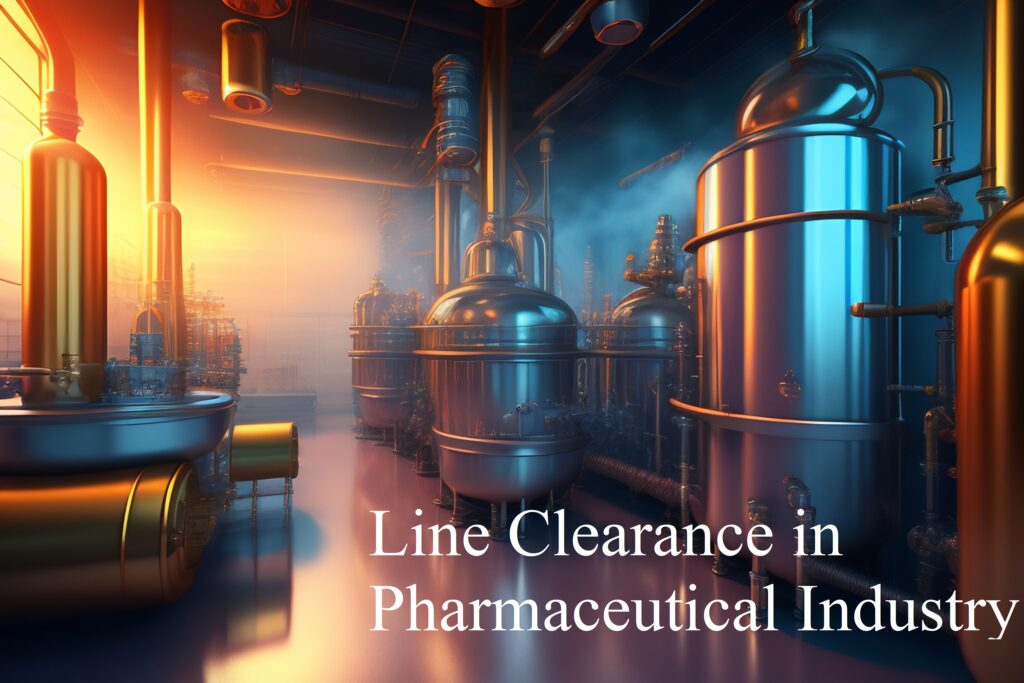
OBJECTIVE:
To lay down a procedure for the line clearance checks at different stages of the warehouse, manufacturing, primary and secondary packing to ensure prevention of product mix-up and cross contamination.
SCOPE:
This SOP shall be applicable for line clearance checks at different stages of the warehouse, manufacturing and packing of External preparation & cosmetics at {Company Name}{Company Location}.
RESPONSIBILITY:
Operator shall be responsible for cleaning of Equipment/Area.
Officer/Executive Production shall be responsible for checking of line clearance of the respective area.
Officer/Executive Warehouse shall be responsible for checking of line clearance of the respective area.
Officer/Executive IPQA shall be responsible for line clearance verification.
ACCOUNTABILITY:
Head QA and Concern Department Head shall be accountable for the compliance of this SOP.
- PROCEDURE:
- General Points for Line Clearance:
- Line clearance shall be done before commencing any activity in production and warehouse.
- Prior to commencing dispensing, manufacturing and packing for a particular product, warehouse/production officer/executive shall intimate to QA officer/executive.
- After receipt of the intimation from officer/executive of production/warehouse department for the area/ line clearance, QA officer/executive shall go to the concern area for the verification of area/line clearance.
- QA officer/executive shall ensure that approved copy of the BMR/BPR of the particular batch are in place.
- The area wise line clearance check list area wise shall be referred from the respective BMR/BPR of the particular batch.
- Check and ensure the cleanliness of area and equipment.
- Ensure the proper gowning of personnel in the operational area.
- Check and ensure that the HVAC system is functional and environmental conditions Temperature, Rh & pressure differential of area are within limit.
- Check and ensure that the log book of area and equipment are completed and signed.
- Check and ensure that Batch record, labels and materials related to previous batch are removed from area.
- Check and ensure that preventive maintenance of machines has been carried out as per the schedule and equipment’s are affixed with preventive maintenance label.
- Check and ensure that the calibration and validation status of all equipment’s are within validity periods.
- Check and ensure that the status labels in all the area are maintained.
