- OBJECTIVE:
To lay down a procedure for Self inspection/Internal audit of facility by a team of qualified persons to monitor the implementation and compliance with Current Good Manufacturing Practices and proposed corrective actions.
- SCOPE:
This procedure shall be applicable to assess the level of cGMP compliance for activities in the various departments that impact on the safety, efficacy and quality of the final products at {Company Name} {Company Location}.
- RESPONSIBILITY:
- It is a joint responsibility of all the departments and team members involved in the self inspection / internal audit in coordination with Quality Assurance.
- Head QA shall be responsible for ensuring that self inspection is being conducted for all above quality system at the defined frequency and all audit observations are being complied and suitable corrective and preventive action is planned and being executed.
- ACCOUNTABILITY:
QA Head shall be accountable for implementation and compliances of this SOP.
- PROCEDURE:
- SELF INSPECTIONS/INTERNAL AUDITS SHALL BE CONDUCTED IN ORDER TO:
- To ensure that products are consistently produced and controlled against predetermined quality standards appropriate to their intended use.
- To monitor the implementation and compliance with cGMP principles.
- To monitor all aspects of quality systems and current regulatory requirements.
- To monitor the adherence to Standard Operating Procedures (SOPs).
- To propose necessary corrective and preventive actions.To improve the awareness and responsibilities of personnel.
- DEPARTMENTS FOR SELF INSPECTION:
Following departments shall be audited in order to assess the cGMP compliances:
- Warehouse operations.
- Production: Manufacturing and Packing operations.
- Quality Control.
- Engineering support- Utilities, maintenance and calibration system.
- Human Resources.
- Quality Assurance.
- AUDIT TEAM:
- The self inspection team shall consist of qualified auditors only. List of qualified auditors shall be available with QA.
- Auditors shall be decided by QA head based on the qualification, working experience and expertise in the relevant field.
- Self inspection shall be performed by a minimum of two auditors. Audit team shall include a QA expert and a person from cross functional department, i.e., Production, QC, Engineering, warehouse and HR(Human Resources) but from the department other than that being inspected. An external consultant can also add to self inspection team as per need.
- During self inspection of any department, concerned department personnel shall not be the part of auditing team.
- The self inspection team for any self inspection activity shall be lead by the QA expert.
- The self inspection team members shall be aware of the cGMPs, contamination, gowning practices, production/laboratory work dynamics so that the inspection does not lead to any disturbance or interruption of operations that may lead to failure or deviation.
- The self inspection team members shall be cordial, non-controversial, non confronting and patient while interacting with the auditee group.
- The self inspection team members shall strive to add value during the inspection by providing guidance, recommendation and on the spot tips to the operating personnel.
Click the link for download word file copy of this document: https://pharmaguidehub.com/product/self-inspection-in-pharmaceutical/
- CERTIFICATE OF QUALIFIED AUDITOR:
- Technical Experts from each Department on recommendation from respective Department Heads shall be considered for Auditor.
- QA Head shall evaluate the technical competency of Auditor on the following points:
- Technical Education Qualification
- Work Experience
- Exposure to external trainings
- Exposure to Regulatory Audits
- After evaluation individual shall be allowed to work as a Qualified Internal Auditor and Certificate of Qualified Auditor as shown in Annexure-XIII, shall be given to him / her.
- In case, Head Operations act as a Auditor, their Certificate shall be signed by QA Head.
- In case, QA Head act as a Auditor, their Certificate shall be signed by Director of {Company Name}. {Company Location}.
- FREQUENCY OF SELF INSPECTION:
- Self inspection for each department shall be conducted half yearly and frequency shall be twice in a year.
- Audit may be performed more frequently prior to Client / regulatory inspection or after major changes occurred.
- In addition to scheduled audits, QA can perform unscheduled audits of any function, system or process with no prior intimation to the auditee.
- In the audit schedule, latitude of 15 days is acceptable.
- Apart from the above defined frequency, Self inspection may also be conducted in either of the following cases:
- Following an OOS results.
- Following a product complaint.
- Following a batch failure.
- Note: In such cases the self inspections may be focused only to the required departments (or as applicable).
- SCHEDULE OF SELF INSPECTION:
- QA Executive shall prepare a detailed yearly self inspection schedule within first week of January of the corresponding year which shall include audit team, date, time of audit, and audit department as per Annexure-I.
- Self inspection schedule is approved by QA Head.
- QA shall retain the master copy of self inspection schedule and shall issue the controlled copy to all departments.
- PROCEDURE OF SELF INSPECTION:
- QA shall be responsible to communicate prior information to the self inspection team members and the auditee department about the self inspection through mail / telephone at least three working days earlier the date of inspection.
- The self inspection shall be conducted as per separate checklists prepared by QA for all the departments to be audited and shall be approved by QA Head.
- The self inspection team members shall be empowered and authorized to visit any area for inspection and review any process, procedures or document within the scope.
- The self inspection team shall discuss the focus areas of inspection, follow-up points, and previous CAPA implementation. The team may also decide to divide responsibilities during the self inspection.
- The inspection of the facilities and equipment, processes and operations, procedures and practices, compliance and documents shall be thorough. This may include interviewing the operating personnel and interrogation.
- The self inspection shall be carried out as per the self inspection check list.
- The deficiencies / deviations observed during the self inspection shall be listed in the self inspection check list by the QA representative.
- The observations shall also be categorized as critical, major and minor. Comments for recommendations shall also be entered in the check list.
- The categories are defined as follows:
- MINOR-Minor findings are those that deviate from accepted standards but have a relatively low probability of affecting the quality or usability of the product. They are minor breach of cGMP or internal procedures.
- MAJOR –That may have significant impact on the safety, efficacy and quality of a product; may be considered major deviations by regulatory authorities or are a combination of several minor deficiencies which indicates a major system failure. It is due to not following the standard procedures specified and reoccurrence of minor deficiencies.
- CRITICAL –Critical findings have a high probability of causing adverse consequences to the patient or consumer and may result in significant deviations in the safety identity, strength or purity of the product or are a combination of several major deficiencies, which indicates a critical system failure. Such defects require immediate action and are likely to risk the acceptance of the site by the regulatory authorities or customer.
- COMMENTS – There are recommendations whose implementation may lead to improvement of system.
- At the end of self inspection, the inspection team members shall have a wrap up meeting with the auditee group.
- The observations and comments from the self inspection shall be shared with the auditee group after self inspection audit by the QA representative to avoid any disagreement later. The critical observations can be complied immediately.
- Necessary clarifications and explanations shall be provided.
- In case any observation disputed by the auditee group, necessary evidence shall be provided by the auditee group. Subsequently, the QA representative shall annotate in the inspection report.
- All self inspection documents shall be archived in QA department.
REPORT OF SELF INSPECTION:
The finalized self inspection report (Annexure-VIII) shall be prepared by the QA representative and to be circulated to all departments within 07 working days after completion of audit.
Self inspection report numbering shall be as follows: ZZZ/SI/YY/NNN.
Where:
ZZZ indicates : Represent the initial of company Name
SI indicates : Self Inspection
YY indicates : Year like 22, 23…..
NNN indicates : Serial No. like 001, 002………..
QA representative and self inspection team members shall discuss the self inspection report with the auditee group and auditee department head to decide the suitable Corrective Action and Preventive Action and their target dates.
QA shall prepare follow-up Inspection report (Annexure-XII) and forward to the auditee department head/representative to give corrective action and preventive action and target date for compliance.
QA head shall review the corrective action & preventive action given by concerned relevant department in compliance report.
QA Manager / Designee shall finally prepare a conclusion report of self inspection as per Annexure-XI, and submit to the QA Head. The conclusion report shall include a brief note on deficiency, the proposed corrective action, evaluation comments and recommendations.
The critical and major findings shall be addressed by the auditee group on priority; these may require resources and special focus on Corrective & Preventive Action (CAPA) SOP No. QA/021 shall be followed by the auditee group.
A final report of internal audit findings and CAPA taken shall be discussed with management within 10 working days from the receipt of proposed corrective action report.
The self inspection findings/ reports shall be for improvement of GMP and system within the organization and shall not be shared with any external agency. QA shall maintain the records for conducting the self inspection.
COMPLIANCE OF SELF INSPECTION FINDINGS:
The critical deficiency shall be complied immediately and major deficiency shall be complied within 30 working days to avoid GMP non compliance.
Click the link for download word file copy of this document: https://pharmaguidehub.com/product/self-inspection-in-pharmaceutical/
Head of concerned department shall be responsible for preparing the proposed corrective action report as per Annexure-IX for the deficiencies reported within a week from the receipt of self inspection report and submit to QA department.
In case non- closure of the critical or major deficiency results in GMP or quality problem, then the operation shall not be allowed until corrected and closed to satisfaction. The possibility of recall of the products affected must be considered, as the case may be.
