SOP of SOP (SOP on SOP in Pharmaceutical)
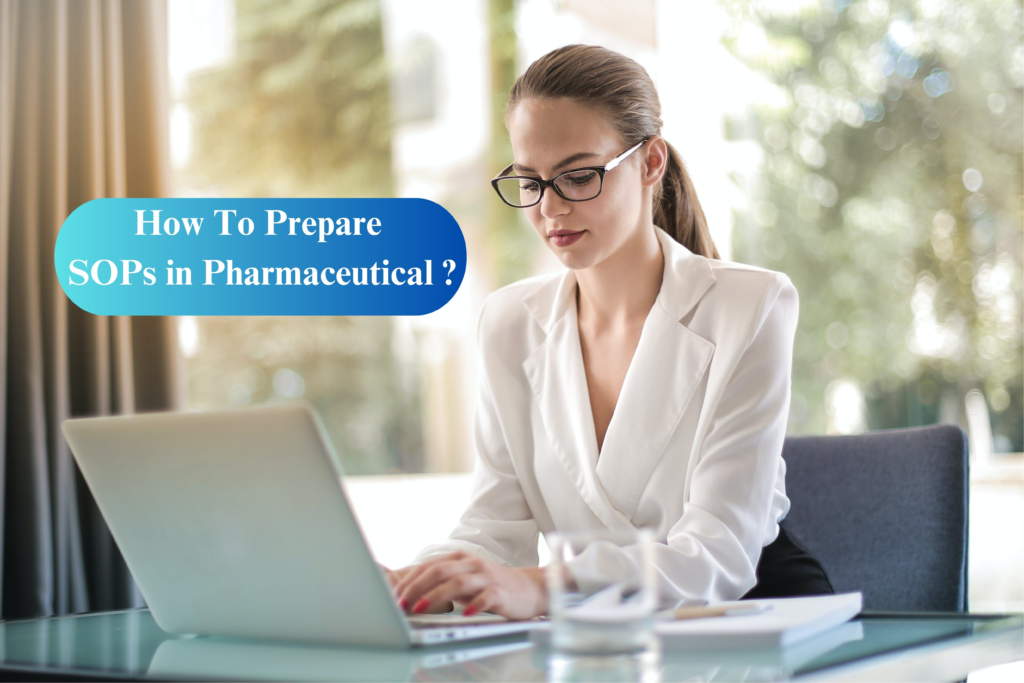
OBJECTIVE:
To lay down a Procedure for writing the Standard Operating Procedure for Implementation of Standard Policies, Work Instructions, Standard Procedures of Operation and Standard Practices.
SCOPE:
This SOP is applicable for all concerned department for Preparation, Issuance, Review, Approval, Distribution, Control, Retrieval, Revision, Storage, Destruction and Discontinuation/Deletion of all Standard Operating Procedures at {COMPANY NAME} {Location}.
RESPONSIBILITY:
Concerned department (Officer/ Executive) shall be responsible for preparation of SOPs.
Department Head shall be responsible for the review of SOPs.
Head QA shall be responsible for the Approval of SOPs.
Officer/Executive QA or above shall be responsible for control, storage, issuance, retrieval, destruction and discontinuation/deletion of SOPs.
ACCOUNTABILITY:
Head QA and Concern Department Head is accountable for the implementation of SOPs.
PROCEDURE:
PREPARATION OF A NEW SOP:
New SOP shall be prepared due to the following reasons:
- To comply the cGMP and regulatory requirements.
- Provide more clarity while performing the operations.
- Change in Process, Procedure and Inclusion of New Equipment or Facility.
- To introduce additional control on process.
- To comply with the audit findings.
For writing SOPs, all Departments shall follow following Guidelines / Instructions:
The SOP shall be written in English Language by using Microsoft Word typing.
SOP shall be initiated by User Department. The person directly supervising the Operation or Activity shall initiate the New SOP / Revision of SOP.
SOP shall be written after thorough understanding of the Procedure. The author of the SOP shall have adequate knowledge, training, and experience in the related areas of operations.
The SOP shall cover all activities of Operation in order and area of application mentioned in Scope.
Click the link for download word file copy of this document:
https://pharmaguidehub.com/product/sop-of-sop/
The related Diagrams, Flow Charts, Pictures (wherever it helps to understand the procedure better) and reference to other related SOP or Documents shall be made part of the SOP to clarify the procedure of SOP.
The procedure of SOP shall have reference of related document such as Current Good Manufacturing Practices, Manuals (Equipment, Instrument and Machine etc.), Pharmacopoeia, and Guidelines published by concern Regulatory Authorities.
Initiator shall check the completeness of draft SOP and send the hardcopy to the concerned Department Manager / Operating Manager (who would be directly affected by the SOP) for review.
The reviewer shall check the draft SOP for accuracy of the subject matter & logical sequence of instructions.
On receipt of the comments (if any), the same shall be reviewed and incorporated in the SOP, if agreed.
The draft SOP after completion of checking and incorporation of comments or suggestions as agreed, shall be destroyed, this shall be done in Concerned Originating Department.
The Soft Copy of final SOP shall be transferred to QA Department and the soft copy in Originating Department shall be deleted.
Master Copies of all SOPs shall be printed in QA Department only.
SOPs should be handled with care and should not be Spoiled or Torn.
No manual correction shall be made in Approved Copy.
Photocopy of Controlled SOP shall not be used for execution in any Department.
Procedure for new SOP initiation
For new SOP, user department will raise a request/ for New ‘SOP Initiation Form’ to QA.SOP initiator shall record relevant details in “New SOP Initiation Form / Format Initiation Form (SIF)” as per Annexure-VIII (Format No. QA-001/F08-00), attach the draft SOP along with this form and forward it to the concerned Department Head for review.