- Line clearance before Dispensing of Raw material:
Following points shall be checked during line clearance before dispensing of Raw material and records shall be maintained in the BMR.
- Check and ensure that the area is free from all material of previous product dispensed.
- Ensure that utensils and accessories from previous operations have been removed.
- Check and ensure that neat and clean utensils shall be used to dispense raw materials of next product.
- BMR of previous operations has been removed.
- Status labels of previous operations have been removed.
- All the equipment’s and accessories required for dispensing should be cleaned and labeled.
- Ensure that the RLAF is started15 minutes before start the dispensing.
- Check and verify the cleanliness of entire booth (RLAF inner & outer side cover, roof of RLAF) and Floor, pre-filter grill, HEPA filter grill, balance, SS stools etc. Ensure the validity of area and dispensing booth cleaning.
- Ensure that environmental conditions in the dispensing room are within limit and same shall be recorded in respective log book and BMR. Ensure that Differential pressure of the area is within specified limit.
- Verify the status of calibration and pressure of RLAF (dispensing booth) unit.
- Check the calibration status of balance and ensure its calibration and daily weight verification record.
- Verify the material requisition, it should be checked by Production department & approved by QA Department.
- Ensure the availability of BMR.
- Verify the release status & retest validity period of each materials.
- Verify the rinse/swab sample release report (if any).
- Ensure the availability of hand gloves, nose mask & head-cover/cap.
- Ensure the proper gowning of personnel in the operational area.
- Check and ensure if any specific precautions are mentioned in the batch record.
- Check the status of calibration / preventive maintenance of equipment / instrument.
- Ensure that the qualified person involved in Dispensing.
- Line clearance before Manufacturing:
Following points shall be checked during line clearance before manufacturing and records shall be maintained in the BMR.
- Verify that the area should be free from previous product.
- Check the environmental condition and same shall be recorded. Ensure that Differential pressure of the area is within specified limit.
- Check and ensure the Area cleanliness and also validity of cleaning procedure adopted.
- Ensure that the drain is cleaned.
- Ensure that all materials and residues from previous operations have been removed.
- Ensure that utensils and accessories from previous operations have been removed.
- Ensure that storage vessel used for previous operations have been cleaned.
- Ensure that BMR and other paperwork from previous operations have been removed.
- Ensure that Status labels from previous operations have been removed.
- Ensure that all equipment’s should be cleaned and labeled.
- Ensure the cleaning of return riser filters and housing.
- Verify the equipment’s and utensils for cleaning, if there is product change over then swab/rinse test result shall comply with respect to specification (if applicable).
- Verify the calibration status of instrument.
- Check and ensure the balance calibration record.
- Verify the raw material quantity physically.
- Verify the raw material for its identity by matching the information given on the dispensing label with raw material requisition attached with BMR.
- Check and ensure if any specific precautions are mentioned in the batch record.
- Check the status of calibration / preventive maintenance of equipment / instrument.
- Ensure that the completion of logbook/record.
- Ensure that the material stored at controlled environmental condition.
- Line clearance for Packing Area:
- Ensure that the Packing area is cleaned.
- Ensure that the gowning procedure is followed.
- Ensure that status board is displayed with the updated batch details.
- Ensure that the excess packing material and rejects of previous batch are removed.
- Ensure all the accessories are visibly cleaned.
- Ensure that the equipment’s used in the packing area are cleaned.
- Daily Balance Performance checks and Balance Calibration records are updated.
- Ensure that all the logbooks pertaining to the machine are updated.
- Ensure that preventive maintenance of machines has been carried out as per the schedule and the equipment in affixed with preventive maintenance label.
- Ensure that packing materials required for batch are issued by warehouse and received by production and stored in specified crates duly wrapped with shrink film.
- Ensure that carton printing machine (ink jet) should be cleaned. Take a specimen of over printing on carton and signed by Production Officer and verified by QA Officer. Retain this specimen to Batch Packing Record.
- Line clearance shall be checked as per the checklist of the BPR by Production Officer, verified and signed by QA person.
- Ensure that the coded shipper & the stereo of previous batch are removed from the area.
- Take a specimen of shipper coding on a paper signed by Production Officer and verified by QA Officer. Retain this specimen to Batch Packing Record.
- Ensure that the activity is started within the same shift in which the line clearance is given by QA and if activity is not started within the same shift, then verification of line clearance activity shall be done before starting the activity in the subsequent shift. Remark to be mentioned in the batch record with sign for the same.
