OBJECTIVE:
To lay down a Procedure for Vendor Qualification.
SCOPE:
This SOP is applicable to Qualification and Approval of Raw Material and Packaging Material Vendors of {Company Name} {Location}.
RESPONSIBILITY:
Quality Assurance – Execution as per laid down procedure.
Purchase Manager– Co-ordination with the vendor & execution as per the laid procedure.
ACCOUNTABILITY:
QA manager shall be accountable for approval and implementation of SOP.
About Vendor Qualification:
Vendor qualification in the pharmaceutical industry is a critical process to ensure the consistent supply of high-quality materials and services. It involves a rigorous evaluation of potential vendors based on various factors, including quality management systems, manufacturing processes, experience, financial stability, and regulatory compliance. This assessment aims to minimize risks associated with product quality, safety, and efficacy. Key aspects of vendor qualification include:
Performance Monitoring: Continuously evaluating vendor performance and addressing any deviations.
Quality Agreements: Formal contracts outlining quality expectations and responsibilities.
Risk Assessments: Identifying and mitigating potential risks associated with each vendor.
Regular Audits: Conducting on-site audits to verify compliance with quality standards.
PROCEDURE:
Vendor For Raw Materials (Active & Excipients) And Packaging Materials:
Concerned Department shall give written information through Inter Office Memo (IOM) to Purchase Department about the material required and the quantity required.
On the receipt of IOM, the Purchase Department shall identify the vendor for required material and after identification, thePurchase Department shall initiate for vendor assessment.
Quality Control Department / QA Department shall provide the specifications for the material to be used in product.
QA Department shall provide Vendor / Supplier Assessment Questionnaire as per Format shown in Annexure-I & II toPurchaseDepartment.
The Purchase Department shall send “Vendor Assessment Questionnaire” (as per Annexure-I) to proposed Manufacturer and “Supplier Assessment Questionnaire” (as per Annexure-II) to proposed Supplier.
Filled Questionnairefrom Manufacturer / Supplier shall be received back by Purchase Department and the same shall be forwarded to QA department for evaluation.
After evaluation of the Questionnaire, QA Manager shall evaluate the information furnished by the vendor.
If vendor qualifies and meets the requirement of cGMP based on questionnaire, Purchase Department personnel shall procure at least three samples of different batches with sufficient quantity of the material along with certificate of analysis.
The procured samples shall be handed over to Quality Control Department along with the certificate of analysis by QA Department.
Click the link for download word file copy of this document: https://pharmaguidehub.com/product/vendor-qualification/
After evaluation of vendor if any gaps are observed then same shall be intimated to vendor for correction. If the gap comes under minor category (which are not impact on product quality, safety and efficacy) then based on the documented evidence of correction, the vendor can be approved. If major and critical gaps (which moderately and significantly impact on product quality, safety and efficacy) will be observed then the gaps will be intimated to the vendor and after getting correction, along with gap verification a physical audit by Manager Quality Assurance or his designee, designated team or a designated trained person as per Annexure III (for raw material) or Annexure IV (For packing material) shall be performed.
The audit team comprises of responsible person of QA / Production / Purchase / Commercial.
In the case of conducting vendor facility audit, QA Department shall intimate to Purchase Department for Vendor Facility Audit and the Purchase Department shall intimate the same to vendor with date and time along with the number of persons in audit team.
After confirmation of Audit dates from Vendor, Audit Agenda shall be prepared by QA as shown in Annexure-XI (Remove word Raw or Packaging which ever not applicable) by adding information of Material, Vendor, Auditee, Auditor & Audit scheduleand send to the respective vendor through mail or courier; copy of same shall be kept for record.
Vendor Audit Checklist shall be issued by QA along with Audit Report Number.
Vendor Audit report shall be prepared by Lead Auditor as per format shown in Annexure-IX.
Vendor Audit Report shall be send to respective Vendor within 15 Days of Audit by QA Department.
In case of overseas vendor, vendor evaluation & approval shall be made on the basis of analysis of Samples of three batches.
Overseas vendor can also be approved if Site / Material already approved by USFDA / MHRA / ANVISA / WHO / EU or on the basis of information available on Internet / Official web sites of Manufacturer or on the basis copy of approval received from vendor.
The following Vendors / Suppliers can be approved on the basis of Questionnaire.
Vendors Audit can be eliminated if the vendor is supplying its products to customer in Regulatory Country.
Vendors shall be directly approved if the company has any regulatory approvals for site, like USFDA / MHRA / ANVISA / WHO / EU / WHO Geneva/ FSSAI/Ayush licence registered or licensed from other regulatory authorities.
It is recommended to have food grade certificates for applicable food processing aids from suppliers.
Audit Report Numbering System:
All Vendor Audit Checklist shall contain a Audit Report No., which consist of an Nine alphanumerical characters as shown below :
Where,
“PGH” denotes Pharmaguidehub {Company Name}
“VA” denotes Vendor Audit
“/” denotes as Separator.
“25” denotes Year.
“001” denotes Serial Number
For Example, First Vendor Audit Report for the year 2018 shall be numbered as PGH/VA/25/001, PGH/VA/25/002,
Details of Audit Report Number shall be maintained in Annexure-V by QA.
After satisfactory vendor site Audit, vendor shall be asked to supply three commercial consignments preferably from three different batches.
After reviewing, the results of these consignments, Quality Assurance Department shall prepare a Vendor Qualification Report as shown in Annexure-VI.
On satisfactory completion of all steps of Vendor Qualification process, a written approval or disapproval of the vendor for the specific material shall be provided by QA to the Purchase Department
Purchase Department shall communicate the approval or disapproval status to the vendor.
After satisfactory auditing of Vendor QA Department shall get technical agreement of raw material and packing material as per Annexure-XVI & Annexure-XVII.
The Purchase Department will accordingly request for additional commercial quantities of the material from the vendor.
For each material that successfully completes the qualification process, QA shall issuea Vendor code for the material approved.
A Separate Raw and Packaging Material list of Approved Vendors shall be maintained by QA in a Format Shown in Annexure-VII and a copy of the same shall be issued to QC, Production, and Warehouse, Purchase Department. This list shall be updated by QA, periodically.
Click the link for download word file copy of this document: https://pharmaguidehub.com/product/vendor-qualification/
RE-EVALUATION / RENEWAL OF QUALIFICATION OF EXISTING VENDOR:
For the exiting vendor, from which company is procuring material can be approved retrospectively by evaluating the data of number of batches procured, number of batches Approved and Rejected.
After receiving the approval, any major changes to material’s Specification, Process Control, Raw Material Source, Equipment, Manufacturing Site, Testing, or any other criteria determined by the vendor to be necessary or significant shall be reported to {Company Name} in writing.
The written report shall include detail of changes and also the data from three lots manufactured prior to the change and three lots manufactured after the change.
On receipt of such report, {Company Name} QA shall expedite the review of such change and communicate its decision at the earliest to the Purchase Department, who in turn will communicate to the Vendor.
QC shall perform at a minimum an annual evaluation of the Approved Material from the specific vendor to ensure that it continues to meet the criteria.
Requalification of Vendor:
Vendor shall be requalified at the frequency of 5 Years or as when required.
Vendor Assessment :
Such “Quality Score” shall include review of the critical quality attributes, which are trended for all the batches tested and analyzed over the period of evaluation. This shall be documented.
Continuous Evaluation of supply for Quality (Q-Score):
Performance of all vendors shall be evaluated annually by calculation of their Q score.
Annual Risk Assessment:
Risk Assessment shall be performed for all the vendors of API, Excipient and Primary Packaging Materials once in a year by the Site QA.
Site shall create and maintain a list of all existing and potential vendors of API, Excipients and Primary Packing Materials for the assessment period.
Identify source of information of the vendors and analyze the information to determine the risk of an individual vendor.
Classify the potential risks arising from assessment of each category/ parameter into different levels namely High, Medium, and Low.
Depending on risk level of parameter used for evaluation, a risk factor shall be assigned.
By using the potential risk for each category and risk factors, a Risk Priority Number (RPN) shall be calculated (quantitatively).
Risk factors can be grouped into three categories as shown in the following table (1).
Category | Typical parameters for assessment |
Severity | Criticality of material and impact on end product quality |
Probability | Supply history of vendor and status of Quality Systems of the vendor |
Detection | Possibility of detecting quality failures for a material and the stage at which detection is possible (e.g. incoming inspection, final testing, etc.) |
Severity: This category describes the criticality of material for quality of end product. Assessment for this category shall be done as per Below Table (2)
Table (2) Potential impact level of category “ Severity ”
Assessment Criteria | Impact Assessment of Risk level | Risk Factor |
Material under consideration is API | High | 10 |
Material under consideration is Excipients | Medium | 8 |
Material under consideration is primary packing | Low | 4 |
Probability of Occurrence: This category considers the past supply history (from a quality perspective), product SISPQ (Safety, Integrity, Strength, Purity and Quality) requirement compliance status and state of quality systems of a vendor.
The risk criteria “compliance” classifies the product SISPQ requirement compliance and regulatory compliance status of the vendor using all available information from the company’s quality management systems.
Data for parameter ‘Compliance’ can be taken from different sources, for example, the previous audits, assessment of information’s provided by vendor in vendor questionnaire etc. If the compliance status is unknown, the highest risk level shall be used.
Supply History of vendor will be calculated by considering Q score of vendor. In case of a new vendor or existing vendor for new material where no previous Q score is available, for impact assessment of this parameter it will be considered as high risk.
Assessment for parameters “supply history of vendor” and “compliance” shall be done as per table No. 3 or 4.
Table 3: Potential impact level of Category “Supply History of Vendor” If total batch received in year is 1-2 than the risk factor shall be considered as 10 batch received in year is 3-5 risk factor shall be considered as 8 batch received in year is 6-10 than the risk factor shall be considered as 6 received in year is more than 10 than risk factor shall be considered as 4.