In case, the compliance to the corrective action and/or preventive action target date is delayed/ or going to be delayed, the auditee department head or representative shall inform the QA in writing, with justification and request for extension of target date.
QA shall evaluate this request and provide extension on this written request with signature and date.
Trending of audit observations shall be done annually.
Trending shall be done, department-wise, number of audit observations, based on category of the observation, repeated observation, Open observations, etc.
Critical and repeated observations shall be shared with management for their review and necessary action.
INTERNAL AUDIT RISK ASSESSMENT
Internal audit risk assessment shall be assessed as per Annexure-XV.
Areas where the combined likelihood and consequence is NLT 4 & NMT 8 will be audited at six month intervals. A score NLT 1 & NMT 3 will be done annually & a score NLT 9 & NMT 10 will be done Quarterly Risks will be reviewed in accordance with audit findings and ratings will be adjusted accordingly given below table :
Sum | Frequency |
1-3 | Annual |
4-8 | 6 Months |
9-10 | Quarterly |
The rating system shall be determined as per given below table
Rating | Likelihood | Rating | Consequence |
1 | Unlikely to cause a problem | 1 | No impact to Food Safety |
2 | Potential to cause problem | 2 | Minor impact to Food Safety |
3 | Need to monitor situation | 3 | Potential Food Safety issue |
4 | Highly likely to be a problem | 4 | Serious Food Safety issue |
5 | Will regularly cause problems | 5 | Complete system breakdown |
- Sum shall be calculated as addition of Likelihood and consequences
Likelihood + consequences = Sum
REFERENCES:
Schedule M, ICH Q7A.
- ANNEXURES:
ANNEXURE No. | TITLE OF ANNEXURE | FORMAT No. |
Annexure-I | Self Inspection Schedule | QA-024/F01-00 |
Annexure-II | Checklist for Self Inspection / Internal Audit – Warehouse | QA-024/F02-00 |
Annexure-III | Checklist for Self Inspection / Internal Audit – Production | QA-024/F03-00 |
Annexure-IV | Checklist for Self Inspection / Internal Audit – Quality Control | QA-024/F04-00 |
Annexure-V | Checklist for Self Inspection / Internal Audit – Engineering | QA-024/F05-00 |
Annexure-VI | Checklist for Self Inspection / Internal Audit – Human Resources | QA-024/F06-00 |
Annexure-VII | Checklist for Self Inspection / Internal Audit – Quality Assurance | QA-024/F07-00 |
Annexure-VIII | Self Inspection Report | QA-024/F08-00 |
Annexure-IX | Proposed Corrective Action Report | QA-024/F09-00 |
Annexure-X | Annual Self Inspection Planner | QA-024/F10-00 |