QA Executive shall assign SIF number as ‘SIF/YY/XXX’ to the “New SOP Initiation Form (SIF)”, where;
- First three character ‘SIF’ denotes ‘SOP Initiation Form’,
- 4th character ‘/’ is a forwarding slash,
- 5th & 6th character ‘YY’ represents last two digit of current year,
- 7th character ‘/’ is a forwarding Shash and,
- 8th, 9th & 10th character ‘XXX’ denotes sequential serial number of the SOP initiation forms.
QA shall maintain a logbook/ or ‘SIF’ as per Annexure-XI (Format No. QA-001/F11-00).
Draft SOP shall be reviewed by the concerned Department Head/Document In-Charge, for accuracy of subject matter as well as logical arrangement of data & text.
SOP number shall be assigned by QA Department as per below given procedure. Records shall be maintained in “SOP Numbering Register” as per Annexure-IX (Format No. QA-001/F09-00).
Click the link for download word file copy of this document:
https://pharmaguidehub.com/product/sop-of-sop/
Note: If any SOP with similar procedure exists or if the SOP is under revision, QA department shall inform the same to user and no SOP number shall be issued. Further appropriate action shall be decided by User Department with the consultation of QA Department.
SOP number register shall be maintained department wise by the QA department as per annexure-IX.
Storage of SOP (Master Copy / Soft Copy):
All Master Copy / Soft Copy of Approved SOPs shall be stored in QA Department and Data Backup shall be kept in Information Technology (IT) Department.
SUBMANAGERING OF A SOP:
The SOP shall contain following Submanagerings:
- Objective
- Scope
- Responsibility
- Accountability
- Procedure
- References
- Annexure
- Distribution
- Abbreviations
- Revision History
PROCEDURE FOR WRITING SOP IN LOCAL LANGUAGE:
SOP’s may be additionally prepared in local language for easy understanding of the support functions, wherever required
Selected English SOPs shall be directly translated into Local Language Version.
The SOP shall be prepared as per above mentioned procedure
In case of any difference in the text matter, English Version of the SOP shall be considered as final.
LAYOUT OF SOP:
SOP Format Considerations:
All SOPs shall contain Managerer, Footer and Body. SOP Format shown in Annexure-I.
All pages shall contain Sign, Date, Name & Designation in the column provide in footer part.
SOPs (Master Copy) should be printed on A4 size Off-white Executive Bond Paper 70 or 100 GSM by using “Times New Roman” Font with black ink or colored print as per requirement.
If required color print of SOP can be given, SOP which are having photograph or picture color print can be given. Manual or module can be given on color print.
Printing should be done on one side of paper.
Paper Width 8.5”, Height 11.5” (Paper Size Custom) & Margin Top, Left, Right 24pt, Bottom Margin 31pt, gutter 0” and paragraph spacing one ENTER (before and after).
All the points in the SOP shall be numbered sequentially and sub paragraph of the SOP be also numbered sequentially with an incremental number derived from the Managering number.
All SOP contents shall be covered by Single Borderline (Line width ½ pt).
LINE SPACING:
- The Line Spacing between two points or title & subtitle shall be single and font style shall be Times New Roman 12 font.
- From left side of page there shall be 0.13” of space between margin line and increasing aligned number.
FONT SIZE OF MANAGERER, FOOTER & BODY CONTENTS:
NAME OF CONTENT | FONT SIZE |
MANAGERER: | |
Name of the Organization | 16 Bold & Capital |
Location ({Company Location}) | 12 Normal & Capital |
NAME OF CONTENT | FONT SIZE |
Logo with {COMPANY NAME} (On Left Hand Side Corner of The Page) | Logo– Height-0.75”& Width-0.65” |
Restricted Circulation | 08 Capital & Bold |
Standard Operating Procedure | 12 Bold & Capital |
Title of SOP | 12 Bold & Capital |
SOP No. (Managering) | 12 Normal & Bold |
Copy No. (Managering) | 12 Normal & Bold |
Revision No. (Managering) | 12 Normal & Bold |
Supersede SOP No. (Managering) | 12 Normal & Bold |
Department (Managering) | 12 Normal & Bold |
Effective Date (Managering) | 12 Normal & Bold |
Revision Date (Managering) | 12 Normal & Bold |
Page No.(Managering) | 12 Normal & Bold |
SOP No., Revision No., Supersede SOP No., Department and Page No. | 12 Normal & Unbold |
FOOTER: | |
Prepared, Reviewed & Approved By | 12 Normal & Bold |
Sign. , Date, Name | 12 Normal & Bold |
Format No. | 09 Capital & Unbold |
BODY: | |
Paragraph Main Managering | 12 Bold & Capital |
SubManagering | 12 Normal / Capital & Bold |
Table Managering | 12 Capital / Normal & Bold |
CONTENT OF MANAGERER AND FOOTER:
Managerer:
The Managerer of SOP shall have the Name of Organization (Including Name of Location). Managerer shall have the “Logo” of Organization in Left corner on top, and Restricted Circulation on right corner in font size of 8 followed by “STANDARD OPERATING PROCEDURE” in centerwritten in Bold and Capital letter of font size 12 as shown in Annexure-I.
Title:
The “TITLE” of the SOP shall be written in bold and capital letter of font size 12.
SOP No.:
Numbering System of SOPs:
Each SOP shall be given a Unique Number, once number is allotted to any SOP; the same number shall not be assigned to any other SOP.
All SOP Nos. shall contain Six Alphanumeric Characters (Two Alphabets, Three Numeric and One Separators).