Assessment Criteria | Impact Assessment of risk level | Risk factor |
Quality Score for current year | ||
1-2 | High | 10 |
3-5 | Medium | 8 |
6-10 | Low | 6 |
>10 | Negligible | 4 |
In case there is no supply history for a particular material for the previous three years, if the vendor however has been supplying other materials regularly from the same site, assessment may be done based on the supply history of the other materials being regularly supplied by vendor from the same manufacturing site.
Table 4: Potential impact level of Category “Probability” and parameter “Compliance”
Assessment Criteria | Impact Assessment of Risk level | Risk Factor |
Compliance status by {COMPANY NAME} audit or inspection by competent regulatory authority (USFDA, FDQM, Japanese or any European health authority , WHO, TGA, Indian FDA, ANVISA, FSSAI, ISO, IPEC etc.) but older than 3 years or more for API and older than 5 years or more for immediate and primary packing material. | High | 10 |
Compliance status by {COMPANY NAME} audit or inspection by competent regulatory authority (USFDA, FDQM, Japanese or any European health authority , WHO, TGA, Indian FDA, ANVISA, FSSAI, ISO, IPEC etc.) available but more than 2 years old for API and 4 years or more for immediate and primary packing material. | Medium | 6 |
Compliance status by {COMPANY NAME} audit or inspection by competent regulatory authority available , more than 1 year old, but less than or equal to 2 years for API and more than 3 years old, but less than or equal to 4 years for immediate and primary packing material. | Low | 4 |
Vendor is audited by {COMPANY NAME} in last one year for API and last 3 years for immediate and primary packing material | Negligible | 1 |