Annexure-XI | Conclusion Report of Self Inspection | QA-024/F11-00 |
Annexure-XII | Follow-up Inspection Report | QA-024/F12-00 |
Annexure-XIII | List of Qualified Auditor | QA-024/F13-00 |
Annexure-XIV | Certificate of Qualified Auditor | QA-024/F14-00 |
Annexure-XV | Internal Audit Risk Assessment | QA-024/F15-00 |
ENCLOSURES: SOP Training Record.
DISTRIBUTION:
- Controlled Copy No. 01 : Head Quality Assurance
- Controlled Copy No. 02 : Head Quality Control
- Controlled Copy No. 03 : Head Production
- Controlled Copy No. 04 : Head Engineering
- Controlled Copy No. 05 : Head Warehouse
- Controlled Copy No. 06 : Head Human Resources
Master Copy : Quality Assurance Department
ABBREVIATIONS:
QA | : | Quality Assurance |
SOP | : | Standard Operating Procedure |
cGMP | : | Current Good Manufacturing Practices |
OOS | : | Out of specification |
HR | : | Human Resources |
QC | : | Quality Control |
ICH | : | International conference on harmonization of technical requirement for the registration of pharmaceuticals for human use. |
CAPA | : | Corrective actions & preventive actions |
SME | : | Subject Matter Expert |
REVISION HISTORY
CHANGE HISTORY LOG
Revision No. | Details of Changes | Reason for Change | Effective Date |
00 | New SOP | Not Applicable | To be enter manual |
ANNEXURE-I
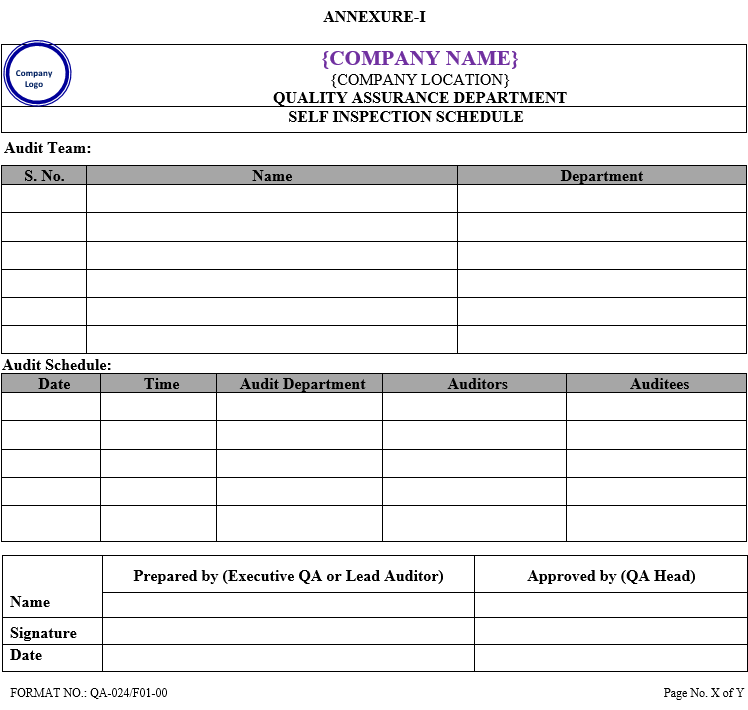