For Example the First SOP of QA Department shall be numbered as QA/001
First 2 characters ‘QA’ indicate the name of Department i.e. Quality Assurance.
3rd character ‘/’ is Separator and 4th, 5th and 6th characters are numeric digits ‘001’ indicating the Serial Number of SOP.
SOPs Numbering System shall be followed as mentioned below:
The SOP No. Shall be given as: XX/NNN
Where:
XX | : | Indicates Department Code |
/ | : | Forwarding Slash |
NNN | : | Indicates Serial No. |
LIST OF DEPARTMENT CODE
S. No. | DEPARTMENT | CODE |
1 | Quality Assurance | QA |
2 | Quality Control | QC |
3 | Microbiology | MB |
4 | Production | PD |
5 | Packing | PK |
6 | Warehouse | WH |
7 | Engineering | EG |
8 | Environment Health & Safety | ES |
9 | Human Resources | HR |
10 | Accounts | AC |
11 | Information Technology | IT |
12 | Purchase / Commercial | PU |
13 | PPIC | PP |
Supersede SOP No.:
In the left hand side of the Managerer, Supersedes shall have the History of the previous Revision No. and shall start from Nil.
Revision No.:
The new version of SOP shall be written, as ‘00’. If it is a revision then subsequent Revision No. shall be given as ‘01’, ‘02’ etc.
Department:
Write the name of the department for which SOP is applicable.
Effective Date:
Effective Date shall be assigned in the form of DD/MM/YY.
For Example: 01/02/23
This date mentions the day; SOP is implemented for any particular operation. There shall be within Seven Days between Date of Approval and Effective Date for the training of the particular SOP.
For Example: If any SOP is approved on 01/02/23, Effective Date shall be 08/02/23.
Revision Date:
The normal review period shall be Two Years from the effective date of the SOP.
For Example: If any SOP having effective date “10/02/23” its review date shall be “09/02/25”. Effective date and revision date shall be mentioned manually.
Square Space for Stamping:
“MASTER COPY” stamp shall be stamped in space provided in the Managerer part on the right hand side of the page.
Page No.:
The Page Number shall be mentioned in ‘X of Y’ format.
For Example: If a SOP contains 30 pages then the first page of the SOP shall be 1 of 30 and the second page shall be 2 of 30 respectively.
Footer:
Footer shall contain following Manage rings:
Prepared By:
Shall be signed by Executive / Designee who initiates the SOP along with Date and Name.
Reviewed By:
Shall be reviewed by Sr. Executive/ Designee and signed along with Date and Name.
Approved By:
Shall be approved by QA Head / Designee. Designee shall be Manager and Assistant Manager can be signed along with Date & Name.
Format No.:
09 Normal & Capital font size printed on the left corner of the page after Footer, out of page border and shall be printed as QA-001/F01-00 on all pages of the SOP.
Sign: Shall be signed in person by Blue Ink Ball Point Pen.
Date: Date shall be in the form of DD/MM/YY (Date/Month/Year).
Name: Full Name of person who signs the SOP.
All Signatures, Date, Name on Master Copy shall be written by in person with Blue Ink Ball Point Pen.
CONTENT OF THE BODY:
Objective:
Write here the reason for preparing the SOP in one sentence or maximum two sentences starting with a letter ‘To lay down’.
Scope:
This Section defines the applicability of the SOP and also specifies Departments, areas or sections to which this SOP shall be applicable. Start the SOP sentence with ‘This SOP is applicable’.
Click the link for download word file copy of this document:
https://pharmaguidehub.com/product/sop-of-sop/
Responsibility:
Write here the designation of the Person / Persons who are directly responsible for the operations mentioned in the ‘Objective’ of the SOP.
Accountability:
Write here the Head of the Department and QA Head who is accountable for compliance of the SOP.
Procedure:
Write the Procedure / Method in short sentences. Do not write the instructions in long paragraphs; subManagering shall be given, if required.
Mention all the checks to be carried out, records to be maintained, frequency of various operations, checks and special precautions, if any.
References:
Mention a list of references or any other guidance documents based on which the SOP has been prepared. If there is no reference for the SOP, mention ‘Not Applicable’ under this subManagering. Do not use abbreviation NA.
Annexure:
Enclose all the Annexure with SOP if applicable and also mention a list of all Annexure enclosed in the SOP. If there is no Annexure in the SOP, mention ‘Not Applicable’ under this subManagering. Do not use abbreviation NA.
If any training record is attached with SOP it shall be mentioning as enclosure.
Procedure for making the Annexure:
All Formats of the SOP shall be attached as Annexure.
All the Annexure relevant to the SOPs shall be attached as a part of specimen, and its reference shall be mentioned in the SOP.
Each Annexure shall be numbered sequentially by Roman Numbering System as per order of attachment.
First Annexure of any particular SOP shall be numbered as Annexure-I.
New Annexure shall be made as per Annexure-II.
Each Annexure shall have unique Format Number which contains Managerer, Body and Footer. Font size of Annexure contents is mentioned below:
FONT SIZE DETAILS OF ANNEXURE CONTENT:
CONTENT OF ANNEXURE | FONT SIZE |
MANAGERER: | |
Numbering of the Annexure | 12 Bold & Capital (Upper Case) |
Logo with {COMPANY NAME} on the Left Hand Corner of the Annexure | Logo– Height-0.75”& Width-0.65” |
{COMPANY NAME} | 16 Bold & Capital |
Location | 12 Normal & Capital |
Department Name (If Required) | 12 Bold & Capital |
Title | 12 Bold & Capital |
BODY: | |
Subtitle | 12 Bold & Capital |
Actual Recording / Documenting in the form of Table or any suitable manner as per requirement. | |
Frequency of recording and limits of the parameters to be mentioned wherever applicable | |
FOOTER: | |
“Format No.:” | 09 Normal & Capital out of Page Border |
“Page No.” in the form of “X of Y ” | 09 Normal out of Page Border |
Numbering System of Formats :
Each Format No. (XX-YYY/FZZ-NN) shall have unique Format No. for identification and control. Once a number is allocated to any Format, the same number shall not be repeated to any other format & Vice- Versa.