The total risk for category Probability shall be arrived at by averaging risk factor of each parameter assessed under this category.
Total Risk (Probability) = {Risk factor (Supply History of vendor)) + Risk factor (Compliance)} / 2.
Click the link for download word file copy of this document: https://pharmaguidehub.com/product/vendor-qualification/
Detection: This category considers Possibility of detecting quality failures for a material and the stage at which detection is possible and the assessment shall be carried out as per Table 5.
Table 5 : Risk Assessment for detecting possible quality failure for a material at various stages
Assessment Criteria | Impact Assessment of risk level | Risk Factor |
Can be detected at In Process /Intermediate stage/At finished product stage only | High | 10 |
Can be detected during testing only but reduced testing performed. | Medium | 6 |
Can be detected at receipt stage. No reduced testing performed however reduced sampling is done and vice versa | Low | 2 |
Can be detected at receipt stage. No reduced testing/ reduced sampling performed. | Negligible | 1 |
Evaluating the Total Risk Arising from a Vendor: The risks identified for all the three categories (Severity, Probability, and Detection) shall be evaluated for each individual vendor. Vendor’s overall risk priority number (RPN) can be calculated by multiplying the total risk of each category.
RPN = Risk factor of Severity x Probability x Detectability
In case of different RPN number obtained for different material/ material type by same vendor, the worst case shall be considered for deciding requirement of onsite audit of vendor.
