.
- Update the status board of Visual Inspection, as Product Name, Batch No., Mfg. Date, Exp. Date, Stage, sign, Date.
- Unload the parenteral products after Leak Test / Terminal Sterilization and further transfer into plastic trays/carets for visual inspection.
- Inspection Process
- Sample Selection: Select a representative sample of ampoules from the batch according to the sampling plan defined in the batch record.
- Visual inspectors shall collect the trays / carets of filled of parenteral products and hold the specific quantity of specific size as mentioned in Annexure-I at a time in hand for visual inspection and inspect the filled parenteral product in white and black background for NLT 5 seconds each. (In case of Repulse, five-five/single-single/lose to be inspected).
- Inspection Process
- Sample Selection: Select a representative sample of ampoules from the batch according to the sampling plan defined in the batch record.
- Visual inspectors shall collect the trays / carets of filled of parenteral products and hold the specific quantity of specific size as mentioned in Annexure-I at a time in hand for visual inspection and inspect the filled parenteral product in white and black background for NLT 5 seconds each. (In case of Repulse, five-five/single-single/lose to be inspected).
- Inspection Process
- Sample Selection: Select a representative sample of ampoules from the batch according to the sampling plan defined in the batch record.
- Visual inspectors shall collect the trays / carets of filled of parenteral products and hold the specific quantity of specific size as mentioned in Annexure-I at a time in hand for visual inspection and inspect the filled parenteral product in white and black background for NLT 5 seconds each. (In case of Repulse, five-five/single-single/lose to be inspected).
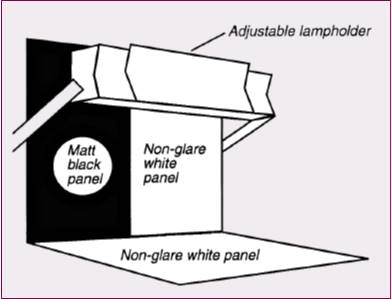
- Illumination at the inspection point by two 13-W / 15-W fluorescent lamps.
- Intensity between 2000 and 3750 lux.
- Individual Ampoule Inspection:
- Pick up an ampoule without obstructing the view with your hands.
- All individual Parenteral Products of Ampoules will be checked for sealing defects, Glass particle, less volume, High volume, Black particles, Fiber, White particle and charring.
- Hold the ampoule against the black background and visually inspect for:
- Clarity of solution: Look for any cloudiness, haziness, or presence of foreign particles.
- Color: Ensure the solution color matches the product specifications.
- Fill level: Verify the fill level is within the acceptable range.
- Container integrity: Inspect for cracks, chips, or other defects in the glass ampoule.
- Seal integrity: Check for any leaks or imperfections in the seal.
- Gently spin the ampoule and repeat the inspection against the white background.
- Use a magnifying glass for a closer inspection of any suspect particles or defects.
- All individual Parenteral Products of Dry powder injection vials will be checked for Air Bubble, Molded Vial, Sealing defects, cracked vial, Less fill weight, High fill weight, Broken Flip off Seal and Empty vial.
- All individual Parenteral Products of Three Piece vials will be checked for Dirty Vial, Vial Without Cap, Mold defect, Broken Ratchet, Improper Sealing, Leaked vial, Surface Particle, Improper Fixing of Cap.
- In case of Repulse Inspect for Less Volume, High volume, Rough surface, De- shaped, foreign particles, Extra plastic, Leakages and Empty.
- Visual Inspection shall be performed under Black and White background separately for NLT five second each to detect the defective of Filled & Sealed Ampoules & Repulse.
- Visual Inspection shall be performed on the Roller rail of Visual Inspection machine (if available) each to detect the defective of Dry powder products.
- Visual Inspection shall be performed of physically check the Individual vial each to detect the defective of Three piece Vial.
- Rejected of Parenteral Products shall be kept in respective compartment of Visual Inspection Rejection Pigeon Box with lock & key system/Respective crates.
- Good Parenteral Products to be collect in trays/carets with status label as “INSPECTED” and that particular are ready for labeling.
- After completion of visual inspection activity, the lock of Rejection Pigeon Box will be opened in presence of IPQA personnel & counts the different type of rejections (or from Respective carets) record in Annexure-II & Annexure-III for Respective Line (For Ampoule and Respules product, rejection data shall be filled in respective BMR only).
- After Every hour of visual inspection, 05 minutes eye rest to be given to all visual inspectors.
- Visual Inspection Defects of Parenteral products as per Annexure-II.
- Annexure – III “Visual Inspectors Rotation Record” can be used on need basis.
- Post Inspection Sampling:
- Mandatory sampling and inspection after 100% visual inspection.
- Sampling plan as per ANSI/ASQ Z1.4 – 2008 (or ISO 2859-1): General Inspection Level – II, Single sampling plans for Normal inspection with an AQL of 0.65%.
- Batch releasing criteria: NMT the specified number of units contains visible particulates.
- Acceptance Criteria and Rejection:
- Ampoules that meet all the defined acceptance criteria are considered acceptable.
- Ampoules with any defects exceeding the predefined limits are rejected and placed in the designated rejection container.
- Investigate the cause of rejections and document corrective actions taken.
