OBJECTIVE:
To describe a procedure for sampling and in-process checks at different stages of manufacturing & packing in tablet and capsule section.
SCOPE:
This SOP is applicable to Production (Manufacturing & Packing), IPQA and Quality Control for sampling and in-process checks at different stages of the manufacturing & Packing in tablet and capsule section at {Company Name} {Location}.
RESPONSIBILITY:
Officer Production shall be responsible for in-process testing.
QA Officer – shall be responsible for sampling and in-process checks. QA Executive – Executive QA/QC/Production shall be responsible for review of analysis report..
ACCOUNTABILITY:
Head QA
PROCEDURE:
- Sampling and in-process checks shall be carried out at different stages of manufacturing (e.g. dry mixing, drying, blending, lubrication, compression / filling, check weighing, coating & Tablet printing) and packing operations as per the requirements.
- On receipt of “Sample Test Request for Intermediate/Finished Goods” (in triplicate) from production as per Annexure-I, QA shall check and ensure completeness of BMR/BPR up to the last stage.
- Prepare ‘Sample for Analysis’ label and affix the same on the sampled container.
- Ensure that sampling rod / sampling tools are cleaned before use and affixed with “CLEANED” status label.
- Wear the latex hand gloves.
- Verify the batch details on the label affixed on the in-process container.
- Check the status label of the product to ascertain the stage of processing and ensure it is matching with the requirement.
- Sampling at Granulation Stage :
- Open the lid of the RMG/ Blender/Container/Bin and perform the sampling by dipping the sampling rod wherever applicable up to the maximum possible depth of the RMG/ Blender/Container/Bin, open the sampling ports of the sampling rod by twisting the handle clockwise / anti-clockwise.
- Close the sampling ports of the sampling rod containing sample and remove the rod from RMG/ Blender/Container/Bin.
- After taking out SS sampling rod from the RMG/ Blender/Container/Bin, collect the sample from each sampling port to get the representative sample of approximately equal to 100g/ as per process validation protocol/As per BMR instructions.
- Enter the drawn samples quantity in the respective BMR.
- Verify the product details from the container label ensure the printed slip having Product Name, Batch Number, Date, Time, Weight and Signature (Production & QA) of granule attached with BMR.
- Put ‘UNDER TEST’ label on the sampled container(s).
- Record the sampling details in sample log book as per Annexure-II.
- Send the sample to QC for analysis along with “Sample Test Request for Bulk/Finished Goods”.
- Take the signature of QC designee in sample log book for receipt of the sample.
- After QC release of lubricated granules, affix ‘APPROVED’ label over the ‘UNDER TEST’ label.
- Sampling of Core/Uncoated Tablets
- After completion of compression inspect the tablets (if required).
- Composite sample shall be collected from each container / as per process validation protocol/As per BMR instructions of the batch. Product that are having Std. wt. more than 250 mg then 100 Nos. of tablets shall be collected if it have Std. wt. less than or equal to 250 mg then 200 Nos. of sample shall be collected from each container by mixing homogeneously equal portions in a self locking poly bag or tie the poly bag with cable tie.
- Verify the product details from the container label ensure the printed slip having Product Name, Batch Number, Mfg. Date, Exp. Date, Date, Weight and Signature (Production & QA) of uncoated Tablets attached with BMR.
- Sampling of Coated Tablets
- Verify the number of containers from BMR.
- Composite sample of 100 tablets shall be sampled from every containers of each lot/ as per process validation protocol/As per BMR instructions in self locking poly bag or tie the poly bag with cable tie.
- Verify the product details from the container label ensure the printed slip having Product Name, Batch Number, Mfg. Date, Exp. Date, Date, Weight and Signature (Production & QA) of coated Tablets attached with BMR.
- Enter the drawn samples quantity in the respective BMR.
- Paste ‘UNDER TEST’ label on the sampled container(s).