RPN values obtained shall be used for sorting vendors according to their overall risk factor once in a year.
Risk Control Evaluation and Audit Plan:
Risk control evaluation shall involve focusing the scope of risk management by selectively reducing risk control for low-risk suppliers and increasing risk control for high-risk suppliers as per Table 6.
Table 6 : Risk control evaluation and audit plan
Risk Priority Number (RPN) | Action |
Less than or equal to 100 (Low risk ) | No further action required till the next risk assessment |
101-250 (Medium Risk ) | Audit shall be performed |
>250 (High Risk ) | All such vendor shall be included in annual audit plan for onsite audit |
For medium risk Vendors, Site QA shall prepare a list of Vendors (once in a year) to be considered for audit of the Vendors by reviewing the Vendor qualification documents without conducting a physical on-site audit of the manufacturing facility.
Vendor / Supplier Audit Details shall be recorded in the format shown in Annexure-V by QA.
If the Vendor is approved the details of vendor shall be incorporated by Purchase in records.
CRITERIA FOR DISCONTINUATION OF VENDOR:
If some discrepancy observed in the performance of vendor during one year span then vendor’s name shall be deleted from the Approved Vendor list.
Vendor can be Discontinue or Eliminate from the Approved Vendor list if its three continuous supplies does not match with pre-approved specification & termination Report shall be prepared by QA as per format shown in Annexure-X.
Vendor can be eliminated from vendor list if the vendor does not perform Vendor Audit at any defined frequency.
Vendor can be discontinue or deleted from approved vendor list if its manufacturing licence get supersede or cancelled / terminated by local or international regulatory agency.