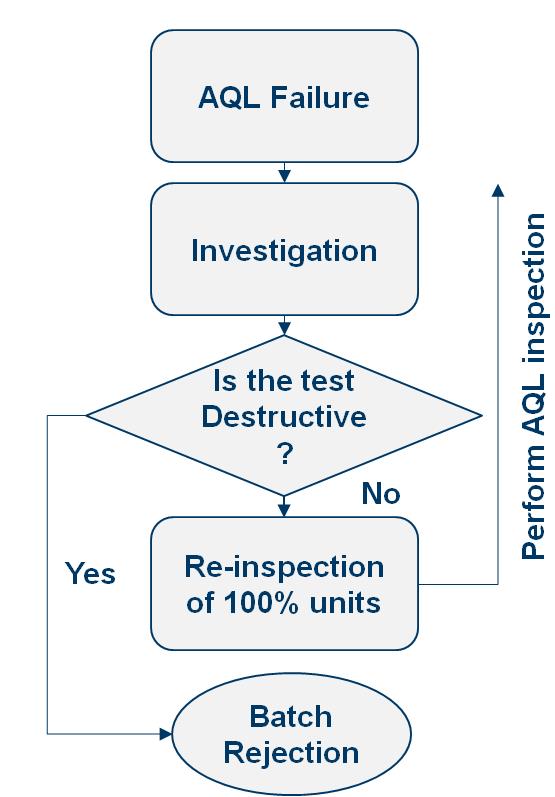
- ANNEXURES:
ANNEXURE No. | TITLE OF ANNEXURE |
Annexure-I | Sufficient visual quantity |
Annexure-II | List of Defected Parenteral Products |
Annexure-III | Visual Inspectors Rotation Record |
ANNEXURE – I
SUFFICIENT VISUAL QUANTITY
S. No. | Required Product for Visual Inspection | Quantity |
1 ml Ampoule | 04-06 nos. | |
2 ml Ampoule | 03-05 nos. | |
3ml Ampoule | 02-04 nos. | |
5 ml Ampoule | 02-04 nos. | |
5 ml Repulse | Five-Five/Single-Single/Lose | |
10 ml DPI Vial | Online Roller Rail of Visual Inspection Machine | |
5 ml & 10 ml Three Piece Vial | Single-Single Vial |
ANNEXURE – II
LIST OF DEFECTED PARENTERAL PRODUCTS
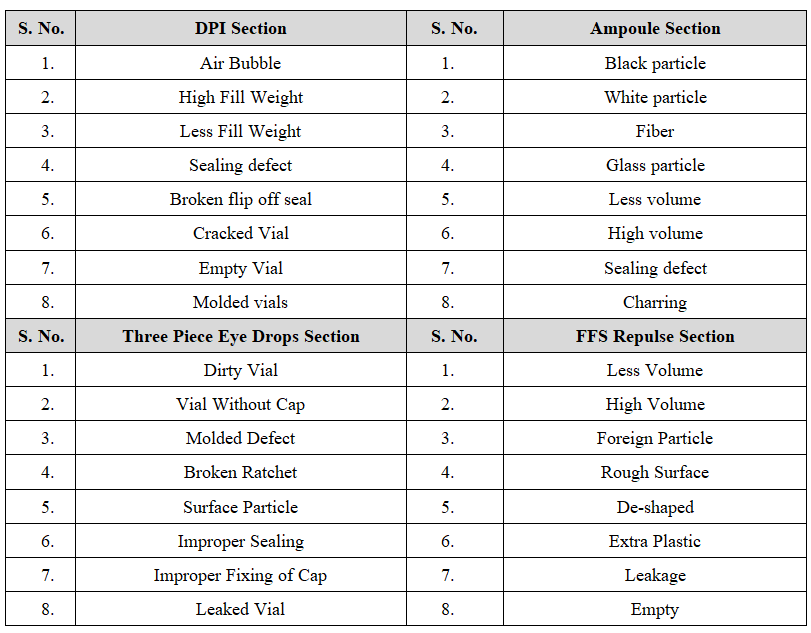
ANNEXURE-III
VISUAL INSPECTORS ROTATION RECORD
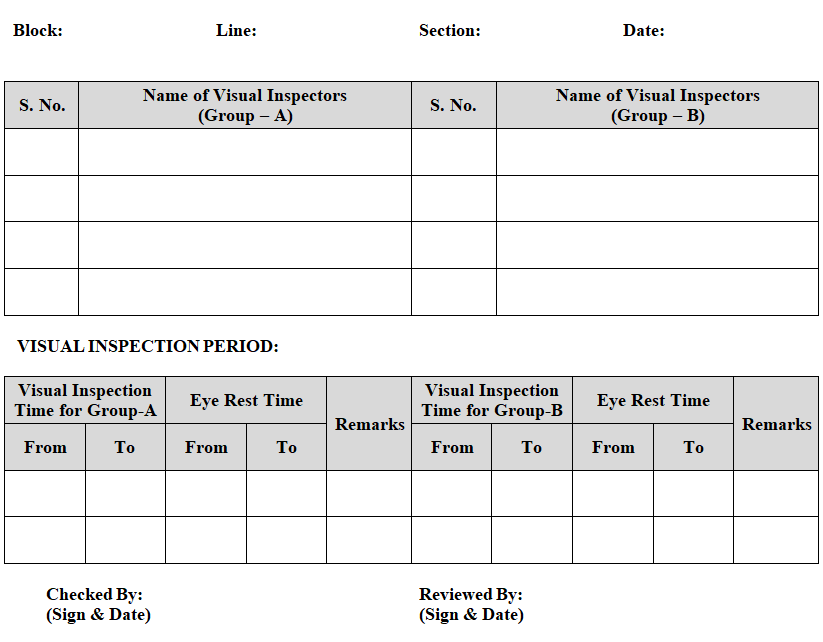