Each Format No. shall consist of 17 Alphanumeric Characters (Six Alphabets, Seven Numeric and Four Separators).
Where:
XX | : | Department Code |
/ | : | Forwarding slash |
YYY | : | SOP No. |
FZZ | : | Format No. |
– | : | dash |
NN | : | Revision No. |
For Example: First format No. for Production SOP, SOP No. PD/001 shall be numbered as PD-001/F01-00.
Where:
First 6 characters indicate the SOP to which the format pertains (Excluding 3rd character use ‘-’ in place of ‘/’).
7th character is Slash ‘/’ for Separator.
8th character ‘F’ indicates for Formats.
9th and 10th Numerical characters ‘01’ indicate Serial Number of the format.
11th character is hyphen ‘-’ for Separator.
12th and 13th Numerical characters indicate Revision Number of that particular format which starts with ‘00’ and there shall be increment of One Digit after every Revision.
The Format No. of new SOP shall start with ‘01’.
In case of Hindi SOPs, the Format / Annexure attached as a reference to the SOP shall be that of English Version and numbering system shall be same as English version.
In case of Computer-Generated Format, it shall have same Format No. as mentioned in Annexure / Format of SOP.
Actual recording can be made in the form of:
- Duplicate / Triplicate Books / Bound Books
- Ledgers
- Bound Book
- Computer Print outs
- Registers
- Pre Printed Forms
All Register / Duplicate / Triplicate Book / Computer Print outs / Ledgers / Pre Printed forms shall have Format No. on left lower corner same as of Annexure in SOP.
In case of Bound Book (Registers, Log Books & Ledgers) of Annexure / Formats / Register Pages shall have the page numbering followed by XXX form.
Revision of Formats and Annexure:
Any changes in the Format shall be handled through Change Control Procedure.
Revision of format shall be along with a revision of SOP.
After reviewing the current version of format, QA Department shall retrieve all the Obsolete Formats and replace with the current version.
QA Department shall retrieve all the Controlled Copy of Cancelled Formats of various Departments and destroy as per SOP of destruction. The details of destruction shall be recorded in the Annexure-III.
Distribution of a SOP:
The SOP shall be distributed to respective departments by QA and a Distribution list shall be maintained as per Annexure-III. Additional Copy (if required) shall be issued as per Annexure-IV.
QA shall put the ‘Copy No.’ on each SOP distributed to different departments, which is mentioned in the Managerer of SOPs with Black Ink Ball Point Pen.
This contains the list of copy which is distributed to different departments with their respective Copy Number.
The Revised SOP shall be distributed only after recall of Superseded SOP.
Abbreviations :
This Part of the SOP shall contain full form of any abbreviations which shall be used during writing a SOP (For e.g. SOP = Standard Operating Procedure).
If there is no Abbreviation in the SOP, mention ‘Not Applicable’ under this Submanagering.
Revision History:
Any Change / Revision in the SOP shall be updated and should be mentioned in Change History Log with summarization of all changes and reason for changes with the date of change being effected.
Format of Change History Log is shown below:
CHANGE HISTORY LOG
Revision No. | Details of Changes | Reason for Change | Effective Date |
TRAINING OF SOPs:
Specimen of Training Copy stamp is shown below:
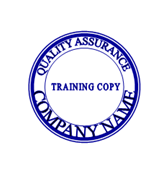
Once the SOP is approved, Document in-charge shall stamp on the top center of the Photo-state of the approved SOP in blue color as “Training Copy” on each page of SOP.
User department shall impart training to the person(s) directly involved in the activity to the concerned supervisor/ in-charge and record the training as per respective SOP and training of cross functional SOP’s shall be given to the departments effected by the SOP.
There shall be a within 7 days between date of Approved and Effective Date, and these days shall be used for training of SOP.
Training of SOP shall be given to all concern Departments before distribution.
Training of SOP shall be given by Approved Trainer.
After training of SOP, the training shall be recorded in SOP training record as per respective SOP and the photocopy shall be made enclosure of the SOP.
ISSUANCE & CONTROL OF SOP’s:
Master list of SOP of all departments shall be prepared by QA officer/executive as per Annexure-VI on behalf of approved SOP index of respective department.
Master list of SOP shall be retained in QA department.
The list of SOPs shall be updated every month (end week of the month + 7 days) or whenever required, manual corrections shall not be allowed in this list.
In case of discontinuation of the existing practice, the SOP may be discontinued; however the same SOP No. shall not be allotted to any newly prepared SOP.
The deletion of the SOP shall be initiated by the Originating Department through Change Control.
Head QA/Designee shall assess the impact of deletion of the SOP on the GMP system and authorize the deletion.
All Master Copy of SOP shall be stamped as “MASTER COPY” in Red ink in square space provided in Managerer (on all the pages).
Specimen of Master Copy stamp is shown below:
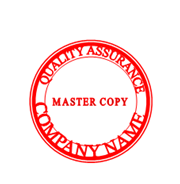
The user copy of SOP shall be distributed by making photocopy copies of the Master Copy and shall be stamped as “CONTROLLED COPY” in Green Ink (on all pages of SOP).
Controlled Copy stamp shall be always in the right upper corner of the page.