Vendor can be eliminated from Approved Vendor list if the vendor change the manufacturing procedure without inform to {Company Name} QA.
Purchase Department shall communicate the disapproval / Termination status to the vendor.
{Company Name} QA shall inform to Purchase & Account Department for necessary action as per format shown in Annexure-X.
For Vendor Audit Flow Chart refer Annexure-VIII.
CRITERIA FOR AUDITOR SELECTION IN VENDOR AUDIT
The auditor shall be selected for vendor audit as per following points:
Having work experience 6 years or more than 6 years.
Practically handled a Regulatory audit.
Knowledge of Regulatory requirements and handled the regulatory audits.
Experience/Knowledge to perform the vendor audit.
List of Approved Auditor for vendor audit shall be prepared as per Annexure-XV.
REFERENCES:
Schedule M
ICH Harmonized Triplicate Guidelines
GUIDANCE DOCUMENT FOOD SAFETY MANAGEMENT SYSTEMS (Based on Part II of Schedule 4 of Food Safety & Standards (Licensing & Food Registration of Businesses) Regulation, 2011)
ANNEXURES:
ANNEXURE No. | TITLE OF ANNEXURE |
Annexure-I | Vendor Assessment Questionnaire |
Annexure-II | Supplier Assessment Questionnaire |
Annexure-III | Vendor Audit Checklist (Raw Material) |
Annexure-IV | Vendor Audit Checklist (Packaging Material) |
Annexure-V | Vendor Audit Log Book |
Annexure-VI | Vendor Qualification Report |
Annexure-VII | Approved Vendor List (Raw / Packaging Material) |
Annexure-VIII | Flow Chart For Vendor Qualification |
Annexure-IX | Vendor Audit Report |
Annexure-X | Vendor Termination Report |
Annexure-XI | Audit Agenda |