ANNEXURE-II
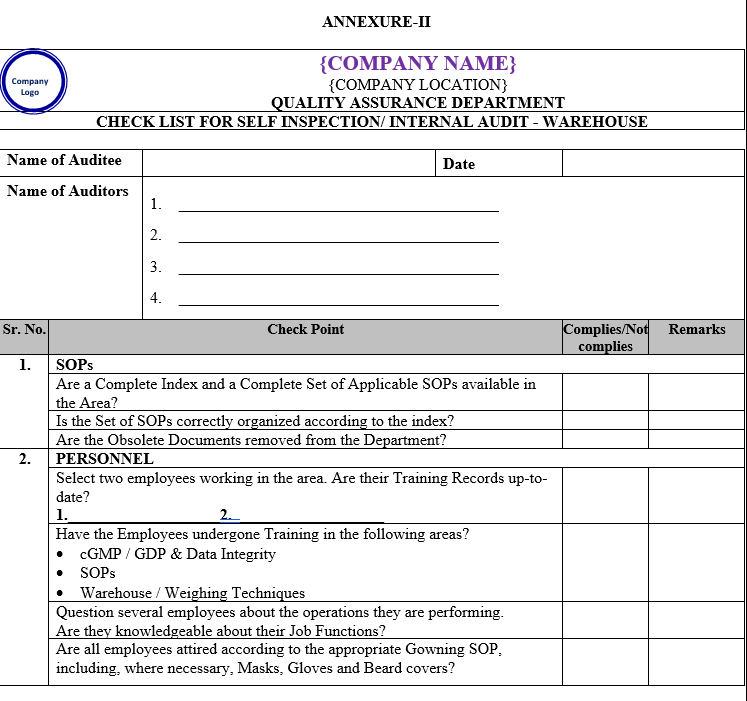
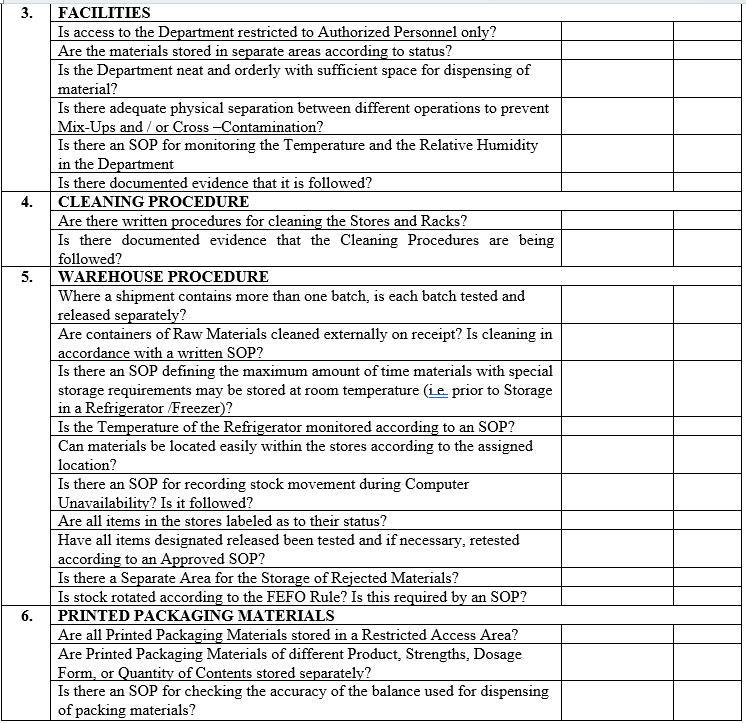

Click the link for download word file copy of this document: https://pharmaguidehub.com/product/self-inspection-in-pharmaceutical/
ANNEXURE – III
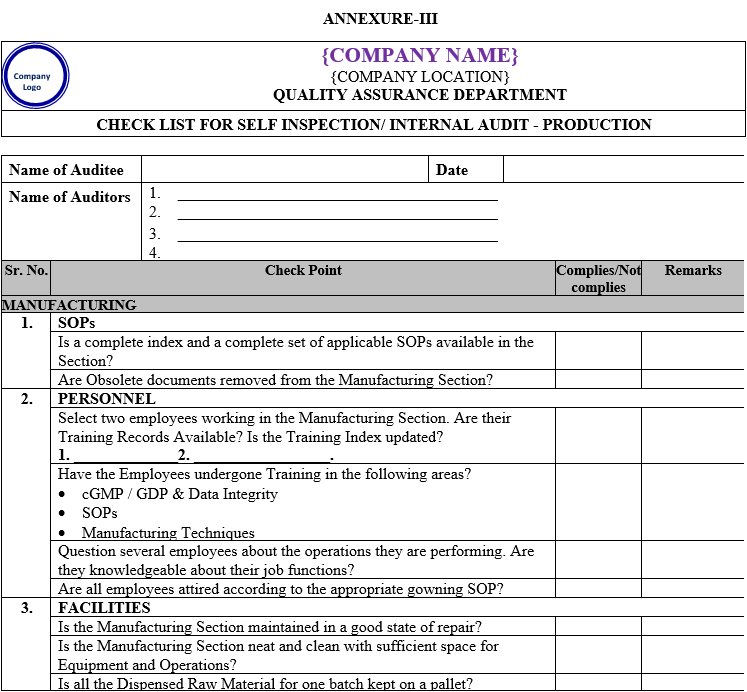
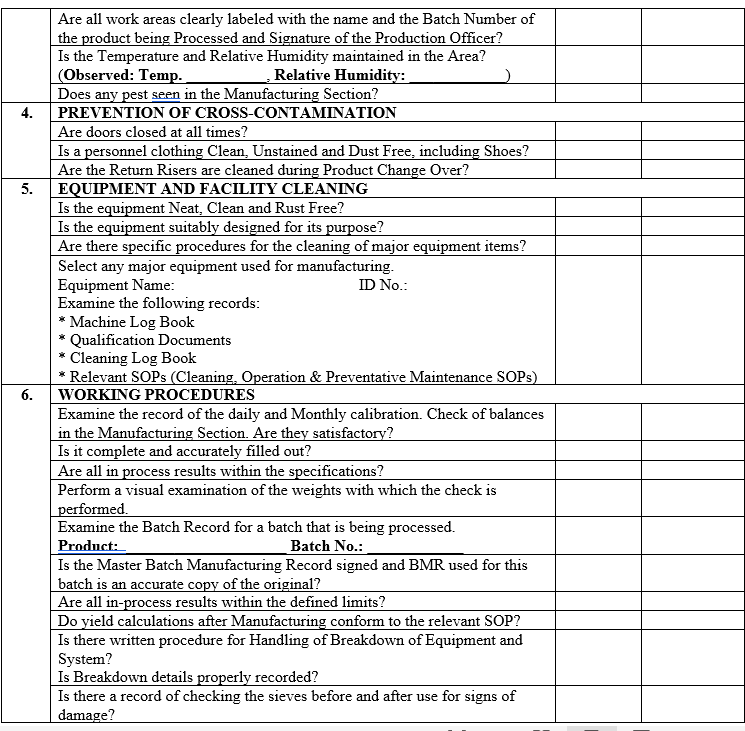
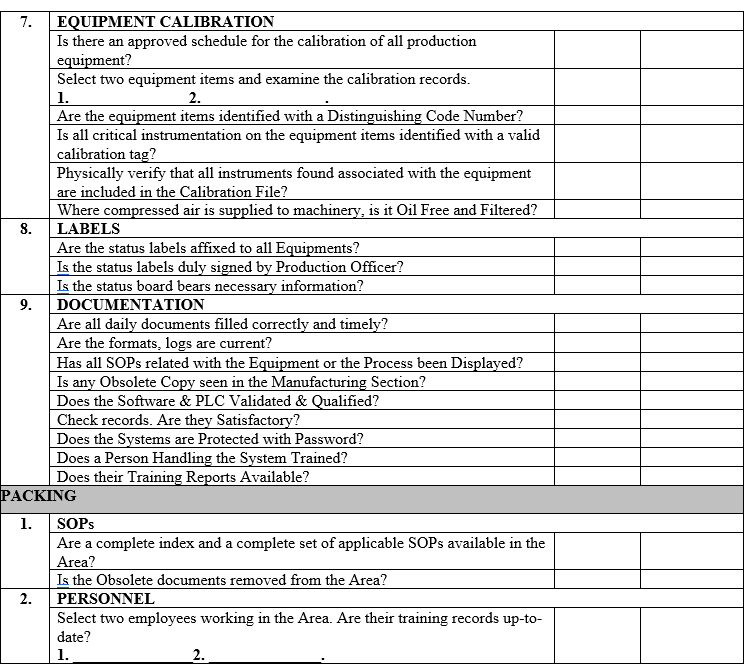
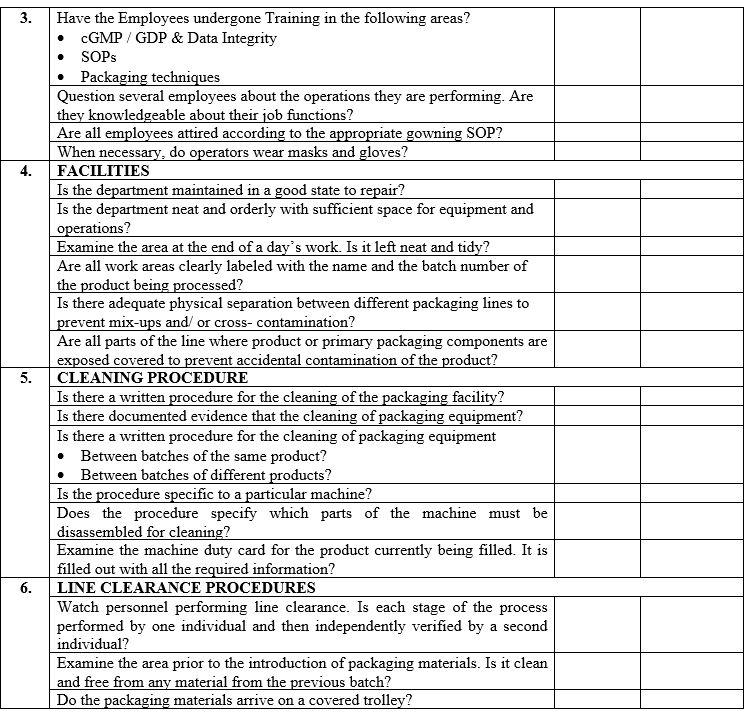
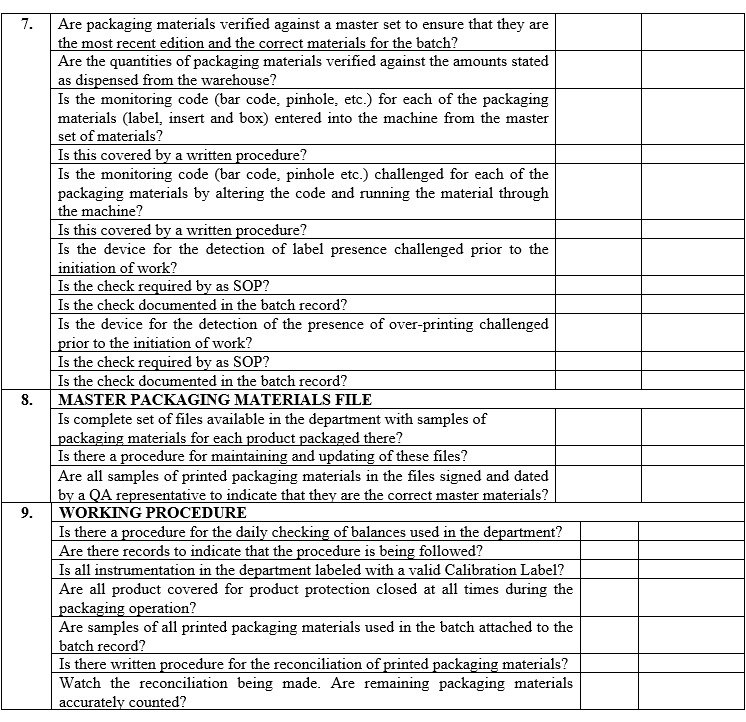
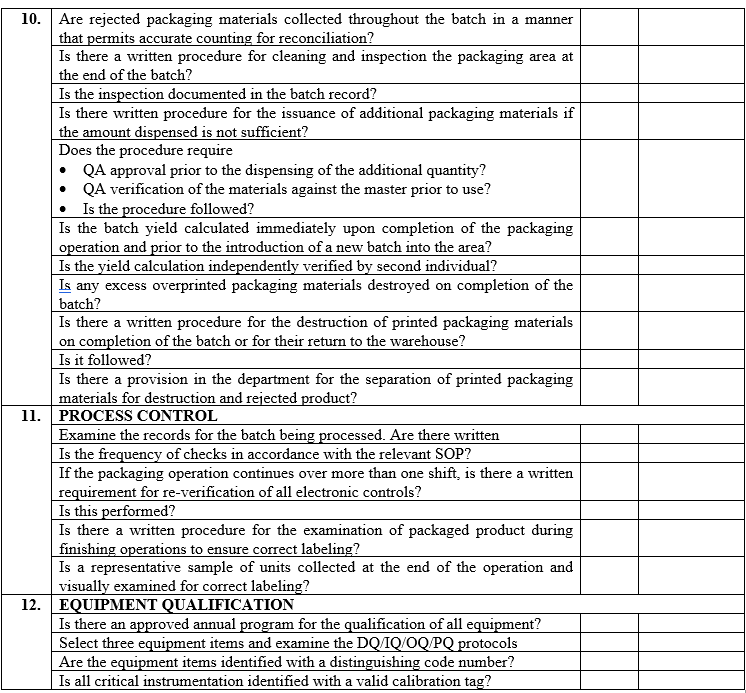

ANNEXURE-IV
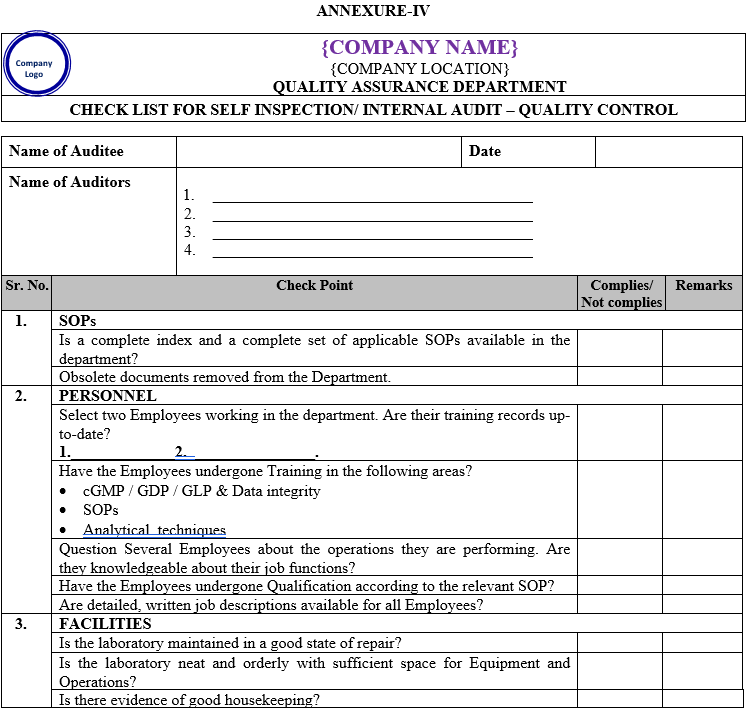
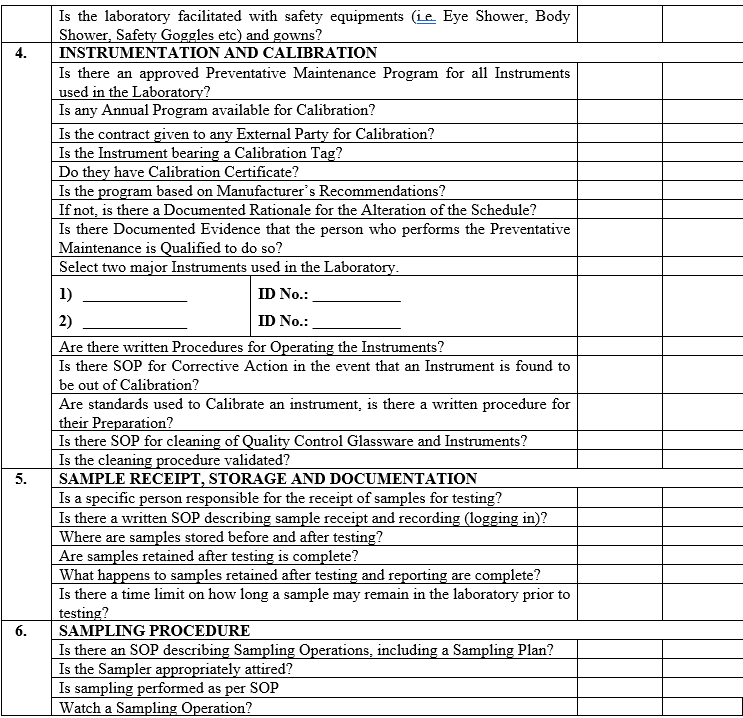
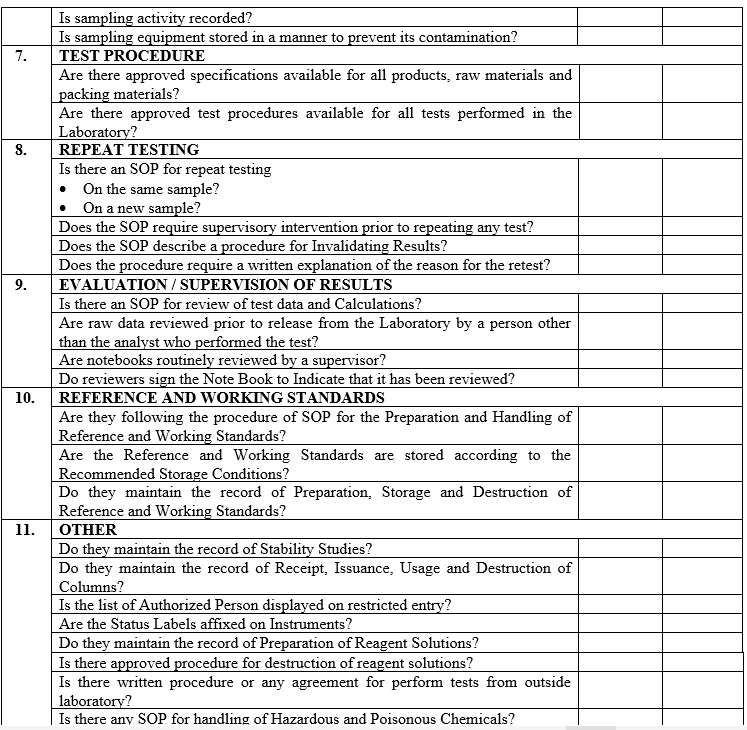

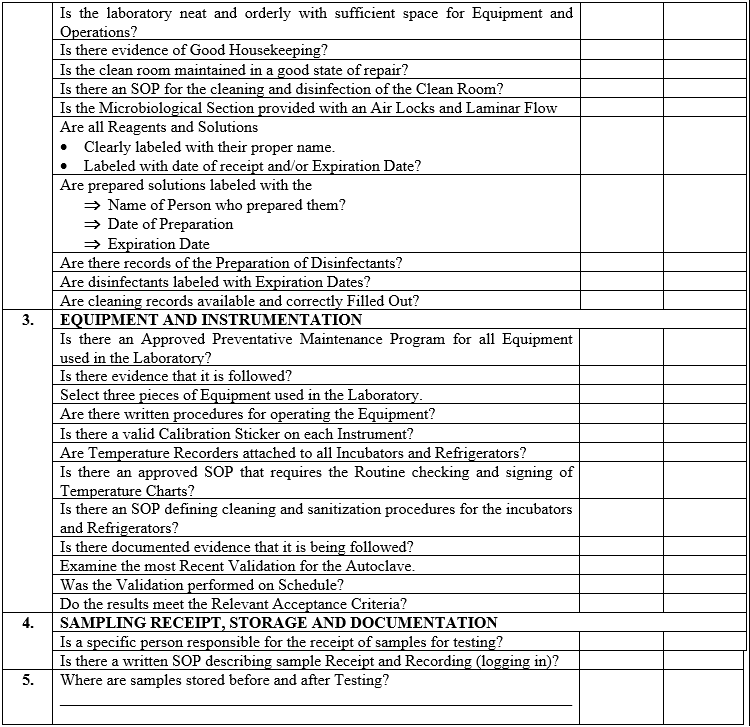
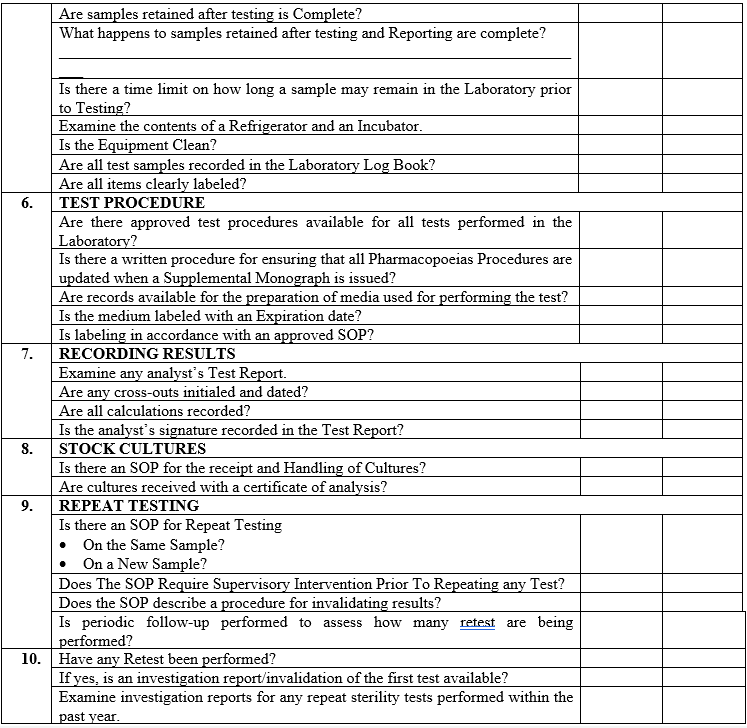
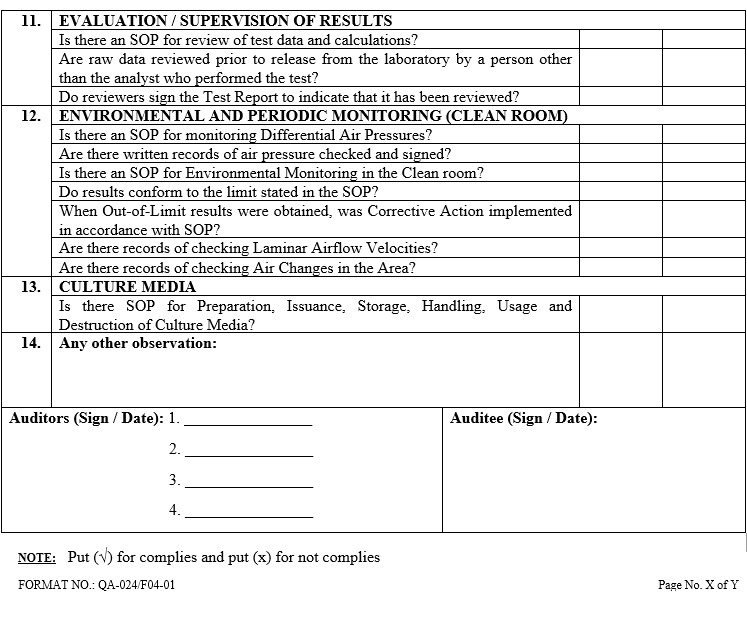
ANNEXURE-V
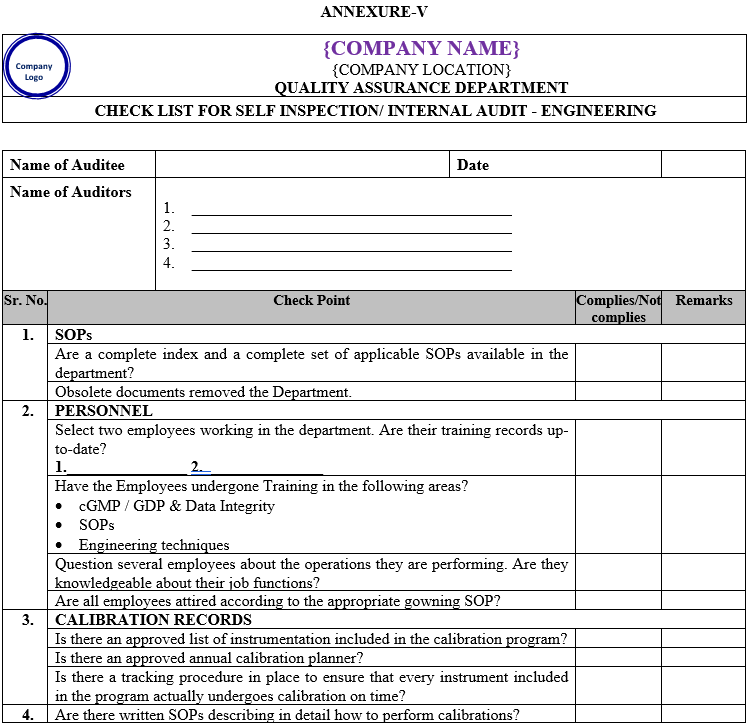

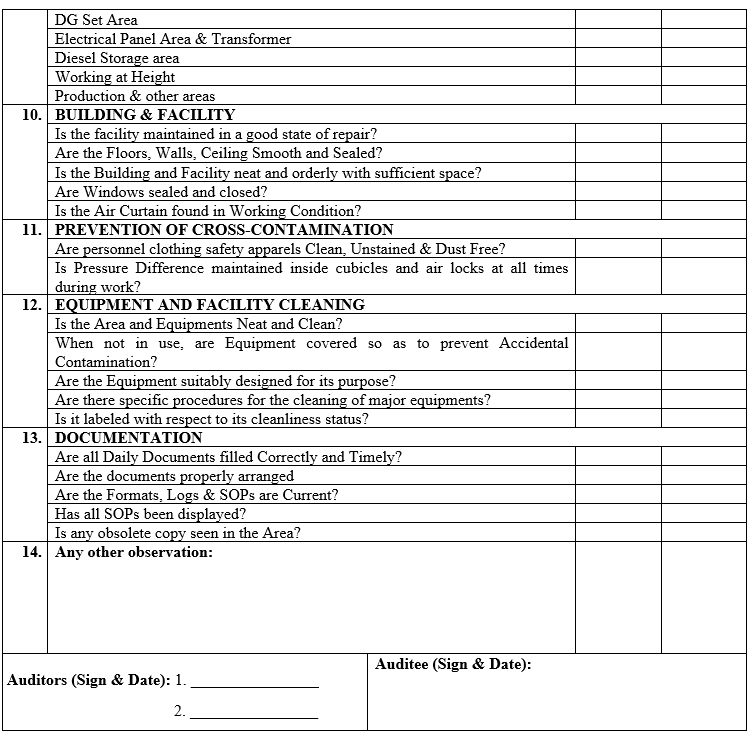
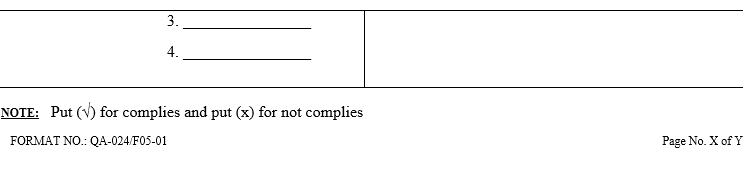
ANNEXURE-VI
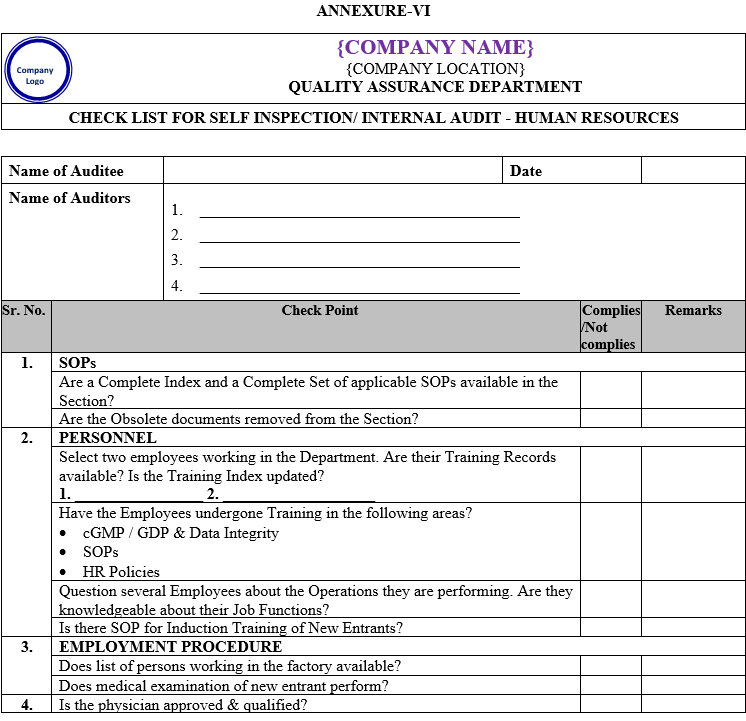
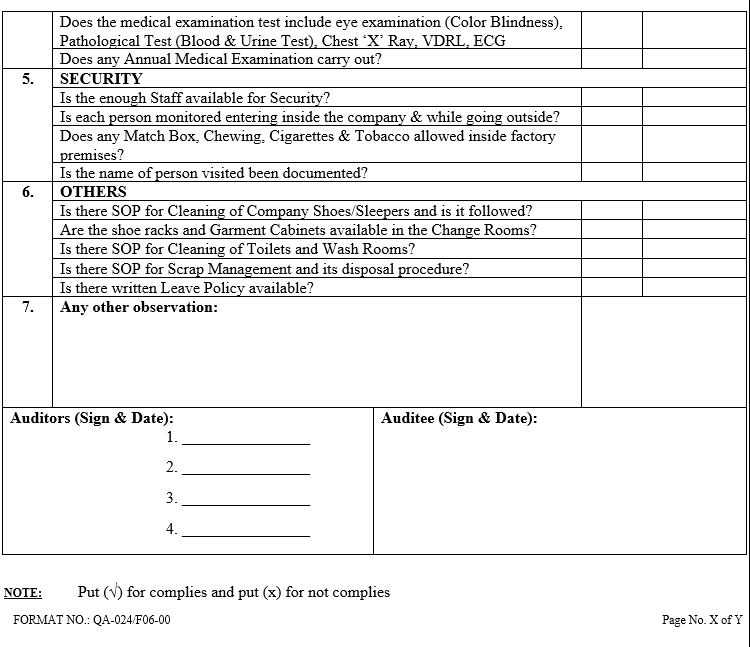
ANNEXURE-VII
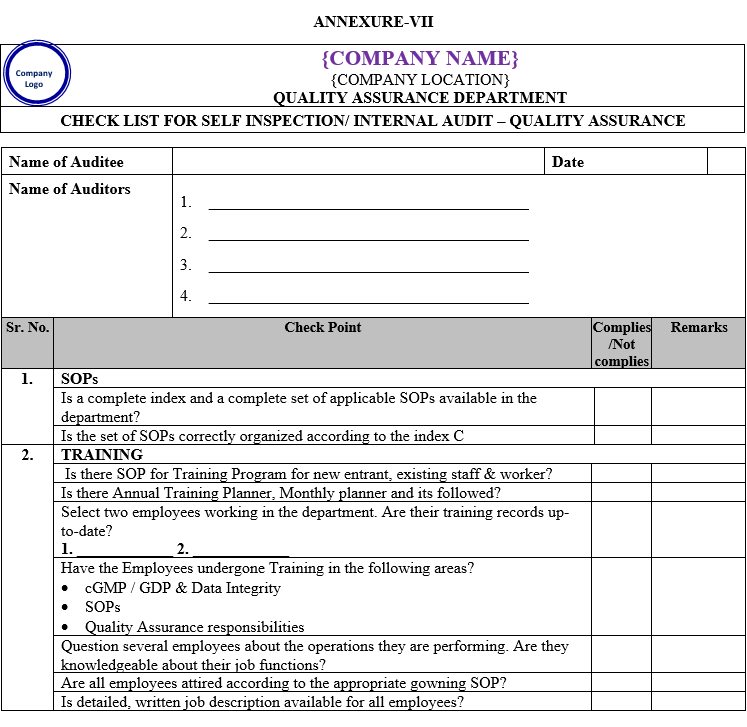
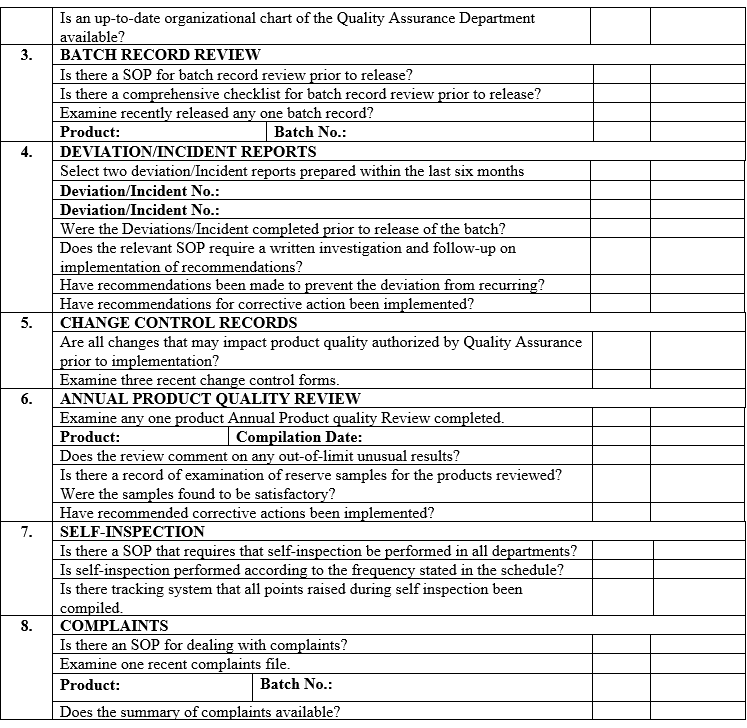
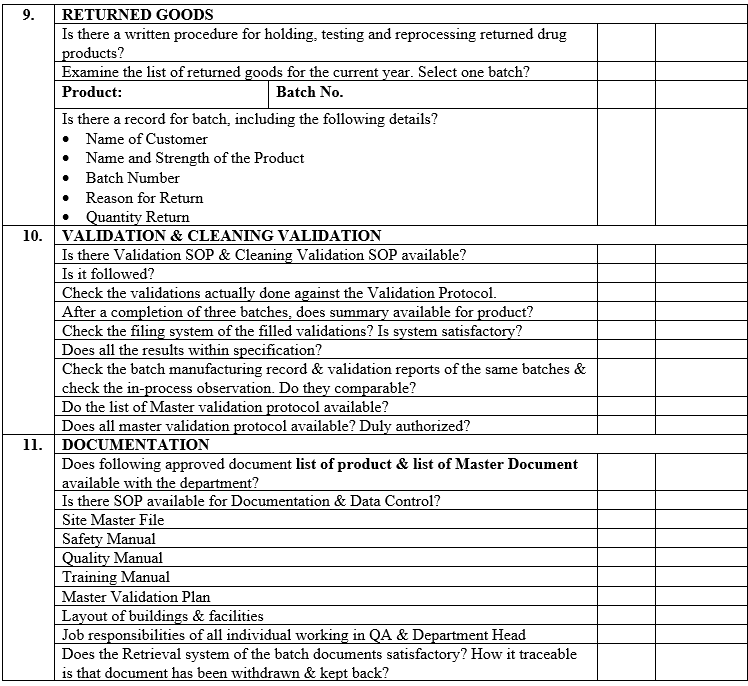
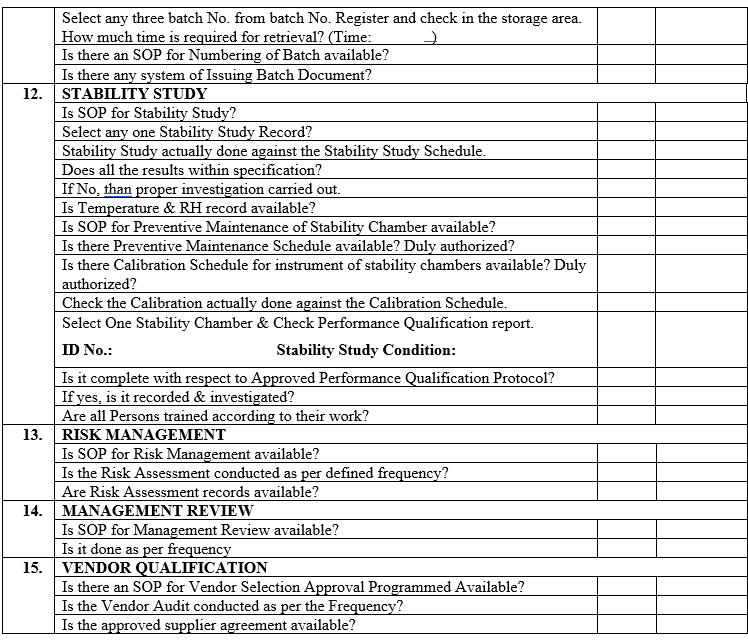
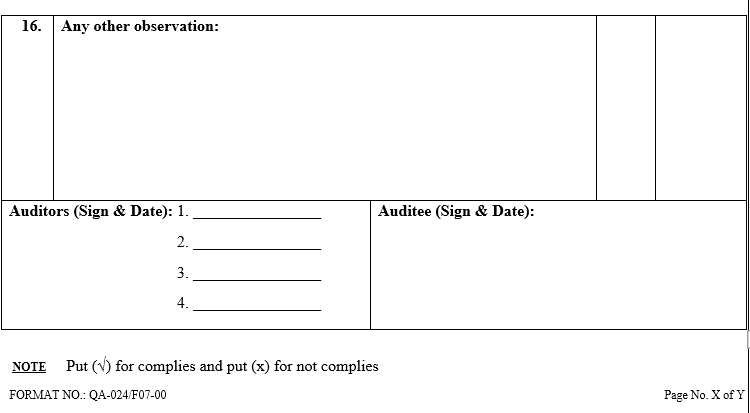
ANNEXURE-VIII
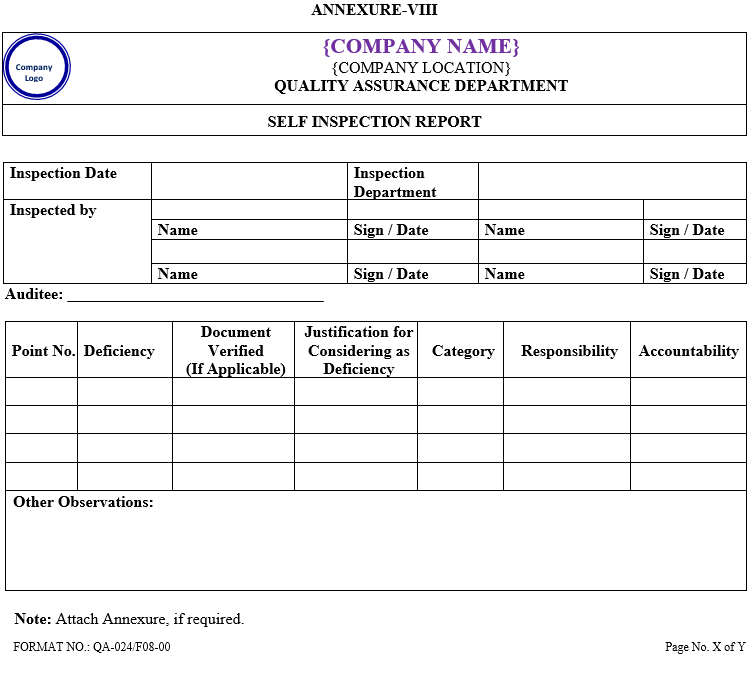
ANNEXURE-IX
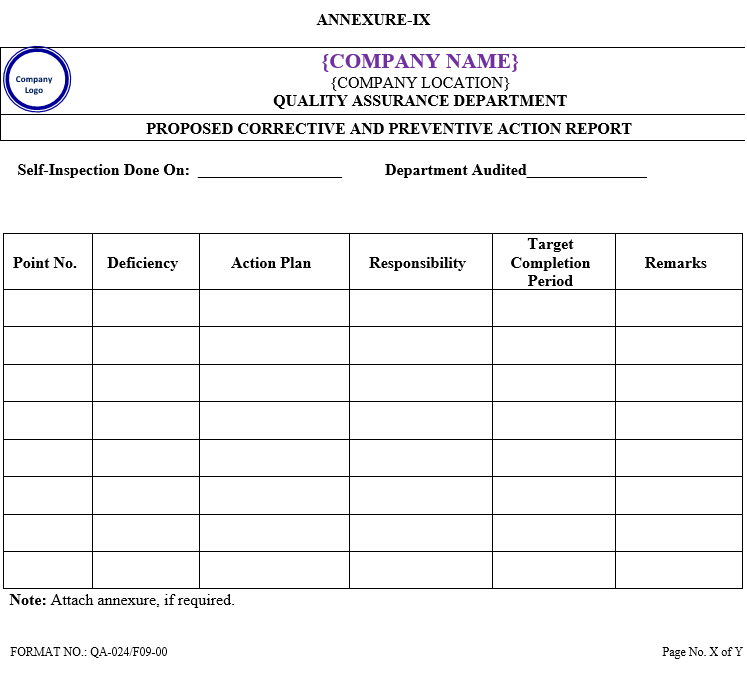