- Record the sampling details in sample log book i.e. Annexure-II).
- Send the sample to QC for analysis along with “Sample test request for bulk/finished goods”.
- Take the signature of QC designee in sample log book for receipt of the sample.
- After QC release of tablets affix ‘APPROVED’ label over the ‘UNDER TEST’ label.
- Sampling of Tablet after Tablet Printing
- Verify the number of containers from BMR.
- Composite sample of 100 tablets shall be sampled from every containers of each lot/ as per process validation protocol/As per BMR instructions in self locking poly bag or tie the poly bag with cable tie.
- Verify the product details from the container label ensure the printed slip having Product Name, Batch Number, Mfg. Date, Exp. Date, Date, Weight and Signature (Production & QA) of tablet printing attached with BMR.
- Enter the drawn samples quantity in the respective BMR.
- Paste ‘UNDER TEST’ label on the sampled container(s).
- Record the sampling details in sample log book i.e. Annexure-II).
- Send the sample to QC for analysis along with “Sample test request for bulk/finished goods”.
- Take the signature of QC designee in sample log book for receipt of the sample.
- After QC release of tablets affix ‘APPROVED’ label over the ‘UNDER TEST’ label.
- Sampling for MLT Analysis (If required).
- Collect representative samples of finished product (if required) for microbial limit test during packing.
- Quantity of drawn sample shall be equivalent to 25g (or as per requirement).
- Sampling of Capsules
- Composite sample of 100 capsules (or as per requirement) shall be sampled from each container / as per process validation protocol/As per BMR instructions of batch.
- Samples shall be drawn from each container by mixing homogeneously equal portions in a self sealing poly bag or tie the poly bag with cable tie.
- Verify the product details from the container label ensure the printed slip having Product Name, Batch Number, Mfg. Date, Exp. Date, Date, Weight and Signature (Production & QA) of Filled capsules attached with BMR.
- Sampling of Capsules after checkweighing
- Composite sample of 100 capsules (or as per requirement) shall be sampled from each container / as per process validation protocol/As per BMR instructions of batch. Samples shall be drawn from each container by mixing homogeneously equal portions in a self sealing poly bag or tie the poly bag with cable tie.
- Verify the product details from the container label ensure the printed slip having Product Name, Batch Number, Mfg. Date, Exp. Date, Date, Weight and Signature (Production & QA) of Filled capsules attached with BMR.
- In Process Checks at Various Stages of Manufacturing and Packing
- In Process Checks of Tablets / Capsules at Manufacturing Stage:
Click the link for download word file copy of this document: https://pharmaguidehub.com/product/sampling-and-inprocess-checks-at-different-stages-of-manufacturing-and-packing-in-tablet-and-capsule/
- In- process test Sample of tablet/capsule shall be collected at defined frequency as per respective BMR and at the time of sample collection record the time in BMR and perform in process as per BMR/ process validation protocol. If there is some gap between sample collection time and in process check time then sample must be store in self sealing poly bag or tie the poly bag with cable tie and kept inside the production cubical with labeling which contain Product Name, Batch Number, Mfg. Date, Exp. Date, Date & sample collection Time.
- Sample used for in-process check in DT, Friability, Hardness, Dimension & thickness should be destroyed and sample used for group weight & individual weight checking inside the production cubical should be consider as a good product if group weight & individual weight in-process check performed outside the production cubical like IPQA lab, QC lab etc. then it should be destroyed.
- In case of batches manufacturing of new product which have below 10 batches manufactured at site, critical process parameters with defined stages wise as per below table shall be evaluated before proceeding to next stages.