- Ensure that the activity is re-started within the same shift in which the process break has been occurred, if not re-started in the same shift in which process break has been occurred then, verification of line clearance activity shall be done before re-start of activity in the subsequent shift. Remark to be mentioned in the batch record with sign for the same.
- In case of any observation which is not acceptable or a nonconformance (i.e., product / material / document pertaining to previous product, incomplete / wrong documentation & any foreign particle / things not pertaining to that area etc.) inform to concern officer /executive present on duty. Initiate incident and complete the investigation along with corrective & preventive action.
- Record the approval for the area and equipment clearance in the respective BMR/BPR.
- If same product runs in manufacturing and primary packing area then it can be run up to 72 hours or maximum 5 consecutive batches (whichever is less) can be taken for manufacturing and primary packing. During batch changeover Type A cleaning shall be performed and after completion of 72 hours or 5 consecutive batches (whichever is less) type B cleaning shall be performed.
- REFERENCES:
- Not Applicable
- ANNEXURES:
ANNEXURE No. | TITLE OF ANNEXURE | FORMAT No. |
Annexure-I | Area / Line Clearance Checklist For Raw Material Dispensing | QA-007/F01-00 |
Annexure-II | Area / Line Clearance Checklist For Manufacturing Area | QA-007/F02-00 |
Annexure-III | Area / Line Clearance Checklist For Primary/Secondary packing | QA-007/F03-00 |