Annexure-XII | Vendor quality score record (Active Nutraceutical Ingredient) |
Annexure-XIII | Vendor quality score record (Excipient) |
Annexure-XIV | Vendor quality score record (packing material) |
Annexure-XV | List of approved auditors for vendor audit |
Annexure-XVI | Technical Agreement for Raw material vendors |
Annexure-XVII | Technical Agreement for Packing Material vendors |
ENCLOSURES: SOP Training Record.
DISTRIBUTION:
Controlled Copy No. 01 | : | Manger Quality Assurance |
Controlled Copy No. 02 | : | Manager Warehouse |
Controlled Copy No. 03 | : | Manager Quality Control |
Controlled Copy No. 04 | : | Manager Production |
Master Copy | : | Quality Assurance Department |
ABBREVIATIONS:
No. | : | Number |
Dept. | : | Department |
Ltd. | : | Limited |
QA | : | Quality Assurance |
SOP | : | Standard Operating Procedure |
QC | : | Quality Control |
FIFO | : | First in First Out |
FEFO | : | First Expiry First Out |
QA | : | Quality Assurance |
IOM | : | Inter Office Memo |
cGMP | : | Current Goods Manufacturing |
F&D | : | Formulation and Development |
IQ | : | Installation Qualification |
OQ | : | Operation Qualification |
PQ | : | Performance Qualification |
MOC | : | Material of Construction |
cGLP | : | Current Good Laboratories Practices |
RM | : | Raw Material |
PM | : | Packaging Material |
STP | : | Standard Testing Procedure |
ICH | : | International Conference on Harmonization of Technical Requirements for Registration of Pharmaceuticals for Human Use |
PQR | : | Product Quality Review |
REVISION HISTORY:
CHANGE HISTORY LOG
Revision No. | Details of Changes | Reason for Change | Effective Date |
00 | New SOP | Introduction of New SOP | To Be Written Manual |