Table-1
Stage | Critical Quality Attributes |
Lubricated granules | Assay, BD, TD& Particle Size Distribution |
Compressed tablets | Assay , Dissolution ,Content uniformity |
Coated tablets | Assay , Dissolution ,Residual solvent (If solvent used during the process ), Content uniformity & Related substances |
Printed Tablet | Assay , Dissolution ,Residual solvent (If solvent used during the process ), Content uniformity & Related substances |
Capsules | |
Blend | Assay, BD, TD & Particle Size Distribution |
En-capsulation | Assay , Dissolution ,Content uniformity |
Capsule check weighing | Assay , Dissolution ,Content uniformity |
- Critical process parameters shall be analyzed as per specification and stage wise process shall be proceed to next stage after getting results of previous stage well within the limit.
- In case if results are observed out of limit, it shall be addressed through QMS tools (incident/Deviation/CAPA).
- In Process Checks of Tablets/Capsules at Packing Stage:
- In-process tests of tablet/capsule shall be performed at defined frequency as per respective BPR.
- In case of any results of in-process parameters shall be observed out of specified limits of BMR, deviations/incidents shall be recorded as per the SOP.
- Sample used for leak test shall be destroyed and sample used for appearance check shall be considered as a good product.
- During the in process check for colour description of coated tablets shall be check with pantone shade card before proceeding to next stage of packing.
- QC person also verify the colour description of coated tablets as per pantone shade card during the analysis of Bulk/Finished product testing.
Sampling of Finished product at packing Stage
- Composite sample shall be collected from initial, middle and end stage of packaging operation.
- Verify the product details from BPR/Carton having Product Name, Batch Number, Mfg. Date, Exp. Date, Pack Style, Pack Size etc. of packed tablets/Capsules attached with BPR.
- Enter the drawn samples quantity in the respective BPR.
- Records the sampling details in sample log book i.e. Annexure-II.
- Send the sample to QC for analysis along with “Sample test request for bulk/finished goods”.
- Take the signature of QC designee in sample log book for receipt of the sample.
- While sending Control sample, party sample, stability sample and other sample record in sample log book i.e. Annexure-II and take signature of concern department person to whom sample submitted.
Click the link for download word file copy of this document: https://pharmaguidehub.com/product/sampling-and-inprocess-checks-at-different-stages-of-manufacturing-and-packing-in-tablet-and-capsule/
- REFERENCES:
- Not Applicable
ANNEXURES:
ANNEXURE No. | TITLE OF ANNEXURE | FORMAT No. |
Annexure -I | Sample Test Request for Bulk /Finished Goods | QA-012/F01-00 |
Annexure- II | Sampling Log Book | QA-012/F02-00 |
DISTRIBUTION:
Controlled Copy No.01 | : | Head Quality Assurance |
Controlled Copy No.02 | : | Head Production |
Controlled Copy No.03 | : | Head Warehouse |
Master Copy | : | Quality Assurance Department |
ABBREVIATIONS
SOP | : | Standard Operating Procedure |
QA | : | Quality Assurance |
QC | : | Quality Control |
BPR | : | Batch Packing Record |
RMG | : | Rapid Mixture Granulator |
IPC | : | Intermediate Process Container |
BMR | : | Batch Manufacturing Record |
MLT | : | Microbial Limit Test |
REVISION HISTORY:
CHANGE HISTORY LOG