Specimen of Controlled Copy stamp is shown below:
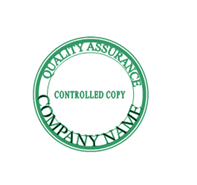
At the time of issuance, QA officer/executive shall assign a copy number manually in the space provided in Managerer section of the respective SOP after taking required photocopies for the distribution as per requirement. (Copy No. shall not be assigned to the master copy).
QA officer/executive shall put ISSUED BY QA stamp in Purple color along with his sign. /date in blue ink ball point pen on top left hand corner on front page of each respective SOP.
Specimen of ISSUED BY QA stamp is shown below:
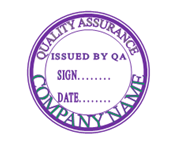
Copies of SOPs issued for display shall be stamped as “DISPLAY COPY” in Blue ink on right corner, below Footer on front page of respective SOP.
Specimen of Display Copy stamp is shown below:
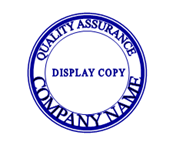
The Copy of SOP that is meant only for Information / Reference purpose shall be made by photocopy of Master Copy.
In case, if any SOP is submitted to the external agencies (i.e. Regulatory, Customers / Partners etc.) a photocopy of master copy shall be made by QA and shall be stamped as “UNCONTROLLED COPY” in Blue ink on left corner of the page below footer on all pages.
Click the link for download word file copy of this document:
https://pharmaguidehub.com/product/sop-of-sop/
Specimen of Uncontrolled Copy stamp is shown below:
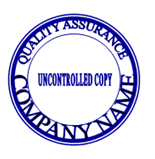
If Soft Copy of SOP is forwarded it shall be submitted as “Read only” protected PDF format.
Revision of SOP shall be regulated through SOP of Change Control Procedure. The Obsolete Copy shall be stamped as “OBSOLETE COPY” in Black Ink in the Left Upper Corner of all the pages.
Specimen of Obsolete Copy stamp is shown below:
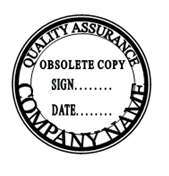
The Master Copy of SOPs which are discontinued or which are cancelled due to implementation of any new SOP shall be stamped as “CANCELLED COPY” in Black Ink at the Left Upper Corner of all the pages.
The details of destruction shall be recorded in Annexure-III.
The specimen of Cancelled stamp is shown below:
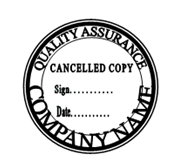
All the recalled copies shall be collected by QA Department and shall be destroyed with the help of Paper Shredder for disposal.
Destruction of Cancelled / Obsolete SOPs shall be recorded in record as shown in Annexure-III.
The QA Department shall maintain the records of destructed SOPs.
REVISION OF SOP:
The normal review period shall be Two Years from the effective date of the SOP. If any change is required in the SOP, same can be done at any time during the period after due approval of Change Control.
At the end of two years, the SOP shall be reviewed.
QA shall inform to concern Department Manager prior 30 days for revision of SOP which is to be Review.
If no change observed during periodic review then concern department officer/executive shall send request for revalidate the respective SOP as per Annexure-VII to QA dully signed by user department Manager.
QA Head or his designee shall review the SOP and if found satisfactory that no change is required then QA officer/executive put stamped as “REVIEWED (No Change Made)” in Blue Ink at Managerer in center on front page of the Master SOP and shall be signed by Blue Ink Ball Point Pen.
Revalidation period of that particular SOP shall be valid for further 2 years until and unless any change is incorporated during this period.
The reviewed (No Change Made) stamp shall be used on the Master Copy and same shall be photocopy, stamped as “Controlled copy” or “Display copy” for further use or as per requirement.
If further no change observed in the next review before date of revalidated period of that particular SOP then the respective SOP shall be revised through change control procedure. A subsequent revision no. shall be allotted to that particular SOP.
The generation and approval of the revised SOP shall be done as follow:
- Original SOP (first edition) shall have revision number 00 & supersedes Nil.
- First revision shall have revision No. 01 & so on.
- Supersedes for first revision of SOP No. QA/001 shall be QA/001-00,
Where:
“QA/001” indicates the respective SOP No.
“/” Forwarding slash.
Last two digits “00” indicates the Supersedes No. of existing SOPs.
The revision No. & supersedes shall be mentioned in the designated cell of the Managerer of the SOP.
Specimen of reviewed stamp is shown below:
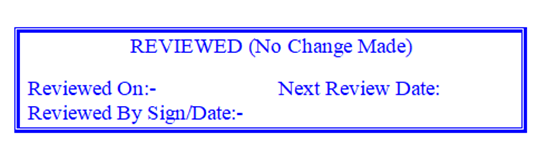
If any change is required in the SOP, the revision of the SOP shall be made after “Change Control Approval”.
The Revised SOP shall have next Revision No. and change made in SOP shall be recorded in Change History Log.
In normal course the SOPs can be reviewed Before One Month from the due date of review.
The Department making a change in the SOPs shall submit the necessary Training Records or the supportive Validation data to QA Department along with the SOP.
The Department making a change in the SOPs shall submit the necessary Training Records or the supportive Validation data to QA Department along with the SOP.
RETRIVAL / DESTRUCTION OF SOP:
QA Officer / Executive shall be responsible for retrieval of the previous version of SOPs before issuing revised copy.
All the retrieved Controlled / Display Copies shall be recorded in format as shown in Annexure-III and destroyed by Paper Shredding Machine.
All Obsolete / Cancelled SOP (Master) shall be preserved for Five Years from the date on which it was made Obsolete / Cancelled and thereafter it may be destroyed.