ANNEXURE-X
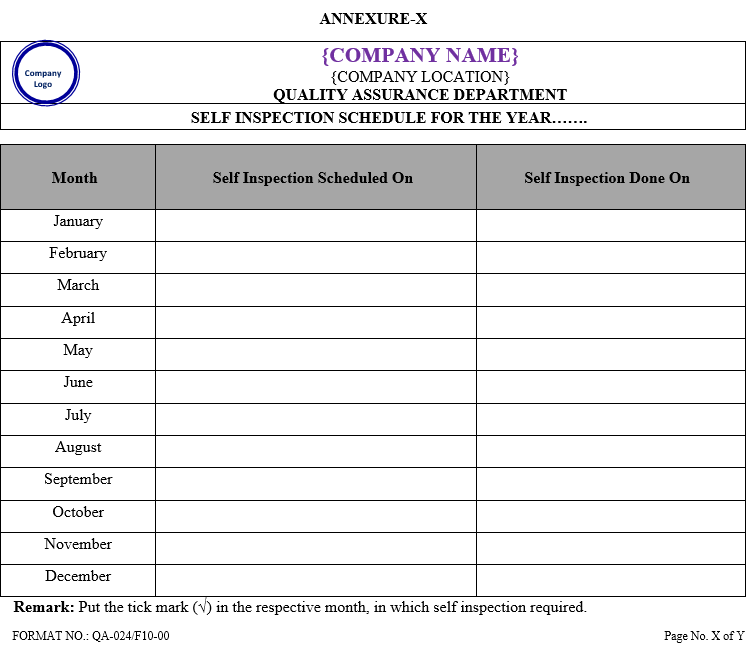
ANNEXURE-XI
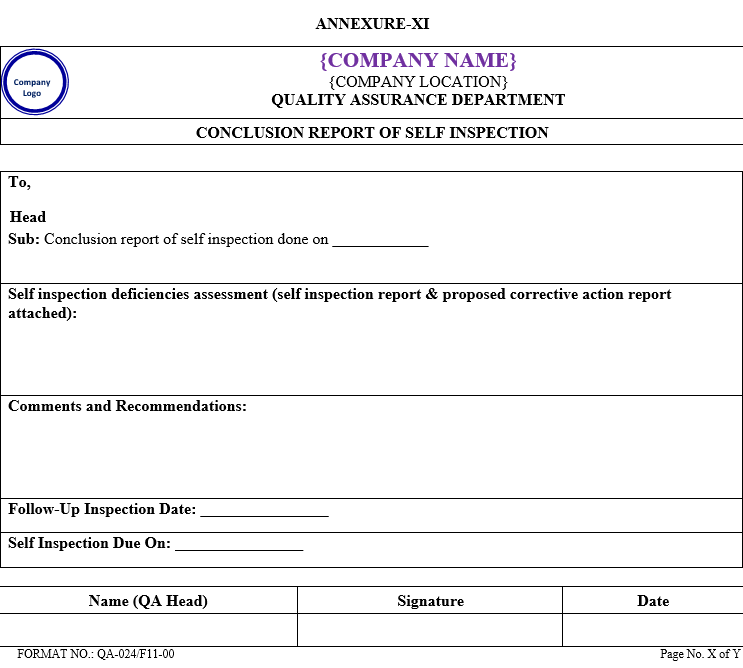
ANNEXURE-XII
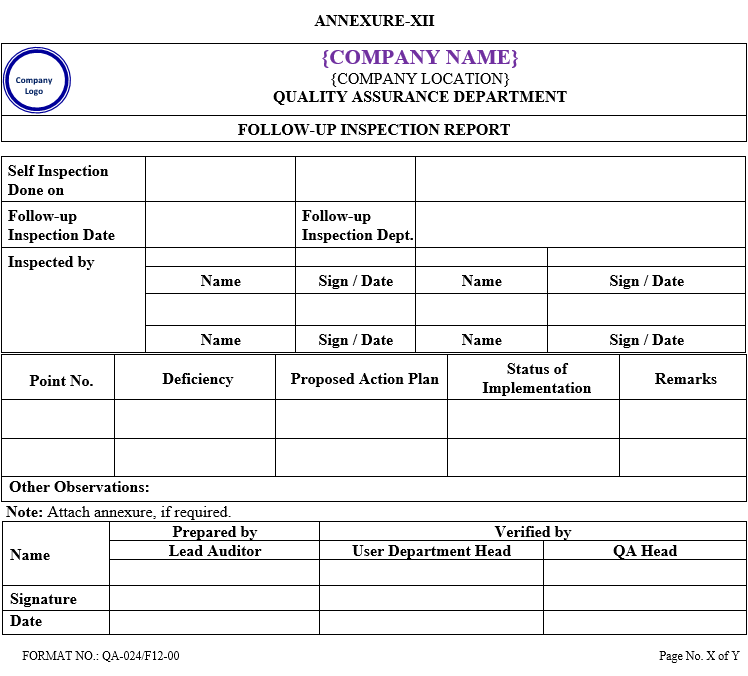
ANNEXURE-XIII
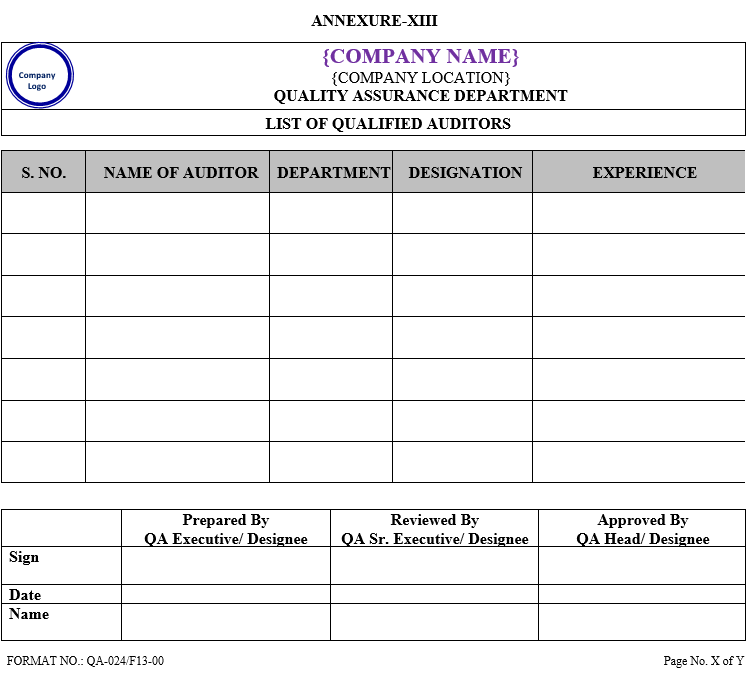
ANNEXURE-XIV
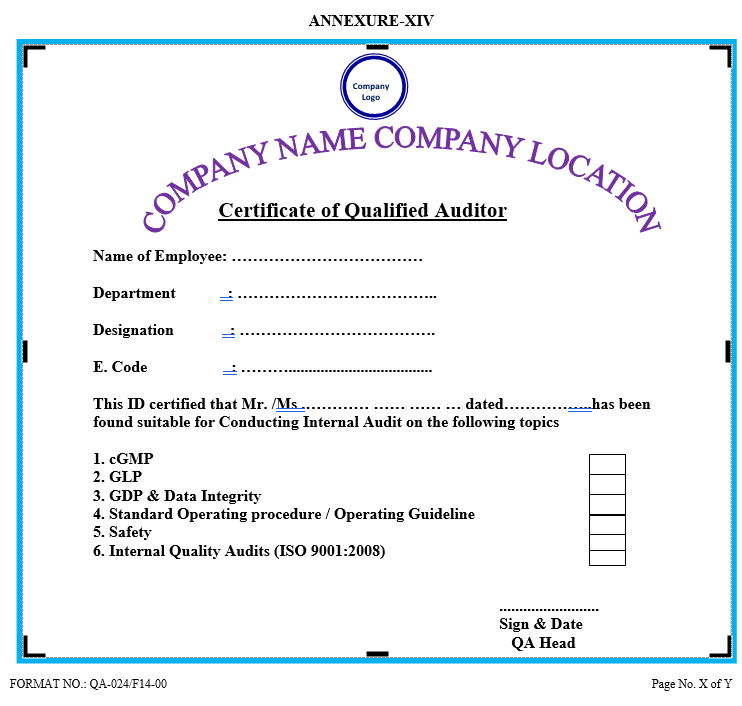
ANNEXURE-XV
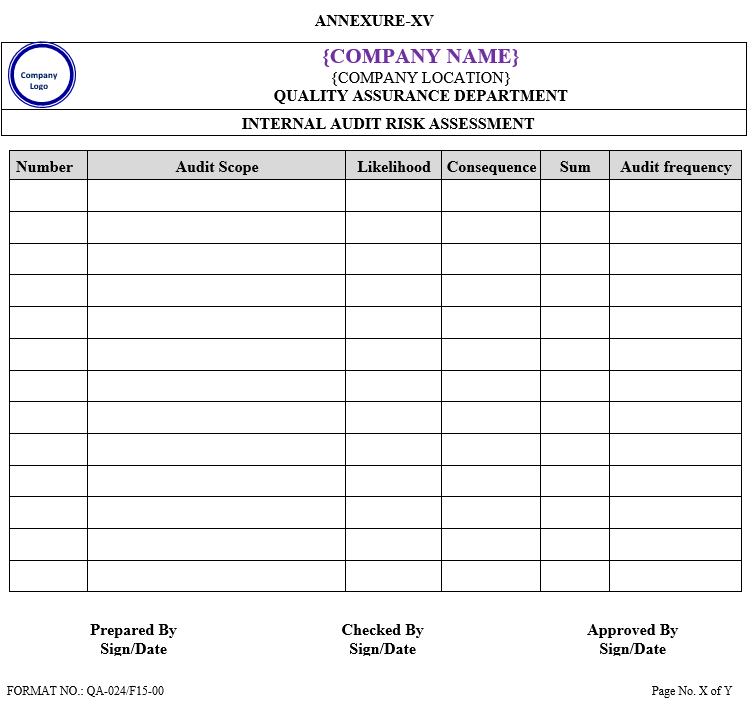
Click the link for download word file copy of this document: https://pharmaguidehub.com/product/self-inspection-in-pharmaceutical/
Frequently Asked Questions
- What is the purpose of conducting self-inspections in the pharmaceutical industry?
- Answer: Self-inspections are conducted to ensure compliance with regulatory standards, verify the effectiveness of quality management systems, and identify areas for continuous improvement in pharmaceutical manufacturing processes.
- How often should a pharmaceutical company perform self-inspections?
- Answer: The frequency of self-inspections should be determined by regulatory requirements and the company’s risk assessment. Typically, they are conducted regularly, such as two time in a year.
- What are the key areas that should be covered during a self-inspection in a pharmaceutical facility?