Annexure-IV | Area / Line Clearance Checklist For Visual Inspection | QA-007/F04-00 |
ENCLOSURES: SOP Training Record.
- DISTRIBUTION:
Controlled Copy No. 01 | : | Head Quality Assurance |
Controlled Copy No. 02 | : | Head Production |
Controlled Copy No. 03 | : | Head Warehouse |
Master Copy | : | Quality Assurance Department |
- ABBREVIATIONS:
QA | : | Quality Assurance |
SOP | : | Standard Operating Procedure |
BMR | : | Batch Manufacturing Record |
No. | : | Number |
BPR | : | Batch Packing Record |
RLAF | : | Reverse Laminar Air Flow |
HVAC | : | Heating Ventilation and Air Conditioning |
IPQA | : | In-process Quality Assurance |
RH | : | Relative Humidity |
DP | : | Differential Pressure |
HEPA | : | High Efficiency Particulate Air |
QC | : | Quality Control |
SS | : | Stainless Steel |
REVISION HISTORY:
CHANGE HISTORY LOG
Revision No. | Details of Change | Reason for Change | Effective Date |
00 | New SOP | Not Applicable | To be mention manual |
ANNEXURE – I
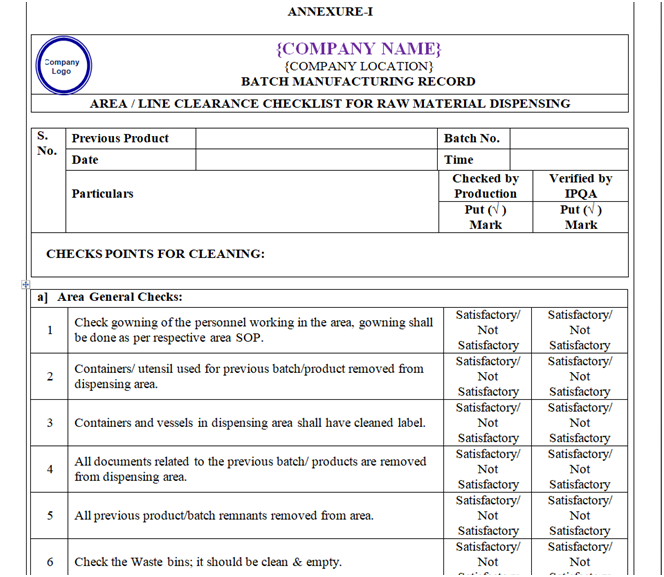
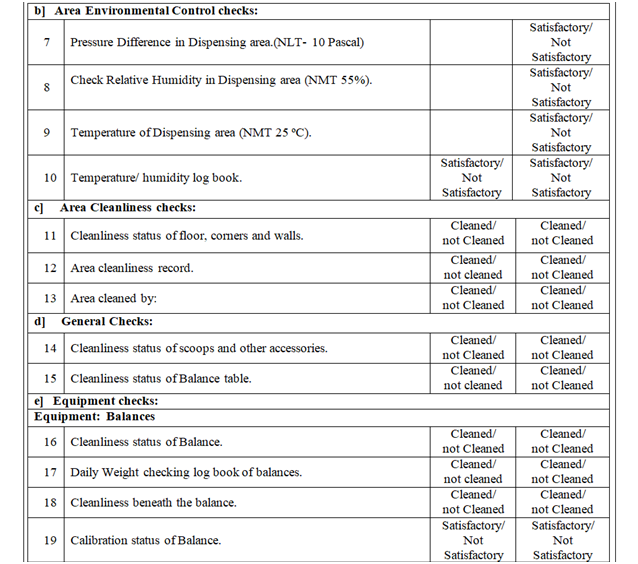
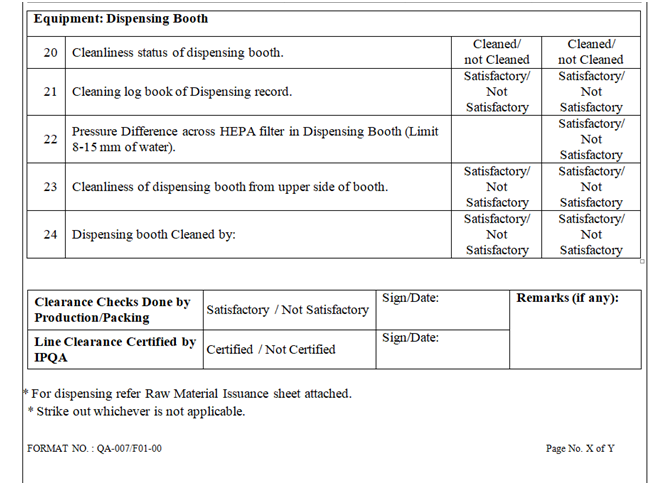
ANNEXURE – II
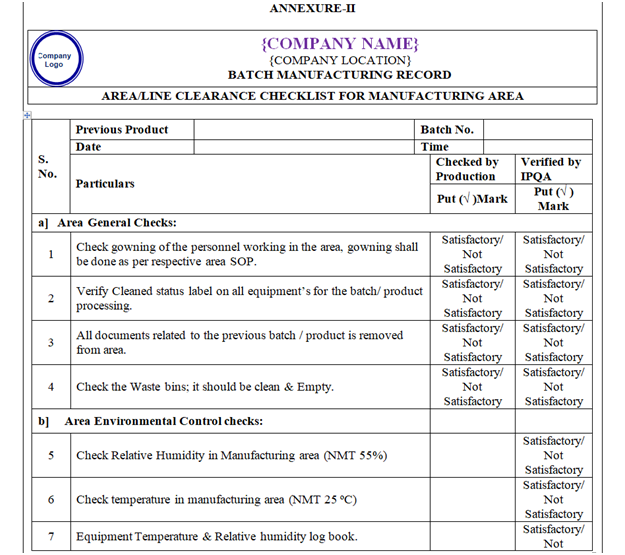
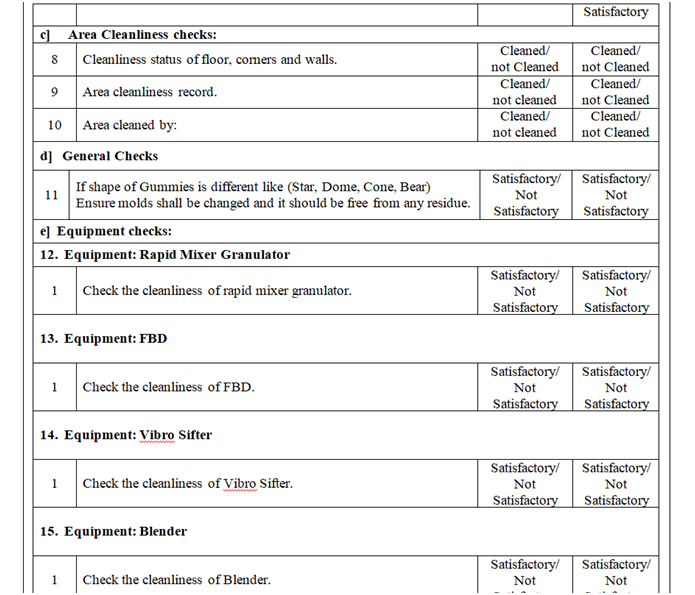
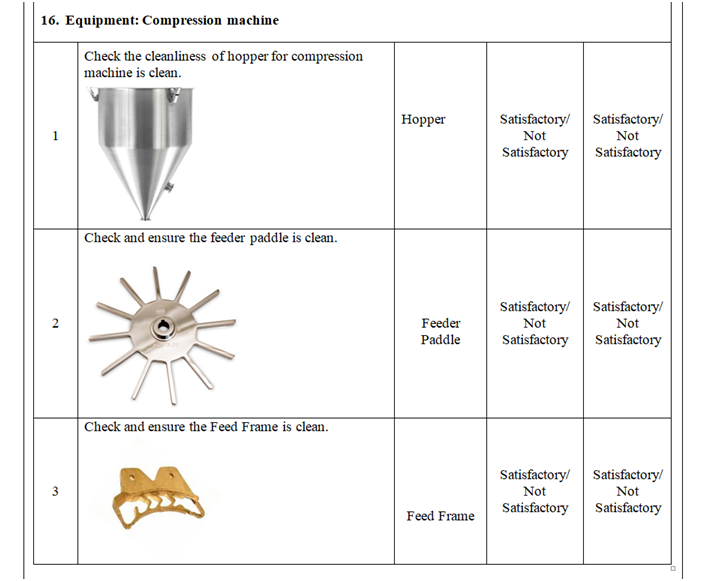
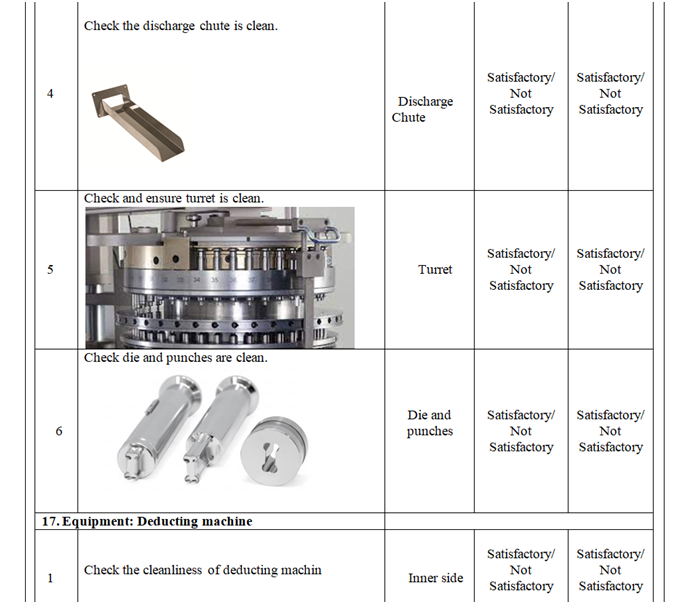
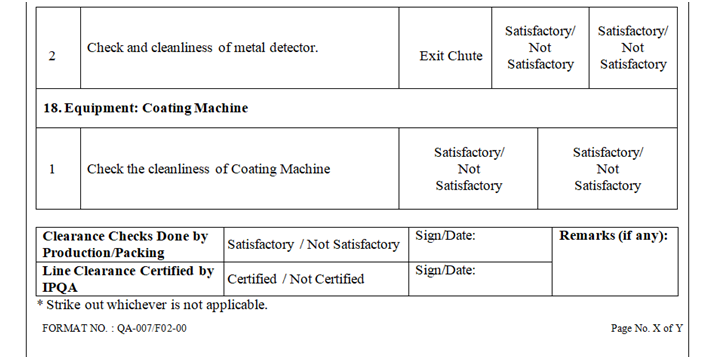
ANNEXURE-III
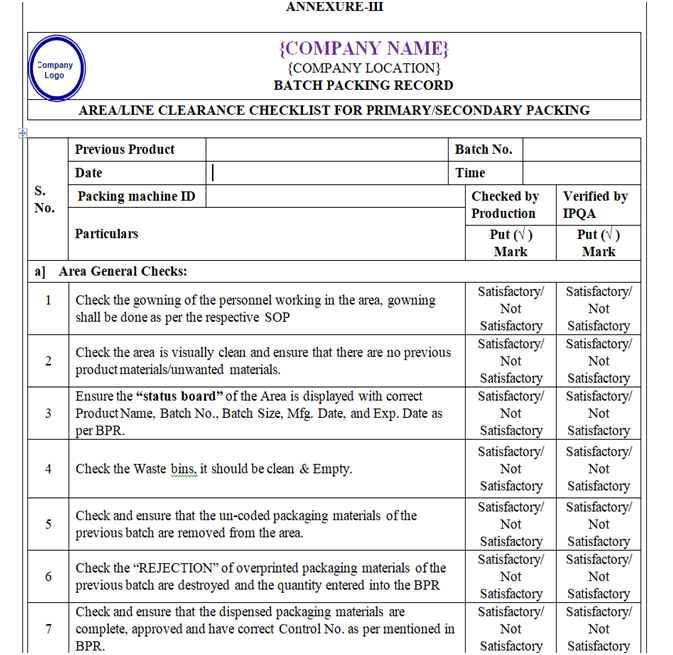
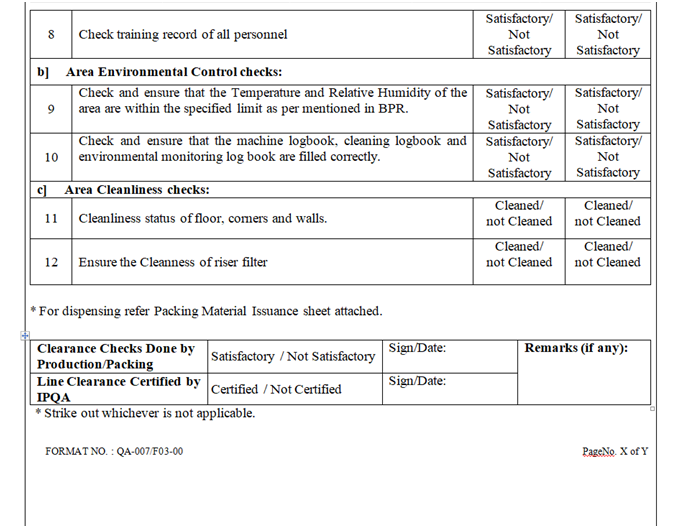
ANNEXURE – IV
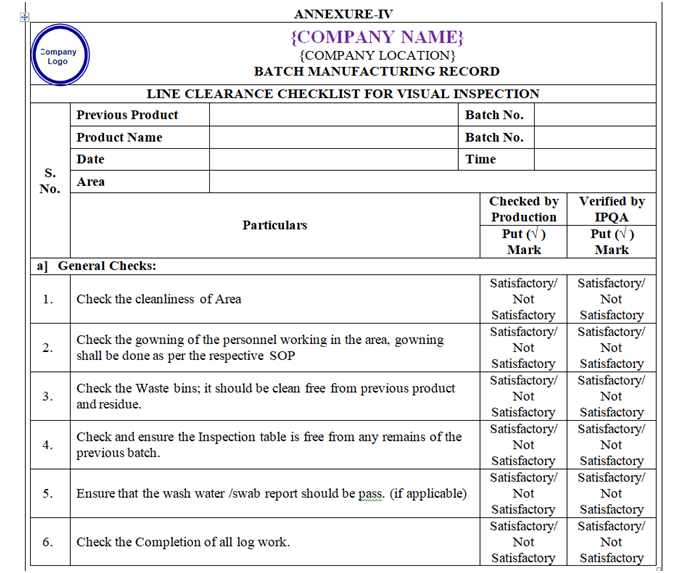
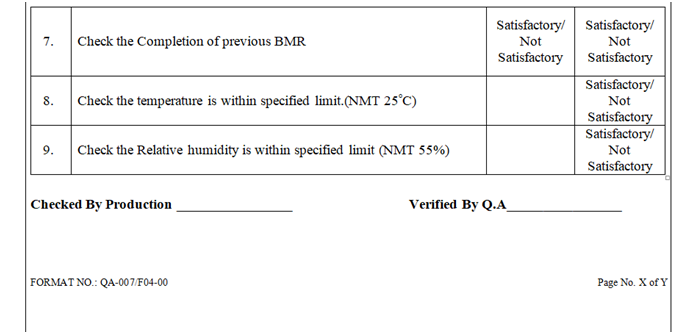