QA shall destroy the Obsolete / Cancelled / Retrieved copies by Paper Shredding.
For new SOPs, distribution list shall be developed in consultation with Originating Department.
The Manager of the SOP Originating Department shall also provide the list of copies required in his / her Department.
The Manager of User Department shall send the request for the additional copies (if required) for any SOP to QA Department as per Annexure-IV.
The distribution, of the SOP shall be carried out by QA only.
The extension period of SOP as mentioned shall be reviewed as per procedure mentioned in above steps and for its issuance all other distributed controlled or display copies shall be retrieved and destruction to be done as per procedure.
Discontinuation/ Deletion of SOP
In case of discontinuation/deletion of an existing Standard operating procedure, existing SOP shall be discontinued/deleted and recorded as per the Annexure-X (Format No. QA-001/F010-00). However, same SOP number shall not be allotted to any newly created SOP.
Discontinuation / deletion of SOP shall be initiated by Executive originating department, as per Annexure-X (Format No. QA-001/F10-00).
Head QA shall assess the impact of deletion of that SOP, on cGMP system and accordingly authorize the deletion.
QA shall initiate the discontinuation / deletion of SOP as per Annexure-X and accordingly Master list of SOP’s shall be updated.
PREPARATION, DISTRIBUTION & RETRIEVAL OF SOP INDEX:
User department officer/executive shall prepare SOP index of their respective department SOP’s as per Annexure-V and get it reviewed from their respective department Manager & then forward the same to QA department for approval.
Head QA shall approve the SOP index.
Signing on the respective SOP index shall be as per below mentioned procedure.
User department Officer/executive shall sign. on prepared by column space provided in respective SOP index.
User department Head/Designee shall sign. on reviewed by column space provided in respective SOP index. If only one person is available in respective department then QA Executive / Sr. Officer shall sign. along with date in reviewed by column.
Head QA or his designee shall sign. on approved by column space provided in respective SOP index along with his sign. /date.
After approval of respective department SOP index, QA officer / Executive shall affix Master Copy stamp in Red color in Square space provided in Managerer of the respective SOP index.
QA officer/executive shall take Photocopy of the respective department SOP index as per user department requirement from the master copy. All photocopies shall be stamped as Controlled copy on the right upper corner on all pages of SOP index. Photocopies should be legible & clear.
QA officer/executive shall take receiving sign of respective department officer /executive or above on issuance record of SOP index as per SOP No. QA/001at the time of issuance.
SOP’s index shall be updated and reviewed by user department Executive/Designee at the frequency of one month (end week of the month + 7 days) or as and whenever required w.r.t master SOPs.
Updated respective department SOP index shall be issued to the user department by QA officer/executive only after successfully retrieval of previously issued SOP index.
A record of issuance & retrieval of respective SOP index shall be maintained by QA officer/executive as per SOP No. QA/001
User department Manager shall periodically review the all respective department SOP’s with the help of SOP index.
Click the link for download word file copy of this document:
https://pharmaguidehub.com/product/sop-of-sop/
REFERENCES:
WHO/VSQ/97.01– A WHO guide to good manufacturing practice (GMP) requirements, Part 1: SOP and Master Formulae.
ORA-LAB.4.3 – Document Control and Management (ORA Laboratory Procedure, FDA).
ANNEXURES:
ANNEXURE No. | TITLE OF ANNEXURE | FORMAT No. |
Annexure-I | SOP Format | QA-001/F01-00 |
Annexure-II | Format for Making New Format | QA-001/F02-00 |
Annexure-III | SOP Issuance, Retrieval & Destruction Log | QA-001/F03-00 |
Annexure-IV | Request Form for Issuance of Additional SOP | QA-001/F04-00 |
Annexure-V | SOP Index | QA-001/F05-00 |
Annexure-VI | Master List of SOP | QA-001/F06-00 |
Annexure-VII | Request For Revalidation Of Sop’s | QA-001/F07-00 |
Annexure-VIII | New SOP/Format Initiation Form | QA-001/F08-00 |
Annexure-IX | SOP Numbering Register | QA-001/F09-00 |
Annexure-X | SOP Discontinuation / Deletion Form | QA-001/F10-00 |
Annexure-XI | Log Book for SOP Initiation Form | QA-001/F11-00 |
ENCLOSURES: SOP Training Record.