- Answer: Self-inspections should cover all aspects of pharmaceutical operations, including facilities, equipment, documentation, personnel, quality control, and adherence to Good Manufacturing Practices (GMP). All departments should be inspected during self-inspection by a cross-functional team.
- How should a pharmaceutical company prepare for a self-inspection?
- Answer: Preparation involves developing a comprehensive checklist, reviewing relevant documentation, ensuring the availability of necessary records, and training personnel on the self-inspection process.
- What actions should be taken if non-compliance or deviations are identified during a self-inspection?
- Answer: Corrective and preventive actions (CAPA) should be implemented promptly to address non-compliance issues. This may involve process improvements, additional training, or changes to standard operating procedures.
- Why is documentation crucial during a self-inspection in the pharmaceutical industry?
- Answer: Documentation serves as evidence of compliance, providing a transparent record of processes, procedures, and outcomes. Documentation aids in identifying areas for improvement and demonstrating adherence to regulatory requirements.
- How can a pharmaceutical company ensure the independence and objectivity of the self-inspection process?
- Answer: Independence can be achieved by assigning qualified personnel who are not directly involved in the areas being inspected. External consultants or third-party auditors may also be engaged for an unbiased evaluation.
- What role does senior management play in the self-inspection process?
- Answer: Senior management is responsible for fostering a culture of quality and compliance. They should actively support self-inspection initiatives, allocate resources, and ensure that corrective actions are implemented promptly.
- What is the relationship between self-inspections and continuous improvement in the pharmaceutical industry?
- Answer: Self-inspections contribute to continuous improvement by identifying weaknesses and inefficiencies in processes. The findings help pharmaceutical companies enhance their systems, reduce risks, and optimize overall performance.
- How can lessons learned from self-inspections be utilized to enhance overall quality in pharmaceutical manufacturing?
- Answer: Insights gained from self-inspections should be used to update and improve standard operating procedures, training programs, and quality management systems. This proactive approach helps prevent future non-compliance issues and strengthens the overall quality culture within the company.
Click the link for download word file copy of this document: https://pharmaguidehub.com/product/self-inspection-in-pharmaceutical/