Click the link for download word file copy of this document: https://pharmaguidehub.com/product/vendor-qualification/
ANNEXURE-I
VENDOR ASSESSMENT QUESTIONNAIRE
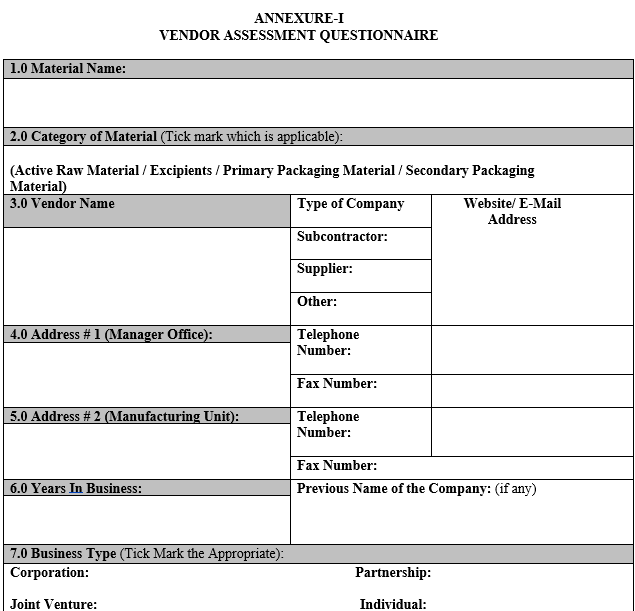
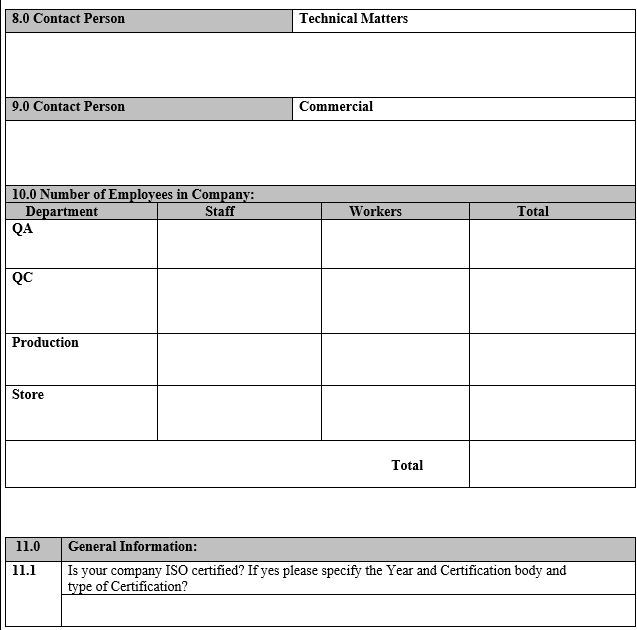
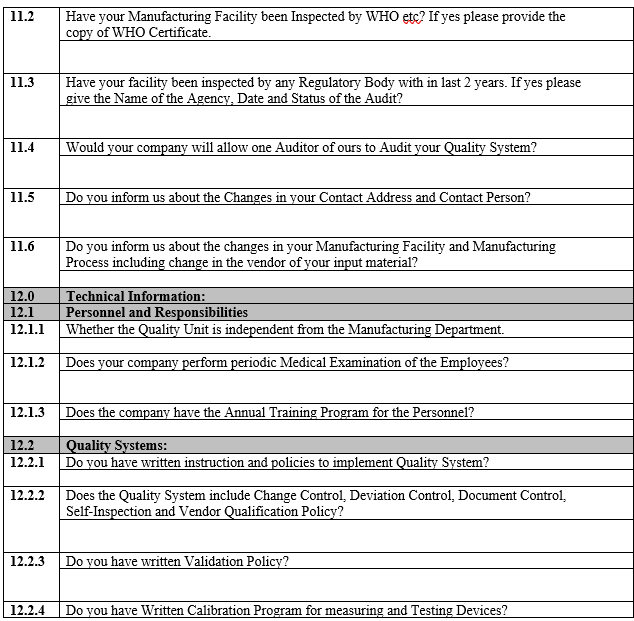
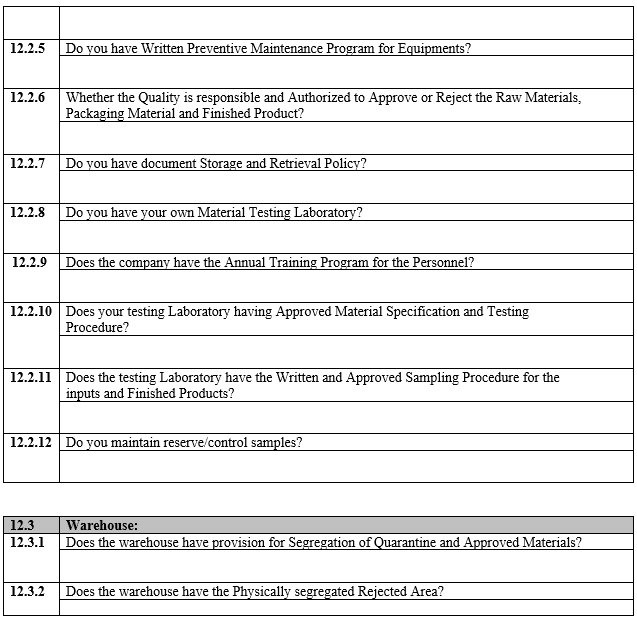
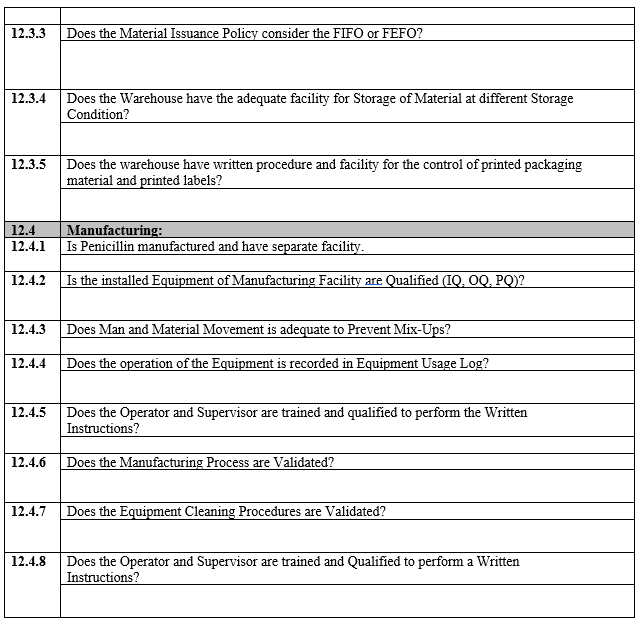
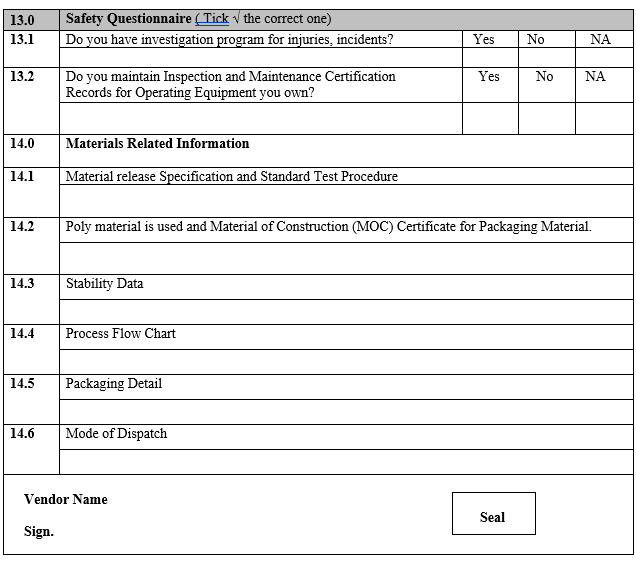
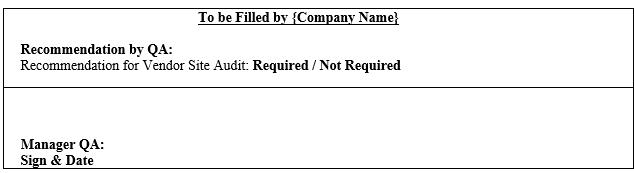
ANNEXURE-II
SUPPLIER ASSESSMENT QUESTIONNAIRE
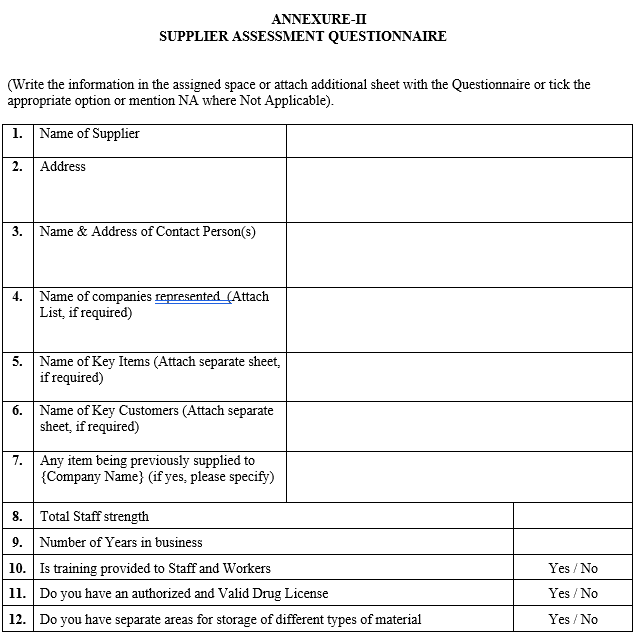
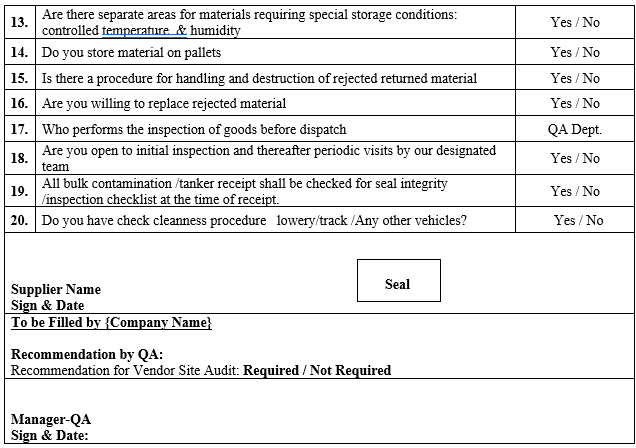
ANNEXURE-III
VENDOR AUDIT CHECKLIST (RAW MATERIAL)
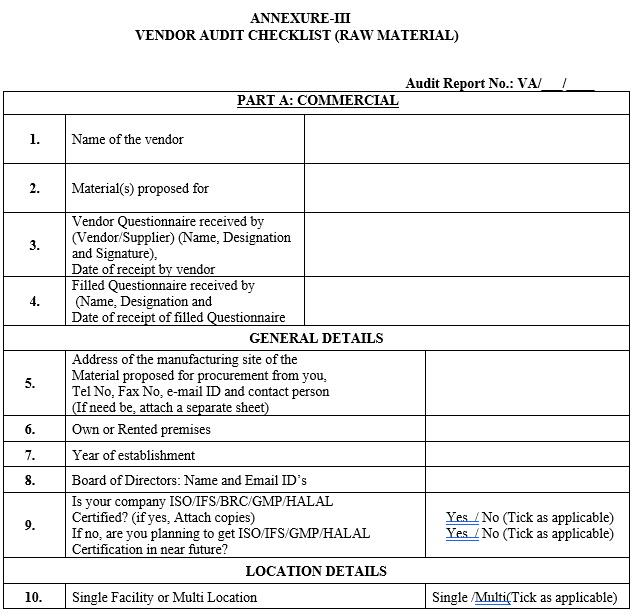
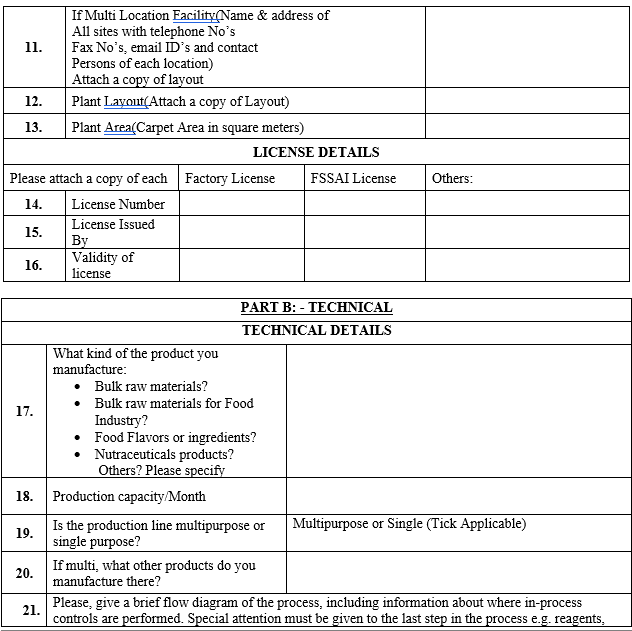
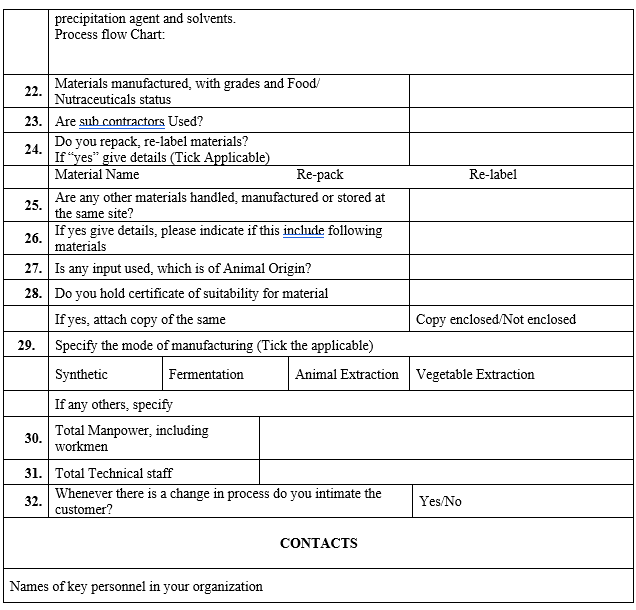
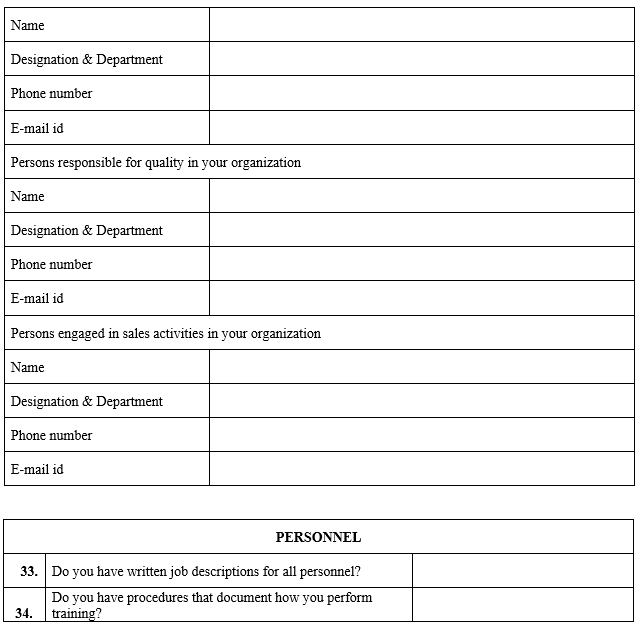
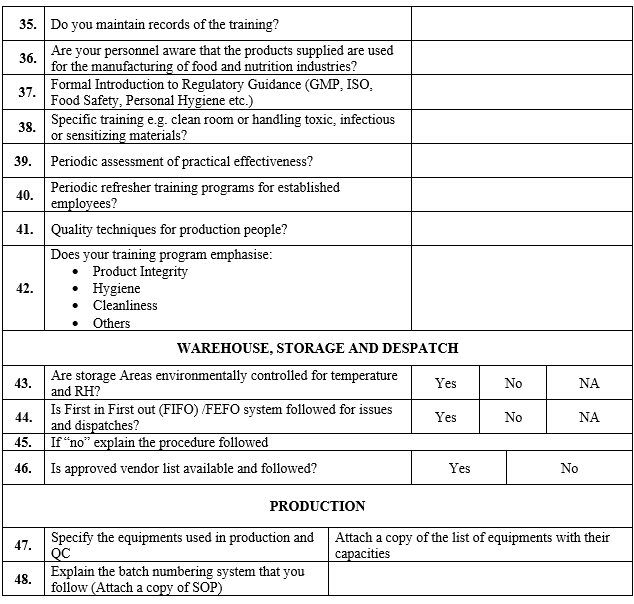
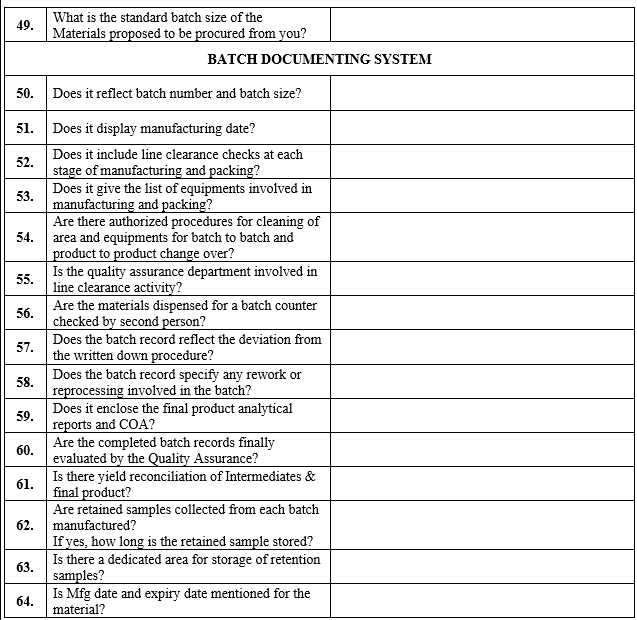
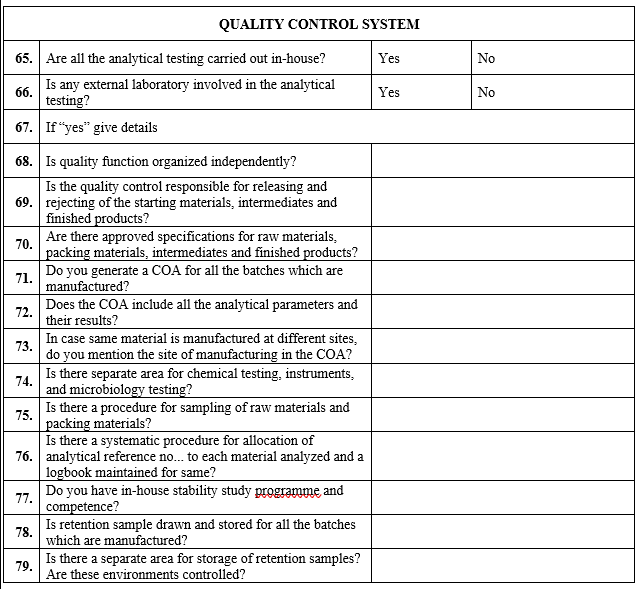
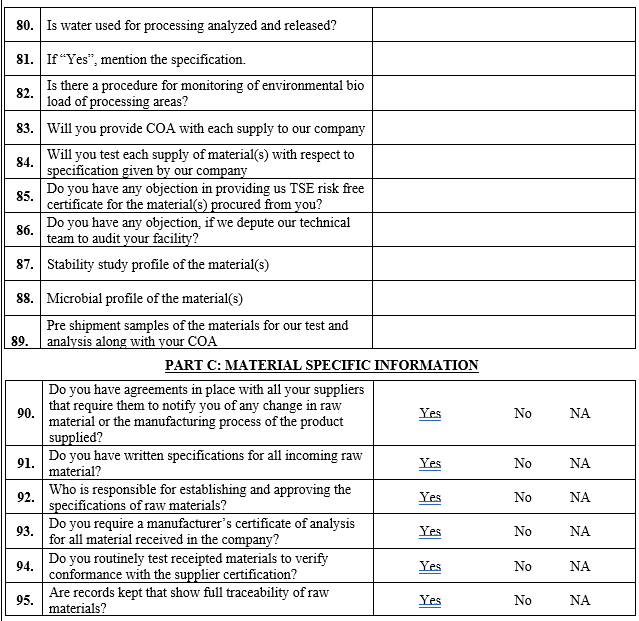
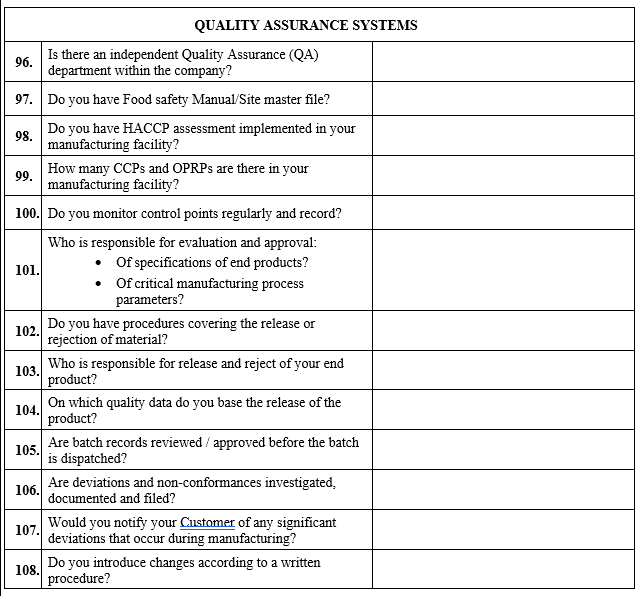
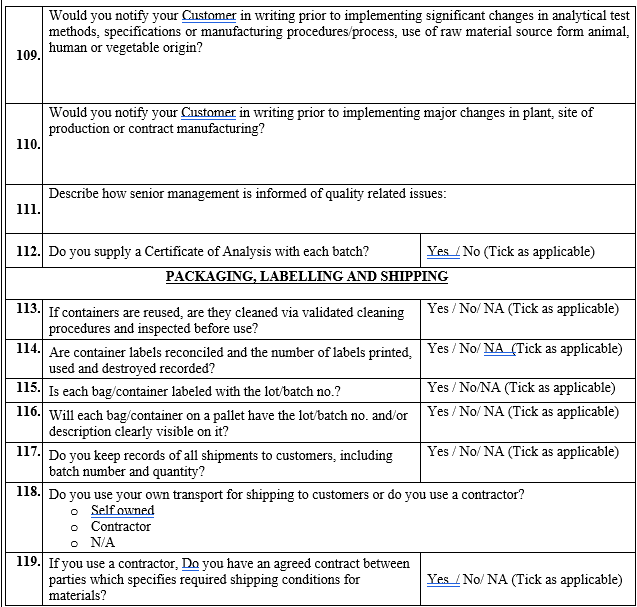
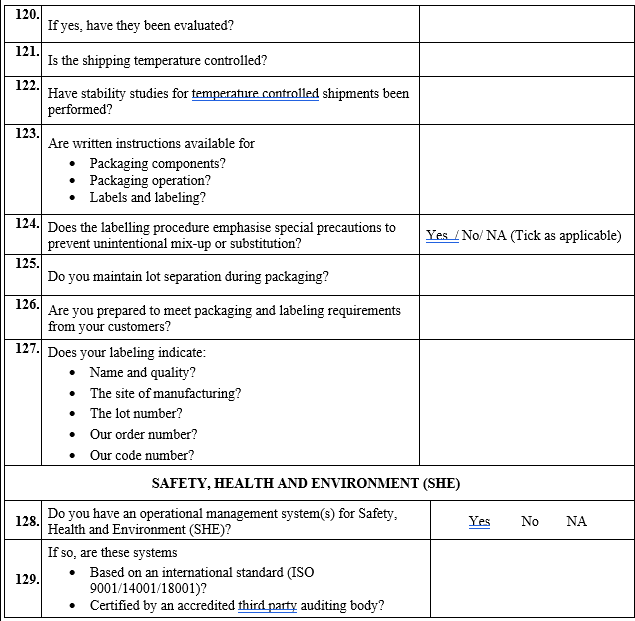
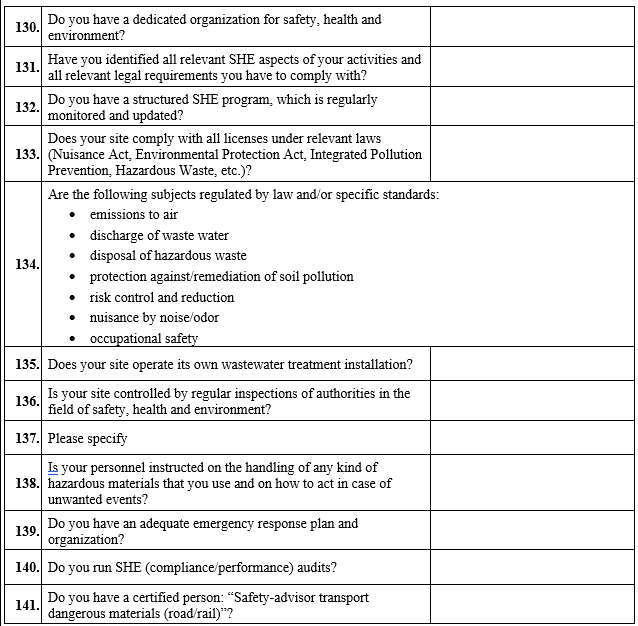
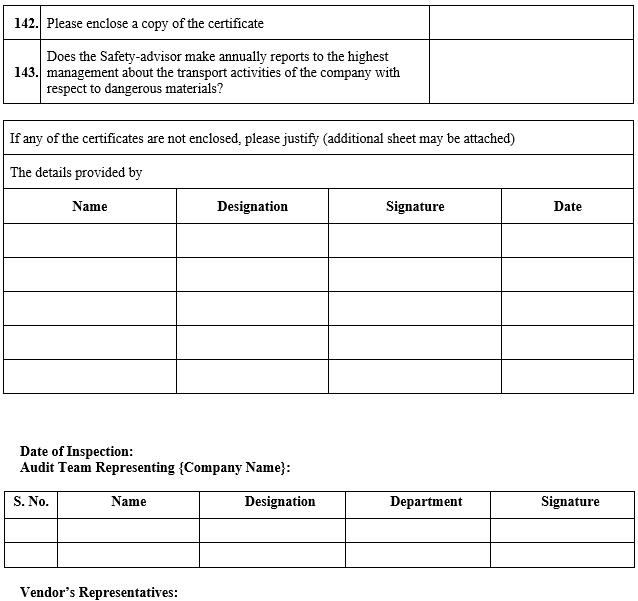
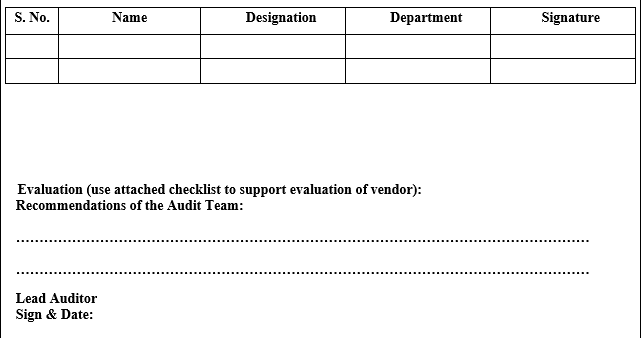
Click the link for download word file copy of this document: https://pharmaguidehub.com/product/vendor-qualification/
ANNEXURE-IV
VENDOR AUDIT CHECKLIST (PACKAGING MATERIAL)
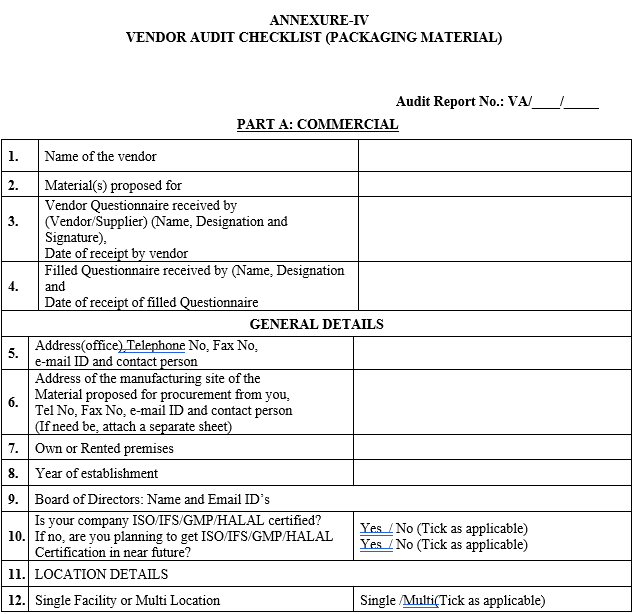
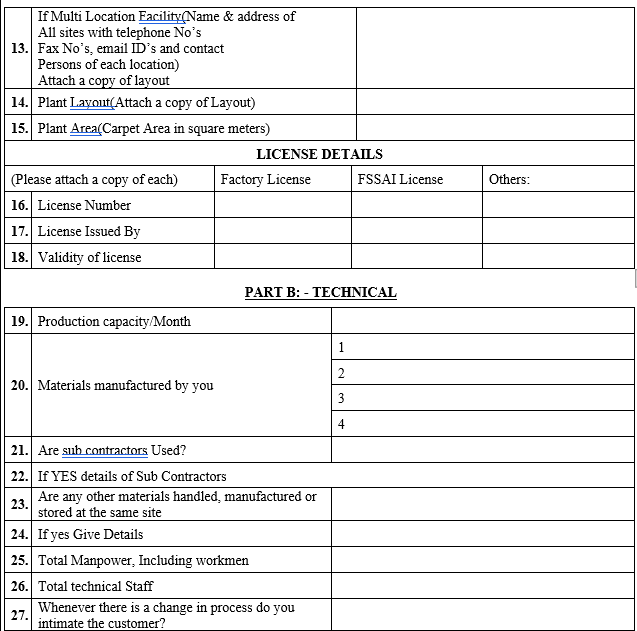
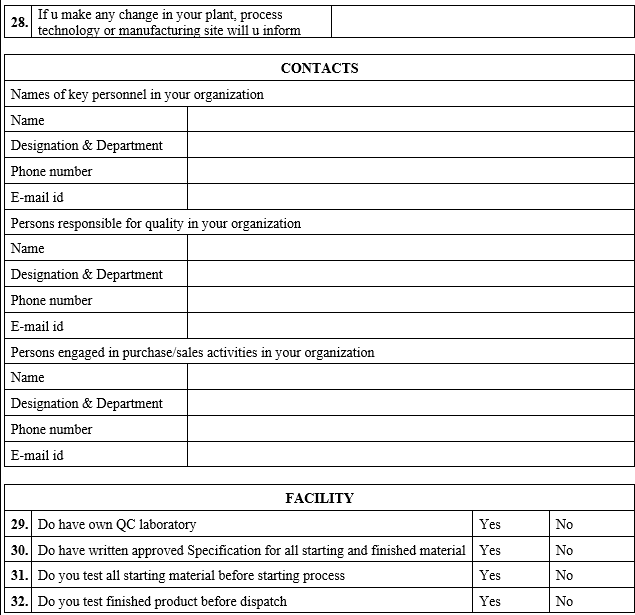
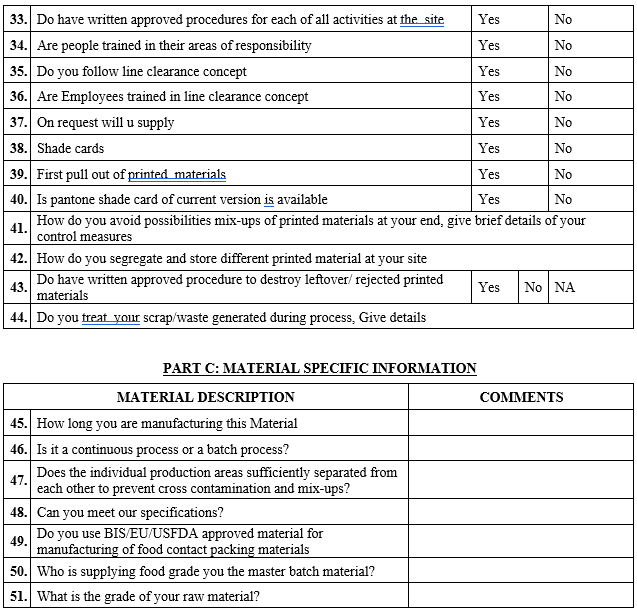
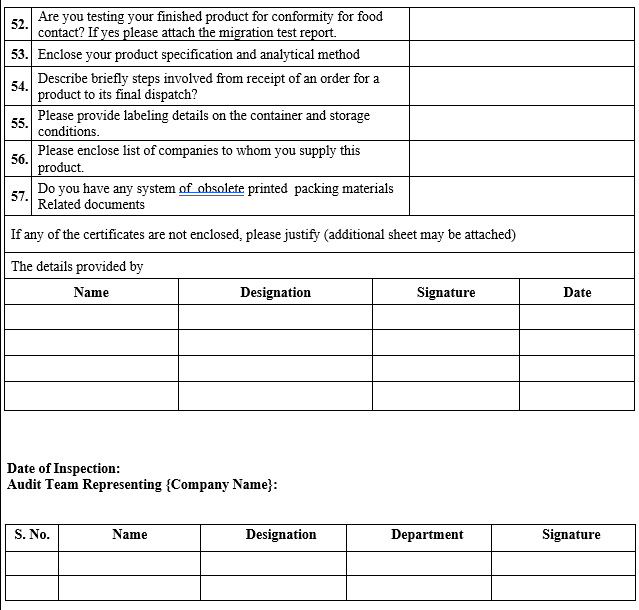
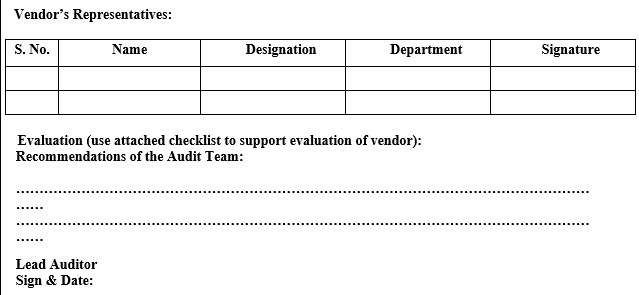
ANNEXURE – V
VENDOR AUDIT LOGBOOK
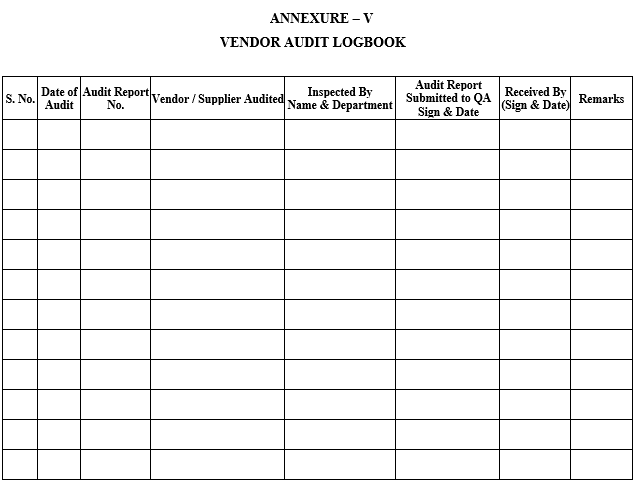
ANNEXURE-VI
VENDOR QUALIFICATION REPORT
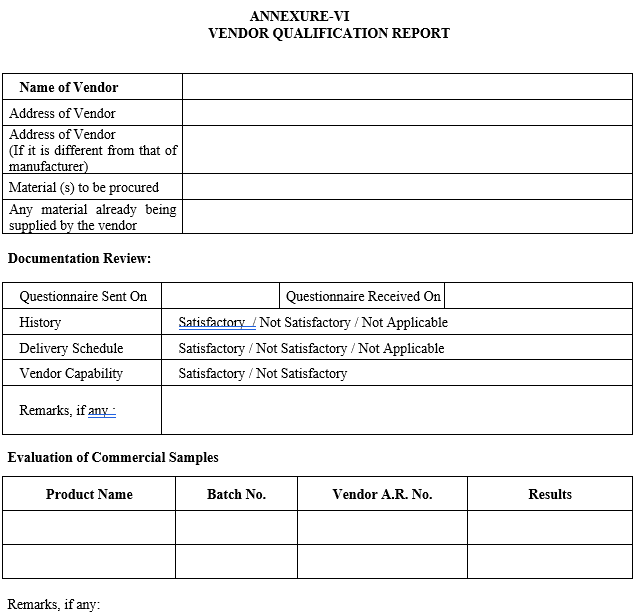