Revision No. | Details of Changes | Reason for Change | Effective Date |
00 | New SOP | Not Applicable | To Be recorded Manual |
ANNEXURE-I
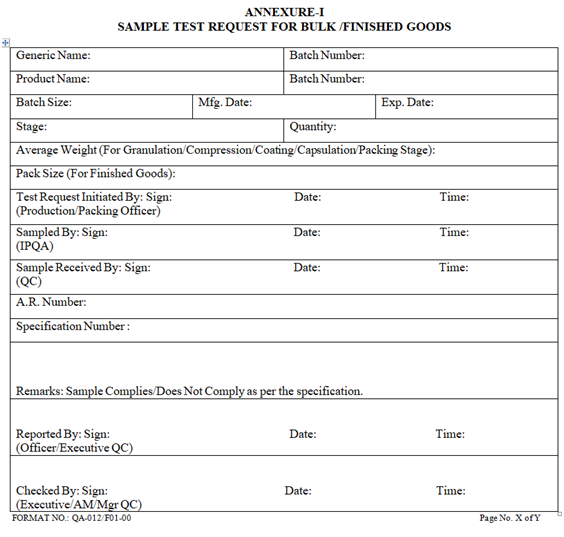
ANNEXURE-II
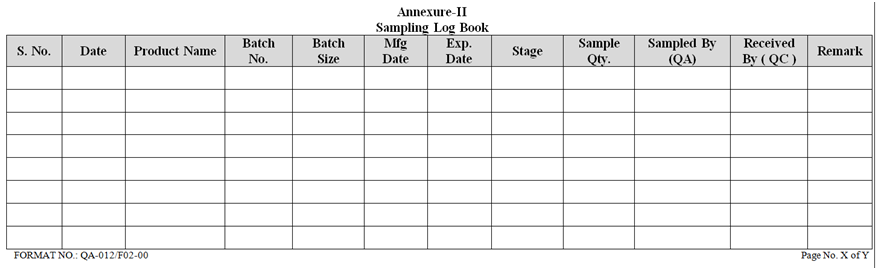
Click the link for download word file copy of this document: https://pharmaguidehub.com/product/sampling-and-inprocess-checks-at-different-stages-of-manufacturing-and-packing-in-tablet-and-capsule/
Frequently Asked Questions?
- Q: What is the purpose of in-process checks during tablet and capsule manufacturing?
- A: In-process checks ensure that the manufacturing process is proceeding as per the predefined standards, helping to identify and rectify any deviations promptly. This ensures the production of high-quality pharmaceutical products.
- Q: What are the key in-process checks for tablet and capsule manufacturing?
- A: Key checks include blend uniformity, granule size and distribution, tablet weight and hardness, content uniformity, disintegration, and dissolution testing.
- Q: How is blend uniformity assessed during tablet manufacturing?
- A: Blend uniformity is evaluated by taking samples at various stages of blending and analyzing them for uniform distribution of active pharmaceutical ingredient (API) using validated methods such as HPLC.
- Q: Why is content uniformity crucial in tablet and capsule production?
- A: Content uniformity ensures that each tablet or capsule contains the specified amount of the active ingredient, minimizing variations in dosage and ensuring therapeutic efficacy.
- Q: How is tablet weight controlled during manufacturing?
- A: Tablet weight is monitored by sampling tablets at regular intervals and weighing them individually. Deviations from the target weight are investigated and corrected.
- Q: What is the significance of disintegration testing in tablet manufacturing?
- A: Disintegration testing assesses the time it takes for tablets to break down into smaller particles. It ensures that tablets dissolve within a specified time, which is critical for drug absorption.
- Q: How is dissolution testing performed in capsule manufacturing?
- A: Dissolution testing measures the rate at which the capsule contents dissolve. It is essential for assessing the bioavailability of the drug and ensuring consistent therapeutic effects.
- Q: What measures are taken to control granule size and distribution in the manufacturing process?
- A: Granule size and distribution are controlled by monitoring and adjusting the parameters of the granulation process, such as screen size and impeller speed, to achieve the desired characteristics.
- Q: How is cross-contamination prevented during tablet and capsule manufacturing?
- A: Cross-contamination is prevented by implementing cleaning procedures between product changeovers, using dedicated equipment for high-risk products, and employing appropriate containment measures.
- Q: What actions are taken if in-process checks reveal deviations from specifications?
- A: If deviations are identified, investigations are conducted to determine the root cause. Corrective and preventive actions are then implemented to address the issue and prevent its recurrence, ensuring product quality and compliance with regulatory requirements.
Click the link for download word file copy of this document: https://pharmaguidehub.com/product/sampling-and-inprocess-checks-at-different-stages-of-manufacturing-and-packing-in-tablet-and-capsule/