DISTRIBUTION:
Controlled Copy No. 01 | : | Manager Quality Assurance |
Controlled Copy No. 02 | : | Manager Quality Control |
Controlled Copy No. 03 | : | Manager Production |
Controlled Copy No. 04 | : | Manager Warehouse |
Controlled Copy No. 05 | : | Manager Engineering |
Controlled Copy No. 06 | : | Manager Human Resources |
Controlled Copy No. 07 | : | Manager Information Technology |
Controlled Copy No. 08 | : | Manager Accounts |
Controlled Copy No. 09 | : | Manager Purchase/Commercial |
Controlled Copy No. 10 | : | Manager Packing |
Controlled Copy No. 11 | : | Manager Microbiology |
Controlled Copy No. 12 | : | Manager Environmental Health & Safety |
Controlled Copy No. 13 | : | Manager PPIC |
Master Copy | : | Quality Assurance Department |
ABBREVIATIONS:
SOP | : | Standard Operating Procedure |
No. | : | Number |
QA | : | Quality Assurance |
QC | : | Quality Control |
PD | : | Production |
WH | : | Warehouse |
EG | : | Engineering |
IT | : | Information Technology |
HR | : | Human Resources |
AC | : | Accounts |
PU | : | Purchase |
ES | : | Environment Health & Safety |
PP | : | PPIC |
REVISION HISTORY:
CHANGE HISTORY LOG
Revision No. | Details of Changes | Reason for Change | Effective Date |
00 | New SOP | Not Applicable | To be filled manual |
Click the link for download word file copy of this document:
https://pharmaguidehub.com/product/sop-of-sop/
ANNEXURE–I
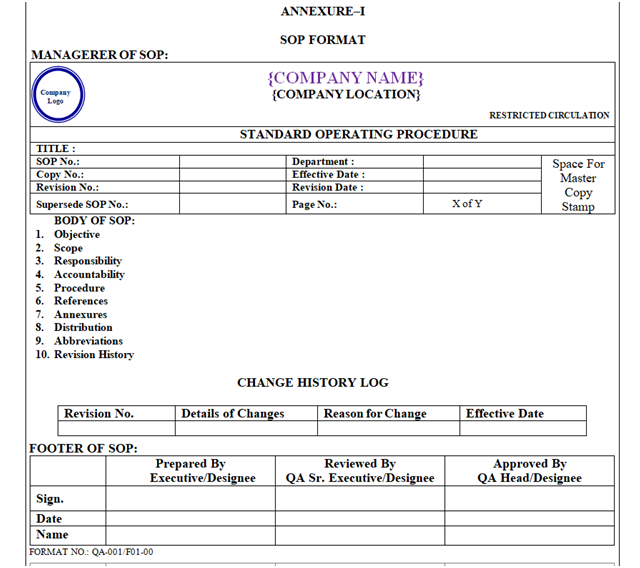
ANNEXURE – II
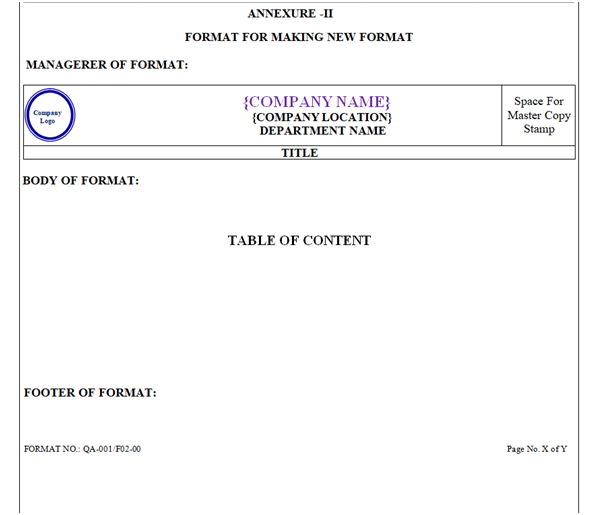
ANNEXURE – III
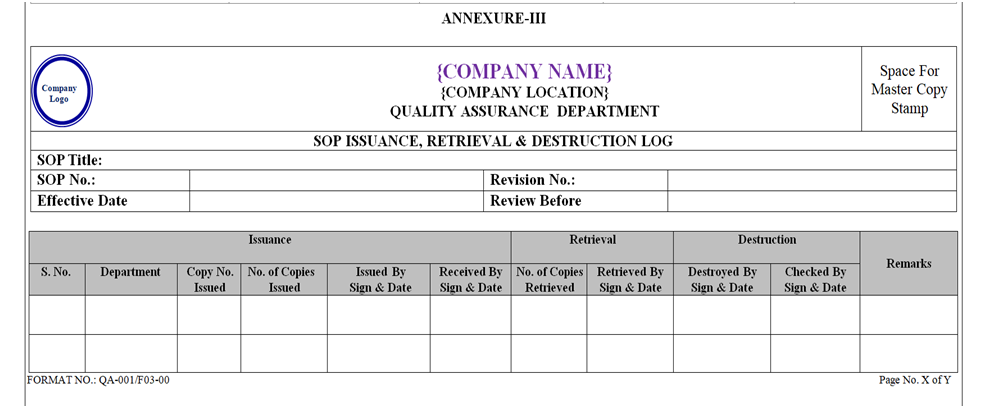
ANNEXURE – IV
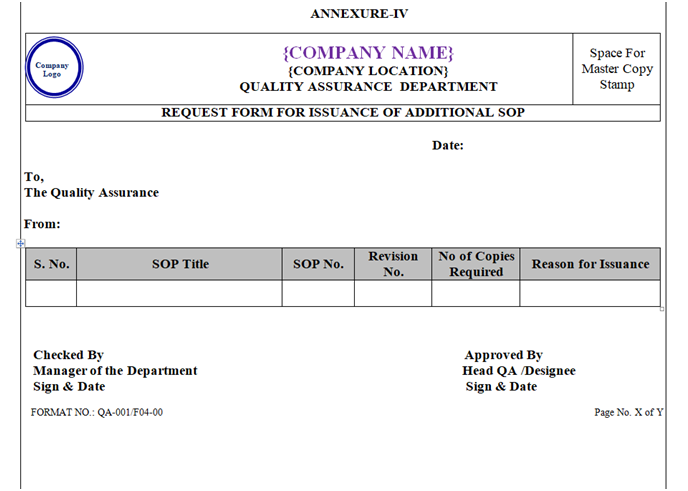
ANNEXURE – V

ANNEXURE – VI
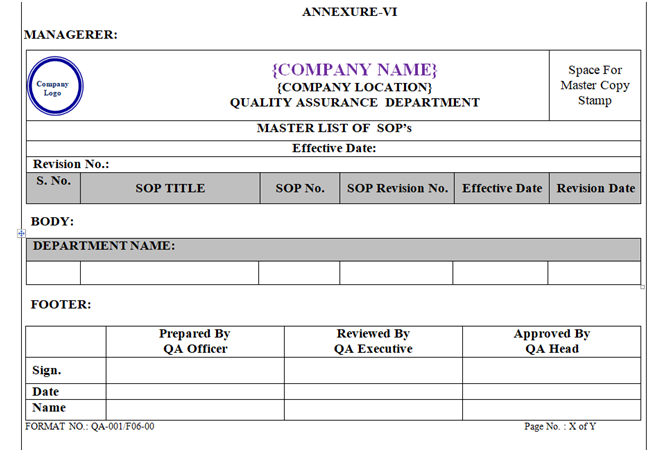
ANNEXURE – VII
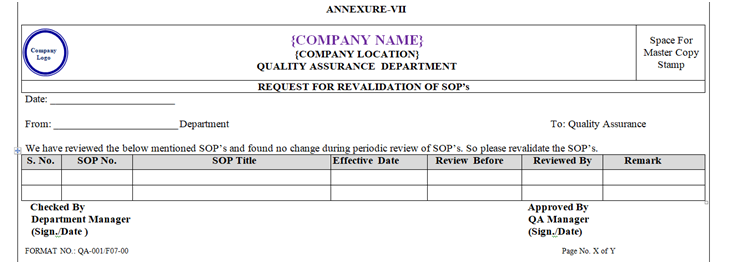
ANNEXURE – VIII
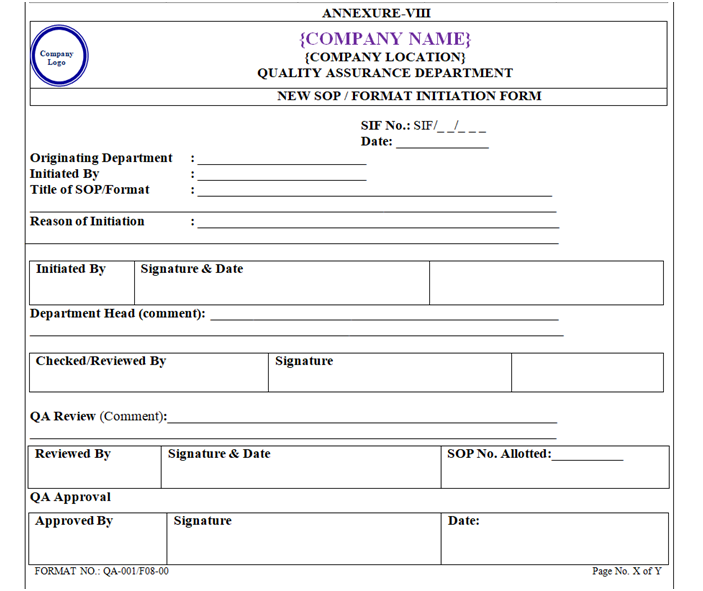
ANNEXURE – IX
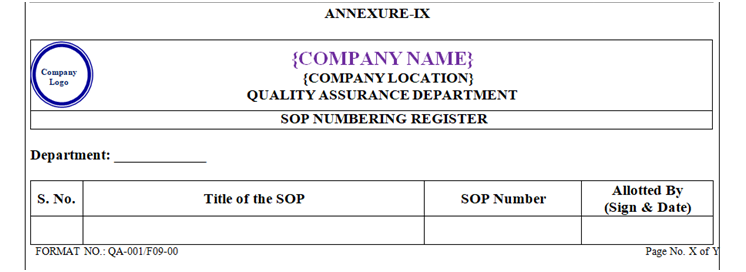
ANNEXURE – X
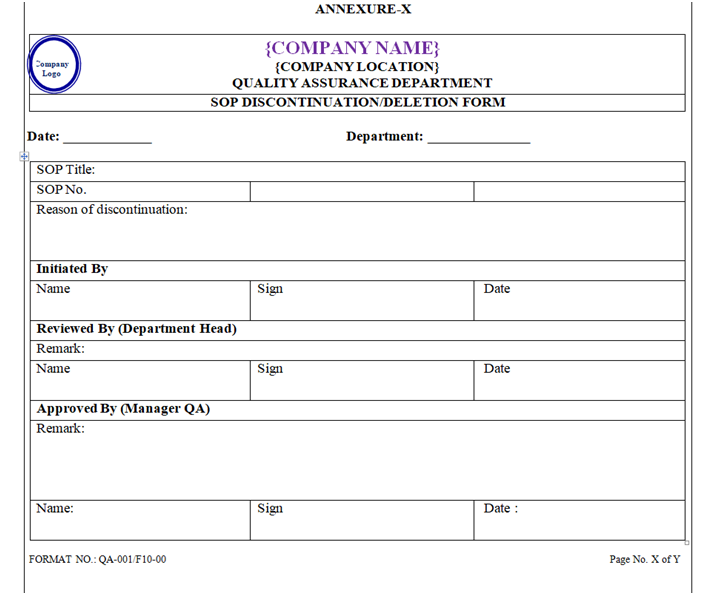
ANNEXURE – XI
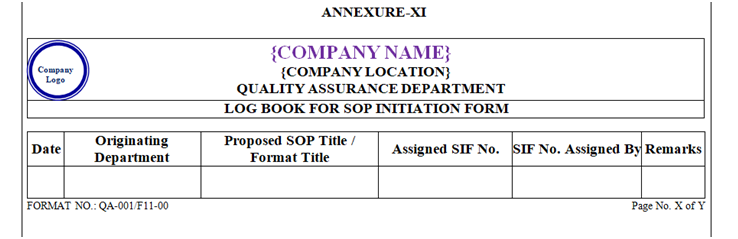
Click the link for download word file copy of this document:
https://pharmaguidehub.com/product/sop-of-sop/