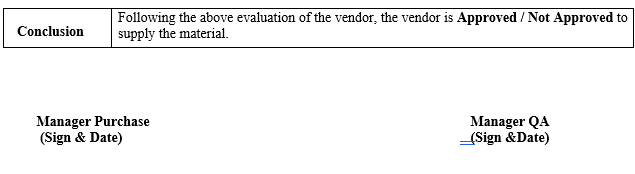
ANNEXURE – VII
APPROVED VENDOR LIST (RAW / PACKAGING MATERIAL)
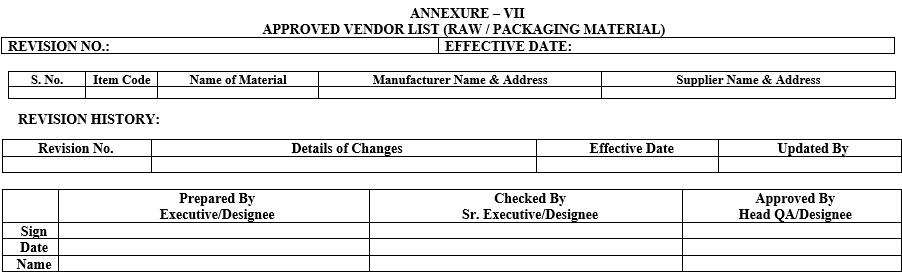
ANNEXURE – VIII
FLOW CHART FOR VENDOR QUALIFICATION
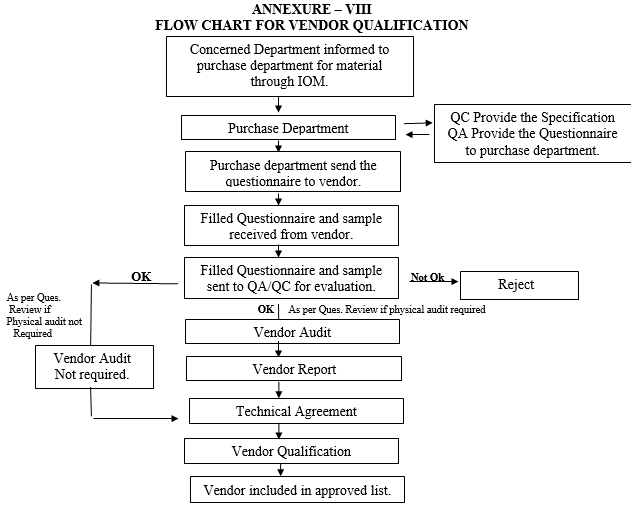
ANNEXURE – IX
VENDOR AUDIT REPORT
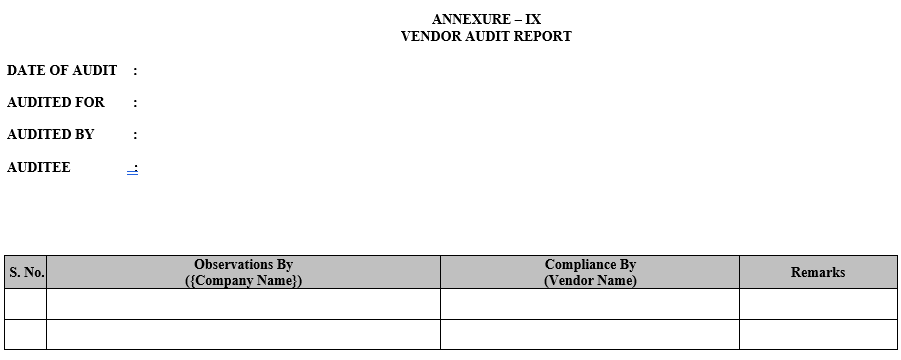
Recommendation:
Click the link for download word file copy of this document: https://pharmaguidehub.com/product/vendor-qualification/
ANNEXURE-X
VENDOR TERMINATION REPORT
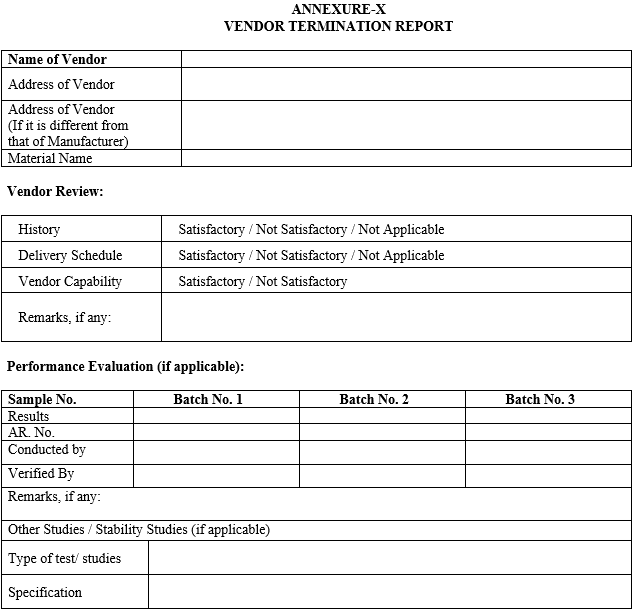
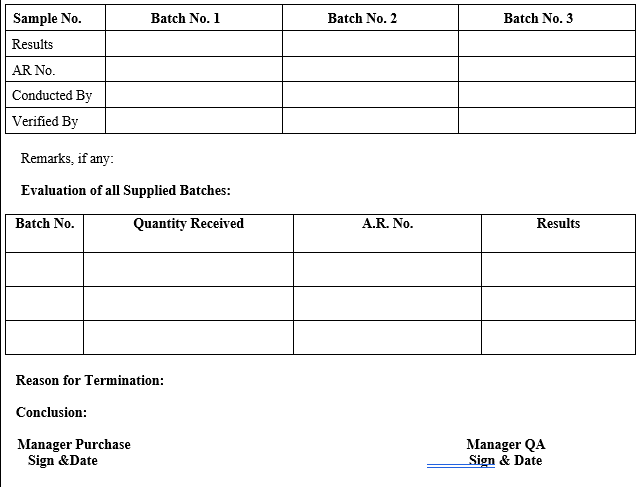
ANNEXURE-XI
AUDIT AGENDA
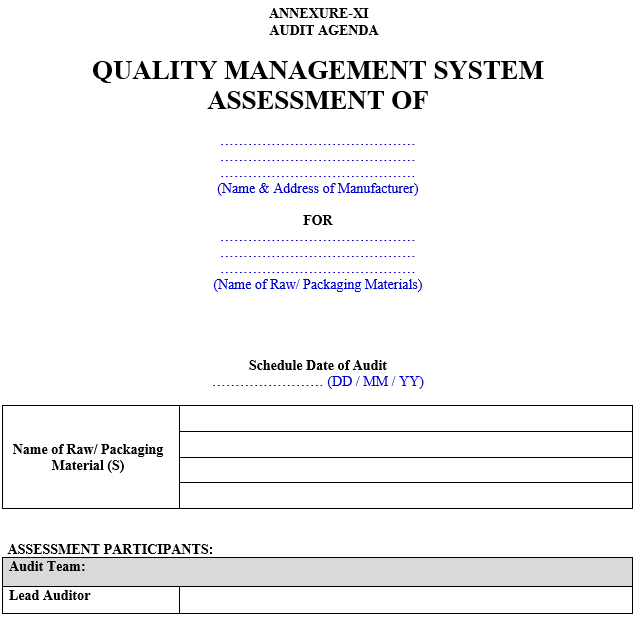
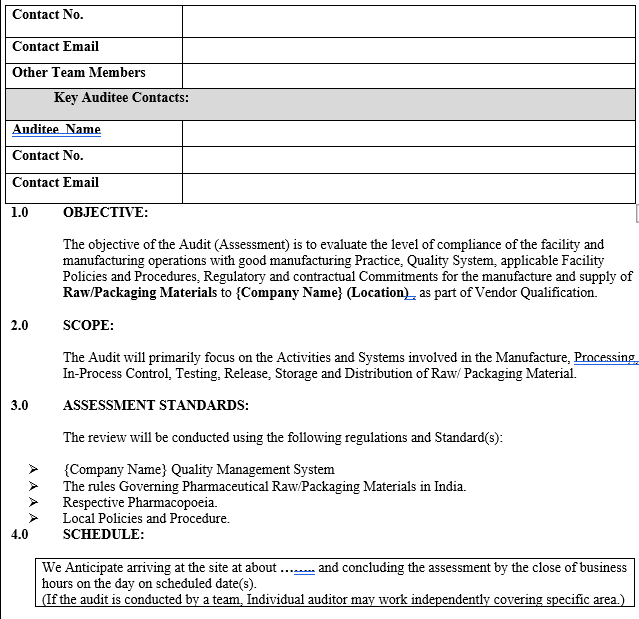
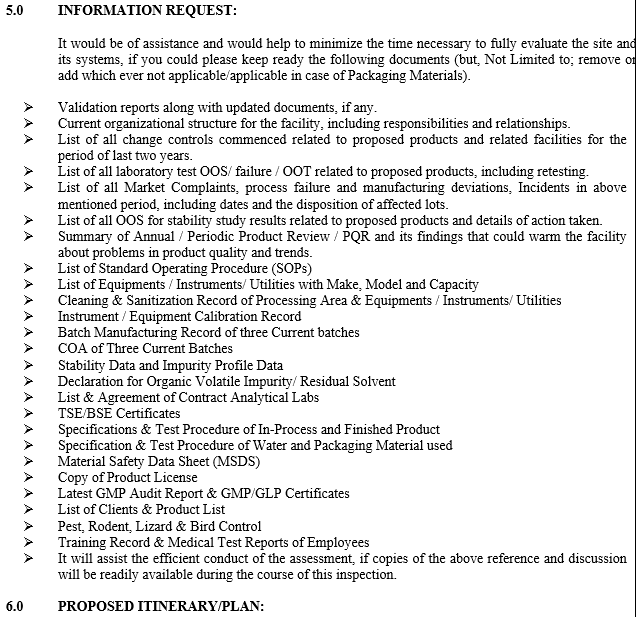
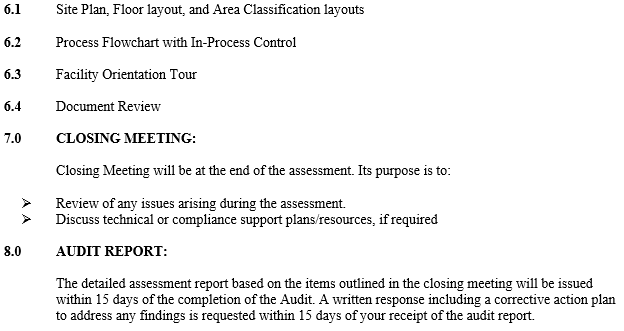
ANNEXURE-XII
VENDOR QUALITY SCORE RECORD (FOR ACTIVE NUTRACEUTICAL INGRIDIENT)
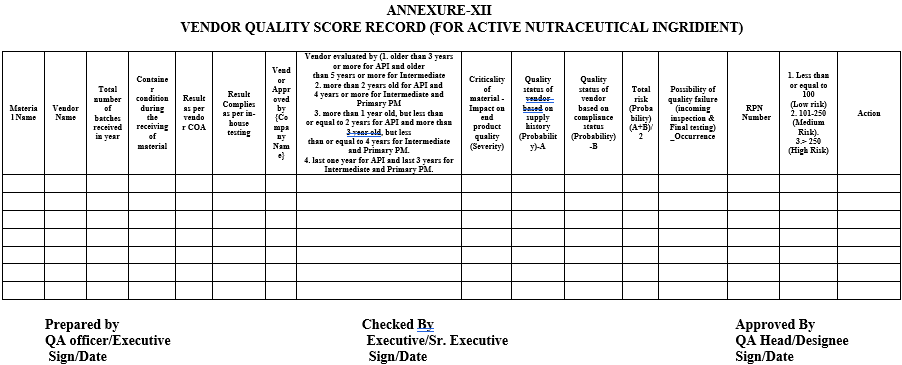
ANNEXURE-XIII
VENDOR QUALITY SCORE RECORD (EXCIPIENT)
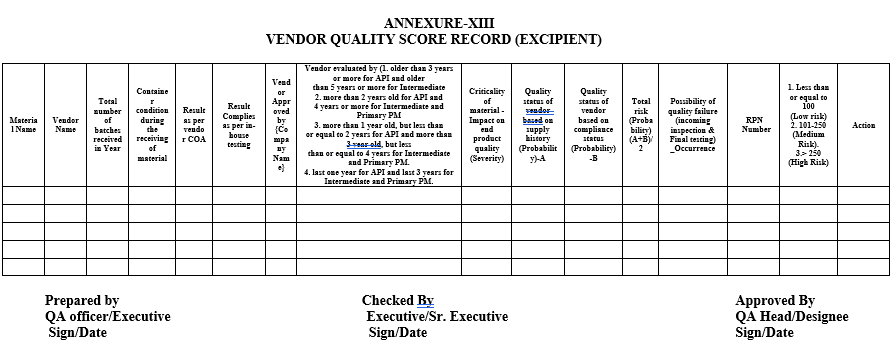
ANNEXURE-XIV
VENDOR QUALITY SCORE RECORD (PACKING MATERIAL)
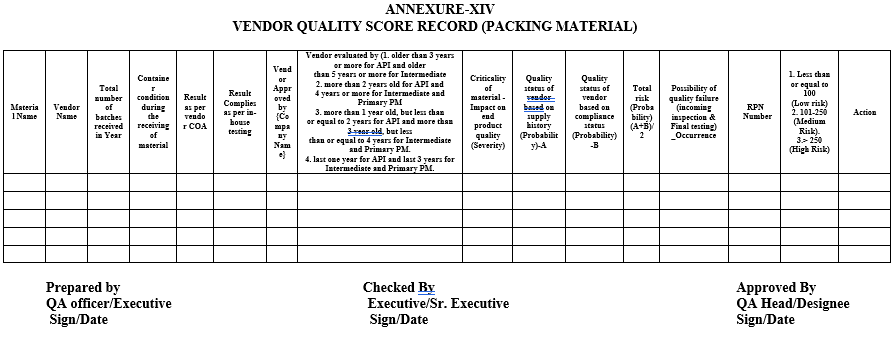
ANNEXURE-XV
LIST OF APPROVED AUDITORS FOR VENDOR AUDIT
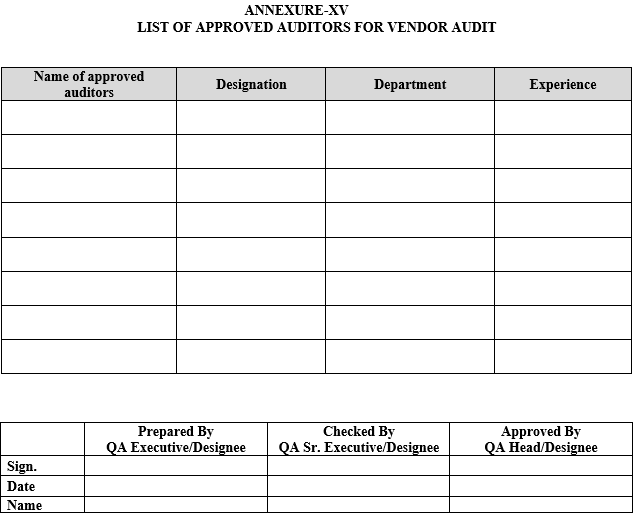
ANNEXURE-XVI
TECHNICAL AGREEMENT FOR RAW MATERIAL VENDORS
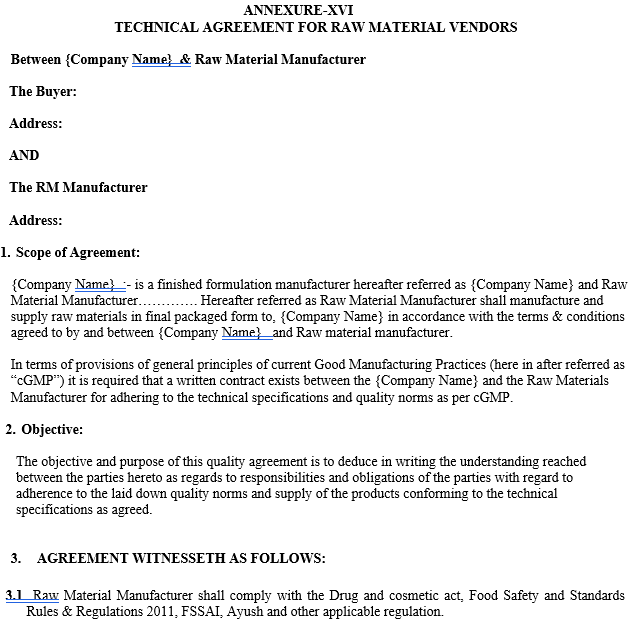
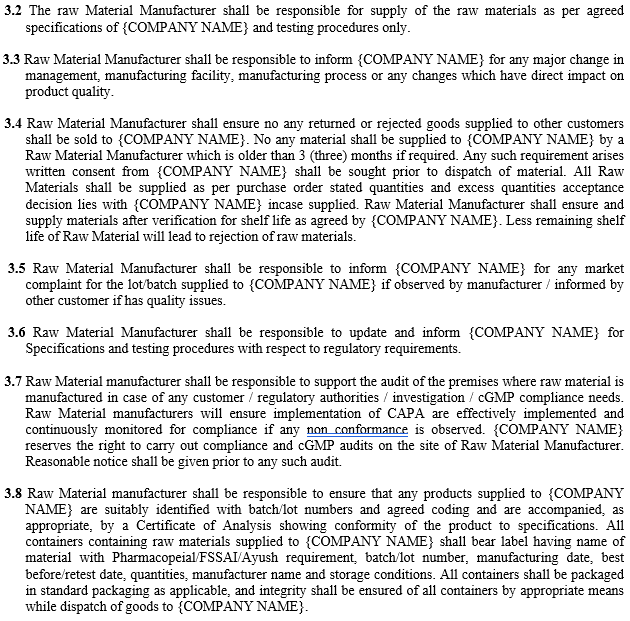

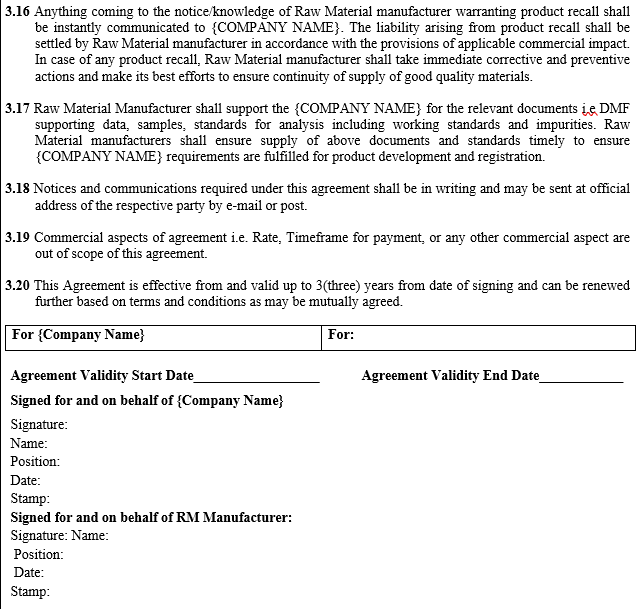
ANNEXURE-XVII
TECHNICAL AGREEMENT FOR PACKING MATERIAL VENDORS
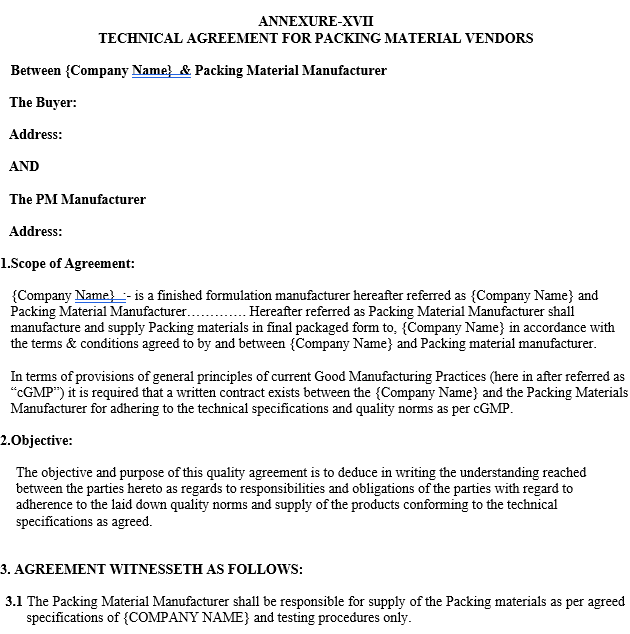
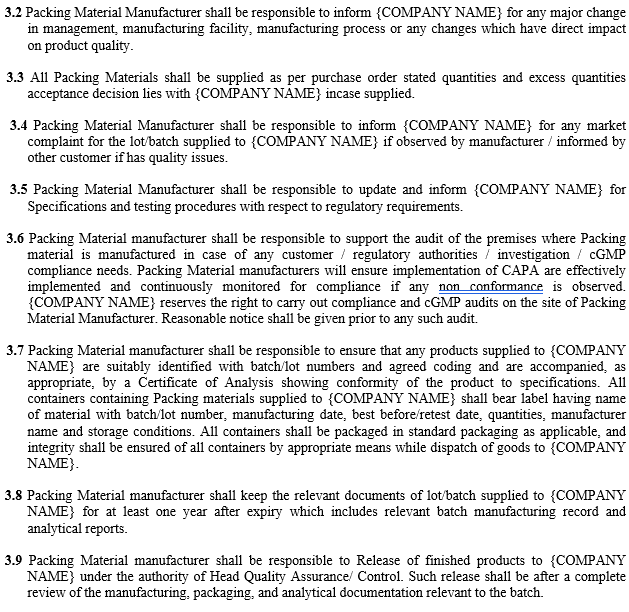
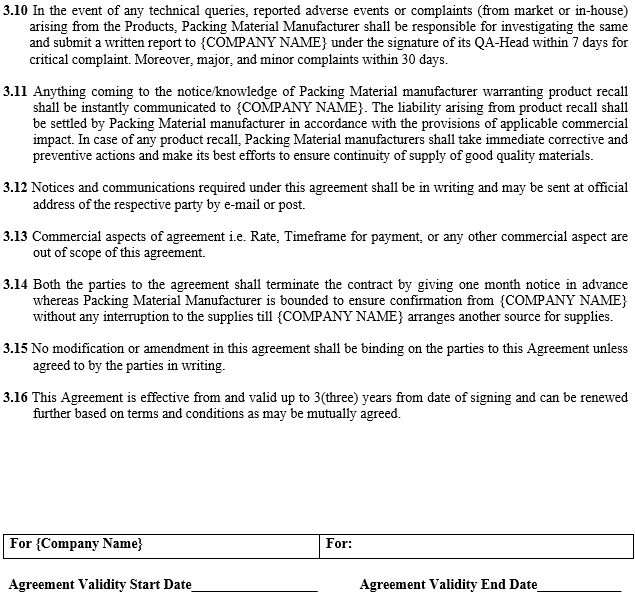
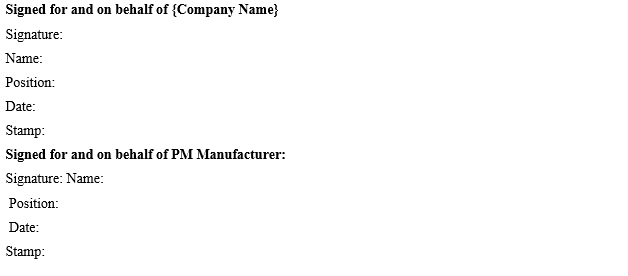
Click the link for download word file copy of this document: https://pharmaguidehub.com/product/vendor-qualification/